Using Lattice Structures in 3D Printing for Strength and Lightweighting
A less is more philosophy in designing printed part interiors can pay off in time, money, and quality
La impresión 3D es un proceso singular en su capacidad de producir piezas con estructuras de celosía o malla. Por varias razones, las celosías son una herramienta muy versátil para los ingenieros. Las estructuras de celosía aumentan la ligereza y la resistencia de las piezas. También ayudan a reducir su volumen, con la consiguiente reducción de los defectos superficiales o la acumulación excesiva de tensiones. Un menor volumen conlleva la ventaja añadida de ahorrar tiempo de fabricación y, por tanto, de ahorrar costes. El área de superficie adicional de las estructuras de celosía también se puede utilizar en aplicaciones de transferencia de calor. Sigue leyendo para aprender a usar las estructuras de celosía en tus piezas impresas en 3D sin complicarte la vida.

Estructuras de celosía para las tecnologías de Protolabs
Con las tecnologías internas que ofrecemos, las piezas se fabrican rodeadas de materia prima, ya sea resina o polvo. Por lo tanto, las estructuras de celosía no se pueden envolver por completo. Las piezas requerirán agujeros de acceso para que la materia prima pueda extraerse por completo. Esto contrasta con el modelado por deposición fundida (FDM) —una tecnología aditiva basada en filamentos—, en la que las piezas están rodeadas de aire durante la fabricación, dejando que las paredes externas de la pieza encierren la celosía interna.
El uso de estructuras de celosía con tecnologías de impresión 3D más avanzadas basadas en resinas y polvos sigue siendo una realidad con algunas reservas:
Tecnologías con estructuras de soporte
La estereolitografía (SLA) es una tecnología basada en resina que requiere soporte durante la impresión. Para estas tecnologías, preferimos contar con algunos agujeros de drenaje para limpiar la resina no endurecida de la pieza antes del endurecimiento por UV posterior. Si queda algún resto de resina sin endurecer, se solidificará durante el proceso de endurecimiento posterior. Si es necesario que la celosía esté completamente cerrada, podemos agregar agujeros de drenaje para la fabricación y la limpieza de las piezas, y tapar después los agujeros antes del envío. Utiliza el campo Instrucciones especiales de tu presupuesto para solicitar que añadamos agujeros de drenaje y tapones, e indícanos si tienes una ubicación preferida para estas características.
El sinterizado directo de metal por láser (DMLS) es una tecnología de polvo para metal que también requiere estructuras de soporte. A diferencia de nuestros plásticos basados en polvo, el polvo de metal no se adhiere a las piezas. El polvo fluye libremente, como la arena, y facilita mucho la limpieza de las cavidades internas. También tenemos una máquina de eliminación de polvo que sacude y hace vibrar las piezas para extraer el polvo de los canales internos complejos. Sin embargo, cualquier polvo que quede dentro de la pieza se solidificará durante el ciclo de liberación de tensiones. Si es necesario vaciar un canal o una cavidad, asegúrate de que haya suficientes lugares para drenar el polvo.
Tecnologías sin soporte
El sinterizado selectivo por láser (SLS) y la Multi Jet Fusion (MJF) utilizan materiales plásticos a base de polvo. Ambos se basan en polvo parcialmente sinterizado o parcialmente fundido para sostener las piezas durante la fabricación, eliminando la necesidad de estructuras de soporte adicionales. Esto significa que el polvo que rodea las piezas se endurece como barro seco. Usamos aire comprimido para eliminar el polvo después de la fabricación. Sin embargo, necesitamos disponer de visión directa al polvo para eliminarlo de manera efectiva. Aunque el aire se arremolina en el interior de la cavidad, solo se elimina el polvo situado directamente ante la boquilla de aire. Debido a esto, las estructuras de celosía para SLS y MJF deben diseñarse con muchos puntos de acceso para limpiar el polvo.
A continuación se muestran ejemplos de piezas con acceso cada vez mayor para limpiar el polvo parcialmente sinterizado/fundido. En el primer ejemplo, a la izquierda, se puede eliminar muy poco polvo. El polvo se limpiará en la zona de alrededor de la abertura, pero las esquinas más alejadas de la pieza acabarán llenas de polvo. El ejemplo central es mejor, ya hay un acceso mucho mayor para soplar el polvo. Sin embargo, es posible que quede algo de polvo en la parte posterior de la pieza en las áreas más difíciles de alcanzar. El último ejemplo, a la derecha, es ideal; hay mucho acceso para eliminar el polvo y podemos realizar la eliminación del polvo desde ambos lados.
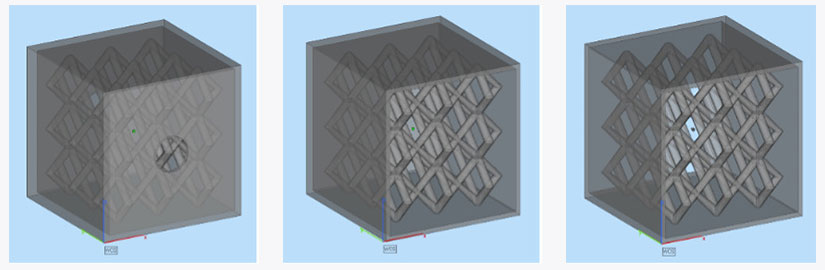
Es importante añadir elementos de diseño que faciliten la eliminación del exceso de polvo de sus piezas. El ejemplo de la derecha es el mejor.
Cómo diseñar tu celosía
Todos los modelos que recibimos se fabrican 100 % sólidos (salvo que nos preocupe la deformación): no aplicamos relleno antes de fabricarlos. Antes de enviar la pieza a nuestra web, te pedimos que modeles cualquier estructura de celosía en la pieza. A continuación se incluyen algunas pautas sobre cómo diseñar estructuras de celosía que no atrapen materia prima ni requieran soportes inaccesibles.
Los dos obstáculos principales para una celosía sin estructuras de soporte son las distancias entre puentes y el ángulo desde la placa de fabricación. Las tecnologías SLS y MJF ofrecen la mayor libertad de diseño en lo que respecta a la estructura de soporte. La celosía ideal para esta tecnología es relativamente abierta, de modo que haya suficiente acceso para soplar el polvo sin sinterizar/fundir.
Como la SLA puede abarcar distancias mucho mayores sin necesidad de estructuras de soporte, la mayoría de los diseños de celosía carecen de dichas estructuras. Si es necesario cerrar completamente la celosía, podemos agregar agujeros de drenaje a la pieza para la fabricación y luego taparlos con el mismo material después de quitar la resina sin endurecer del interior. Si deseas seguir este método, puedes solicitarlo en el campo Instrucciones especiales en tu presupuesto e indicarnos en qué superficies deseas los tapones.
DMLS es la tecnología más complicada para diseñar estructuras de celosía, ya que solo puede abarcar unos 2 mm antes de requerir estructuras de soporte. Las distancias entre puentes y los ángulos sin estructura de soporte desempeñan un papel mucho más importante para evitar soportes dentro de una celosía
Pautas para características sin estructuras de soporte
|
Puente máximo |
Ángulo mínimo (grados) |
Espesor de elemento de celosía recomendado |
SLA |
0.300” (7.62mm) |
45 |
0.030 in. (0.76mm) |
DMLS |
0.080” (2.03mm) |
45* |
0.030 in. (0.76mm) High Res 0.050 in. (1.27mm) Normal Res |
SLS and MJF |
n/a |
n/a |
0.125 in. (3.16mm) |
Los siguientes seis ejemplos presentan diferentes tipos de celosías. Ninguno de ellos necesita estructura de soporte en SLA debido a las cortas distancias entre puentes. Sin embargo, solo algunos de estos ejemplos no necesitarían dicha estructura en DMLS. Sigue leyendo para saber qué celosías necesitan soportes en DMLS y por qué. Los elementos en naranja son áreas que requieren una estructura de soporte. Es importante destacar que, si bien es posible que podamos eliminar estructuras de soporte en los bordes exteriores de una celosía, no podremos eliminarlas en el centro de la celosía
¿Cuándo la longitud entre puentes requiere soportes?
En ambos casos, las áreas resaltadas necesitan soporte porque la distancia entre puentes supera los 2 mm. Los soportes adecuados se muestran en las versiones del extremo derecho de cada pieza.
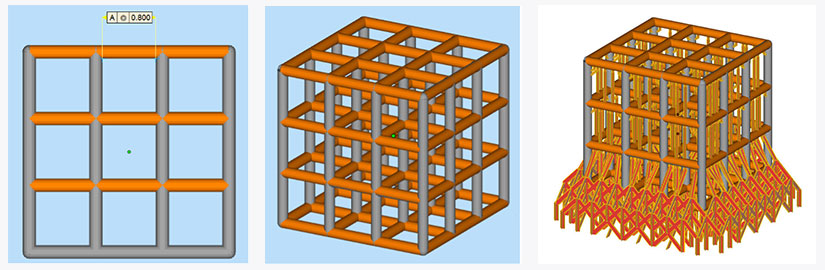
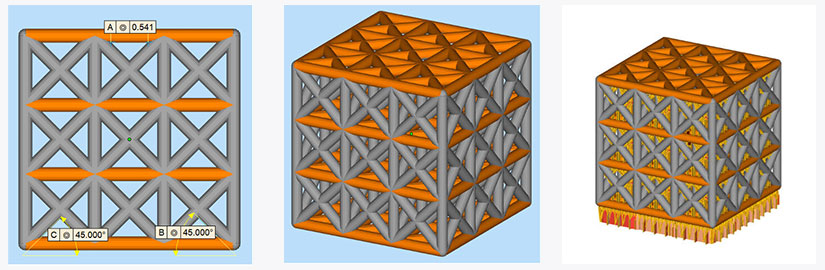
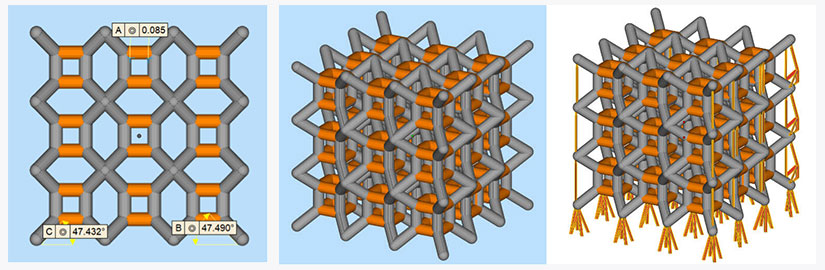
Trabajar con salientes y estructuras de soporte
Las zonas resaltadas necesitan soportes porque sobresalen en un ángulo inferior a 45 grados con respecto a la placa de fabricación. Se consideran salientes, no puentes, porque cada lado conecta de nuevo con la pieza a una altura Z diferente. Los otros elementos no requieren soportes porque sobresalen en un ángulo elevado.
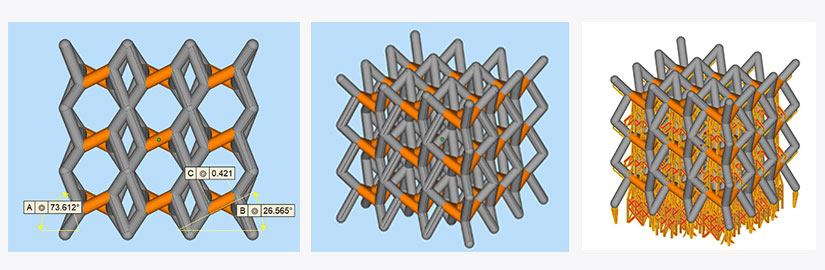
Los ángulos elevados ayudan a simplificar las estructuras de celosía
Los ejemplos de celosía siguientes no necesitan estructura de soporte porque todos los elementos sobresalen en un ángulo de ≥45 grados

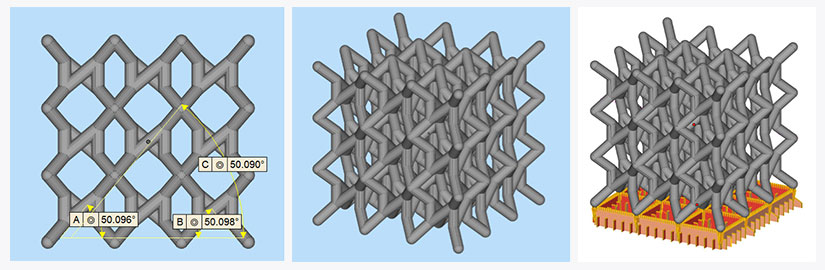
Garantizar un acabado resistente de la celosía
Los bordes de la celosía también deben tenerse en cuenta porque garantizan la integridad de la pieza. Incluso una celosía sin soportes puede requerir algunas estructuras de soporte donde se una con una sección sólida de la pieza. La celosía que se muestra a la izquierda no tiene soportes. Sin embargo, en el techo de la pieza, la distancia entre puentes es demasiado larga, y estas zonas necesitarán soportes.
Una forma de evitar las estructuras de soporte es hacer que el área entre la parte superior de la celosía y la pared de la pieza sea sólida, como se muestra a continuación a la derecha. Alternativamente, si algunas estructuras de soporte son aceptables, podemos fabricar la pieza tal como está.
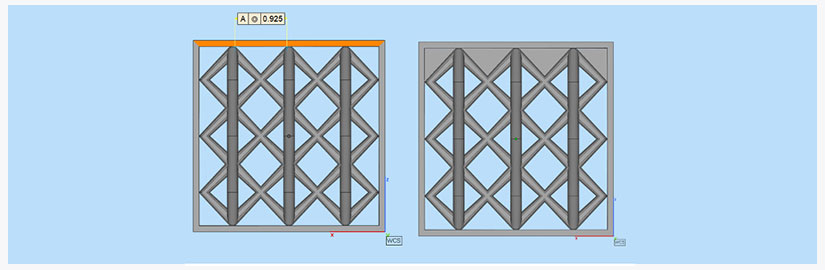
Si la estructura de celosía no termina en una pared, como en el ejemplo anterior, la celosía debe terminar de la forma más limpia posible. En el siguiente ejemplo, el lado izquierdo de la celosía termina de tal manera que algunos elementos necesitarán soportes. La imagen de la izquierda muestra una sección transversal que representa el aspecto que tendrá esta pieza a medida que crezca. Observa que hay cuatro islas, en naranja, que crecen de forma flotante, en lugar de crecer fuera de un elemento existente. Cualquier elemento que crezca de esta manera requerirá soporte. Los cuadros en color naranja de la imagen de la derecha muestran dónde estarán los soportes en esta pieza si se fabrica tal como está. Si bien se podrá acceder a estos soportes, existe el riesgo de que los elementos finos de la celosía se doblen o se rompan como parte del proceso de extracción del soporte. Lo ideal sería que la celosía terminara de forma que no hubiera estas islas, como en el borde derecho de la imagen inferior.
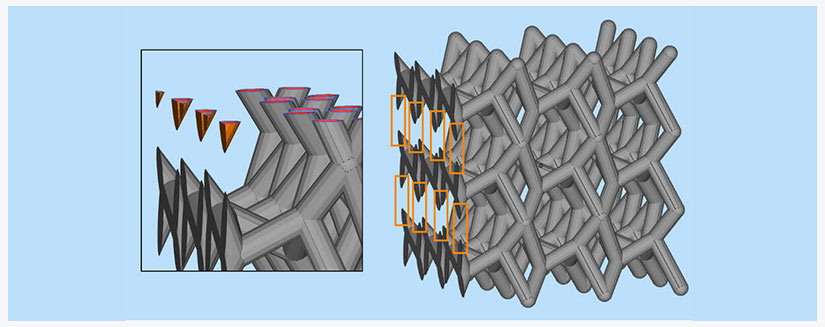

Celosía giroidal
Las celosías giroidales son más complejas, pero ofrecen ventajas únicas. Tienen propiedades casi isotrópicas y una buena relación entre resistencia y densidad del enrejado. Esto significa que el uso de celosías giroidales puede reducir el volumen de material, el tiempo de fabricación y el coste. Sin embargo, son más difíciles de llevar a la práctica sin que surjan inconvenientes como soportes atrapados o polvo.
Tecnologías con estructuras de soporte
Para SLA y DMLS, el primer obstáculo es evitar los soportes internos. Vistas lateralmente, podemos entender las celosías giroidales como canales en los que se recortan las paredes. Para evitar soportes internos en el interior de la celosía, el diámetro del canal debe estar dentro del diámetro máximo para canales sin estructuras de soporte.
Con una celosía giroidal, la resolución del archivo también es importante. Si la resolución del archivo es baja y hay muchas facetas gruesas, el facetado puede causar artefactos afilados que crecerán en forma de islas y requerirán soportes. En los dos primeros ejemplos que se muestran a continuación, la resolución del archivo es suficiente. Sin embargo, en el último ejemplo, la resolución del archivo es muy baja y es probable que los ángulos más agudos provoquen el crecimiento de soportes en alguna parte del entramado. Con las celosías giroidales, la complejidad hace que sea difícil revisar manualmente el archivo e identificar áreas que requieren soportes que no los tienen. Cuanto menor sea la resolución del archivo, mayor será la posibilidad de que las áreas con soporte insuficiente causen problemas de fabricación.
|
Canal máximo sin estructura de soporte |
SLA |
1.00 in. (25.4mm) |
DMLS |
0.236 in. (6.00mm) |
SLS and MJF |
n/a |
Por otro lado, si la resolución del archivo es demasiado alta, el tamaño del archivo será extremadamente grande y puede ser difícil de preparar y dividir. Por consiguiente, las celosías giroidales funcionan mejor para piezas pequeñas o secciones pequeñas de piezas, de modo que el tamaño del archivo no supere lo que puede manejar nuestro software de preparación y corte. Consulta esta sugerencia de diseño para obtener más información sobre la resolución de los archivos STL.
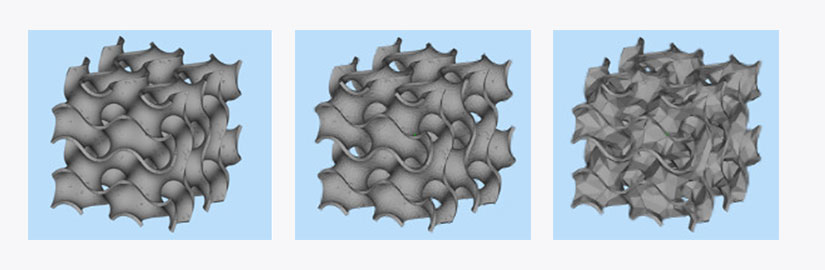
Ejemplos de estructuras giroidales y cómo la resolución afecta a la fabricación.
Tecnologías sin soporte
Para nuestras tecnologías sin soporte, SLS y MJF, la celosía giroidal ideal sería una de baja densidad. Puesto que necesitamos visión directa a todas las zonas para limpiar completamente el polvo, cualquier celosía giroidal presentará problemas para eliminar el polvo y habrá riesgo de que quede algo. Dicho esto, cuanto más densa sea la celosía, más polvo residual habrá.
Diámetro del canal y estructuras de soporte
En este primer ejemplo, toda la celosía requiere soportes en DMLS porque el diámetro del canal es superior a 6 mm.
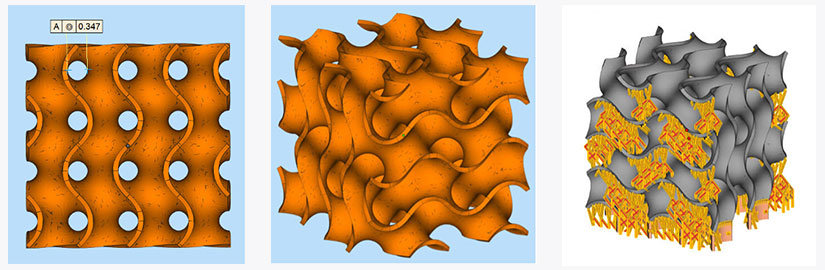
Esta celosía, sin embargo, no necesita estructura de soporte porque el diámetro del canal es inferior a 6 mm.
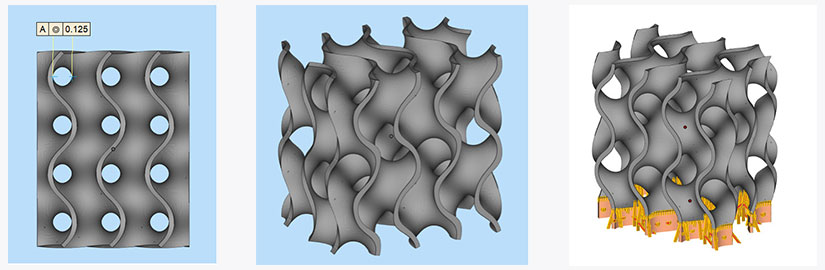

Garantizar un acabado correcto de las celosías giroidales
Como ocurre con otros tipos de celosías, la forma en que termine la celosía giroidal puede determinar el éxito de la fabricación. Lo ideal es que una celosía giroidal esté rodeada de paredes sólidas para que, a medida que crezca, no termine en un elemento que requiera estructuras de soporte. La pieza inferior izquierda que se muestra a continuación tiene la celosía rodeada de muros por los cuatro lados, que ayudarán a sostenerla. En la segunda pieza, la celosía termina sin el apoyo de una pared sólida. Como la celosía de la segunda pieza termina en ángulos poco profundos, los bordes de las celosías necesitarán estructuras de soporte que tal vez no podamos eliminar.
Si la celosía debe terminar sin una pared sólida, el acabado de los bordes debe realizarse sin estructuras de soporte. La primera imagen siguiente muestra un lado de la celosía que termina en lugares con paredes poco inclinadas que requerirán estructuras de soporte. Sin embargo, la celosía de la segunda imagen termina de forma que todos los ángulos son de 45 grados o más desde la placa de fabricación. La segunda celosía no necesitará soportes y se fabricará mucho mejor.
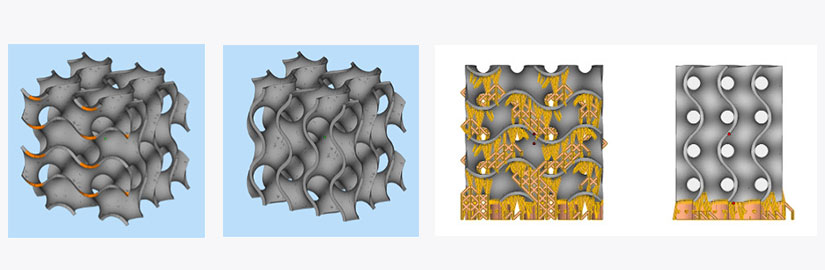
Recursos adicionales
Si necesitas más ayuda, tienes a tu disposición los siguientes recursos:
- Habla con tu gestor de cuentas para concertar una revisión del diseño con uno de nuestros ingenieros de aplicaciones 3DP.
-
Pantalla característica de un análisis de fabricación.
- Escríbenos a [email protected]
- Llámanos al +34 932 711 332