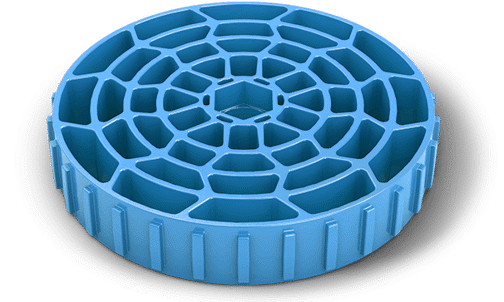
Kontrola jakości i standardy formowania wtryskowego
Jak wykorzystujemy procesy cyfrowe, formowanie naukowe i raporty z kontroli, aby konsekwentnie wytwarzać części wysokiej jakości
- Analiza produkcji
- Formowanie naukowe i kwalifikacja procesu
- Krytyczne dla raportowania jakości
- Specyfikacje GD&T
Certyfikaty
ISO 9001:2015
Konsekwentne wytwarzanie wysokiej jakości wyprasek wymaga połączenia inspekcji i kontroli w trakcie procesu oraz weryfikacji wymiarów po zakończeniu produkcji. Projektowanie części z uwzględnieniem procesu produkcyjnego jest pierwszym krokiem do zapewnienia wysokiej jakości wypraski. Dlatego do każdej wyceny formowania wtryskowego dołączamy analizę projektu. Uzyskanie analizy produkcyjnej na wczesnym etapie procesu formowania może pomóc w wyeliminowaniu kosztownych przeprojektowań, skróceniu czasu opracowywania i wyeliminowaniu domysłów z procesu formowania. Przed złożeniem zamówienia dowiesz się, czy Twój projekt wymaga jakichkolwiek zmian, uzyskasz zalecenia dotyczące poprawy jego formowalności i uzyskasz inne przydatne informacje, aby zrozumieć, w jaki sposób zostanie uformowana ostateczna część.
Analiza projektu dla produkcji (DFM)
Prosząc o wycenę za pośrednictwem naszego internetowego systemu wycen, otrzymasz analizę produkcji i wycenę. Pierwszy krok w cyfrowym procesie produkcyjnym może umożliwić klientom jednoczesne testowanie wielu projektów, a tym samym szybsze dotarcie do akceptacji projektu, co oszczędza czas w cyklu rozwoju.
W jaki sposób nasza analiza produkcyjna może poprawić jakość części formowanych wtryskowo:
- identyfikuje grube ścianki
- Identyfikuje elementy o niewystarczającym nachyleniu
- Wybierz lokalizację bramki
- Wybierz położenie kołka wypychacza
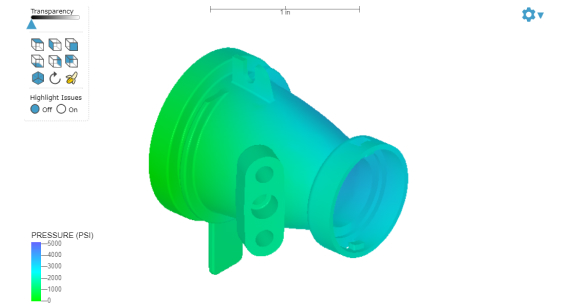
Wsparcie projektowe ze strony ekspertów w dziedzinie formowania wtryskowego
Konsultacyjne usługi projektowe: współpracuj bezpośrednio z inżynierem zajmującym się formowaniem wtryskowym, aby poprawić formowalność swojego projektu. Pomyśl o tym jak o posiadaniu własnego konsultanta ds. formowania wtryskowego w swoim zespole. W trakcie tego procesu nasz inżynier ds. zastosowań będzie z Tobą współpracować, aby zrozumieć cele Twojego projektu, przejrzeć analizę produkcji dostarczoną w ofercie online i wprowadzić zmiany w pliku 3D CAD.
Proponowana wersja Protolabs (PPR): W niektórych przypadkach możemy dostarczyć Ci drugi model CAD — zwany Proponowaną wersją Protolabs (PPR). Jest to nowy plik CAD z już wprowadzonymi zmianami. Poprawiony model może być użyty natychmiast lub można przenieść modyfikacje do oryginalnego modelu. Po analizie DFM, a w niektórych przypadkach PPR, gdy część zostanie zatwierdzona, Protolabs przechodzi do ostatniego etapu przed rzeczywistą produkcją – przygotowania cyfrowego.

Naukowe formowanie: Konsekwentna dostawa wysokiej jakości części
Wykorzystujemy naukowy proces formowania wtryskowego, zwany również procesem rozdzielonym, aby produkować spójne i powtarzalne części dla naszych klientów z branży formowania wtryskowego. Opracowujemy, optymalizujemy i udokumentowujemy proces idealnego przygotowania dla każdego projektu formowania wtryskowego, aby ten sam proces i parametry były stosowane przy każdym uruchomieniu formy klienta. Wszelkie modyfikacje są dokumentowane, aby zapewnić możliwość śledzenia wszystkich uruchomień formowania.
Bez względu na to, czy część zostanie ponownie wykonana na tej samej maszynie wtryskowej czy na innej, czy też będzie zamówiona po kilku miesiącach, naukowe formowanie zapewnia spójność zarówno między częściami, jak i między kolejnymi produkcjami, poprzez udokumentowanie dokładnego procesu ustawienia narzędzia, który spełnia wymagania dotyczące żywicy i wymiarów.
Przestrzegając tych najlepszych praktyk branżowych, możemy zapewnić, że każda część ma takie same właściwości jak poprzednia, kontrolując napełnianie, zagęszczanie i utrzymywanie ciśnienia. Daje to naszym klientom dwa główne korzyści: bardziej jednorodne i wysokiej jakości części oraz raporty inspekcyjne do potwierdzenia ich jakości.
Nasz raport dotyczący parametrów krytycznych dla jakości (CTQ)
Raport dotyczący parametrów krytycznych dla jakości (CTQ) to funkcja naszego procesu kontroli, która pozwala zidentyfikować do pięciu krytycznych cech lub wymiarów ważnych dla funkcjonalności i wydajności części. Jest on dołączany do wszystkich zamówień na formy produkcyjne na żądanie. Klienci otrzymują zarówno raport z kontroli pierwszej części, jak i raport dotyczący wydajności 30 sztuk. Mówiąc najprościej, nasz proces CTQ pozwala zidentyfikować aspekty, które są najbardziej krytyczne dla Twoich części i te, które mają znaczenie drugorzędne, dzięki czemu zamawiane części są zgodne z Twoim modelem.
Nasz raport CTQ zapewnia:
- Informacje zwrotne na temat jakości w trakcie procesu na prasie bez wpływu na czas realizacji
- Redukcję kosztów i czasu dzięki wyeliminowaniu pomiarów wewnętrznych
- Raport dotyczący wymiarowy do kwalifikacji próbek
- Wnioski dotyczące konstrukcji i efektywności materiałów dla obecnych i przyszłych iteracji
- Poprawioną dokładność części i zgodność wymiarową w zakresie wymiarów krytycznych określonych przez klienta
W ramach naszego procesu CTQ oferujemy następujące funkcje GD&T:
- Pozycja
- Płaskość
- Prostość
- Okrągłość
- Równoległość
- Prostopadłość
- Współśrodkowość
- Walcowość
Jak mierzone są wymiary części?
Jako wiodący w branży partner produkcyjny używamy standardowych współrzędnościowych maszyn pomiarowych (CMM) — suwmiarki i mierniki kołków. Tym, co wyróżnia nasz proces, jest to, że zastosowaliśmy opatentowaną technologię automatyzacji w naszych maszynach współrzędnościowych, aby umożliwić kontrolę w trakcie procesu bez dodatkowych kosztów i wydłużania czasu realizacji.
Części są mierzone w równych odstępach czasu n/30, gdzie n = całkowita ilość zamówionych części. Wraz z danymi pomiarowymi każdej części, raport zdolności będzie również zawierał również średnią pomiaru, odchylenie standardowe i wartość wskaźnika zdolności procesu (Cpk) dla wszystkich krytycznych wymiarów.
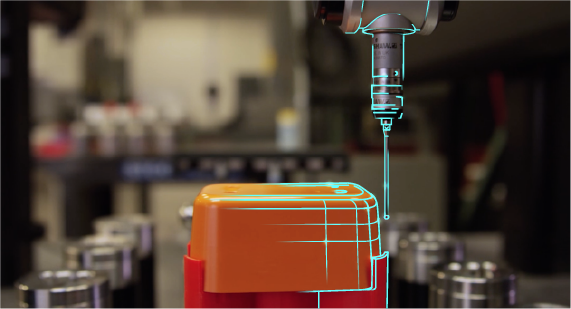
Dodatkowe możliwości jakościowe
Proces zatwierdzania części do produkcji (PPAP)
PPAP to proces kontroli jakości, zwykle stosowany w przemyśle motoryzacyjnym. Metodę stosuje się do sprawdzenia, czy proces produkcyjny może wielokrotnie wytwarzać wysokiej jakości części. Kontrola PPAP składa się z 18 elementów, od zatwierdzenia przez klienta po produkcję części próbnej.