Injection Molding Surface Finishes
From textured to highly cosmetic, there are a number of surface finish options for molded parts
Injection-molded parts are everywhere—from highly cosmetic housings hiding in plain sight to internal components where a fine polish is unnecessary. Most people pay no attention to the surface finish on those parts. But for product designers and engineers, it’s an important design consideration. Identifying the right surface finish is dependent on a few important elements, namely the development or production stage that your parts are in, the materials they’re being manufactured in, and their end-use application.
Surface Finishes for Thermoplastics
Injection molding offers hundreds of thermoplastic resins that are flexible, strong, and can have fine cosmetic finishes. At Protolabs, aluminum molds can be quickly produced by three-axis milling and easily hand polished or textured to one of eight surface finishes, which range from non-cosmetic to high-gloss polish.
Material color and hardness significantly affects the visual aesthetics of finished molded parts. For example:
- Harder materials pick up textures more than softer ones. Polycarbonate shows the difference between an F1 surface finish and a B1 more than on a part made of TPV.
- Darker colors show textures more than lighter colors, regardless of part hardness.
- Fillers impact the overall appearance of texture. A non-filled nylon part will pick up finishes more than a 30% glass filled nylon part, for example.
Surface Finish Specification | Description |
PM-F0 | Non-cosmetic, finish to Protolabs discretion |
PM-F2 | Non-cosmetic, EDM permissible |
PM-F1 | Low-cosmetic, most toolmarks removed |
SPI-C1 | 600 grit stone |
SPI-B1 | 600 grit paper |
SPI-A2 | Grade #2 Diamond Buff |
PM-T1 | Light bead blast |
PM-T2 | Medium bead blast |
All polish and texture is applied directly to the mold itself and transferred to the parts during the injection molding process. For this reason, secondary finishing is not available, which makes material selection critical in some cases. Typically, the link between the surface finish and material is small, but glass, mineral, or soft and high-shrink materials can produce parts that don’t always reflect what you may be looking for in a finish.
Below are images depicting each surface finish option for injection molding.
Glass- and mineral-filled materials provide unique material properties that unfilled materials don’t, but be cautious when using them if they are intended to be a highly cosmetic part. Glass and minerals can create material streaking and the polish can even be difficult to distinguish between grades. This isn’t the case with all filled resins, but we suggest speaking with one of our applications engineers (AEs) or requesting a material sample plaque of the actual material you intend to use.
At Protolabs, you’ll receive a fully interactive quote with design for manufacturability (DFM) feedback that highlights problematic areas where increased attention should be paid—a textured surface may have more draft requirements than a polished surface would, for instance.
Draft is required for two reasons: to provide proper release from the mold so you can avoid scratches or drag marks on your part, and to provide a proper angle for a bead blast finish to be applied to the mold. A minimum of 3-degree draft is required for a PM-T1 finish and a minimum of 5 degrees for a PM-T2. Additionally, finishes on deep and thin ribs may not be possible on parts as they are challenging to reach within the mold.
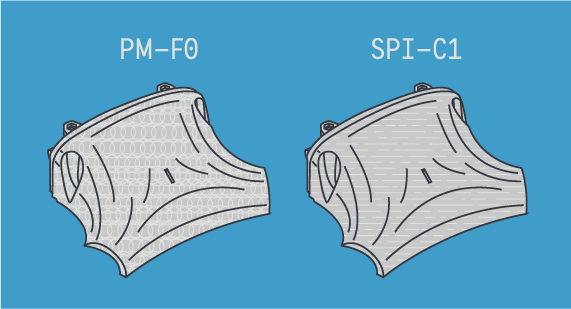
In addition to the eight available surface finishes at Protolabs, you can also obtain a custom finish. With a custom finish, you still have to choose from the seven options, but different finishes can be applied to the A and B sides of the mold. Note that the A side of the mold typically represents the outside of the part and the B side is often the one with the most retention and ejector pins.
We can easily add a custom finish as long as you follow these simple rules:
- Provide a clearly marked, color-coded image (jpg or pdf) of your part indicating the finishes required.
- The part has clearly defined surfaces with a minimum of 0.015 in. (.38mm) of feature height definition, so we can mask off areas for polish or texturing.
- A CAD model is provided with the aforementioned required draft angles for the chosen textures.
Gating and part ejection on clear or cosmetic parts is another consideration to keep in mind. If you have a clear lens, or if the side with the most retention is actually the cosmetic side of the part, you may want to have a discussion with one of our AEs. Ejector pins vary in size, location, and quantity, but are often times a necessity for extracting a part from the mold. Some materials may lend themselves to be extracted manually. Another alternative is to use an ejector plate that covers more surface area and can be added, depending on part geometry.
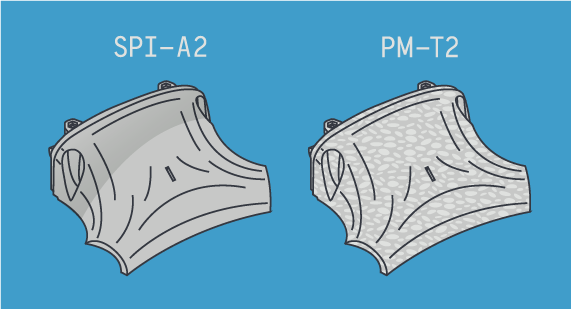
Surface Finish Options for Silicone Rubber Parts
Liquid silicone rubber (LSR) is a thermoset material using the same manufacturing methods for producing a mold as earlier discussed, but the molding process itself is different. LSR molding uses two liquids mixed together, which are then heat cured in the mold to produce a final part.
Surface finish options for LSR are same are more limited than plastics. LSR offers four finishes:
PM-F0: Non-cosmetic, finish to Protolabs discretion
PM-F1: Low-cosmetic, most toolmarks removed
SPI-C1: 600 grit stone
PM-T1: SPI-C1 + light bead blast
PM-T2: SPI-C1 + medium bead blast
SPI-A2: Grade #2 Diamond Buff
And like plastic, a custom option that may include two or more of the available finishes is also possible. Unlike plastics, however, LSR is much more forgiving as no ejectors are required for the removal of the parts. All LSR parts are manually pulled from the mold so you don’t need to consider ejection or retention using this process. Another bonus is gating, LSR has extremely shallow gates that are nearly undetectable after molding.
As always, please contact a Protolabs Applications Engineer at customerservice@protolabs.com or 877-479-3680 with any questions you may have.

If you have any issues getting your guide, click here to download.