
Cleanbrace
Innovazione per l'igiene al polso, con il supporto di Protolabs
Una combinazione di design e funzionalità. Questo era l'obiettivo dei creatori di Cleanbrace, un braccialetto igienico che consente una comoda disinfezione delle mani in qualsiasi momento. Insieme al leader globale nella fabbricazione digitale, Protolabs, è ora pronto per entrare in produzione.
Avere le mani pulite è uno dei principali fondamentali di un'interazione igienica con altre persone. Naturalmente, il lavaggio regolare delle mani è considerato un comportamento educato e prudente, non solo dall'inizio della pandemia di Covid-19. A causa delle recenti circostanze e della campagna "Mani, Viso, Spazio", l'igiene corretta delle mani è diventata essenziale.
Tuttavia, non è sempre possibile effettuare l'igiene e la disinfezione delle mani in modo semplice e senza problemi. Ad esempio, potrebbe non essere possibile lavarsi le mani perché non si ha a disposizione sapone o acqua corrente ed è necessario portare con sé il disinfettante appropriato. Mentre molte persone portano con sé la mascherina, pochissime hanno sempre a portata di mano dei disinfettanti. Per i fondatori di Cleanbrace, una start-up con sede in Germania, questo è stato l'ostacolo nella battaglia contro le mani non igienizzate. Insieme al fornitore di servizi di fabbricazione Protolabs, sono stati in grado di rivoluzionare la disinfezione delle mani in pochi mesi e trasformare un braccialetto per la disinfezione di nuova concezione in un accessorio quotidiano.
Un piccolo braccialetto con un grande impatto
L'obiettivo comune dei fondatori quando hanno iniziato a lavorare a questa idea nel febbraio 2020 era quello di utilizzare i mezzi più semplici possibili per produrre un braccialetto che combinasse design, funzionalità e durata senza rischiare danni alla pelle. L'idea alla base dell'accessorio era tanto semplice quanto convincente: il disinfettante doveva essere conservato in un piccolo serbatoio ricaricabile all'interno del braccialetto ed essere erogato premendo un pulsante. Al fine di ottenere il più rapidamente possibile un prototipo funzionale, la start-up si è concentrata su singoli componenti che erano già disponibili sul mercato in questa forma. I braccialetti in silicone, utilizzati anche per noti tracker di attività, sarebbero diventati la base di Cleanbrace. Il serbatoio per il disinfettante è stato realizzato semplicemente convertendo una testa di pipetta che consente da 5 a 6 applicazioni. Questo potrebbe essere riempito utilizzando bottiglie artigianali, leggermente modificate, aventi una capacità di 30 millilitri.
IN BREVE... |
---|
Creare un dispositivo indossabile e alla moda che si raddoppia come un dispenser di disinfettante per le mani, ricaricabile.
Team dedicato istituito per garantire la fattibilita' del design: suggerimento di un sistema a due utensili per le staffe per assicurare la produzione simultanea e un approccio a due stampi a cavita' per il tappo.
Tre utensili sono stati stampati a iniezione in soli tre giorni e, grazie all'approccio produttivo di Protolabs, sono stati raggiunti volumi giornalieri di entrambi i pezzi. Dalla richiesta iniziale alla consegna completa di tutti i componenti sono passati solo 14 giorni. |
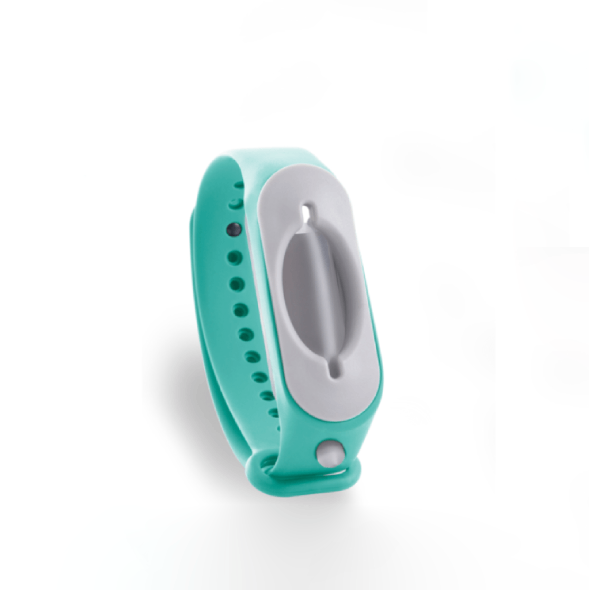
Un vantaggio importante di questi componenti è che possiedono già i requisiti principali per l'uso in un braccialetto per la disinfezione: Sono delicati sulla pelle e resistenti alle soluzioni alcoliche come i disinfettanti. Per trasformare questi singoli componenti in un braccialetto disinfettante elegante e funzionale, mancava un adattatore centrale.
Per produrre questo pezzo centrale in cui è situato il serbatoio del disinfettante, la realizzazione dei primi prototipi si è basata sulla produzione additiva. In linea con lo spirito "si può fare" che prevale nelle start-up, il team si è procurato una stampante 3D e ha iniziato a produrre i primi adattatori. “Dopo poco tempo abbiamo raggiunto i limiti di produzione con la prima stampante. Ben presto sia la risoluzione che la capacità di produzione non sono state più sufficienti per le nostre concezioni", ha commentato André Maaß, responsabile dello sviluppo di Cleanbrace. “Per questo motivo, abbiamo rapidamente acquistato la nostra piccola flotta di stampanti 3D SLA per produrre i componenti dell'adattatore. A questo punto la qualità dei componenti era già molto migliore”.
Il percorso verso la produzione in serie
Il successo di Cleanbrace con i primi prototipi rese presto necessaria un'altra modifica. Il braccialetto disinfettante che, proprio come previsto dai creatori, può essere integrato con discrezione nella vita di tutti i giorni, consente a chi lo indossa di disinfettarsi le mani. Il prototipo è stato un tale successo che la produzione dell'adattatore utilizzando la fabbricazione additiva non è stata più sufficiente. Il passo logico successivo è stato quello di passare dalla fabbricazione additiva alla produzione in serie utilizzando lo stampaggio a iniezione per produrre la parte centrale.
Dopo una breve ricerca nel mercato, i creatori hanno trovato il partner giusto per la produzione mediante stampaggio a iniezione in Protolabs, un'azienda specializzata nella produzione di prototipi e in serie che utilizza un'ampia gamma di servizi di produzione digitale, incluso lo stampaggio a iniezione. "Il nostro progetto originale per l'adattatore è stato ottimizzato in modo da realizzarlo utilizzando la fabbricazione additiva. Per consentire la produzione in serie mediante stampaggio a iniezione, abbiamo dovuto modificare nuovamente il progetto. In Protolabs abbiamo trovato un partner veramente esperto”, spiega Maaß.

“A differenza della fabbricazione additiva, la produzione mediante stampaggio a iniezione consente volumi significativamente più elevati e una fabbricazione più rapida. Ma il design dei rispettivi componenti deve essere anche fattibile con il metodo di produzione. Mentre la stampa 3D consente un'ampia libertà in termini di progettazione, con lo stampaggio a iniezione devono essere considerati gli aspetti essenziali del progetto a causa della dipendenza da utensili e stampi", spiega Julian Lietzau, Senior Marketing Manager Protolabs.
“I sottosquadri, come gli elementi costruttivi che sporgono liberamente dalla fusione, possono impedire, ad esempio, l'estrazione del componente desiderato dallo stampo”. Sono proprio questi sottosquadri e altri aspetti dell'adattatore che sono stati modificati da Cleanbrace con l'aiuto di Protolabs. Anche il servizio Design for Manufacture (DFM) di Protolabs è stato molto utile per il team dei braccialetti disinfettanti. “Poiché non ci eravamo mai occupati di stampaggio a iniezione prima, lo studio di fattibilità automatizzato di Protolabs si è rivelato molto utile. Ma abbiamo potuto imparare molto anche dalle discussioni faccia a faccia con il team", sintetizza Maaß. Dopo 14 processi di revisione e iterazioni, in totale, tutti i componenti sono stati finalmente adattati per la progettazione del nuovo adattatore ed è iniziata la produzione in serie.
Collaborazione di successo come base per un ulteriore sviluppo congiunto
La collaborazione professionale reciproca ha svolto un ruolo importante nel successo della produzione rapida in serie. "Al fine di aiutare rapidamente i nostri clienti, è importante lavorare a stretto contatto con loro e analizzare e apportare insieme tutte le modifiche al progetto", riferisce Fischer. “In Protolabs si riceve assistenza rapida e mirata. In particolare, la rapidità con cui vengono affrontati e risolti i problemi, ci ha convinto a continuare ad affidarci ai suoi servizi anche in futuro”, aggiunge Maaß.
In futuro, il braccialetto dovrebbe migliorare in modo ancora più efficace la vita quotidiana di chi lo indossa. Cleanbrace è anche lungimirante quando si tratta di rifinire i singoli componenti in post-produzione. I braccialetti disinfettanti vengono lavorati in un villaggio vicino, qui persone con una serie di disabilità assemblano le singole parti, attaccano le ricariche e confezionano il prodotto finito in modo che i braccialetti possano essere messi in vendita. Altri progetti futuri sono già in fase di pianificazione. “Per poter utilizzare Cleanbrace più a lungo, stiamo attualmente lavorando a una valvola che verrà ancorata nella sede del serbatoio. In questo modo, vogliamo gestire meglio l'effetto dell'evaporazione e semplificare il dosaggio", spiega Maaß. Perché si spera che l'igiene delle mani sia ancora una priorità assoluta, anche dopo la pandemia, e quale modo migliore per soddisfarla che indossare un elegante braccialetto igienizzante.
“Poiché non ci eravamo mai occupati di stampaggio a iniezione prima, lo studio di fattibilità automatizzato di Protolabs si è rivelato molto utile. Ma abbiamo potuto imparare molto anche dalle discussioni faccia a faccia con il team.”
Citazione cliente
"In Protolabs si riceve assistenza rapida e mirata. In particolare, la rapidità con cui vengono affrontati e risolti i problemi, ci ha convinto a continuare ad affidarci ai suoi servizi anche in futuro.”
André Maaß, CTO & Co-Founder a Cleanbrace
Volete saperne di più su come Protolabs supporta aziende simili con prototipi lavorati a CNC, stampati a iniezione o in 3D?
Date un'occhiata al nostro case study su The Boxing Hand Grenade, un dispositivo indossabile che migliora l'integrità strutturale delle mani dei pugili all'interno dei guanti e delle fasce tradizionali.