Questione di materiali: il processo di selezione dei materiali
Questo White Paper si rivolge ai tecnici e agli ingegneri che devono analizzare quantitativamente un pezzo, determinare carichi, sforzi, deformazioni e condizioni, e che desiderano prendere decisioni ragionate sui materiali partendo dall’analisi effettuata. Quando interviene il fattore sicurezza o è assolutamente necessario garantire affidabilità ed efficacia di un prodotto, ogni pezzo deve essere ingegnerizzato e i materiali devono essere selezionati di conseguenza. Questa documentazione illustra i numerosi fattori coinvolti e mostra in che modo l’ambiente e l’applicazione intervengono nella scelta dei materiali. Al termine della lettura, si capirà quindi perché un ingegnere è sempre poco propenso a consigliare un materiale specifico per il pezzo di qualcun altro.
Tuttavia, molti dei clienti di Protolabs che progettano pezzi non sono ingegneri e molte applicazioni dei pezzi realizzati da Protolabs sono abbastanza innocue e saranno probabilmente comprese nei limiti di prestazione delle plastiche di uso più comune. Se la vostra applicazione sarà utilizzata a temperatura ambiente e non dovrà sopportare carichi particolari e siete disposti a produrre un certo numero di pezzi e a percuoterli con un martello per testarne l’effettiva resistenza per l’uso voluto, potete saltare direttamente ai suggerimenti rapidi per la scelta dei materiali presentati alla fine del documento, nella sezione “Risparmiamoci qualche calcolo”.
- La scheda tecnica standard dei materiali
- La temperatura massima di breve utilizzo
- Resistenza alla trazione e allo snervamento
- Il rapporto tra sforzo e temperatura
- Il rapporto tra temperatura e invecchiamento
- Modulo
- Stress Cracking: la causa più frequente di guasto durante l'utilizzo per i pezzi in plastica
- Effetto della velocità di deformazione sul modulo e sulla tensione di snervamento
- Variazioni del modulo in funzione della temperatura
- Resistanza all'urto
- Indice di fluidità
- Altre proprietà dei materiali
- Risparmiamoci qualche calcolo
A volte, quando si deve scegliere un materiale, si finisce per tirare a indovinare. Il motivo è, innanzitutto, la scarsa comprensione della relazione di base tra la struttura interna di un materiale e le sue proprietà. In secondo luogo, di solito la definizione accurata dei requisiti dell’applicazione non riceve il tempo e l’attenzione necessari. Infine, anche riuscendo a superare questi primi due scogli, può essere difficile trovare dei dati precisi sulle proprietà dei diversi materiali.
Nei database dei materiali sono elencate oltre 85.000 possibilità commerciali per i materiali plastici, ma la cifra effettiva supera probabilmente i 90.000. Questo ricco insieme può essere suddiviso approssimativamente in 45 miscele o famiglie di polimeri, suddivisibili a loro volta in due categorie generali: i materiali termoindurenti e i materiali termoplastici. I materiali termoindurenti sono stati i primi polimeri disponibili in commercio, ma il loro utilizzo è andato diminuendo e oggi costituiscono appena il 15% circa dei materiali lavorati in un anno. Questa documentazione si concentrerà quindi sui materiali termoplastici.
La scheda tecnica standard dei materiali
La scheda tecnica standard dei materiali contiene quasi esclusivamente caratteristiche di prestazione misurate a temperatura ambiente. Inoltre, queste caratteristiche vengono associate a eventi catastrofici, che sono considerati esiti non accettabili per i prodotti in plastica. La resistenza alla trazione a snervamento e l’allungamento a rottura rappresentano i parametri standard di prestazione dei materiali, ma lo snervamento e la rottura non rappresentano la risposta che si desidera osservare in un pezzo in plastica messo sotto carico.
Per stabilire qual è il materiale più adatto per una data applicazione, è necessario operare una sintesi tra le informazioni reperite da diverse fonti incomplete. La scheda tecnica è la principale fonte di informazioni ed è importante imparare a estrarre quanti più dati possibili da questo strumento. L’Appendice A presenta un buon esempio di scheda tecnica sufficientemente dettagliata: la scheda del poliestere PBT rinforzato con il 30% di fibra di vetro.
A volte è possibile colmare le lacune delle schede tecniche ottenendo informazioni più dettagliate dai manuali di progettazione e dalle note sulle applicazioni pubblicate dai singoli fornitori di materiali. Per i materiali speciali e tecnici a prestazioni più elevate sono spesso disponibili maggiori informazioni rispetto ai materiali di uso comune. Per comprendere fino in fondo un materiale, è necessario quindi prepararsi a fare un po’ di ricerca.
La temperatura massima di breve utilizzo
La temperatura massima di breve utilizzo è probabilmente il parametro più importante di una scheda tecnica. È chiamata tradizionalmente temperatura di inflessione sotto carico (DTUL) o temperatura di inflessione per calore (HDT) ed è correlata ad un altro parametro, quello della temperatura di rammollimento Vicat. La DTUL misura l’inflessione meccanica, mentre il punto Vicat è più prossimo al punto effettivo di fusione o rammollimento del polimero, perciò il valore Vicat è generalmente più elevato. Per un materiale come il PBT rinforzato con fibra di vetro presentato nell’ Appendice A, che è un materiale semicristallino, tutti questi valori saranno molto vicini al punto di fusione cristallina del polimero, 223 °C (435 °F). Le applicazioni che prevedono escursioni termiche anche momentanee superiori a questo valore escludono automaticamente l’impiego di questo polimero.
Il valore di HDT o DTUL permette di conoscere anche il limite di temperatura superiore dei polimeri amorfi, caricati o meno. Ad esempio, nel caso del policarbonato non caricato, i valori di HDT variano dai 130 ai 140 °C, a seconda della categoria. Il punto di rammollimento Vicat (quando indicato) è più alto di qualche grado. I polimeri amorfi non presentano una struttura cristallina significativa quando si solidificano, perciò non hanno un punto di fusione. Tuttavia, sono caratterizzati dalla cosiddetta “transizione vetrosa” che, da un punto di vista pratico, è la temperatura alla quale i polimeri amorfi perdono la capacità di carico.
Nel caso del policarbonato, questo valore, misurato con metodi meccanici dinamici, è approssimativamente 153 °C, qualche grado sopra il punto di rammollimento Vicat e 10-20 °C sopra la temperatura DTUL, a seconda della geometria del campione e del metodo di misurazione della DTUL. La temperatura di rammollimento Vicat e il valore di DTUL non devono mai essere utilizzati come caratteristiche di prestazione a lungo termine, ma possono essere impiegati per calcolare la resistenza termica di breve durata, quando tale durata è definita in minuti. Gli ambienti di applicazione che prevedono escursioni termiche superiori a queste proprietà escludono automaticamente l’impiego del materiale in questione, a prescindere da eventuali altre caratteristiche possedute.
Resistenza alla trazione e allo snervamento
Le prestazioni a lungo termine di un materiale sottoposto a sollecitazioni costanti chiamano in causa una proprietà chiamata “resistenza allo scorrimento”; se le sollecitazioni sono periodiche, la resistenza a fatica diventa l’aspetto principale da considerare. Tra sforzo, tempo e temperatura esiste una relazione complessa e spesso non si dispone dei dati necessari per prendere decisioni ragionate sul comportamento a lungo termine di un materiale sotto carico. Anche in questo caso, la scheda tecnica può indicare il limite superiore. Il limite superiore dei materiali duttili è la resistenza allo snervamento del materiale, mentre per i materiali fragili è lo sforzo di rottura. I due valori definiscono entrambi il punto in cui il materiale subisce un guasto catastrofico. Gli ambienti che comportano sforzi e deformazioni superiori a questi valori escludono automaticamente l’impiego del materiale anche per prestazioni a breve termine. Una volta applicato questo semplice filtro, si passerà a considerare gli effetti termici a lungo termine.
Tabella 1: Resistenza alla trazione e modullo di un nylon 6/6, con 43% di fibra di vetro a diverse temperature | |
---|---|
Temperatura(C) | Resistenza alla trazione (psi) |
-40 | 36500 |
73 | 30000 |
171 | 17500 |
250 | 12500 |
Il rapporto tra sforzo e temperatura
Per definire le prestazioni alle alte temperature a lungo termine, è necessario avere accesso a più punti dati. All’aumentare della temperatura o della durata desiderata del prodotto, il livello di sforzo accettabile al quale il materiale può essere usato diminuisce sulla base delle proprietà termiche e meccaniche del materiale in questione. Le correlazioni tra prestazioni a breve e a lungo termine hanno dimostrato che i livelli di tensione di esercizio a lungo termine di un materiale termoplastico corrispondono normalmente al 20-40% della resistenza allo snervamento o alla rottura a breve termine. I materiali non caricati si collocano in genere nella parte inferiore del range, mentre i composti altamente caricati tendono a trovarsi nella parte superiore. I fattori legati alla sicurezza per un dato prodotto fanno diminuire questi valori e se la temperatura dell’ambiente di applicazione è prossima ai valori di DTUL, la tensione di esercizio sostenibile può arrivare a corrispondere ad appena il 3-5% del valore indicato sulla scheda tecnica. Alcune schede tecniche contengono valori di resistenza alla trazione e modulo relativi a diverse temperature. Questi dati, quando presenti, agevolano in maniera decisiva la scelta del materiale. La Tabella 1 presenta un esempio dei valori di resistenza alla trazione a diverse temperature per un materiale in nylon 6/6 rinforzato con fibra di vetro.
Il rapporto tra temperatura e invecchiamento
I polimeri presentano tutti una certa sensibilità a lungo termine all’ossigeno, che aumenta all’aumentare della temperatura. La degradazione associata all’invecchiamento è definita da una proprietà detta “indice termico relativo” o RTI (Relative Thermal Index). Questo valore deriva da un test proposto ed eseguito da Underwriters Laboratories e che rappresenta attualmente il migliore indicatore per misurare gli effetti a lungo termine dell’invecchiamento sulle proprietà meccaniche ed elettriche dei polimeri. Il test dell’indice termico relativo inizia con la misurazione delle proprietà chiave di base, come la resistenza alla trazione, la resistenza all’urto Izod con intaglio e la resistenza all’arco. I campioni di prova vengono quindi invecchiati a diverse temperature, monitorando le proprietà di base finché queste non perdono il 50% dei valori originari. Il tempo necessario per scendere al 50% delle prestazioni è detto “tempo di guasto”. Se si utilizzano tre o quattro temperature di invecchiamento e il logaritmo del tempo di guasto è calcolato in funzione della temperatura reciproca, i punti dati possono essere disposti su una linea retta, da cui viene poi estrapolata una durata standard (in genere circa otto anni); la temperatura che secondo i calcoli provoca un guasto al termine della durata standard è l’indice termico relativo. Nella maggior parte dei materiali termoplastici, i valori di RTI sono inferiori ai valori di DTUL e di rammollimento Vicat. È il caso del PBT con fibre di vetro della scheda tecnica di esempio dell’Appendice A che presenta valori DTUL e Vicat tutti superiori a 200 °C (392 °F) e valori RTI pari a 140 °C (284 °F). Invece, i materiali morbidi e flessibili con buona stabilità all’ossidazione come il PTFE possono avere valori RTI superiori a quelli di DTUL.
I valori di RTI possono essere utilizzati per stabilire le prestazioni a lungo termine quando l’invecchiamento costituisce il fattore di maggiore interesse. Il processo di invecchiamento segue una regola empirica che correla la degradazione alla temperatura. Il tasso di degradazione raddoppia ad ogni incremento di 10 °C della temperatura. Si tratta di una relazione esponenziale, perciò ogni variazione di 20 °C produrrà un incremento del tasso di degradazione di un fattore di 22 o 4, mentre un incremento di 30 °C farà aumentare il tasso di un fattore di 23 o 8. Dal momento che il valore di RTI fa riferimento a un orizzonte temporale di circa otto anni, si può calcolare che un materiale potrebbe sopravvivere per quattro anni a temperature di 10 °C superiori rispetto al valore di RTI, per due anni a un punto 20 °C più alto rispetto al valore di RTI, e per un anno a un punto più alto di 30 °C rispetto al valore RTI. Questo calcolo deve tenere conto anche dei fattori legati alla sicurezza perché è stato dimostrato che il fattore di accelerazione eff ettiva, anche se nominalmente a 2, può variare da un minimo di 1,8 a un massimo di 2,5.
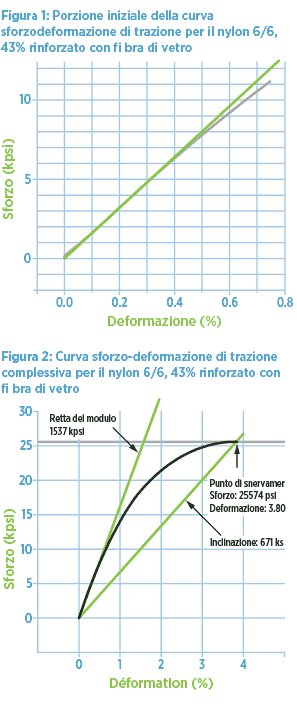
Modulo
Il modulo è riportato in qualsiasi scheda tecnica ed è presentato il più delle volte come modulo di trazione o modulo di flessione. Questo parametro correla lo sforzo alla deformazione e può essere considerato una misura della rigidezza. Nella maggior parte dei casi, è calcolato nella regione lineare della curva sforzo-deformazione. Spesso in corrispondenza di valori di deformazione molto bassi la linearità si perde. La Figura 1 presenta una visione ingrandita della porzione iniziale della curva sforzo-deformazione di un materiale in nylon 6/6 con rinforzo elevato in fibra di vetro. Il modulo di questo materiale a temperatura ambiente è definito a 10600 MPa (1.537.000 psi), ma la figura mostra che l’andamento della curva sforzodeformazione inizia a perdere linearità in corrispondenza dello 0,4% circa. Oltre questo punto, ogni aumento incrementale dello sforzo produce una deformazione corrispondente progressivamente maggiore. La Figura 2 mostra che, anche se l’inclinazione della retta del modulo riflette il valore indicato sulla scheda tecnica, l’inclinazione effettiva della retta che collega l’origine al punto di snervamento ha una pendenza pari ad appena il 40% del valore riportato. Pertanto, quando si usa il modulo come parametro di scelta è importante comprendere la posizione dello sforzo di applicazione sulla curva sforzo-deformazione. Man mano che lo sforzo di applicazione si avvicina al punto di snervamento, la durata prevista del prodotto diminuisce. La Tabella 2 mostra la tensione di esercizio massima di un materiale in policarbonato in funzione del tempo a due diverse temperature. Per periodi molto brevi, inferiori a un’ora, il limite di sforzo è quasi identico alla tensione di snervamento per la temperatura data. Man mano che l’orizzonte temporale dell’applicazione aumenta sotto carico, la tensione di esercizio massima consentita diminuisce.
Stress Cracking:la causa più frequente di guasto durante l’utilizzo per i pezzi in plastica
Se nell’ambiente di applicazione è presente un agente chimico in grado di indurre un fenomeno chiamato “stress cracking” o fessurazione sotto sforzo, la tensione di esercizio massima diminuisce. La Tabella 3 mostra la tensione di esercizio massima relativa al policarbonato rappresentato nella Tabella 2, dove allo sforzo costante si abbina la presenza di un liquido che agisce da agente di fessurazione sotto sforzo. I dati dimostrano che la capacità meccanica del materiale diminuisce quando è presente l’agente chimico. Il guasto di un materiale plastico sotto l’eff etto combinato di sforzo e agente chimico è detto fessurazione sotto sforzo per eff etto ambientale (ESC) e rappresenta la causa più frequente di guasto durante l’utilizzo per i pezzi in plastica.
Tabella 2: Tensione di esercizio massima del Policarbonato in funzione del tempo a due temperature | ||
---|---|---|
Tempo(ore) | Tensione di esercizio a 23° C (psi) | Tensione di esercizio a 60° C (psi) |
0.01 | 9200 | 7200 |
0.1 | 8850 | 7000 |
1 | 8450 | 6850 |
10 | 8080 | 6450 |
100 | 7700 | 6050 |
1000 | 7425 | 5800 |
10000 | 7100 | 5100 |
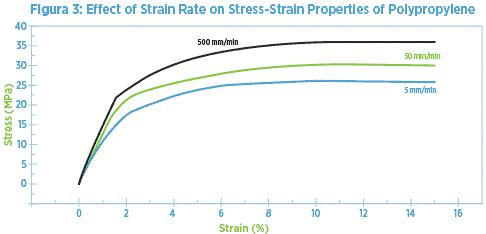
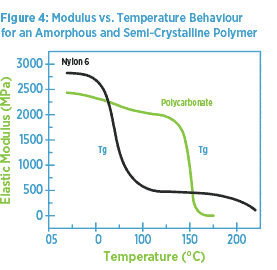
Effetto della velocità di deformazione sul modulo e sulla tensione di snervamento
Alcune proprietà dei materiali dipendono dalla velocità di deformazione. La velocità a cui il materiale viene caricato influisce sul modulo e sulla tensione di snervamento, come mostra la Figura 3. Velocità maggiori di deformazione producono un incremento del valore del modulo e della tensione di snervamento. Per quanto desiderabile, non sempre i fornitori di un dato tipo di materiale utilizzano la stessa velocità di deformazione nei test. Questa mancanza di armonizzazione può generare differenze evidenti tra le proprietà delle varie schede tecniche.
Variazioni del modulo in funzione della temperatura
Il modulo varia con la temperatura. Le schede tecniche che indicano i valori di modulo in funzione di temperature diverse come quelli presentati nella Tabella 1 offrono un quadro più completo del comportamento di un materiale. Tuttavia, è raro trovare dati relativi a più di quattro temperature e i livelli vanno spesso da 150 a 200 °C. Restano così molti dubbi sul comportamento del materiale tra i due estremi e fuori dall’intervallo definito da tali estremi. L’analisi dinamico-meccanica (DMA) consente misurazioni continue del modulo in un intervallo ampio di temperatura. La Figura 4 mostra la curva temperatura-modulo del policarbonato, un polimero amorfo, e del nylon 6, un polimero semicristallino.
Questi due materiali esibiscono il comportamento tipico delle rispettive strutture. Entrambi possiedono una transizione vetrosa che rappresenta l’inizio del movimento molecolare nelle regioni amorfe della struttura. Nel policarbonato amorfo, ciò produce la perdita completa di tutte le proprietà meccaniche utili su un intervallo di temperatura relativamente ristretto. Nel nylon, invece, la riduzione di modulo, anche se significativa, non produce conseguenze catastrofiche e circa il 20% delle prestazioni a temperatura ambiente viene conservato. Questa misura mostra il contributo della struttura cristallina del polimero. Tutti i polimeri amorfi presentano un comportamento termico simile a quello del policarbonato, mentre tutti i materiali semicristallini esibiscono un profilo termico simile a quello del nylon. La differenza di base sta nell’esatta temperatura di transizione di ciascun polimero.
Resistenza all’urto
Non è facile valutare la resistenza all’urto di un materiale analizzando i valori di una tipica scheda tecnica perché i metodi utilizzati nel settore per testare la resistenza agli urti e presentare i risultati delle prove sono più di uno. Il metodo di prova più usato per valutare la resistenza agli urti è la prova Izod con intaglio. Il test impiega un campione con un intaglio affilato fresato nel pezzo e un pendolo oscillante che trasmette l’energia necessaria per produrre il guasto.
Il raggio minimo dell’intaglio Izod amplifica spesso le differenze di duttilità per via delle diverse sensibilità all’intaglio dei vari materiali. Ad esempio, il policarbonato e il poliestere PET amorfo possiedono entrambi una buona tenacità pratica. Il poliestere PET è più sensibile all’intaglio rispetto al policarbonato. Di conseguenza, i valori di resistenza all’urto Izod con intaglio del policarbonato a temperatura ambiente possono essere molto più alti rispetto a quelli di alcuni tipi di poliestere PET e presentano il policarbonato come un materiale molto più tenace. È possibile ottenere un quadro più completo sulla resistenza agli urti raccogliendo i risultati ottenuti con tipi diversi di prove d’urto.
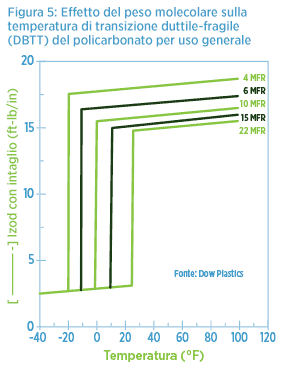
Le prove a caduta di dardo come il test Gardner o la prova d’urto strumentato con il dardo possono fornire punti dati aggiuntivi. Questi test utilizzano campioni privi di concentrazioni di sforzi nel pezzo e danno una rappresentazione più accurata delle prestazioni prevedibili di un pezzo ben progettato.
Le proprietà di impatto sono influenzate anche dalla temperatura. Temperature inferiori tendono a produrre più facilmente comportamenti fragili nei materiali e il passaggio dalla duttilità alla fragilità può essere molto repentino. Non è facile ottenere un quadro completo su questo tipo di comportamento perché i fornitori di materiali sono restii a riportare i difetti di prestazione dei propri prodotti. Una ricerca può comunque fornire dati preziosi, anche se non per tutti i materiali. La Figura 5 mostra la resistenza all’urto Izod con intaglio di diverse categorie di policarbonato in funzione della temperatura. I risultati mettono in evidenza un rapido passaggio dalla duttilità alla fragilità, che si verifica generalmente al diminuire della temperatura. Il grafico mostra inoltre che il passaggio dalla duttilità alla fragilità è legato al peso molecolare del polimero. Un indice di fluidità più basso è associato a tipologie con peso molecolare medio maggiore. Questa proprietà incide in maniera signifi cativa sulla temperatura di variazione della resistenza all’urto.
Indice di fluidità
L’indice di fluidità o melt flow rate è una proprietà riportata dalla maggior parte delle schede tecniche che tenta di cogliere con un valore unico un aspetto importante del comportamento dei materiali. È usato spesso dai processori per valutare lo scorrimento del materiale durante lo stampaggio. L’importanza dell’indice di fluidità è nella sua relazione con il peso molecolare medio del polimero. Un indice di fluidità più basso è associato a materiali con peso molecolare medio maggiore. Un peso molecolare maggiore, a sua volta, consente prestazioni migliori, in particolare in termini di resistenza agli urti, allo scorrimento e alla fatica, e di proprietà di barriera.
Il confronto dei materiali sulla base dell’indice di fluidità è valido soltanto se eseguito all’interno di una data famiglia di polimeri. Inoltre, alcuni materiali impiegano più condizioni di prova. Ad esempio, l’ABS può essere testato in diverse condizioni definite dalla temperatura e dal carico a cui è sottoposto il materiale. La Tabella 4 presenta le condizioni di prova e le differenze tipiche dei risultati associati a ciascuna condizione. Quando si confrontano due tipi diversi di materiali, è importante tenere conto dei parametri di prova e adeguarsi di conseguenza.
Tabella 4: Effetti di condizioni di prova sul tasso di fluidità ABS | |
---|---|
Condizioni di prova | Indice di fluidità nominale (grammi/10minuti) |
200 C/5.0kg |
1.5 |
230 C/3.8 kg | 4.5 |
220 C/10.0 kg | 18.0 |
Tabella 5: Valori del coefficiente di dilatazione di un nylon 6/6, con 43% di fibra di vetro a diversi intervalli di temperatura | ||
---|---|---|
Intervallo di temperatura | (F) | Coefficiente di dilatazione termica lineare |
-40 to 73 | 0.00034 | |
73 to 131 | 0.00044 | |
131 tp 320 | 0.000071 |
Altre proprietà dei materiali
Oltre alle proprietà termiche e meccaniche, in alcune applicazioni particolari contano anche altre caratteristiche, ad esempio le proprietà elettriche come la costante e la rigidità dielettrica, la resistività superficiale e di volume, e il coefficiente di dilatazione termica. Le misurazioni standard del coefficiente di dilatazione termica sono eseguite tra -30°C e +30°C. Tuttavia, alcuni fornitori presentano valori relativi a intervalli di temperatura diversi, come quelli illustrati nella Tabella 5. Questo quadro più completo, se disponibile, mostra che questi tipi di proprietà dipendono anche dalla temperatura e che i valori tendono ad aumentare all’aumentare stesso della temperatura.
I materiali plastici sono considerati generalmente eccellenti isolanti elettrici, tranne quando il composto è progettato specificatamente per dissipare l’elettricità statica o diventare conduttore con l’aggiunta di ingredienti come il carbonio o l’acciaio inossidabile. Pertanto, la maggior parte dei materiali ha valori di resistività molto alti, compresi tra 1010 e 1016 ohm o ohm-cm per, rispettivamente, la resistività superficiale e di volume. Continue sollecitazioni elettriche possono provocare con il passare del tempo la perforazione del dielettrico del materiale. Questo comportamento dipende dall’ampiezza della tensione applicata ed è definito in maniera particolarmente efficace da proprietà che possono essere presenti sulle schede tecniche standard, ma che è più facile reperire nel database di Underwriters Laboratories all’interno del sistema Yellow Card (carta gialla). Questo metodo applica valori numerici a proprietà come l’accensione ad alto amperaggio, la resistenza d’arco e la resistenza alla corrente superficiale, dove per ciascun parametro valori inferiori indicano un livello di resistenza superiore e viceversa.
Questo comportamento dipende dall’ampiezza della tensione applicata ed è definito in maniera particolarmente efficace da proprietà che possono essere presenti sulle schede tecniche standard, ma che è più facile reperire nel database di Underwriters Laboratories all’interno del sistema Yellow Card (carta gialla). Questo metodo applica valori numerici a proprietà come l’accensione ad alto amperaggio, la resistenza d’arco e la resistenza alla corrente superficiale, dove per ciascun parametro valori inferiori indicano un livello di resistenza superiore e viceversa.
Risparmiamoci qualche calcolo
I consulenti in genere preferiscono non dare consigli sui materiali se prima non hanno compreso i requisiti completi dell’applicazione del pezzo e non hanno eseguito un’analisi del progetto sul modello 3D. A volte ingegnerizzare completamente il pezzo per capire quale materiale usare costituisce una soluzione troppo costosa. Se volete risparmiarvi la fase di ingegnerizzazione e preferite fare una scelta ragionata sui materiali, ecco alcune regole d’oro da seguire:
1 Provate l’ABS. L’ABS è indicato per molte, moltissime applicazioni. Ha un prezzo ragionevole, è resistente, abbastanza tenace, ha un aspetto accettabile e mostra una certa tolleranza anche quando non vengono seguite tutte le regole di progettazione standard per i pezzi in plastica. Inoltre, ha un punto di fusione relativamente basso. Tutti i pezzi del Demo Mold di Protolabs sono in ABS.
2 Se la rigidità e l’estetica non sono importanti, ma è il costo l’aspetto fondamentale, provate il polipropilene (PP). Il Design Cube di Protolabs è in PP.
3 Se vi serve qualcosa di un po’ più tenace dell’ABS o in grado di resistere a temperature un po’ più alte, provate il policarbonato (PC). Il PC è meno adattabile dell’ABS quando non si seguono le regole di progettazione standard per i pezzi in plastica.
4 Se vi serve un materiale trasparente e piacevole alla vista, provate l’acrilico (PMMA). Questo materiale ha l’inconveniente di essere un po’ fragile. Il PC trasparente è più tenace del PMMA ma ha un aspetto meno gradevole.
5 Se le regole 1-4 non si applicano al caso vostro, allora dovete fare qualche calcolo.
Per i pezzi da stampare, prima di passare allo stampaggio potreste provare a realizzare un paio di pezzi di prova nel materiale voluto utilizzando il servizio di lavorazione con macchine CNC di Protolabs. Gli stampi sono progettati per adattarsi al valore di ritiro delle singole resine, perciò l’uso di uno stesso stampo per provare resine diverse potrebbe compromettere le misure, le tolleranze e/o le dimensioni.