
Epson verwendet bearbeitete Prototypen zur Optimierung von Datenbrillen
Elektronikriese nutzt Rapid Prototyping zur Verbesserung von Tragekomfort und Design seiner Moverio Augmented-Reality-Brille

Die Seiko Epson Corporation mit Sitz in Japan hat vor kurzem die Markteinführung des neuesten Modells seiner Augmented-Reality (AR)-Datenbrille Moverio angekündigt. Protolabs stelle mit seiner CNC-Expressbearbeitung Prototyping-Dienstleistungen bereit, die Epson halfen, den Tragekomfort dieser leichten hochauflösenden Brille zu verbessern.
Das Modell Moverio BT-300 besitzt ein stylisches, futuristisches Design mit einem silbern glänzenden Gestell, in dem die modernste optische Technik, einschließlich Flüssigkristall-Mikrodisplays, integriert ist. Die Datenbrille bietet dem Benutzer eine AR-Erfahrung und einen Tragekomfort ähnlich wie bei einer normalen Brille. Sie ist mit einer Schnittstelle zu externen Medien ausgestattet, wodurch Benutzer auf Online-Videos zugreifen und Luftaufnahmen von einer fliegenden Drohne über eine spezielle App sehen können.
„Da sie für Verbraucher bestimmt ist, haben wir auf ein leichtes und komfortables Design Wert gelegt“, so Kazuya Kamakura, Senior Staff, HMD Business Management Department, Visual Products Operations Division bei Epson. „Bei unserem Vorgängermodell bekamen wir von Benutzern viele Anfragen zu Gewicht und Größe. Deshalb haben wir uns bei der Entwicklung zum Ziel gesetzt, den Tragekomfort zu verbessern und die Datenbrille kompakter und leichter zu gestalten.“
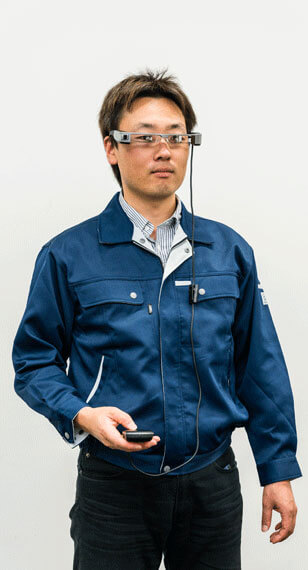
Kazuya Kamakura
Herausforderung für die Entwicklung: Tragekomfort verbessern, Gewicht reduzieren
Die Herstellung möglichst leichter und kompakter Produkte unter Beibehaltung der Festigkeit ist in unserer Branche eine Standardanforderung. Die Verbesserung des Komforts war eine schwierig zu lösende Aufgabe für Kamakura, der für die Entwicklung des BT-300 verantwortlich war.
„Das Produkt wird weltweit verkauft, das heißt es wird von internationalen und nicht nur japanischen Kunden benutzt“, so Kamakura. Außerdem war zu berücksichtigen, dass Größe und Passform bei Männern und Frauen unterschiedlich ausfallen. „Natürlich gibt es Unterschiede bei der Kopfgröße, und auch die Einstellung zum Tragen von Datenbrillen ist nicht die gleiche.“
Faktoren wie die Festigkeit oder der Massenschwerpunkt können mit Daten verifiziert werden. Das Komfortniveau hingegen kann nur am tatsächlich hergestellten Produkt geprüft werden. Die Tatsache, dass BT-300 für zukünftige Generationen des Geräts als Vorlage dient, ließ der Entwicklung, die mit knappen Fristen konfrontiert war, wenig Spielraum für Fehler.
Fertigungslösung: Prototypenherstellung mittels Schnellbearbeitung
Eine weiterhin hohe Markenqualität und die Bestätigung des Tragekomforts vor der Freigabe des Designs waren für Epson besonders wichtig. Das Produktdesignteam entdeckte den Bearbeitungsservice von Protolabs kurz bevor es die Zeichnungen vorlegen sollte.
„Vor der Massenproduktion wollten wir unbedingt irgendwie den Tragekomfort der Bügel und der Nasenauflage physisch bestätigen“, so Kamakura.
Über die Prüfung von Design und Komfort hinaus half der Prototyp den Entwicklern außerdem, von der Operations Division von Epson grünes Licht für die Produktion zu bekommen. Kamakura und sein Team ließen von Protolabs in mehreren Runden Prototypen herstellen, bevor sie das Design fertigstellten.
„Während herkömmliche Methoden der Prototypenherstellung teuer und zeitaufwendig sind, hatten wir mit Protolabs diese Probleme nicht“, so Kamakura. „Wir freuten uns sehr, dass wir den Prototypingzyklus genauso schnell wiederholen konnten.“

Mithilfe der Angebots- und Designanalysesoftware konnten Kamakura und sein Team sich die Risiken bei der Bearbeitung anzeigen lassen und Schnittreste auswerten, um so vor der Produktion alle Probleme auszuräumen. Die telefonische Kundenbetreuung durch die Anwendungstechniker von Protolabs diente nicht nur der Bestätigung der Machbarkeit, sondern verschaffte darüber hinaus Gewissheit zum Produkt und dem Verfahren.
Das Produkt: Verbesserter Komfort
Nach den Verbesserungen bei Design und Entwicklung wurde die Produktqualität von BT-300 schließlich als für ein Epson-Produkt geeignet befunden, sodass die Massenproduktion starten konnte. Profimodelle seien derzeit in der Entwicklung und näherten sich dem Zyklus zur Prüfung von Qualität, Kosten und Lieferzeiten, erklärt Kamakura. „Das Feedback zum Tragekomfort ist hervorragend“, sagt Kamakura. „Da es sich um ein Wearable handelt, wäre ein unbequemes Produkt nicht hinnehmbar.“
Epson ist mit dem Ergebnis des ersten Projekts mit Protolabs zufrieden und möchte daher in Zukunft auf dessen Prototyping-Dienstleistungen zurückgreifen, um den Designprozess künftiger Iterationen zu erweitern. „Bei den neuen Geräten der Moverio Profimodelle nutzen wir den Service [von Protolabs] für verschiedenen Verfahren, darunter den Spritzguss“, verrät Kamakura. „Die Verbesserung des Designs nimmt jedes Mal Zeit in Anspruch, doch wir können die Lieferzeiten nicht verändern. Die mit herkömmlichen Prototyping-Verfahren verbundenen Termin- und Kostenprobleme haben wir mit Protolabs nicht.“
„Die Verbesserung des Designs nimmt jedes Mal Zeit in Anspruch, doch wir können die Lieferzeiten nicht verändern. Die mit herkömmlichen Prototyping-Verfahren verbundenen Termin- und Kostenprobleme haben wir mit Protolabs nicht.
Neben der Zeit- und Kostenersparnis profitierte Kamakura auch von der klaren Kommunikation, einem der Hauptvorzüge bei der Nutzung der Prototyping-Dienstleistungen von Protolabs.
„Bei Prototypen kommt es häufig zu Rechenfehlern“, sagt er. „So kommt es häufig vor, dass ein Formenbauer versucht, ein Formwerkzeug in der einfachst denkbaren Form herzustellen. Diese weicht jedoch von unserer Vorstellung ab, und die Trennfuge verläuft bei der Lieferung woanders. Bei Protolabs hingegen wird auf Probleme mit Trennfugen sowie Oberflächen, an denen Einfallstellen wahrscheinlicher sind, im Vorfeld deutlich hingewiesen. Von daher sind Missverständnisse ausgeschlossen.“
Außerdem freut sich Kamakura bei der Entwicklung auf einen erfolgreichen Zyklus zur Prüfung von Qualität, Kosten und Lieferzeiten. Durch die Möglichkeit der raschen Durchführung mehrerer Iterationen während des Prototypingzyklus verbessert sich die Genauigkeit des Designs, wodurch die Überarbeitung von Formwerkzeug und Design in der Produktionsphase entfällt.
„In der Entwicklung sind Dinge wie Formänderungen unter allen Umständen zu vermeiden, da sie sich in erheblichem Maße nicht nur auf den Entwicklungszeitplan, sondern auch auf die Entwicklungskosten auswirken“, so Kamakura. „In diesem Sinne sind die Prototyping-Dienstleistungen von Protolabs, bei denen die Überarbeitungen deutlich geringer ausfallen, die ideale Vorbereitung für einen erfolgreichen Zyklus zur Prüfung von Qualität, Kosten und Lieferzeiten bei der Entwicklung.“