Materialfragen: Der Materialauswahlprozess
Die Informationen in dieser Broschüre richten sich an alle, die eine quantitative Auswertung eines Teils vornehmen, Lasten, Spannungen, Dehnungen und Umgebungen ermitteln und eine optimale Werkstoffauswahl auf der Grundlage der Analyse treffen möchten. Wenn der Schutz von Menschenleben eine Rolle spielt oder Zuverlässigkeit oder Effizienz absolut erforderlich sind, muss jedes Teil entsprechend konzipiert und der Werkstoff entsprechend ausgewählt werden. Beim Betrachten dieser Broschüre werden Sie feststellen, wie viele Faktoren an der Werkstoffauswahl beteiligt sind und wie diese durch die Umgebung und die Anwendung beeinflusst wird. Sie werden verstehen, warum ein Ingenieur sich bei der Empfehlung eines spezifischen Materials für das Teil eines anderen sehr zurückhalten wird.
Viele der Kunden von Protolabs, die Teile entwickeln sind jedoch keine Ingenieure, und viele Anwendungen von Teilen, die von Protolabs hergestellt wurden sind relativ harmlos und bewegen sich voraussichtlich im Leistungsbereich gängiger Kunststoffe. Wenn die Anwendung Ihres Teils bei Raumtemperatur erfolgt, es keinen nennenswerten Belastungen ausgesetzt ist und Sie bereit sind, ein paar Teile herzustellen und sie mit einem Hammer zu zerschlagen, um zu sehen, ob sie robust genug für Ihre Anwendung sind, beachten Sie die vereinfachten Empfehlungen für die Auswahl von Werkstoffen am Ende dieser Broschüre („Wie Sie sich das Rechnen ersparen“).
Die Materialauswahl kann manchmal ein Ratespiel sein. Erstens, weil im Allgemeinen das Verständnis des fundamentalen Zusammenhangs zwischen der inneren Struktur des Werkstoffs und seinen Eigenschaften fehlt. Zweitens, weil einer genauen Bestimmung der Anwendungsanforderungen in der Regel nicht genügend Zeit und Aufmerksamkeit gewidmet wird. Schließlich, weil es – selbst nach Überwindung der ersten beiden Hürden – schwierig sein kann, genaue Daten zu den Materialeigenschaften zu finden.
In Werkstoffdatenbanken sind mehr als 85.000 kommerzielle Möglichkeiten für Kunststoffe aufgeführt, die tatsächliche Anzahl liegt wahrscheinlich bei über 90.000. Die umfangreiche Palette an Möglichkeiten kann in etwa 45 Polymerfamilien bzw. -mischungen eingeteilt werden, die wiederum in zwei Hauptkategorien unterteilt werden können: Duroplaste und Thermoplaste. Obwohl Duroplaste die ersten kommerziellen Polymere waren, ist ihre Verwendung dermaßen zurückgegangen, dass sie heute nur noch etwa 15 % aller in einem Jahr verarbeiteten Werkstoffe ausmachen. Daher legt die vorliegende Broschüre ihren Schwerpunkt auf Thermoplaste.
Das Standard-Materialdatenblatt
Das Standard-Materialdatenblatt besteht fast vollständig aus bei Raumtemperatur gemessenen Leistungseigenschaften. Darüber hinaus werden die Leistungseigenschaften mit Katastrophenereignissen in Verbindung gebracht, die als nicht akzeptables Ergebnis für technische Kunststoffteile gelten. Die Streckspannung und die Bruchdehnung sind die Standardkennzahlen der Leistungsfähigkeit eines Werkstoffs, obwohl Streckung und Bruch nicht die gewünschten Reaktionen von Kunststoffteilen sind, wenn sie einer Belastung ausgesetzt werden.
Bei der Bestimmung des richtigen Werkstoffs für Ihre Anwendung müssen Informationen aus einer Reihe unvollständiger Quellen zusammengeführt werden. Das Datenblatt ist die primäre Quelle von Informationen, und Sie sollten lernen, möglichst viele Informationen aus dieser Quelle zu entnehmen. Anhang A zeigt ein Datenblatt für mit 30 % Glasfaser verstärkten PBT-Polyester. Dies ist ein gutes Beispiel eines angemessen detaillierten Datenblatts.
Ausführlichere Informationen können manchmal den von einzelnen Werkstoffanbietern veröffentlichten Konstruktionshandbüchern und Anwendungshinweisen entnommen werden und eventuell in den Datenblättern bestehende Lücken füllen. Zusatzinformationen stehen in der Regel eher für leistungsfähigere technische und Spezialwerkstoffe als für Konsumgütermaterialien zur Verfügung. Wenn Sie einen Werkstoff richtig verstehen möchten, müssen Sie sich auf etwas Detektivarbeit einstellen.
Die maximale kurzzeitige Gebrauchstemperatur verstehen
Die maximale kurzzeitige Gebrauchstemperatur ist wahrscheinlich der wichtigste Datenblattparameter. Traditionell versteht man darunter die Formbeständigkeit in der Wärme (DTUL), auch Wärmeformbeständigkeitstemperatur (HDT) genannt. Ein weiterer verwandter Parameter ist die Vicat-Erweichungstemperatur. Da mit DTUL die mechanische Formbeständigkeit gemessen wird und der Vicat-Punkt näher am tatsächlichen Schmelz- oder Erweichungspunkt des Polymers liegt, ist die Vicat-Zahl in der Regel höher. Bei einem Werkstoff wie dem glasfaserverstärkten PBT aus Anhang A, einem teilkristallinen Werkstoff, liegen alle diese Werte sehr nahe am Kristallitschmelzpunkt des Polymers von 223 °C. Für jede Anwendung, bei der es auch nur zu kurzzeitigen Abweichungen über diese Temperatur kommt, kommt dieses Polymer außer Betracht.
Die obere Temperaturgrenze für gefüllte oder ungefüllte amorphe Polymere lässt sich auch durch Betrachtung der HDT oder DTUL ermitteln. Bei ungefülltem Polycarbonat z.B. liegen die HDT-Werte je nach Gütegrad zwischen 130 und 140 °C. Die Vicat-Erweichungspunkte liegen ggf. ein paar Grad niedriger. Amorphe Polymere weisen beim Erstarren keine signifikante kristalline Struktur auf und besitzen daher keinen Schmelzpunkt. Sie besitzen jedoch einen sogenannten „Glasübergang“. Praktisch gesehen, ist dies die Temperatur, bei der amorphe Polymere ihre Belastbarkeit verlieren. Bei Polycarbonat liegt dieser Wert – bei Messung mithilfe dynamischmechanischer Verfahren – bei etwa 153 °C, nur ein paar Grad über dem Vicat-Erweichungspunkt und 10-20 °C über der DTUL, je nach Probengeometrie und Messmethode der DTUL. Die Vicat-Erweichungstemperaturen und DTUL-Werte sollten nie als langfristige Leistungseigenschaften verwendet werden. Sie können jedoch zur Beurteilung der Kurzzeit-Hitzebeständigkeit herangezogen werden, wenn „Kurzzeit“ im Minutenbereich angesiedelt ist. Für jede Anwendungsumgebung, bei der es zu Temperaturabweichungen oberhalb dieser Werte kommt, kommt dieser bestimmte Werkstoff unabhängig von seinen anderen Eigenschaften außer Betracht.
Streckgrenze und Zugfestigkeit
Zu den langfristigen Leistungseigenschaften eines Werkstoffs unter ständiger Spannung zählt die sogenannte „Kriechfestigkeit“; wenn die Spannung regelmäßig auftritt, wird die Kriechfestigkeit zur wichtigsten Überlegung. Der Zusammenhang zwischen Spannung, Zeit und Temperatur ist kompliziert und oft stehen die Daten, die für eine gute Entscheidung zum langfristigen Verhalten eines Werkstoffs unter Belastung notwendig sind nicht zur Verfügung. Auch hier kann das Datenblatt eine Obergrenze bereitstellen. Bei duktilen Werkstoffen ist die Streckgrenze des Werkstoffs und bei spröden Materialien die Spannung die Obergrenze. Beide Werte definieren den Punkt, bei dem der Werkstoff katastrophal versagt. Für jede Umgebung, in der es zu Spannungen und Dehnungen kommt, die über diesen Werten liegen, kommt der Werkstoff selbst im kurzfristigen Bereich außer Betracht. Abgesehen von diesem einfachen Filter müssen Sie die langfristigen Temperatureinflüsse betrachten.
Tabelle 1: Zugfestigkeitswerten bei unterschiedlichen Temperaturen für ein glasfaserverstärktes Nylon 6/6 | |
---|---|
Temperatur (°C) | Zugfestigkeit (psi) |
-4 | 36.500 |
23 | 30.000 |
77 | 17.500 |
121 | 12.500 |
Den Zusammenhang zwischen Spannung und Temperatur verstehen
Zur Vorhersage der langfristigen Leistung bei hohen Temperaturen ist der Zugriff auf mehrere Datenpunkte notwendig. Mit steigender Temperatur oder mit steigender gewünschter Lebensdauer des Produkts nimmt das zulässige Spannungsniveau, mit dem der Werkstoff verwendet werden kann, je nach den thermischen und mechanischen Eigenschaften des spezifischen Materials, ab. Der Zusammenhang zwischen kurz- und langfristiger Leistung hat gezeigt, dass die langfristigen Arbeitsspannungsniveaus bei einem Thermoplast in der Regel zwischen 20 und 40 % der kurzfristigen Streckfestigkeit oder Bruchfestigkeit liegt. Ungefüllte Werkstoffe fallen tendenziell in das untere Ende dieses Bereichs, während hochgefüllte Compounds tendenziell in das obere Ende dieses Bereichs fallen. Durch Sicherheitsfaktoren für ein bestimmtes Produkt werden diese Werte gesenkt, und wenn die Temperatur der Anwendungsumgebung sich den DTUL-Werten annähert, ist es möglich, dass die nachhaltige Arbeitsspannung nur 3-5 % des auf dem Datenblatt angegebenen Wertes beträgt. Auf manchen Datenblättern werden die Werte für Zugfestigkeit und Elastizitätsmodul bei mehreren Temperaturen angegeben. Gegebenenfalls können diese Daten viel Raterei ersparen. Tabelle 1 zeigt ein Beispiel von Zugfestigkeitswerten bei unterschiedlichen Temperaturen für ein glasfaserverstärktes Nylon 6/6.
Den Zusammenhang zwischen Temperatur und Alterung verstehen
Alle Polymere besitzen eine langfristige Empfindlichkeit gegenüber Sauerstoff. Diese Empfindlichkeit steigt bei höheren Temperaturen. Die mit der Alterung einhergehende Zersetzung wird von der Eigenschaft „relativer Temperaturindex“, kurz RTI, erfasst. Dieser Wert stammt aus einer von Underwriters Laboratories durchgeführten Prüfung. Er ist derzeit das beste Instrument zur Messung der langfristigen Effekte der Alterung auf die mechanischen und elektrischen Eigenschaften von Polymeren. Der RTI-Test beginnt mit der Messung der wichtigsten Basiseigenschaften, wie Zugfestigkeit, Kerbschlagzähigkeit und Lichtbogenfestigkeit. Anschließend werden Testproben bei unterschiedlichen Temperaturen gealtert und die Basiseigenschaften überwacht, bis sie auf 50 % der Ausgangswerte abfallen. Die zum Erreichen einer 50 %igen Leistung benötigte Zeit wird „Zeit bis zum Ausfall“ genannt. Wenn drei bis vier Temperaturen verwendet werden und der Logarithmus der Zeit bis zum Ausfall als eine Funktion der reziproken Temperatur aufgetragen wird, können die Datenpunkte zu einer geraden Linie verbunden werden. Diese Linie wird daraufhin auf eine Standardzeit (normalerweise etwa acht Jahre) extrapoliert und die Temperatur, die bei der Standardzeit voraussichtlich einen Ausfall verursacht ist der relative Temperaturindex. Bei den meisten Thermoplasten liegen die RTI-Werte niedriger als die DTUL- und Vicat-Erweichungstemperaturwerte. Dies ist beim glasfaserverstärkten PBT aus unserem Datenblatt in Anhang A der Fall, wo alle DTUL- und Vicat-Werte über 200 °C (392 °F) liegen, während die RTI-Werte bei 140 °C (284 °F) liegen. Weiche, flexible Werkstoffe mit guter thermischer Oxidationsbeständigkeit, wie PTFE, können jedoch RTI-Werte besitzen, die über ihren DTUL-Werten liegen.
Die RTI-Werte können zur Vorhersage der langfristigen Leistung herangezogen werden, bei der die Alterung das Hauptproblem darstellt. Der Alterungsprozess folgt einer empirischen Regel, die Zersetzung und Temperatur in Beziehung setzt. Die Abbaugeschwindigkeit verdoppelt sich mit jedem Temperaturanstieg um 10 °C. Es besteht also ein exponentielles Verhältnis, sodass eine Veränderung um 20 °C die Abbaugeschwindigkeit um einen Faktor von 22 bzw. um 4 erhöhen wird, während ein Anstieg um 30 °C die Geschwindigkeit um einen Faktor von 23 bzw. um 8 erhöht. Da der RTI auf einen Zeitrahmen von etwa acht Jahren ausgelegt ist, können Sie veranschlagen, dass ein Werkstoff vier Jahre bei einer Temperatur von 10 °C über dem RTI, zwei Jahre bei einer Temperatur von 20 °C über dem RTI und ein Jahr bei einer Temperatur von 30 °C über dem RTI übersteht. Sicherheitsfaktoren sollten in dieser Berechnung berücksichtigt werden, da der nominale Beschleunigungsfaktor von 2 Studien zufolge zwischen 1,8 und 2,5 schwanken kann.

Elastizitätsmodul
Das Elastizitätsmodul ist auf praktisch jedem Datenblatt angegeben. Meistens ist es als E-Modul oder Dehnungsmodul angegeben. Das Elastizitätsmodul beschreibt den Zusammenhang zwischen Spannung und Dehnung und kann als Maß der Steifigkeit angesehen werden. In den meisten Fällen wird das Elastizitätsmodul im linearen Bereich der Spannungs-Dehnungs-Kennlinie berechnet. Bei sehr geringen Dehnungen wird die Linearität häufig verlassen. Abbildung 1 zeigt eine vergrößerte Ansicht des frühen Abschnitts einer Spannungs-Dehnungs- Kennlinie für einen hochglasfaserverstärkten Nylon 6/6. Während das Elastizitätsmodul dieses Werkstoffs bei Raumtemperatur mit einem Wert von 10.600 MPa (1.537.000 psi) angegeben ist, zeigt die Kurve, dass das Spannungs-Dehnungs-Diagramm bei etwa 0,4 % von der Linearität abweicht. Über diesem Punkt geht mit jedem inkrementellen Spannungsanstieg eine progressiv größere Dehnung einher. Abbildung 2 zeigt, dass während der Anstieg das Elastizitätsmodullinie den auf dem Datenblatt angegebenen Wert widerspiegelt, der effektive Anstieg der Linie, die den Ausgangspunkt mit der Dehngrenze verbindet, nur 40 % dieses angegebenen Wertes entspricht. Wenn das Elastizitätsmodul als Auswahlkriterium herangezogen wird, ist es daher wichtig, die Position der Anwendungsspannung auf der Spannungs-Dehnungs-Kennlinie zu verstehen.
Spannungsrisse — Die häufigste Ursache für Versagen von Kunststoffteilen während der Anwendung
Wenn in der Anwendungsumgebung eine Chemikalie vorhanden ist, die das Phänomen der „Spannungsrisse“ hervorrufen kann, nimmt die maximale Arbeitsspannung ab. Tabelle 3 zeigt die maximale Arbeitsspannung für dasselbe Polycarbonat wie in Tabelle 2 wobei die ständige Spannung mit dem Vorhandensein einer Spannungsrisse hervorrufenden Flüssigkeit gekoppelt ist. Die Tabelle zeigt, dass die mechanische Belastbarkeit des Werkstoffs gegenüber seinen Eigenschaften ohne die Chemikalie abnimmt. Das Versagen eines Kunststoffs unter dem kombinierten Einfluss aus Spannung und chemischem Wirkstoff wird umgebungsbedingte Spannungsrisskorrosion genannt und ist die häufigste Ursache für ein Versagen von Kunststoffteilen während der Anwendung.
Tabelle 2: Maximale Arbeitsspannung als Funktion von Zeit für Polycarbonat bei zwei Temperaturen | ||
---|---|---|
Zeit (Stunden) | Arbeitsspannung bei 23°C (psl) | Arbeitsspannung bei 60°C (psl) |
0,01 | 9.200 | 7.200 |
0,1 | 8.850 | 7.000 |
1 | 8.450 | 6.850 |
10 | 8.080 | 6.450 |
100 | 7.700 | 6.050 |
1.000 | 7.425 | 5.800 |
10.000 | 7.100 | 5.100 |

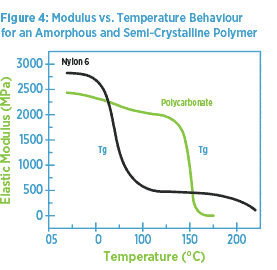
Einfluss der Dehngeschwindigkeit auf Elastizitätsmodul und Dehngrenze
Einige Materialeigenschaften sind abhängig von der Dehngeschwindigkeit. Die Geschwindigkeit, mit der der Werkstoff belastet wird hat einen Einfluss auf den Elastizitätsmodul sowie die Dehngrenze, wie in Abbildung 3 dargestellt. Höhere Dehngeschwindigkeiten gehen mit größeren Elastizitätsmodul- und Dehngrenzenwerten einher. Obwohl es wünschenswert wäre, dass alle Anbieter eines bestimmten Werkstofftyps beim Prüfen dieselben Dehngeschwindigkeiten zugrunde legten, ist dies nicht immer der Fall, sodass die Datenblatteigenschaften aufgrund dieser fehlenden Harmonisierung deutliche Unterschiede aufweisen können.
Temperaturabhängige Änderungen des Elastizitätsmoduls
Das Elastizitätsmodul ändert sich mit der Temperatur. Ein Datenblatt, in dem die Elastizitätsmodulwerte für mehrere Temperaturen, wie die in Tabelle 1 aufgeführt sind, bietet ein vollständigeres Bild des Verhaltens eines Werkstoffs. Selten findet man jedoch Daten für mehr als vier Temperaturen, die sich über eine Spanne von 150-200 °C erstrecken können. Daher besteht starke Unsicherheit über das Verhalten des Werkstoffs zwischen diesen Punkten oder außerhalb des durch diese Punkte definierten Bereichs. Die dynamisch-mechanische Analyse (DMA) ermöglicht eine kontinuierliche Messung des Elastizitätsmodus über einen weiten Temperaturbereich. Abbildung 4 zeigt Elastizitätsmodul-Temperatur-Kurven für Polycarbonat, ein amorphes Polymer, und Nylon 6, ein teilkristallines Polymer.
Diese beiden Werkstoffe weisen ein für ihre jeweilige Struktur typisches Verhalten auf. Beide besitzen einen Glasübergang, bei dem die molekulare Bewegung in den amorphen Regionen der Struktur einsetzt. Im amorphen Polycarbonat führt dies zum vollständigen Verlust aller nützlichen mechanischen Eigenschaften über einen relativ engen Temperaturbereich. Beim Nylon hingegen ist der Abfall des Elastizitätsmoduls zwar erheblich, jedoch nicht katastrophal, da 20 % der Leistung bei Raumtemperatur erhalten bleiben. Dies veranschaulicht den Beitrag der kristallinen Struktur im Polymer. Alle amorphen Polymere weisen ein temperaturabhängiges Verhalten auf, das dem von Polycarbonat ähnelt, und alle teilkristallinen Werkstoffe zeigen ein Eigenschaft-Temperatur-Profil, das dem von Nylon ähnelt. Die wesentlichen Unterschiede liegen in den genauen Übergangstemperaturen bei den einzelnen Polymeren.
Schlagzähigkeit
Die Beurteilung der Schlagzähigkeit anhand typischer Datenblattwerte ist anspruchsvoll, da die Branche viele verschiedene Methoden zum Prüfen der Schlagzähigkeit und zur Darstellung der Ergebnisse verwendet. Die gängigste Prüfmethode zur Bewertung der Schlagzähigkeit ist der Izod-Kerbschlagbiegeversuch. Die Prüfung verwendet einen Prüfkörper mit einer scharfen Kerbe, die in das Teil eingefräst wird, sowie ein Pendel, das die Energie zum Zerschlagen der Probe überträgt.
Aufgrund der unterschiedlichen Kerbempfindlichkeit der Werkstoffe übertreibt der Mindestradius bei der Izod-Kerbe häufig die Duktilitätsunterschiede. Polycarbonat und amorpher PET-Polyester beispielsweise besitzen beide eine gute praktische Zähigkeit. PET-Polyester ist kerbempfindlicher als Polycarbonat.

Infolgedessen können die Kerbschlagzähigkeitswerte für Polycarbonat bei Raumtemperatur deutlich höher sein als bei manchen PET-Polyesterqualitäten, was darauf schließen lässt, dass Polycarbonat ein wesentlich zäherer Werkstoff ist. Ein vollständigeres Bild der Schlagzähigkeit ergibt sich, wenn die Schlagzähigkeitsergebnisse aus unterschiedlichen Kerbschlagbiegeversuchen stammen.
Fallhammerverfahren, wie der Gardner-Test oder der instrumentierte Fallhammer-Kerbschlagbiegeversuch können zusätzliche Datenpunkte liefern. Diese Prüfungen verwenden Proben, bei denen keine Spannungskonzentration in das Teil eingefräst ist und spiegeln die von einem gut konzipierten Teil zu erwartende Leistung genauer wider.
Die Schlageigenschaften werden außerdem von der Temperatur beeinflusst. Niedrigere Temperaturen führen mit größerer Wahrscheinlichkeit zum spröden Verhalten eines Werkstoffs und der Übergang von zäh zu spröde kann sehr plötzlich erfolgen. Es kann schwierig sein, ein vollständiges Bild dieses Verhaltens zu finden, da Werkstoffanbieter zurückhaltend über ungünstige Leistungseigenschaften berichten. Eine Recherche kann jedoch wertvolle Ergebnisse zutage bringen, auch wenn diese Ergebnisse nicht für alle Werkstoffe verfügbar sind Abbildung 5 zeigt das Kerbschlagzähigkeitsverhalten für unterschiedliche Polycarbonat-Qualitäten als Funktion von Temperatur. Diese Ergebnisse veranschaulichen den abrupten Übergang von zäh zu spröde, der typischerweise mit abnehmender Temperatur erfolgt. Dieses Schaubild zeigt außerdem, dass der Übergang von zäh zu spröde mit dem Molekulargewicht des Polymers in Zusammenhang steht. Die niedrigeren Schmelzfließindexwerte stehen im Zusammenhang mit den Qualitäten mit höheren durchschnittlichen Molekulargewichten. Diese Eigenschaft hat einen erheblichen Einfluss auf die Temperatur, bei der sich die Schlagzähigkeit ändert.
Schmelzfließindex
Der Schmelzfließindex ist eine Eigenschaft, die auf den meisten Eigenschafts-Datenblättern erscheint. Er ist ein Versuch, einen wichtigen Aspekt des Werkstoffverhaltens mit einer einzigen Zahl auszudrücken. Der Schmelzfließindex wird häufig von Verarbeitern als Maß dafür verwendet, wie ein Werkstoff beim Spritzgussverfahren fließt. Die Bedeutung des Schmelzfließindexwerts liegt in seiner Beziehung zum durchschnittlichen Molekulargewicht des Polymers begründet. Niedrigere Schmelzfließindexwerte stehen im Zusammenhang mit Werkstoffen mit einem höheren durchschnittlichen Molekulargewicht. Ein höheres Molekulargewicht wiederum sorgt für verbesserte Eigenschaften, besonders in den Bereichen Schlagzähigkeit, Kriechfestigkeit und Ermüdungsverhalten, sowie bessere Sperreigenschaften.
Werkstoffvergleiche auf der Grundlage des Schmelzfließindex sind nur dann aussagekräftig, wenn sie innerhalb einer bestimmten Polymerfamilie erfolgen. Darüber hinaus werden bei manchen Werkstoffen mehrere Bedingungen für die Prüfung verwendet. ABS beispielsweise kann unter verschiedenen, von der Temperatur und der Belastung definierten Bedingungen, denen der Werkstoff ausgesetzt wird, geprüft werden. Diese Prüfbedingungen, sowie die mit den einzelnen Bedingungen verbundenen typischen Unterschiede in den Ergebnissen, sind in Tabelle 4 dargestellt. Beim Vergleich von zwei Werkstoffqualitäten ist es wichtig, die Prüfparameter zu notieren und entsprechend anzupassen.
Tabelle 4: Einfluss von Prüfbedingungen auf den Schmelzfließindex von ABS | |
---|---|
Testbedingungen | Schmelzfließindex (g/10 min) |
200 °C/5,0 kg | 1,5 |
230 °C/3,8 kg | 4,5 |
220 °C/10,0 kg | 18,0 |
Tabelle 5: Wärmeausdehnungskoeffizientwerte für einen zu 43% mit glasfaserverstärktem Nylon 6/6 über verschiedene Temperaturbereiche | |
---|---|
Temperaturbereich | Linearer Wärmeaus- dehnungskoeffizient CLTE (In/In/°F) |
-40 bis 73 | 0,00034 |
73 bis 131 | 0,000044 |
131 bis 320 | 0,000071 |
Andere Materialeigenschaften
Bei spezifischen Anwendungen können neben den thermischen und mechanischen Eigenschaften noch andere Eigenschaften wichtig sein. Dazu gehören elektrische Eigenschaften wie Dielektrizitätskonstante und Durchschlagfestigkeit, spezifischer Oberflächen- und Durchgangswiderstand, sowie der Wärmeausdehnungskoeffizient. Standardmessungen des Wärmeausdehnungskoeffizients werden zwischen -30 °C und +30 °C durchgeführt. Einige Anbieter geben jedoch Werte über mehrere Temperaturbereiche an, wie in Tabelle 5 dargestellt. Sofern ein solches komplexeres Bild verfügbar ist, veranschaulicht es, dass diese Typen von Eigenschaften auch von der Temperatur abhängen und die Werte tendenziell mit zunehmender Temperatur steigen.
Kunststoffe gelten in der Regel als hervorragende elektrische Isolatoren, sofern ein Compound nicht speziell zum Ableiten von elektrostatischer Aufladung hergestellt wird oder durch die Hinzugabe von Bestandteilen, wie Kohlenstoff oder Edelstahl einigermaßen leitfähig wird. Daher liegen die Werte für den spezifischen elektrischen Widerstand bei den meisten Werkstoffen sehr hoch, nämlich zwischen 1010 und 1016 Ohm beim spezifischen Oberflächenwiderstand, bzw. Ohm cm beim spezifischen Durchgangswiderstand. Eine dauerhafte elektrische Belastung kann mit der Zeit zum dielektrischen Durchschlag eines Werkstoffs führen. Dieses Verhalten hängt von der Höhe der angelegten Spannung ab und wird am effektivsten durch Eigenschaften erfasst, die Teil des Standard-Datenblattes sein können, jedoch rascher in der Datenbank der Underwriter Laboratories als Teil ihres Yellow Card-Systems zu finden sind. Diese Methode verwendet nummerische Werte für Eigenschaften, wie die Entzündung durch einen Starkstrom-Lichtbogen, die Kriechstrom- und Lichtbogenfestigkeit, sowie die kontinuierliche Kriechstromfestigkeit, wobei die niedrigsten Werte für jede Maßzahl auf eine höhere Leistung hindeuten und höhere Werte mit niedrigeren Leistungsniveaus in Zusammenhang gebracht werden.
Wie Sie sich das Rechnen ersparen
Ein Berater spricht in der Regel keine Werkstoffempfehlung aus, ohne die kompletten Anwendungsanforderungen für das Teil verstanden und eine Designanalyse zum 3D-Modell des Teils durchgeführt zu haben. Manchmal kann es kostspielig sein, das Teil zuerst vollständig zu entwickeln, um danach eine Werkstoffauswahl zu treffen. Wenn Sie die werkstofftechnischen Aspekte umgehen und dennoch eine fundierte Werkstoffauswahl treffen möchten, können Sie sich an folgende Faustregeln halten:
1 Versuchen Sie es mit ABS. ABS funktioniert bei unzähligen Anwendungen. Der Werkstoff ist preisgünstig, stabil, relativ robust, besitzt ein anständiges Erscheinungsbild und verzeiht Ihnen, selbst wenn Sie nicht alle Standard- Designregeln für Kunststoffteile beherzigen. ABS besitzt einen relativ niedrigen Schmelzpunkt. Alle Teile in dem Musterwerkzeug von Protolabs sind aus ABS gefertigt.
2 Wenn es günstig sein soll und die Steifigkeit und Ästhetik eher unwichtig sind, probieren Sie Polypropylen (PP) aus. Der Design-Würfel von Protolabs besteht aus PP.
3 Wenn Sie etwas Robusteres als ABS oder etwas Hitzebeständigeres suchen, versuchen Sie es mit Polycarbonat (PC). PC ist weniger tolerant als ABS, wenn Sie die folgenden Standard- Designregeln für Kunststoffteile nicht beachten.
4 Wenn es transparent und hübsch aussehen soll, versuchen Sie Acryl (PMMA). PMMA kann etwas spröde sein. Ein transparentes PC ist zwar robuster als PMMA, aber ästhetisch etwas weniger ansprechend.
5 Wenn Sie Spritzgussteile planen, versuchen Sie, mithilfe der CNC-Bearbeitung von Protolabs ein paar Testteile aus dem gewünschten Werkstoff herzustellen, bevor Sie sich für ein Werkzeug entscheiden. Werkzeuge werden so konzipiert, dass sie die Schrumpfrate eines bestimmten Kunststoffs berücksichtigen. Daher ist es unter Umständen nicht möglich, mehrere Kunststoffe in dasselbe Werkzeug zu spritzen, ohne ein Risiko bei der Teilegröße, den Toleranzen und/oder den Abmessungen einzugehen.
^ Back To Top