
Come ridurre i costi di lavorazione CNC
Tenete in considerazione questi aspetti del design e sulla scelta dei materiali per ridurre i vostri costi di lavorazione a macchina
La lavorazione CNC continua a migliorare e a progredire ogni anno e, pertanto, ogni anno diventa un po’ più complessa. Di conseguenza, può essere difficile tenere il passo con gli aspetti accettabili e quelli da evitare del design di un pezzo. Eppure, ridurre i costi dei pezzi lavorati, migliorandone al contempo la funzionalità, è possibile grazie ad alcune modifiche relativamente semplici al design del pezzo o alla selezione del materiale.
In Protolabs, utilizziamo un programma automatizzato per preparare i preventivi per la realizzazione dei pezzi ed evidenziamo le caratteristiche che devono essere considerate in fase di design in base ad un processo sviluppato per produrre rapidamente i pezzi. Il software rileva immediatamente caratteristiche che non possono essere realizzate (oppure che lo possono, ma richiedono utensili ed apparecchiature aggiuntivi) ed evidenzia anche le aree che non richiedono necessariamente alcuna modifica ma che possono migliorare la realizzabilità; angoli sulle tasche, testo inciso, pareti sottili, tasche profonde e fori e geometrie complesse.
Ecco alcuni suggerimenti che vi aiuteranno a progettare pezzi lavorati a macchina in modo più efficace dal punto di vista economico.

1. Prevedete un margine per le tasche angolari
Immaginate gli angoli di una tasca lavorata a macchina: l’interno di un alloggiamento per componenti elettronici, ad esempio, oppure una staffa usata per bloccare il corpo di un componente rettangolare. Una svista comune del design è quella di lasciare che l’intersezione delle pareti verticali insista sulle caratteristiche del pezzo che sono estremamente appuntite. Per farvi un esempio, immaginate la lavorazione a macchina di una scatola in acciaio inossidabile che debba contenere un mazzo di carte. L’unico modo per ottenere angoli verticali perfettamente squadrati, necessari per inserire le carte nella scatola, è mediante elettroerosione (Discharge Machining, EDM) oppure imbullonando diverse piastre piatte. Entrambi i processi possono essere lenti e dispendiosi.
Una possibile alternativa per ottenere una soddisfacente definizione degli angoli prevede il ricorso a una fresa a codolo di dimensioni estremamente ridotte. Con l'acciaio inossidabile 304, questo significa utilizzare una fresa da 0,8 mm, che lascia un raggio angolare di 0,4 mm. Si tratta di un angolo alquanto affilato, ma la profondità è limitata. La lunghezza della maggior parte delle frese a codolo per il taglio dell’acciaio di questa gamma di dimensioni raggiunge un limite massimo pari a cinque volte il diametro del cutter. La lavorazione con frese a codolo di piccole dimensioni come questa comporta inoltre un lavoro lento e delicato, che fa aumentare il costo del vostro progetto a causa del tempo aggiuntivo richiesto.

Un approccio più economico consiste invece nell'introduzione di un margine in corrispondenza di ciascun angolo della tasca. In questo modo si elimina quel raggio fastidioso, lasciando invece uno spazio libero a forma di U o di C. Ciò consente di avere tasche molto più profonde: tagliando un margine largo 6,35 mm ad ogni angolo, è possibile ottenere angoli vivi dal punto di vista funzionale di circa 32 mm di profondità. E se si decide di passare all'alluminio o alla plastica, si otterranno profondità doppie rispetto a quelle dell'acciaio. Ma l’aspetto più importante da considerare è che se si progettano tasche in questo modo, si riduce il costo del pezzo, poiché è possibile usare frese a codolo e aumentare di conseguenza la velocità di rimozione del materiale.
2. Effettuate voi stessi la levigatura dei bordi
Evitare di eliminare gli angoli è un altro accorgimento relativo al raggio che consente di ridurre i costi. Nel tentativo di rimuovere i segni dell'utensileria ed eliminare gli angoli vivi, i progettisti provvedono spesso a levigare le aree di intersezione esterne al pezzo introducendo smussi o angoli di curvatura. Si tratta di una pratica comprensibile e talvolta necessaria, ma che può rivelarsi costosa. Con i pezzi metallici, Protolabs offre un’opzione di levigatura automatizzata e le plastiche sono consegnate come se fossero state lavorate a macchina o con gli spigoli vivi, come nell’illustrazione. Se il design del pezzo richiede la levigatura di uno spigolo, dobbiamo utilizzare un utensile aggiuntivo (una fresa a testa sferica) e lavorare questi angoli con un movimento di profilatura 3D.
In generale, utilizziamo questi utensili a velocità elevate ed è possibile rimuovere piccoli quantitativi di materiale, ma si tratta comunque di un processo lungo perché consiste nel ripassare ciascun angolo sino a quando non diventa liscio. Molti clienti decidono quindi di risparmiare una parte delle risorse a disposizione provvedendo autonomamente alla levigatura dei bordi con l'ausilio di una lima, un po' di carta abrasiva o una rotella di lucidatura.
3. Evitate di aggiungere il testo fino allo stampaggio
Allo stesso modo, il testo inciso è gradevole dal punto di vista cosmetico ma comporta un’operazione lunga che sarebbe da evitare, se possibile. Ancora una volta, si utilizza una fresa a testa sferica per tracciare lettere, numeri e simboli riportati sul modello CAD. L’aspetto è fantastico e potrebbe essere un requisito legittimo sul vostro pezzo lavorato a macchina, ma è probabilmente più adatto sui pezzi stampati a iniezione, per i quali il tempo di lavorazione aggiuntivo viene compensato dalla produzione di volumi elevati. Poiché utilizziamo utensili diversi per i metalli e per le plastiche, la dimensione minima delle caratteristiche è di 0,90 mm per i metalli e di 0,51 mm per la plastica.
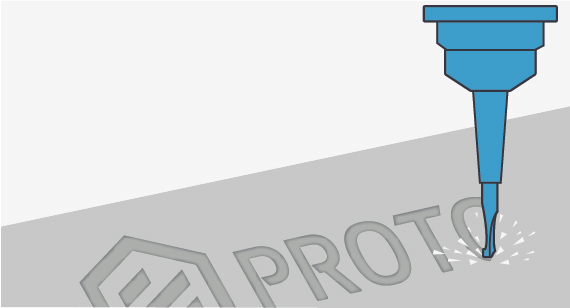
I piccoli diametri dell'utensile aggiungono tempo di lavorazione, quindi si consideri la rimozione di testi o loghi dai prototipi lavorati.
4. Fate attenzione alle pareti sottili e alle caratteristiche
La nostra tolleranza standard per i pezzi è di +/- 0,13 mm. Se la vostra caratteristica è di 0,51 mm o più piccola, il nostro sistema di preventivazione automatizzato la indicherà come geometria dalla parete sottile ma ricordate che potremo comunque lavorarla, anche se il pezzo potrebbe differire leggermente dal vostro design originale. Inoltre, le pareti sottili di 0,51 mm o meno non sono soltanto soggette a rottura durante la lavorazione, ma potrebbero flettersi o deformarsi in un secondo tempo. Cercate di aumentarne al massimo lo spessore, nella misura consentita dal design del vostro pezzo.
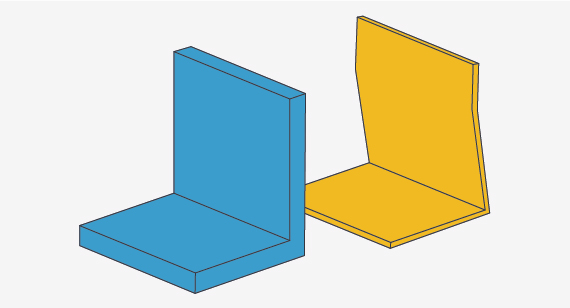
5. Realizzate un design semplice
Tasche molto profonde sono completamente fuori luogo, anche se gli spigoli sono in rilievo. Il processo di rimozione del materiale richiederà infatti tempi di lavorazione estremamente lunghi e, come se non bastasse, l'eventuale presenza di sollecitazioni residue nella materia prima tenderà ad alterare la profondità delle tasche e l'altezza delle pareti. Pezzi di questo tipo potranno essere rinforzati da tasselli triangolari o strutture di supporto (per impedire movimenti dovuti alle sollecitazioni), ma il ricorso a tali stratagemmi tende a far lievitare i costi di lavorazione. Il consiglio migliore che possiamo dare a qualsiasi produttore o progettista di pezzi lavorati a macchina è di fare le cose semplici.

Lo stesso principio vale anche per la geometria complessiva del pezzo. È sempre meglio non sopravvalutare le funzionalità del pezzo. Massimizzare l’utilizzo del materiale può creare problemi di tenuta del lavoro o di lavorazione, aumentando di conseguenza i costi. Se il design diventa troppo complesso, provate a scomporlo in componenti multipli assemblandoli con l'ausilio di viti di fissaggio. A nessuno piace spendere molto per l’assemblaggio né la complessità che caratterizza pezzi multipli, ma questa potrebbe essere la soluzione migliore per i pezzi difficili da lavorare a macchina se la velocità è uno dei vostri requisiti. Superfici scolpite, scanalature cavernose (pensate ai dissipatori di calore), fori molto profondi (collettori idraulici) e filettature: questi sono alcuni dei fattori comuni che incidono sui costi di lavorazione e che possono erodere il budget del vostro progetto.
6. Valutate la possibilità di utilizzare materiali alternativi
Uno dei modi più semplici di non sforare il budget, ipotizzando che soddisfi i vostri requisiti, consiste nell’utilizzare un materiale che possa essere lavorato con maggiore facilità o meno dispendioso. La nostra scelta dei materiali include una gamma di metalli e plastiche, ciascuno con i propri attributi tecnici, cosmetici, considerazioni di lavorazione e costo. Ecco alcune considerazioni chiave sui materiali:
- L’acciaio inossidabile 17-4 PH è difficile da tagliare. Se la resistenza elevata e la resistenza alla corrosione non sono aspetti di primaria importanza, provate a utilizzare il 316L o 304.
- Il rame è un ottimo conduttore di elettricità ma è molto più costoso dell’alluminio. Sebbene l’alluminio abbia circa il 60 per cento della conduttività elettrica del rame, i risparmi in termini di peso e costi potrebbero indurvi a riconsiderare l’alluminio come alternativa valida.
- Se la durezza rappresenta un aspetto importante, il 4140 potrebbe essere la vostra prima scelta ma il 1018 ha un costo molto contenuto e produce ottimi risultati se sottoposto a carbocementazione.
- Per far contento un operatore di macchina, consegnategli un ordine di realizzazione di pezzi in ottone, un metallo dolce facile da fresare, che possiede le proprietà meccaniche, chimiche o conduttive richieste dalla vostra applicazione.
- Sul fronte dei materiali plastici, la nostra selezione include decine di opzioni differenti. Sono tutti relativamente facili da tagliare, aspetto che spesso - ma non sempre - significa ridurre i costi. Alcune plastiche offrono proprietà superiori di resistenza all’usura, alla corrosione o alle sostanze chimiche, altri hanno buone performance in termini di resistenza alle temperature elevate o alle fiamme, mentre altri ancora offrono eccellenti proprietà di resistenza, all’impatto o elettriche. Di solito, tanto più morbido è il materiale, quanto maggiore è il rischio per la stabilità dimensionale e di formazione di filamenti durante la fresatura.
In dubbio sul materiale da considerare? Sentitevi liberi di consultare l’elenco completo dei materiali o di contattare uno dei nostri Application Engineer per richiedere un consiglio.
Vi servono più di 25 pezzi lavorati a macchina? Riducete il costo dei vostri pezzi quando ne ordinate grandi quantitativi realizzati nei nostri materiali più comuni con la produzione rapida, un impianto certificato AS9100.
Quando caricate sul nostro sito web un modello CAD, il nostro strumento di preventivazione calcola quello che può essere lavorato con le nostre macchine, e cosa comporta invece un rischio. I risultati dell'analisi saranno chiaramente indicati all'interno del preventivo, offrendovi la possibilità di apportare modifiche al design del pezzo per poi caricarlo nuovamente. In caso di dubbi, tuttavia, vi invitiamo a contattare i nostri Application Engineer al numero +39 0321 381 211.