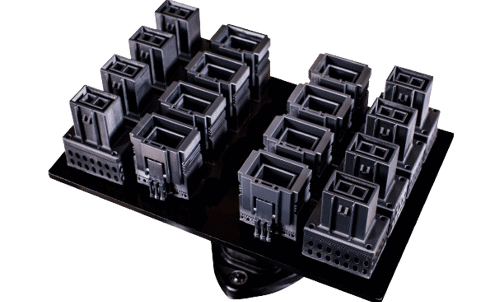
Carbon DLS 3D Printing
Get quality 3D-printed parts built from thermoset resins.
Jump to Section
→ Capabilities
→ Materials
→ Surface Finishes
→ About Carbon DLS 3D Printing
Carbon DLS (digital light synthesis) is an industrial 3D printing process that creates functional, end-use parts with mechanically isotropic properties and smooth surface finishes. You can choose from both rigid and flexible polyurethane materials to meet your application needs for high impact-resistance components.
Common application for Carbon DLS are:
- complex designs that are challenging to mold
- need for isotropic mechanical properties and smooth surface finish
- production parts in materials comparable to ABS or polycarbonate
- durable components for end use

RPU 70 Rigid Polyurethane is manufactured through Carbon’s DLS (digital light synthesis) process. It is a tough all-purpose engineering grade material that comes in black and can be categorized as an ABS-like materials. Ideal part sizes for Carbon materials are 5 in. x 5 in. x 5 in. or less.
Primary Benefits
- Tough material
- UL 94 HB flame resistance classification
Carbon FPU 50 exhibits the highest elongation of any of the 3D printing thermoset resins at 200% making it the most flexible option. Available in black, it falls under the PP-like category of 3D printing resins.
Primary Benefits
- Highest elongation properties
- Fatigue resistance
Carbon EPX 86FR is a flame-retardant resin that offers functional toughness, high strength, and long-term stability. It works well in a variety of applications that require UL 94 V-0 or FAR 25.853(a) ratings.
Primary Benefits
- Flame retardant (UL94 V-0 at 2 mm thick)
- Chemical resistance
Compare Carbon DLS Material Properties
Material | Color | Tensile Strength | Tensile Modulus | Elongation |
---|---|---|---|---|
Carbon RPU 70 | Black | 6 ksi | 245 ksi | 100% |
Carbon FPU 50 | Black | 4 ksi | 100 ksi | 200% |
Carbon EPX 86FR | Black | 13 ksi | 480 ksi | 10% |
Material | Color | Tensile Strength | Tensile Modulus | Elongation |
---|---|---|---|---|
Carbon RPU 70 | Black | 41.4 MPa | 1,690 MPa | 100% |
Carbon FPU 50 | Black | 27.6 MPa | 690 MPa | 200% |
Carbon EPX 86FR | Black | 90 MPa | 3300 MPa | 10% |
These figures are approximate and dependent on a number of factors, including but not limited to, machine and process parameters. The information provided is therefore not binding and not deemed to be certified. When performance is critical, also consider independent lab testing of additive materials or final parts.
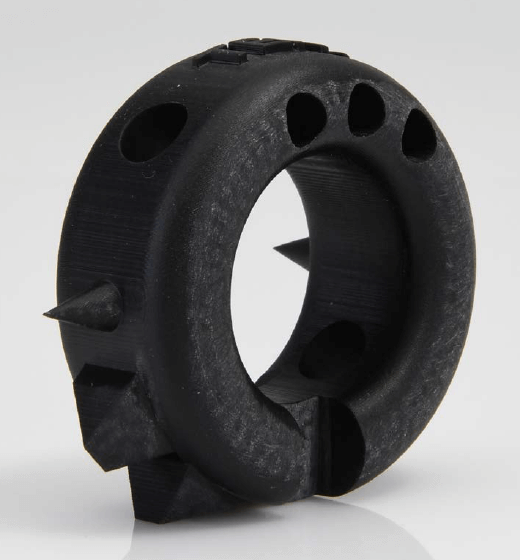
Unfinished
With unfinished, you get varying aesthetics based on build orientation. Dots or standing nibs remain evident on the bottom of the part from the support structure remnants.
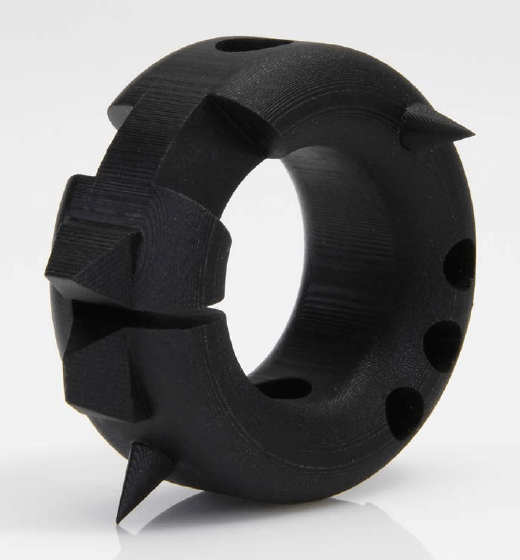
Natural Finish
With natural finishing, you get varying aesthetics based on build orientation. Standing nibs are sanded flat.
How Does Carbon DLS Work?
Carbon DLS uses CLIP (continuous liquid interface production) technology to produce parts through a photochemical process that balances light and oxygen. It works by projecting light through an oxygen-permeable window into a reservoir of UV-curable resin. As a sequence of UV images are projected, the part solidifies, and the build platform rises.
At the core of the CLIP process is a thin, liquid interface of uncured resin between the window and the printing part. Light passes through that area, curing the resin above it to form a solid part. Resin flows beneath the curing part as the print progresses, maintaining the continuous liquid interface that powers CLIP. Following the build, the 3D-printed part is baked in a forced-circulation oven where heat sets off a secondary chemical reaction that causes the materials to adapt and strengthen.