
7 errori da evitare nel design di componenti da stampare in 3D
Migliorare il design dei componenti rispondendo alle sfide della fabbricazione additiva quali l’osservanza delle dimensioni minime degli elementi, evitando la deformazione e adottando altre precauzioni
Progettisti e ingegneri si avvalgono sempre più della stampa 3D industriale (fabbricazione additiva) per la realizzazione di prototipi di qualità elevata e componenti di produzione destinati all’utilizzo finale. E con la stampa 3D non c’è che l’imbarazzo della scelta. In Protolabs offriamo cinque metodi additivi: sinterizzazione laser diretta dei metalli (DMLS), stereolitografia (SLA), sinterizzazione laser selettiva (SLS), Multi Jet Fusion (MJF) e PolyJet.
Abbiamo pertanto chiesto ai nostri Application Engineers di compilare un elenco di aspetti problematici che incontrano frequentemente nei modelli CAD destinati alla stampa 3D e di fornire suggerimenti per risolverli. Ecco i sette errori comuni di evitare che vi aiuteranno a migliorare la realizzabilità dei vostri design da stampare in 3D e a ridurre i tempi di lavorazione.
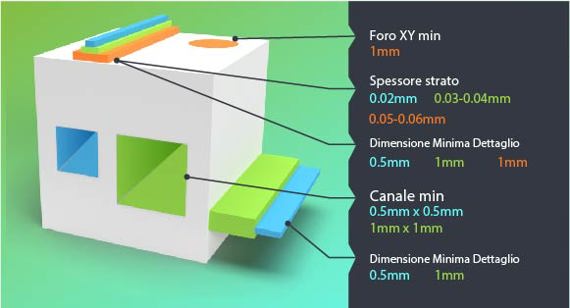
1. Con determinati processi e materiali evitate elementi di dimensioni troppo grandi o troppo piccole
Questo è il principale ostacolo che incontrerete con diversi metodi additivi. Ricordate che alcune geometrie consentono di fare delle eccezioni; pertanto, vi invitiamo a consultarvi con uno dei nostri Application Engineers per qualsiasi vostra domanda.
DMLS
Lo spessore delle pareti nella stampa 3D dei metalli può essere difficile da gestire e varia a seconda della scelta del materiale metallico, dell’orientamento e della risoluzione. Il cobalto-cromo, il titanio e l’acciaio inossidabile richiedono uno spessore di parete di almeno 0,5 mm. Per tutti gli altri metalli, lo spessore di parete è di 1 mm.
Per altri metalli, le dimensioni minime assolute degli elementi (per quelli positivi, solidi o densi) sono di 0,2 mm - 0,3 mm per quanto riguarda lo spessore e di 0,5 mm per quanto riguarda l’altezza. Queste rappresentano le dimensioni minime degli elementi sui quali il laser disegnerà. Ciò non significa che ogni elemento disegnato con questo spessore sarà formato o resisterà alla post-lavorazione. Questo valore minimo si applica agli elementi ben progettati che rientrano nel piano di disegno (X, Y) come le pareti o gli elementi verticali.
La possibilità di praticare fori dipende dalla loro profondità e risoluzione. In genere, i fori di diametro inferiore a 1 mm tendono a sigillarsi o a risultare più piccoli rispetto al design. Per i fori di diametro inferiore a 1 mm suggeriamo di prendere in considerazione l’alta risoluzione.
Ingrandire gli elementi |
|||
---|---|---|---|
DMLS | SLA | ||
Dimensioni minime: Elementi positivi |
Micro Risoluzione (MR): Alta Risoluzione (AR): |
Micro Risoluzione (MR): |
|
Dimensioni minime: Spazi negativi (fori, fessure, canali, spazi aperti) |
0.5mm |
Fori: Canali: Fessure: |
SLA
La precisione dimensionale e l’alta qualità della superficie ottenute con la SLA rendono questo processo ideale per i progetti che richiedono una elevata accuratezza di riproduzione. Tuttavia, l’orientamento gioca un ruolo in termini di formazione degli elementi. La conoscenza delle dimensioni minime in base all’orientamento di realizzazione vi aiuteranno a progettare pezzi migliori destinati alla fabbricazione additiva.
I fori con un diametro inferiore a 0,5 mm tenderanno a sigillarsi durante la realizzazione. I canali interni devono essere di almeno 0,5 mm e le fessure di 0,4 mm. Se un modello richiede fori inferiori a 0,5 mm, o una fessura inferiore a 0,4 mm, prendete in considerazione il nostro materiale da risoluzione microscopica, offerto nelle versioni MicroFine™ Green e Grey. Nella SLA offriamo tre risoluzioni: standard, alta e microscopica (MR).
Quali sono le dimensioni minime degli elementi per la SLA? La tecnologia impiegata dalla SLA offre una delle migliori risoluzioni dell’industria per quanto riguarda gli elementi. Si possono infatti formare elementi di soli 0,07 mm in MR, di 0,13 mm in AR e di 0,25 mm in RS. Questa risoluzione si può ottenere soltanto nel piano di disegno (x, y) e inerisce elementi quali pareti supportate, elementi incassati e in rilievo (pensate agli stampi microscopici stampati 3D). Lo spessore delle pareti è diverso nella direzione di realizzazione quando le dimensioni minime degli elementi sono di 0,4 mm sia in RS che in AR e di 0,2 mm in MR sul piano Z. Ricordate che tanto più lunghi/più alti sono gli elementi sottili tanto maggiore dovrà essere il loro spessore per resistere alla post-lavorazione.
Nylon stampati in 3D
Per i pezzi in nylon stampati in 3D elenchiamo di seguito tre importanti ostacoli che riscontriamo spesso e che devono essere corretti nel modello CAD. Le geometrie più comuni che possono rivelarsi problematiche includono fori ciechi, filettature e aree in cui le rastremazioni e i diametri interni sono troppo vicini alle pareti esterne.
Spessore di parete: Indica lo spessore in qualsiasi direzione sulle pareti o geometrie del pezzo. Lo spessore di parete minimo consentito è di 0,8 mm con la SLS e di 0,5 mm con MJF.
Spazi aperti: Indicano la distanza tra due elementi di dettaglio. Gli spazi aperti meritano attenzione durante la progettazione di componenti in nylon da realizzare mediante stampa 3D perché il processo di sinterizzazione potrebbe provocare l'unione di spazi non conformi ai requisiti minimi. Gli spazi aperti dovrebbero avere una dimensione minima di 0,8 mm sia per la SLS che per MJF.
Bordi sottili: Pensate ai design che prevedono un elemento incassato, come un foro contro alesato. All’estremità distale del foro le dimensioni potrebbero essere inferiori a quelle minime per l’elemento. Questo potrebbe dare origine a un elemento più corto o rotondo non correttamente formato.

2. Evitate file in formato STL a bassa risoluzione
In alcuni casi, riceviamo file STL a bassa risoluzione che causano sfaccettature grezze (superfici simili a quelle di una pietra preziosa). I file a bassa risoluzione con sfaccettature grezze non impediranno da parte nostra la fabbricazione del pezzo ma potrebbero influire sul suo aspetto estetico. La maggior parte dei software di modellazione CAD vi permette di regolare la risoluzione del file STL nelle impostazioni di esportazione. Di solito, la riduzione della tolleranza produce il risultato maggiore e migliora la risoluzione. Raccomandiamo di verificare che i vostri file STL siano in alta risoluzione (ma non così grandi da non poter essere caricati o manipolati, 100 MB o meno) o inviate un file STP/STEP che possiamo convertito in formato STL.
Oltre ai file STL, accettiamo file originali in SolidWorks (.sldprt) o ProE (.prt) così come modelli solidi in 3D CAD provenienti da altri sistemi di output CAD in formato IGES (.igs), STEP (.stp), ACIS (.sat) o Parasolid (.x_t o .x_b).
3. Impedire la deformazione dei pezzi da realizzare con SLS e MJF
I processi di stampa su letto di polvere, come SLS e MJF, utilizzano il calore per sinterizzare la polvere compattandola in un composto solido. Il calore utilizzato per la formazione dei pezzi può tuttavia provocare deformazioni indesiderate. Ancora una volta, le dimensioni e lo spessore complessivo del pezzo hanno un impatto determinante sul potenziale di deformazione. Tanto più grande è il pezzo -200 mm e dimensioni superiori sono particolarmente difficili da lavorare - tanto maggiori saranno le probabilità che si deformi. Il potenziale di deformazione sarà inoltre più pronunciato nei pezzi sottili e negli elementi le cui dimensioni si avvicinano al requisito minimo previsto. Se temete che il vostro design possa essere soggetto a deformazione, raccomandiamo quattro possibili soluzioni.
- Le dimensioni del pezzo dovrebbero essere prossime a uno spessore uniforme di 3 mm per garantirne la stabilità.
- Scegliete un nylon rinforzato in vetro , come il PA 12, rinforzato in vetro al 40% (materiale per SLS).
- Se il pezzo ha dimensioni superiori ai 200 mm e ritenete che si possa deformare, un’altra possibilità consiste nell’utilizzare un materiale in nylon non rinforzato con la nostra macchina per SLS la cui ampia camera di sinterizzazione è in grado di gestire pezzi con dimensioni fino a 676 mm x 367 mm x 564 mm.
- Un’ultima opzione a vostra disposizione consiste nello stampare il pezzo con le nostre macchine da stereolitografia (SLA) per formati più grandi, in grado di realizzare pezzi con dimensioni fino a 736 mm x 635 mm x 533 mm.
4. Quando vi avvalete della SLS o della MJF evitate il ritiro differenziale
Analogamente alla deformazione, il ritiro differenziale si può verificare quando il materiale non è distribuito in modo uniforme nei pezzi. Se un lato presenta uno spessore notevolmente più pronunciato rispetto al resto del pezzo, il raffreddamento potrebbe infatti avvenire in tempi diversi. Ciò significa che le aree più spesse si raffredderanno molto più lentamente rispetto a quelle più sottili, provocando talvolta un restringimento indesiderato del pezzo.
Se è necessario introdurre dettagli più spessi, raccomandiamo di incavare tali elementi mantenendo uno spessore massimo di 3 mm. Se possibile, fate in modo che lo spessore complessivo del pezzo corrisponda allo spessore del suo elemento più grande.

5. Evitate sporgenze di grandi dimensioni nei pezzi da sottoporre a DMLS
La stampa 3D dei metalli presenta i propri problemi specifici per quanto attiene al design, eppure un ostacolo comune che si incontra frequentemente sono le sporgenze. A differenza degli angoli autoportanti che formano una pendenza uniforme nel design, le sporgenze rappresentano repentini cambiamenti nella geometria di un pezzo. Rispetto ad altre tecnologie di stampa 3d come la stereolitografia e la sinterizzazione laser selettiva, la DMLS è piuttosto limitata quando si tratta di supportare le sporgenze. Qualsiasi sporgenza superiore a 0,8 mm dovrebbe avere un supporto aggiuntivo onde evitare di danneggiare il pezzo. Quando si progetta una sporgenza, è bene non eccedere nelle sue dimensioni perché, se troppo grandi, possono limitare la precisione dei dettaglio di un pezzo e, ancora peggio, far crollare l’intera realizzazione. Consultate questo recente suggerimento per il design riguardante i pezzi metallici stampati in 3D nel quale troverete maggiori informazioni su come la DMLS possa creare componenti metallici complessi, durevoli e leggeri.
6. Non scegliete materiale inadatto per i pezzi da realizzare mediante SLA
I macchinari per SLA di oggi utilizzano una gamma di materiali simili alle termoplastiche, incluse varie opzioni che replicano le caratteristiche di polipropilene, ABS e policarbonato. Vogliamo che vi soffermiate sui termini “simili alle termoplastiche”. Occorre fare una distinzione importante in quanto le proprietà meccaniche dei materiali impiegati per la SLA si limitano solo a riprodurre quelle dei materiali termoplastici stampati in modo tradizionale. I pezzi ottenuti mediante SLA non offrono la stessa robustezza e durevolezza di quelli sinterizzati, fusi, lavorati meccanicamente o stampati. Detto ciò, questo processo continua ad essere una scelta eccellente per prototipi di qualità per i quali la valutazione della forma e dell'adattamento (ma non necessariamente il collaudo funzionale) costituisce il fattore più importante. Potete trovare maggiori informazioni nel nostro suggerimento per il design dedicato ai materiali per SLA e nella nostra guida alla scelta dei materiali per la stampa 3D. Inoltre, i nostri Application Engineers possono assistervi nella selezione del materiale e del processo di fabbricazione, qualora necessario.
7. Assicuratevi che i pezzi in materiale elastomerico stampati in 3D siano adatti al sovrastampaggio
Occorre poi fare attenzione ai materiali elastomerici da stampare in 3D. PolyJet utilizza un particolare fotopolimero liquido sotto forma di spray la cui durezza può essere modificata sul momento e nella stessa realizzazione. Questo processo è ideale per la prototipazione di pezzi che, a un certo punto, saranno sovrastampati: un manico morbido antiscivolo per un attrezzo elettrico, per esempio, o il coperchio a tenuta stagna della custodia di uno strumento scientifico. Sono anche disponibili fotopolimeri digitali in bianco, nero e trasparente/traslucido.
Pertanto, se dovete validare il design di un sovrastampo, potreste iniziare da qui. Tuttavia, e questo è l’aspetto che richiede cautela, verificate con uno dei nostri Application Engineers che il vostro pezzo da stampare in 3D sia anche adatto al sovrastampaggio. Alcuni progettisti si “fissano” su un particolare design soltanto per scoprire che non può essere fabbricato su larga scala in modo economico. Potrete trovare maggiori informazioni nel nostro suggerimento per il design relativo agli elastomeri e nella nostra pagina dedicata ai servizi di sovrastampaggio e costampaggio.
Sappiamo di avere trattato in questa sede di molti aspetti della stampa 3D ma come sempre, vi invitiamo a contattarci per qualsiasi domanda al numero +39 0321 381211 o all'indirizzo [email protected].