Guide d'initiation au moulage par injection
Apprenez les bases du processus de moulage par injection, y compris son fonctionnement, les principes de conception, les matières et les systèmes de qualité
Qu'est-ce que le moulage par injection ?
Le moulage par injection est un processus conçu pour produire des pièces en grandes séries. Par rapport à d'autres technologies de fabrication, notamment l'usinage CNC et l'impression 3D, il nécessite un investissement initial dans l'outillage. Mais le prix de chaque pièce est ensuite nettement inférieur à celui d'autres méthodes de fabrication de pièces en plastique. Cette structure des coûts en fait une solution abordable pour la production.
Il est généralement utilisé pour fabriquer des pièces en plastique à grande échelle en raison de la faible quantité de déchets et un coût par pièce réduit. C'est un processus de fabrication idéal pour les dispositifs médicaux, les produits de consommation et les pièces automobiles.
Fonctionnement du moulage par injection
Fabrication de l'outillage : une fois la conception de la pièce achevée, la première étape consiste à fraiser l'outillage, lequel est généralement en acier ou en aluminium. Dans la plupart des cas, le bloc de métal est placé dans une fraiseuse CNC, qui découpe un négatif de la pièce en plastique finale. Des traitements supplémentaires, comme le polissage ou la gravure laser, peuvent ensuite être appliqués à l'outillage pour obtenir des finitions de surface spécifiques.
Production de pièces : La production de pièces en plastique proprement dite commence par le chargement de granulés de résine dans un cylindre. La température de ce dernier est élevée jusqu'à la fusion des granulés de résine, qui sont ensuite comprimés. Le plastique fondu est alors injecté dans l'outil métallique à travers un système de canaux d'alimentation, puis introduit dans la cavité du moule à travers des orifices. La pièce se refroidit, se solidifie et est éjectée de l'outil à l'aide de broches d'éjection.
Types de moulage par injection
Le terme « moulage par injection » englobe une série de procédés qui consistent à injecter de la résine liquide dans un outil pour former des pièces en plastique. En voici quatre parmi les plus courants :
Moulage par injection thermoplastique : le moulage par injection thermoplastique est le type de moulage le plus courant. Il consiste à injecter de la matière thermoplastique dans le moule, où elle refroidit pour former la pièce finale.
Moulage de silicone liquide : le caoutchouc de silicone liquide utilise des matières thermodurcissables et la pièce en plastique est créée par réaction chimique.
Surmoulage : Le surmoulage est un procédé utilisé pour fabriquer des pièces en plastique avec deux matières ou plus. On l'utilise souvent pour des pièces destinées à améliorer la prise en main par ajout de caoutchouc à la poignée.
Moulage d'insert : Le moulage d'insert est un procédé qui commence par la mise en place d'un insert dans le moule avant l'introduction du polymère. La matière est ensuite injectée et coule autour de l'insert, généralement en métal, pour former la pièce finale. Ce procédé est fréquemment utilisé pour les pièces nécessitant un filetage métallique.
Principes de conception de base pour le moulage par injection
Tolérances
Notre processus de moulage par injection nous permet d'obtenir une précision d'usinage d'environ ±0,08 mm. La tolérance de rétraction dépend principalement de la conception de la pièce et du choix du polymère. En fonction de la matière choisie, la tolérance du polymère peut atteindre une précision de 0,002 mm/mm. (Les tolérances du polymère de toutes les matières thermoplastiques sont visibles sur votre devis).
Épaisseur de paroi
L'épaisseur de paroi est importante, car elle peut provoquer des défauts tels que la retassure et le gauchissement. La meilleure pratique consiste à maintenir une épaisseur uniforme sur l'ensemble d'une pièce moulée par injection. Nous recommandons une épaisseur de paroi au moins égale à 40-60 % de l'épaisseur de paroi adjacente, et toutes doivent se situer dans les fourchettes recommandées pour le polymère choisi.
Géométrie du noyau
Noyautez les pièces pour éliminer les parois épaisses. Vous obtiendrez la même fonctionnalité avec une bonne pièce moulée. Les épaisseurs inutiles peuvent modifier les dimensions de la pièce, réduire sa résistance et demander un usinage post-traitement.
Dépouille
L'ajout d'une dépouille à des pièces moulées est essentielle pour s'assurer que ces dernières ne se déforment pas pendant le processus de refroidissement. De plus, elles s'éjectent facilement du moule. L'application de 1 à 2° est approprié dans la plupart des cas. En cas de faces verticales, nous conseillons d'ajouter 0,5° de dépouille.
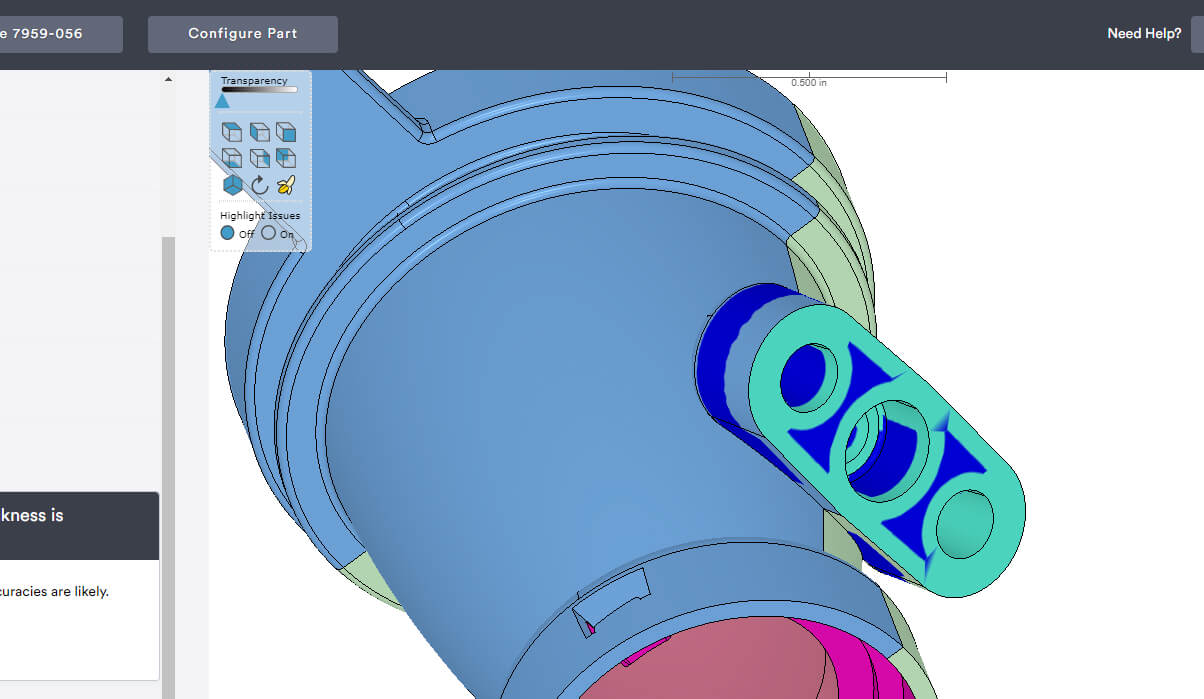
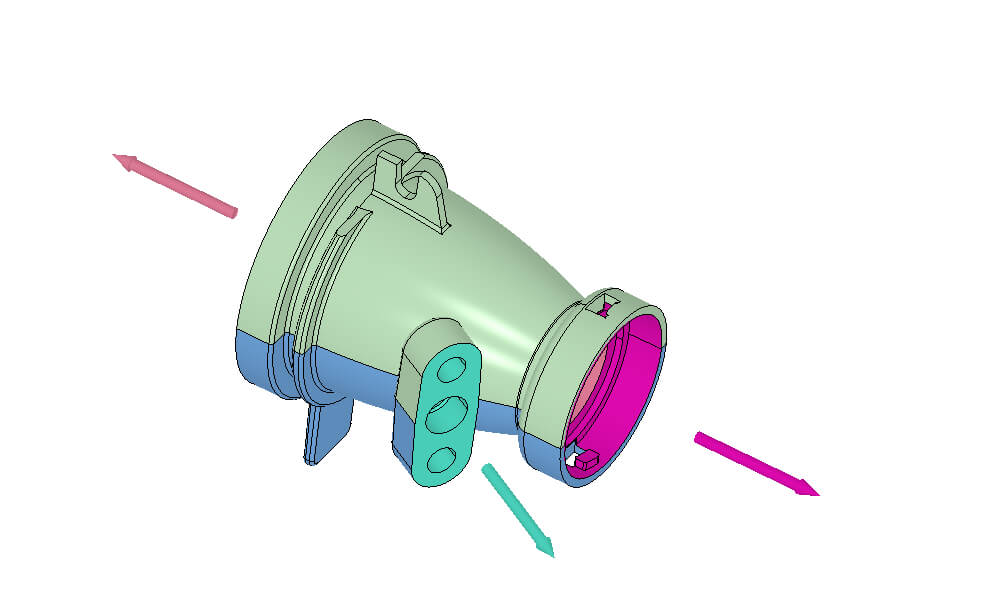
Tiroirs
Élément du moule mis en position lors de la fermeture du moule, à l'aide d'une glissière actionnée par une came. On utilise généralement les tiroirs pour résoudre des problèmes de contre-dépouille, et parfois pour obtenir une paroi extérieure sans dépouille. À l'ouverture du moule, le tiroir s'écarte de la pièce afin de permettre son éjection. Également appelé chariot.
Contre-dépouilles
Partie de la pièce qui en couvre une autre et crée une interférence entre la pièce et l'une ou les deux moitiés du moule. Il pourra s'agir par exemple d'un trou perpendiculaire au sens d'éjection, percé dans le côté d'une pièce. Une contre dépouille rend impossible l'éjection de la pièce ou l'ouverture du moule, ou les deux.
Bossages
Relief cylindrique dans une pièce, souvent prévu pour recevoir des pièces de fixation ou supporter des éléments d'autres pièces qui passent à travers. On peut avoir tendance à concevoir des bossages épais, ce qui augmente la probabilité de retassures et de vides dans une pièce. Considérez la possibilité de renforcer les bossages avec des nervures ou des goussets pour une résistance accrue.
Points d'injection
Un point d'injection est une ouverture dans l'outil de moulage par injection qui permet la pénétration de la matière et le remplissage de la cavité. Il existe trois types communs de points d'injection de moulage par injection.
- Les points d'injection en seuil sont les plus courants, car ils fonctionnent bien avec les additifs et constituent la solution la plus rentable..
- Le point d'injection à buse chaude est idéal pour les pièces dont l'aspect esthétique est la priorité. Il permet également de réduire l'usure de l'outillage et les bavures.
- Les points d'injection en nappe, en sous-marin, en tunnel sont parfaits pour les pièces esthétiques qui ne nécessitent pas de traces. Parfois, cette option n'est pas envisageable en fonction de la matière et de la géométrie.
Nervures
Une nervure est un élément similaire à une fine paroi et parallèle au sens d'ouverture du moule. Elle est fréquemment utilisée pour renforcer une paroi ou un bossage. Pour éviter la retassure, les nervures ne doivent pas représenter plus de 60 % de l'épaisseur de la paroi.
Éjecteur
Les éjecteurs sont intégrés à la moitié B d'un moule et permettent d'éjecter la pièce en plastique en la poussant lorsqu'elle a suffisamment refroidi. La conception d'une dépouille suffisante peut contribuer à réduire le besoin d'éjecteurs sur une pièce.
Logos et texte
Les polices sans empattement sont les plus faciles à fraiser dans un moule avec du texte. Nous recommandons des polices d'une taille supérieure à 20 pt et d'une profondeur entre 0,25 mm à 0,38 mm.
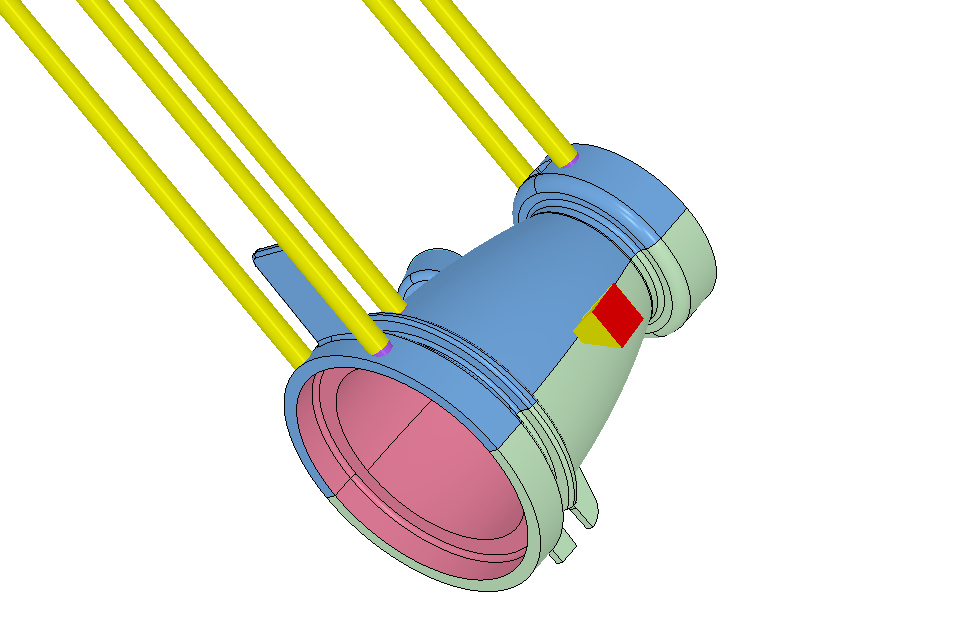

Boîte à outils pour le moulage
Personne n'a dit que la conception et la fabrication de pièces moulées étaient faciles. Notre objectif est de le faire rapidement et avec des pièces de qualité. Notre boîte à outils pour le moulage constitue un bon point de départ.
VOIR LA BOITE A OUTILSMatières plastiques pour le moulage par injection
Lors du choix d'une matière pour votre pièce, plusieurs propriétés peuvent s'avérer pertinentes : la résistance mécanique, physique, chimique, thermique, électrique, l'inflammabilité ou la résistance aux UV. Les fabricants de polymères, les mélangeurs et les moteurs de recherche indépendants de polymères disposent de données en ligne. Voici un aperçu rapide de quelques polymères de base et techniques courantes.
Polymères courants
ABS: L'ABS est un excellent choix pour une grande majorité de pièces. Son prix est raisonnable, il est solide, relativement résistant, son aspect est convenable et il est tolérant même si vous ne suivez pas toutes les règles de conception standard pour les pièces en plastique.
Acétal : une matière solide dotée d'un bon pouvoir lubrifiant
LCP : une matière très résistante qui s'écoule bien, en particulier pour les pièces fines. Elle produit des lignes de soudure peu marquées.
Nylon : coût abordable, robuste et résistant à l'usure. Peut être sujet au rétrécissement et au gauchissement, en particulier le nylon chargé de verre.
Polycarbonate (PC) : il peut tolérer des températures plus élevées et est plus durable qu'un ABS classique, mais il est moins souple pour le moulage.
PMMA (acrylique) : une option abordable pour des pièces transparentes, même s'il peut s'avérer cassant.

Polymères de base
Polypropylène (PP) : le PP est une bonne matière peu onéreuse et convenable lorsque l'esthétique et la rigidité ne sont pas essentielles. Elle résiste aux produits chimiques et est adaptée aux conceptions avec charnières intégrées.
Polyéthylène : options à haute et faible densité. Durable et résistant aux produits chimiques.
Polystyrène : un thermoplastique dur, bon marché et transparent.
Consultez notre guide des matières pour le moulage par injection si vous souhaitez en savoir plus sur les plastiques proposés.
Colorants et additifs pour polymère pour le moulage par injection
Les couleurs disponibles chez le vendeur de polymères sont généralement le noir et le naturel. Le naturel peut être blanc, beige, ambré ou d'une autre couleur. Les couleurs semi-personnalisées sont créées lorsque des granulés de colorant sont ajoutés aux polymères naturels. Nos couleurs en stock n'incluent aucuns frais supplémentaires. Elles peuvent ne pas correspondre exactement et créer des stries ou des tourbillons sur les pièces.
Additifs pour polymère
Les fibres de verre courtes sont utilisées pour renforcer un composite et réduire le fluage, en particulier à des températures élevées. Elles rendent le polymère plus solide, plus rigide, mais plus cassant. Elles peuvent provoquer des déformations en raison de la différence de retrait entre le polymère et les fibres lors du refroidissement.
La fibre de carbone est utilisée pour renforcer et/ou rigidifier un composite, ainsi que pour contribuer à la dissipation de l'électricité statique. Elle présente les mêmes limites que les fibres de verre. La fibre de carbone peut rendre le plastique très rigide.
Des minéraux comme le talc et l'argile sont souvent utilisés comme charges pour réduire le coût ou augmenter la dureté des pièces finies. Comme ils ne rétrécissent pas autant que les polymères lorsqu'ils sont refroidis, ils peuvent réduire les déformations.
Le PTFE (téflon) et le disulfure de molybdène sont utilisés pour rendre les pièces autolubrifiantes dans les applications porteuses..
Comme les fibres de verre courtes, les fibres de verre longues sont utilisées pour renforcer et réduire le fluage, mais elles rendent la résine beaucoup plus résistante et rigide. L'inconvénient est qu'elles peuvent s'avérer particulièrement difficiles à mouler dans le cas de pièces à parois fines et/ou à longs écoulements de matière.
Les fibres d'aramide (Kevlar) sont comparables aux fibres de verre moins abrasives, mais moins résistantes.
Les billes de verre et les flocons de mica sont utilisés pour rigidifier un composite et réduire le gauchissement et le retrait. Avec une charge élevée, ils peuvent s'avérer difficiles à injecter.
Les fibres en acier inoxydable sont utilisées pour contrôler les EMI (interférences électromagnétiques) et les RFI (interférences radioélectriques), généralement dans les boîtiers de composants électroniques. Elles sont plus conductrices que la fibre de carbone.
Inhibiteur d'UV pour les applications extérieures.
Les traitements antistatiques permettent aux résines de dissiper l'électricité statique.
Finitions de surface pour pièces moulées
La finition de la surface est un autre élément important à prendre en compte pour le moulage par injection, car les pièces sont généralement esthétiques et destinées à la production finale. Il ne faut pas oublier qu'une surface texturée nécessitera une dépouille plus importante qu'une finition plus polie. Cela permet de s'assurer que la pièce se détache du moule et que le microbillage peut être appliqué correctement sur l'outil.
Nos options de finition de surface pour le moulage de thermoplastiques et de silicone sont présentées ci-dessous.
Thermoplastique | Caoutchouc de silicone liquide |
|
|
En plus de nos options de finition de surface standard, nous proposons également des finitions Mold Tech / Eschmann standard pour des textures plus complexes. Celles-ci peuvent être utilisées pour améliorer l'adhérence sur la poignée d'une pièce ou pour masquer des défauts esthétiques tels que des plans de joints. Les textures Eschmann permettent d'obtenir les effets suivants :
- des finitions obtenues par microbillage ou par polissage de la surface du moule
- un grainage imitation bois ou imitation cuir
- des surfaces granuleuses
- des finitions mates, brillantes, dépolies, et bien d'autres
Techniques de post-traitement et de moulage avancé
Soudure par ultrasons : Dans les applications de moulage plus complexes, la soudure par ultrasons peut être utilisée pour fusionner les pièces.
Marquage de pièces : il existe deux façons d'ajouter des images, souvent des logos, aux pièces : la tampographie et la gravure laser.
La tampographie permet d'ajouter des graphiques en couleur à des pièces moulées à l'échelle. Elle peut être utilisée pour ajouter des logos, des graphiques et des instructions sur les pièces. Nous proposons la tampographie pour les polymères ABS, PC et ABS/PC.
La gravure laser utilise un laser pour graver une image 2D sur une pièce ou une cavité de moule. Bien que la gravure au laser ne soit pas possible en couleur, elle constitue un moyen plus rentable et plus rapide de marquer des pièces en plastique que la tampographie.
Inserts filetés : les inserts filetés sont des inserts usinés séparément de l'outillage et placés dans le moule avant l'injection de la matière. Ils sont utilisés pour réaliser des contre-dépouilles sur les surfaces intérieures. Les inserts filetés sont éjectés avec la pièce en plastique, puis replacés dans le moule. Ils permettent de contourner de nombreuses restrictions de forme et de positionnement, mais ils sont plus coûteux que les zones de fermeture oblique ou les tiroirs.
Broches en acier : Une broche en acier est suffisamment solide pour supporter les contraintes du démoulage, et sa surface est suffisamment lisse pour se dégager proprement de la pièce sans dépouille. La pièce obtenue ne devrait présenter aucun problème esthétique. Si c'est le cas, il se situera à l'intérieur du trou, là où il ne sera pas visible.
Systèmes de qualité du moulage par injection
Étant donné que les entreprises ont recours au moulage par injection pour produire des milliers, voire des millions de pièces, le contrôle de la qualité est essentiel.
Moulage scientifique : Le moulage scientifique est un processus standard utilisé pour développer, optimiser et documenter le processus de configuration idéal pour chaque projet de moulage par injection. Ainsi, nous suivons le même processus et les mêmes paramètres à chaque utilisation. Cela permet de garantir l'homogénéité des pièces pour chaque série.
Inspection du premier article (FAI) : La FAI est une méthode utilisée pour vérifier que les pièces sont conformes aux spécifications. Nous adoptons une approche critique de la qualité pour les Inspections du premier article en moulage par injection. Grâce à la technologie GD&T, les clients peuvent indiquer les dimensions les plus critiques de leur pièce.
Processus de validation des pièces de production (PPAP) : Le PPAP est un processus d'inspection de la qualité généralement utilisé dans l'industrie automobile. Cette méthode permet de vérifier qu'un processus de production peut produire, de manière fiable et répétée, une pièce de qualité. Une inspection PPAP comporte 18 points, qui vont de la validation par le client jusqu'à la production d'échantillons de pièce.
ISO 13485: La norme ISO 13485 s'applique à l'industrie médicale. Elle comprend la qualification de la conception (DQ), la qualification opérationnelle (OQ) et la qualification des performances (PQ).
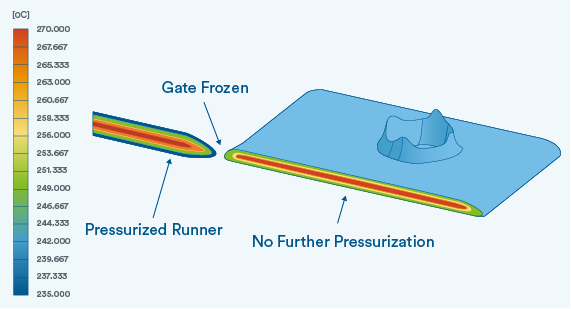