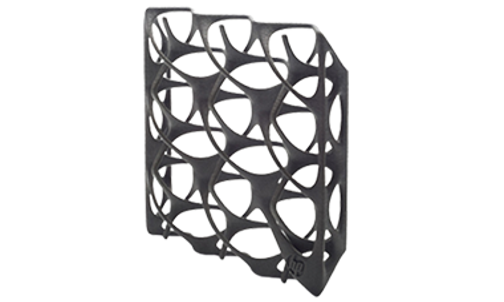
Multi Jet Fusion (MJF 3D Printing)
MJF 3D printing builds quality nylon parts suitable for rapid prototyping and production.
Certifications
ISO 9001:2015 | AS9100D
Multi Jet Fusion is an industrial 3D printing process that produces functional nylon prototypes and end-use production parts in as fast as 1 day. Final parts exhibit quality surface finishes, fine feature resolution, and more consistent mechanical properties when compared to processes like selective laser sintering.
Common applications for Multi Jet Fusion are:
- parts requiring consistent isotropic mechanical properties
- functional prototypes and end-use parts
- complex and organic geometries with fine features

Design Guidelines for Multi Jet Fusion
Our basic guidelines for Multi Jet Fusion include important design considerations to help improve part manufacturability, enhance cosmetic appearance, and reduce overall production time.
US | Metric | |
Maximum Part Size | 11.1 in. x 14.9 in. x 14.9 in | 284mm x 380mm x 380mm |
Layer Thickness | 0.00315 in. | 80 microns |
Minimum Feature Size | 0.020 in. | 0.5mm |
Wall Thickness | 0.020 in. | 0.5mm |
Tolerances: For well-designed parts, tolerances of +/- 0.012 in. (0.30mm) plus 0.1% of nominal length for each additional inch can typically be achieved. Note that tolerances may change depending on part geometry.
Warpage: Larger part sizes (>7 in.) and parts with thin features are the most susceptible to warp. We recommend maintaining a uniform thickness of 0.125 in. (3.175mm) to ensure stability.
MJF Material Options
PA 12 Black
PA 12 Black is a high tensile strength nylon. Final parts are dyed black, and they exhibit quality surface finishes and slightly more isotropic mechanical properties when compared to SLS. When more detail is required, PA 12 can achieve smaller minimum feature resolution (0.02 in) as compared to SLS materials (0.03 in). PA 12 Black is the best material option for designs that incorporate living hinges.
Primary Benefits
- Near isotropic mechanical properties
- Economical material choice
PA 12 40% Glass-Filled Black
PA 12 40% Glass-Filled Black is a 40% glass-filled nylon. Final parts are dyed black. The biggest advantage offered by this material is heat deflection at 347°F (measured at 66 psi), ranking 2nd best after PA 12 Mineral-Filled.
Primary Benefits
- Economical material choice
- Heat deflection
Compare MJF Material Properties
Material | Color | Tensile Strength | Tensile Modulus | Elongation |
---|---|---|---|---|
PA 12 Black | Black | 7.1 ksi | 276 ksi | 8.5% |
PA 12 40% Glass-Filled Black | Black | 4.35 ksi | 508 ksi | 8.5% |
Material | Color | Tensile Strength | Tensile Modulus | Elongation |
---|---|---|---|---|
PA 12 Black | Black | 49 Mpa | 1,900 Mpa | 8.5% |
PA 12 40% Glass-Filled Black | Black | 30 Mpa | 3,500 Mpa | 8.5% |
These figures are approximate and dependent on a number of factors, including but not limited to, machine and process parameters. The information provided is therefore not binding and not deemed to be certified. When performance is critical, also consider independent lab testing of additive materials or final parts.
Multi Jet Fusion Surface Finish
Standard | A bead blast removes all powder and leaves a consistent overall texture. Parts are then dyed a standard black color. |
Vapor Smoothing | Significant reduction of surface roughness from 250+ μin RA (as-printed) to 64 – 100 μin RA after smoothing. Available for PA12 Black. |
Custom | Secondary options include a primer that can be applied as well as taps and inserts. |

Our MJF 3D Printers
We use HP Jet Fusion 3D 4210 and 5210 machines that are capable of accelerated build speeds when compared to other powder-based additive manufacturing technology. The HP 3D printers produce commercial-grade parts with enhanced surface finishes and improved mechanical properties compared to other 3D printing technology.
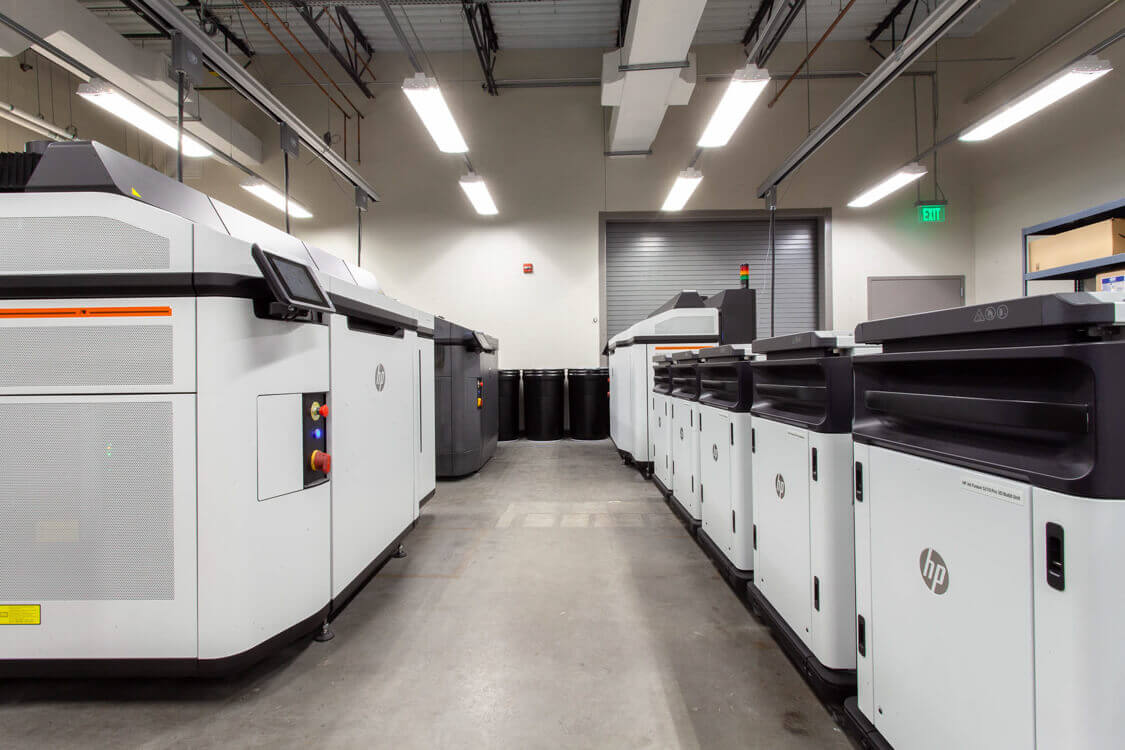
Why Use Multi Jet Fusion?
See how 3D printing with Multi Jet Fusion is ideal for functional prototypes and end-use, production parts.
How Does Multi Jet Fusion Work?
Multi Jet Fusion uses an inkjet array to selectively apply fusing and detailing agents across a bed of nylon powder, which are then fused by heating elements into a solid layer. After each layer, powder is distributed on top of the bed and the process repeats until the part is complete.
When the build finishes, the entire powder bed with the encapsulated parts is moved to a processing station where a majority of the loose powder is removed by an integrated vacuum. Parts are then bead blasted to remove any of the remaining residual powder before ultimately reaching the finishing department where they are dyed black to improve cosmetic appearance.