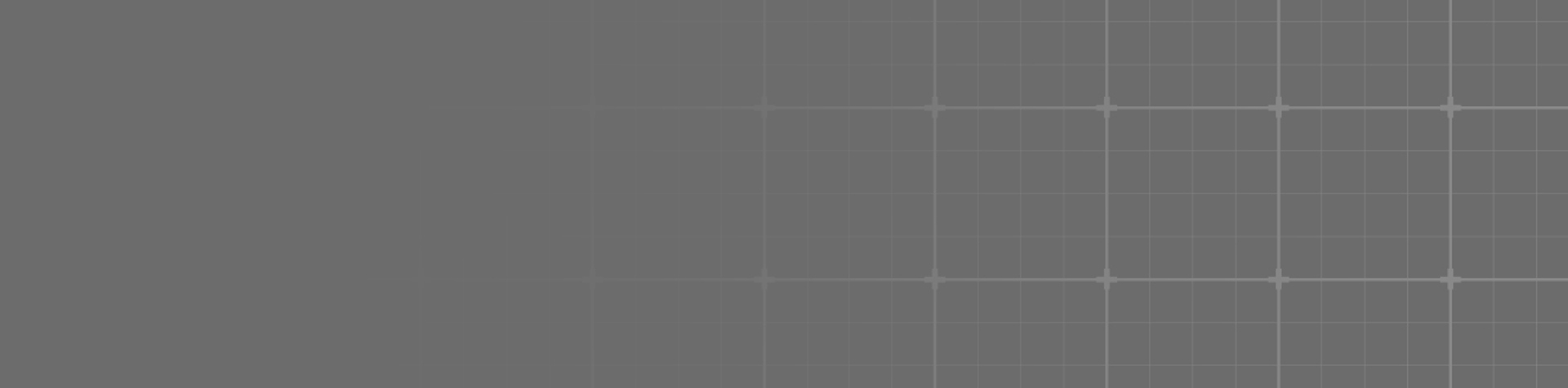
Erfahren Sie mehr über die Herstellungsmöglichkeiten von Elastomerbauteilen
Wenn Sie Materialeigenschaften benötigen, die Ihrem Teil Flexibilität, Haltbarkeit und Widerstandsfähigkeit verleihen, sind Elastomere sowohl für Prototypen als auch für Teile, die für den Endgebrauch vorgesehen sind, eine ausgezeichnete Wahl.
Werkstoffwissenschaftler geben ihren Kreationen gerne komplizierte Namen. Polyethylenterephthalat (eine Form von Polyester). Acrylnitril-Butadien-Styrol (dieser undurchsichtige Thermoplast ist besser bekannt als ABS). Dies sind nur zwei Beispiele für die tausenden von Polymeren, die heutzutage verwendet werden. Viele davon haben unser Leben grundlegend geändert. Eine Polymerart – mit einem weniger sperrigen Namen – gibt es jedoch schon viel länger als ihre vielsilbigen Pendants. Sie ist haltbar, flexibel, temperaturbeständig, in vielen Fällen biokompatibel und für eine Vielzahl an Fertigungsverfahren geeignet, darunter Spritzguss und 3D-Druck. Wie die heißt? Wahrscheinlich ist Sie Ihnen am besten unter der landläufigen Bezeichnung Gummi oder Kautschuk bekannt.
Arten von Elastomeren
Gummi bzw. Kautschuk ist der Stoff, aus dem Reifen, Motorschläuche und vieles mehr bestehen – hier meinen wir aber speziell Silikonkautschuk, das technisch gesehen ein viskoelastisches (kurz für viskos und elastisch) Polymer ist. Wenn wir diesen Ausdruck noch etwas komprimieren, erhalten wir Elastomer. Elastomere sind robust und (in der Regel) flexibel und in einer großen Auswahl an Güteklassen mit hochwertigen, mechanischen, chemischen und optischen Eigenschaften erhältlich. Protolabs bietet die folgenden Arten von elastomeren Werkstoffen an:
Elastomere Werkstoffe:
Spritzguss | 3D Druck |
---|---|
LSR | digitale Photopolymere |
LSR (Fluorsilikon) | TPU (auch für Spritzguss) |
LSR (Optisch) | TPE/TPV |
TPU (auch für 3D-Druck) |

Elastomere für den Spritzguss
Wenn Sie schon einmal zweikomponentigen Epoxidharzkleber für kleine Reparaturen im Haushalt angemischt haben, wissen Sie bereits, wie Teile aus Flüssigsilikon (LSR) hergestellt werden. Mit ähnlichen (in mancher Hinsicht jedoch komplett anderen) Maschinen wie beim Spritzgießen mit Kunststoff werden beim LSR-Spritzgießen gleiche Teile eines chemischen Katalysators mit Flüssigsilikon in eine gekühlte Mischkammer gepresst. Von hier aus wird der Werkstoff in den Formhohlraum gespritzt, der im Fall von LSR erhitzt wird, um den Vulkanisierungsprozess zu beschleunigen.
Die Gestaltungsregeln des LSR-Formens sind sehr nachsichtig. Sorgen über Wanddicken, Verjüngungswinkel, Hinterschneidungen und Eckenradien können weitgehend vernachlässigt werden. Das liegt daran, dass LSR die Konsistenz von Wasser hat, wenn es in die Form gelangt - es gibt keine Probleme mit Spülen, Stricklinien und Hohlräumen an scharfen Ecken oder um tiefe Rippen herum (vorausgesetzt, die Form wurde ordnungsgemäß verschlossen und belüftet). Auch ist das Auswerfen von Teilen kein Problem - LSR-Teile bleiben im Allgemeinen flexibel genug, um selbst von den am meisten geradwandigen Formen zu ziehen. Das einzige, worüber sich Entwickler Gedanken machen müssen, ist Flash - weil LSR eine solche niedrige Viskosität hat, sollten saubere und konsistente Trennlinien verwendet werden, wo immer dies möglich ist.

Bei Protolabs sind zwei Arten von LSR erhältlich. Alle halten sich an dieselben grundlegenden Spielregeln des Designs, verfügen jedoch über recht unterschiedliche Eigenschaften:
1. LSR—Die Serie Elastosil LR 3003 ist in vier Härtegraden von 30 bis 70 Shore A erhältlich und wie die meisten LSRs gut mit Pigmenten kombinierbar. Geeignete Anwendungsbereiche sind elektrische Autoteile, Dichtungen für die Lebensmittelindustrie und überall dort, wo ein flexibles, haltbares und temperaturbeständiges Polymer benötigt wird.
2. LSR (optisch) – Wollen Sie eine klare, aber haltbare Linse oder ein anderes transparentes Teil herstellen? Viele Spritzgießer greifen wahrscheinlich als Erstes zu Polycarbonat, doch optisches LSR ist weitaus besser spritzgießbar und verfügt über bessere optische Eigenschaften, die nur von Glas übertroffen werden. Außerdem ist es biokompatibel und gehört mit einer Härte von 72 Shore A zu den härtesten LSRs.

TPE- und TPV-Werkstoffe werden regelmäßig für spritzgegossene Elastomerteile verwendet, kommen jedoch vor allem bei Spritzgussverfahren mit zwei Werkstoffen, wie dem 2K-Spritzguss, zum Einsatz. Wenn Sie beispielsweise so weit sind, um Ihren PolyJet-Prototyp (3D-Druck) in die nächste Entwicklungsphase zu führen, bietet Ihnen Protolabs zahlreiche Gütegrade von elastomeren Werkstoffen, die alle zur TPE/TPV-Familie (thermoplastisches Elastomer/thermoplastisches Vulkanisat) gehören. So besitzt z. B. Santoprene 111-45 TPV einen hervorragenden Ermüdungswiderstand und ist eine gute Wahl für Smartphone-Hüllen. Gleichermaßen eignet sich Santoprene 101-73 gut für Lenksäulenmanschetten und Lautsprecherringe.
Bei den thermoplastischen Elastomeren bietet Versaflex OM1040X-1 eine weiche Haptik und ein hervorragendes ästhetisches Erscheinungsbild (kann gefärbt werden) und haftet gut auf Polycarbonat und ABS, wodurch es eine gute Wahl für Griffflächen an medizinischen Geräten darstellt. Ein weiteres färbbares TPE ist Versaflex OM 6240-1, bekannt für seine Affinität zu Nylon. Dann gibt es noch Hytrel 3078, der dank seiner höheren Biegsamkeit und Flexibilität im Vergleich zu Standard-Gummimaterial als Duracellhase unter den Elastomeren gilt.
Die Designempfehlungen für all diese Werkstoffe liegen irgendwo zwischen „fast alles geht“ bei LSR und denen für herkömmliche Thermoplasten. Laden Sie in Zweifelsfällen Ihr CAD-Modell in das automatisierte Angebotssystem von Protolabs und beachten Sie genau die anschließend bereitgestellte „Design for Manufacturability“ (DFM)-Analyse.
Unsere Anwendungstechniker stehen Ihnen bei Rückfragen wie immer unter der Rufnummer +49 (0) 89 905002 0 oder per E-Mail an [email protected] zur Verfügung.