Aluminio: material de referencia para la automoción, y la industria aeroespacial
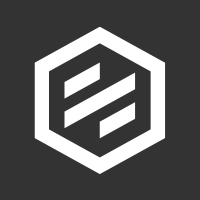
Aplicaciones del aluminio
El aluminio está en todas partes: es el metal más común del planeta. La fina capa de óxido de aluminio que se forma en él cuando se expone al aire lo hace prácticamente libre de corrosión, mientras que su ligero peso evita que sus piezas se comporten como un ancla de barco. Aunque el aluminio no suele reaccionar a los ácidos, tiende a corroerse en ambientes alcalinos (básicos).
En general, el aluminio es adecuado para los aviones y los materiales de construcción, incluidas las estructuras no portantes. Más concretamente, el aluminio 6082 es una opción ideal para los cuadros de las bicicletas, las botellas de buceo, los carretes de pesca, las pequeñas embarcaciones y los chasis de los vehículos. Las mejores propiedades de resistencia del aluminio 7075 son ideales para los moldes de plástico y de utillaje y los bastidores de aviones. Y si se busca un buen conductor eléctrico, el aluminio también es adecuado. Tiene excelentes propiedades de transferencia de calor, por lo que es excelente para los disipadores de calor.
La aleación de aluminio utilizada en nuestro proceso de sinterización directa de metales por láser (DMLS), AlSi10Mg, añade silicio y magnesio. Utilizada a menudo para la fundición, es muy similar a la aleación de la serie 3000, debido a la adición de magnesio como principal elemento de aleación. Las propiedades del aluminio impreso en 3D superan las de su equivalente fundido, excepto por el menor alargamiento a la rotura.
Aplicaciones del titanio
El titanio es también uno de los metales más comunes de la tierra, pero tiene un punto de fusión muy alto, lo que dificulta su transformación en un producto utilizable. Esta es la principal razón por la que es más caro que otros metales. Las piezas de titanio tienen otras implicaciones económicas porque son difíciles de mecanizar. El titanio es conocido por su resistencia y tiene una alta relación resistencia-peso. También tiene una excelente resistencia a la corrosión y es un mal conductor eléctrico.
Una de las ventajas del titanio es su baja expansión térmica. Con un punto de fusión de unos 1660°C, conserva mejor su forma cuando se expone al calor. Además, en lugar de absorber el calor, el titanio tiende a reflejarlo. Por ello, lo encontrará en las ventanas de baja emisividad, que protegen de los calurosos rayos infrarrojos emitidos por el sol.
En cuanto al aspecto, el color del titanio varía en función de su nivel de envejecimiento. Puede variar desde un gris apagado en su forma cruda hasta un plateado brillante cuando se alisa. El titanio utilizado en nuestro proceso DMLS es Ti 6Al4V, más conocido como Ti 6-4. Sus propiedades mecánicas son similares a las del titanio de grado 23 en estado recocido y su resistencia a la tracción es excepcional.
El aluminio es un metal común y popular que se encuentra en una amplia gama de productos: piezas de automoción, componentes aeroespaciales, equipos marinos y navales, electrónica de consumo, incluidos los teléfonos inteligentes, maquinaria industrial, sistemas de climatización, etc. Los ingenieros y diseñadores de productos utilizan con frecuencia el aluminio y sus aleaciones para diseñar tanto prototipos como piezas de uso final.
Los ingenieros y diseñadores de productos utilizan con frecuencia el aluminio y sus aleaciones para diseñar tanto prototipos como piezas de uso final. Este nuevo artículo examina por qué el aluminio es tan comúnmente utilizado, por qué hay tantas aleaciones de aluminio, y ofrece una visión general de las principales aleaciones que utilizamos aquí en Protolabs.

¿Por qué es tan popular el aluminio?
El aluminio tiene una gran relación resistencia-peso, lo que lo hace ligero, pero sobre todo fuerte y flexible. También es asequible, resistente a la corrosión y funciona bien en diversas aplicaciones.
Las aleaciones de aluminio se utilizan a menudo en los coches debido a la versatilidad del material. La conformabilidad y la resistencia a la corrosión del aluminio hacen que sea un material fácil de trabajar y moldear, pero su resistencia estructural cumple el requisito más importante para las carrocerías. La resistencia es importante, pero las carrocerías deben ser ligeras, asequibles de producir, resistentes a la oxidación y tener las cualidades estéticas que desean los consumidores, como unas características de acabado superficial excepcionales. Por lo tanto, el aluminio cumple perfectamente estos requisitos.
Lo mismo ocurre con las piezas aeroespaciales. Las aleaciones de aluminio suelen ser un material de elección para los diseños aeroespaciales, debido a las propiedades de resistencia a la corrosión del aluminio y su alta capacidad de resistencia. En comparación con el acero, es una opción ligera y un material ideal para una amplia gama de componentes de aeronaves y aplicaciones aeroespaciales.
El aligeramiento es un requisito clave de las industrias automovilística y aeroespacial. Ayuda a reducir las emisiones, a cumplir las normas de ahorro de combustible y, lo que es más importante, a reducir los costes de producción.
En el sector aeroespacial, el uso de aleaciones de aluminio reduce significativamente el peso de un avión, ya que es mucho más ligero que el acero, lo que permite a los aviones cargar más peso, aumentar la eficiencia del combustible y reducir los costes. La reducción de peso está estrechamente relacionada con el consumo de combustible. Teniendo esto en cuenta, hay muchas aplicaciones comunes en el sector aeroespacial, muchas de las cuales están hechas de metal: boquillas de distribución de combustible, intercambiadores de calor, colectores, turbobombas, canales de refrigeración, sujetadores, etc.
¿Por qué hay tantas aleaciones?
El aluminio, como elemento puro, tiene muchas propiedades. Sin embargo, el aluminio por sí solo puede no ser lo suficientemente fuerte para ser utilizado con una buena durabilidad. El aluminio puede combinarse con otros elementos para formar aleaciones, que son más duraderas y se adaptan mejor a las aplicaciones industriales.
Que signifient les chiffres dans le nom de l'alliage ? Il existe 3 façons courantes de classer les métaux en Europe, c'est pourquoi nous avons inclus les 3. Voici comment les interpréter :
Aluminio 6082 |
T651 |
3.2315 |
AlSi1MgMn |
Norma EN |
Temper condition |
EN 10027 / DIN 1745 |
ISO Composition |
Norma EN
La serie del aluminio nombra los elementos con cuatro dígitos, en los que el primero representa el elemento principal de la aleación, el segundo indica una modificación de una aleación específica, y el tercero y el cuarto son números arbitrarios asignados a aleaciones específicas de la serie. Por ejemplo, el 6082 forma parte de la serie 6000 (y es casi idéntico al 6061).
Condición de templado
Independientemente del la Condición de templado, la composición química de la aleación sigue siendo la misma. En nuestro ejemplo, el T651 suele denominarse T6 (lo que significa que ha sido tratado térmicamente y envejecido artificialmente). El calentamiento, la embutición y el envejecimiento (calentamiento o enfriamiento controlado) son métodos utilizados para mejorar la combinación de resistencia y tenacidad de una pieza.
EN 10027 / DIN 1745
Cada metal tiene un código único de 4 dígitos: los aceros van de 1.000 a 1.970. Las aleaciones de cobre están en el rango de los 2.000. Las aleaciones de aluminio están en el rango de los 3.000.
ISO
Esto corresponde a la composición química. Por ejemplo, la composición química del aluminio 6082 es AlSI1MgMN, el primer componente Al es el más presente en %. A continuación, se indican los demás componentes en orden descendente. Si no hay ningún número, significa que es <1%.
Esto puede ilustrarse de la siguiente manera :
- AlSi1MgMn = ~99% Aluminio, Silicio (<1%), Magnesio 1%, Manganeso (<1%).
- Ti6Al4V = ~90% Titanio, 6% Aluminio, 4% Vanadio.
Para conocer la composición química exacta, incluidos los oligoelementos, consulte nuestras fichas técnicas.
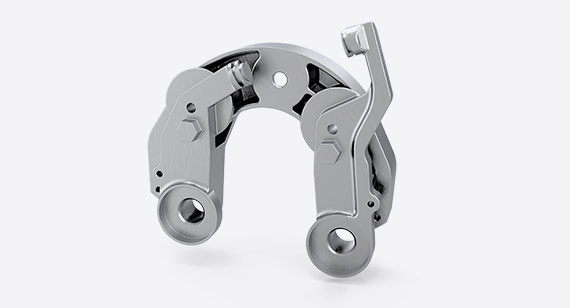
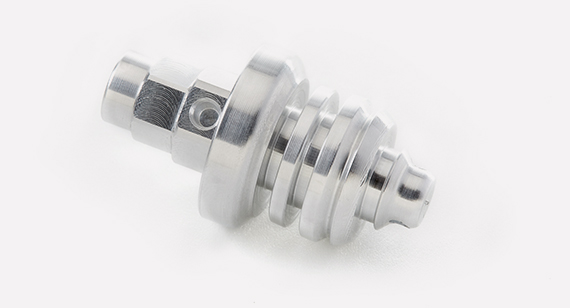
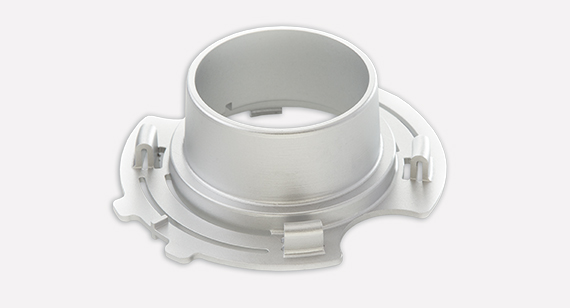
Las aleaciones más comunes
Aluminiio 6082-T651 | 3.2315 | AlSi1MgMn
El aluminio 6082-T651 es la aleación de aluminio más utilizada en Protolabs. Si necesitas un excelente todoterreno, esta es una excelente opción. El aluminio 6082 se utiliza principalmente para el mecanizado CNC. Suele elegirse cuando es necesario soldar la pieza o simplemente por su alta resistencia a la corrosión. La formabilidad es excelente en la condición O y buena en la condición T4. El endurecimiento T6 es más resistente. Se utiliza en la industria aeroespacial, piezas de automóviles, equipos marinos, muebles, electrónica de consumo, equipos deportivos y muchos otros.
Principalmente aluminio; aleado con hasta un 6,1% de zinc, 2,9% de magnesio, 2% de cobre y otros elementos.
Aluminio 5083-H111 | 3.3547 | AlMg4.5Mn0.7
Esta aleación tiene buena maquinabilidad, muy buena resistencia a la corrosión, alta resistencia a la fatiga, soldabilidad y resistencia moderada. Es ideal para su uso en líneas de combustible y aceite de aeronaves, depósitos de combustible, otros transportes, automoción, marina, etc.
Principalmente aluminio; aleado con hasta un 4,9% de magnesio, un 1% de manganeso y un 0,4% de hierro, además de otros elementos.
Aluminio 7075-T651 | 3.4365 | AlZn5.5MgCu
La 7075 es la aleación aeroespacial estándar de la serie 7000 y tiene un buen equilibrio de propiedades necesarias para las aplicaciones aeroespaciales, especialmente bajo altas cargas estáticas.
Predomina el aluminio, aleado con hasta un 6,1% de zinc, un 2,9% de magnesio, un 2% de cobre y otros elementos.
Se utiliza para accesorios de aviación, engranajes, válvulas, herramientas de moldeo, equipos de bicicleta, equipos de camping y deportivos, etc., debido a sus características de ligereza y resistencia. La adición de cromo a la mezcla proporciona una buena resistencia al agrietamiento por corrosión bajo tensión y una mayor resistencia a la fatiga de 160 MPa.
Aluminio 7075-T7351 | 3.4365 | AlZn5.5MgCu
Tratamiento térmico y envejecimiento artificial especial para la resistencia a la corrosión bajo tensión. Al tomar el T6 y sobreenvejecerlo, pierde algo de resistencia pero aumenta la dureza. Esto lo hace más duradero y adecuado para aplicaciones aeroespaciales y de muy baja temperatura, como los satélites y la criogenia.
Aluminio 2024-T351 | 3.1355 | AlCu4Mg1
De grado aeroespacial, la serie 2000 tiene una resistencia a la tracción final (UTS) inferior a la de la 7075, pero una mejor elongación y resistencia a la fatiga. Por lo tanto, es ideal para aplicaciones que requieren una alta resistencia a la fatiga cíclica o para estructuras en tensión.
Principalmente aluminio; aleado con hasta un 4,9% de cobre, un 1,8% de magnesio y un 0,9% de manganeso, además de otros elementos. T351 se refiere al endurecimiento T3: tratamiento térmico de la solución, trabajo en frío y envejecimiento natural. Al igual que el T4, ofrece una buena conformabilidad con una dureza y una resistencia a la tracción final (UTS) ligeramente inferiores. Mayor resistencia a la fatiga de 140 MPa
Aluminio casting 3000 series | 3.2381 | AlSi10Mg
Esta aleación, pilar de nuestro proceso de impresión 3D por sinterización directa de metales (DMLS), es comparable a la aleación de la serie 3000 utilizada en los procesos de fundición y moldeado a presión. Tiene una buena relación resistencia-peso, alta resistencia a la temperatura y a la corrosión, y buena resistencia a la fatiga, a la fluencia y a la fractura. El AlSi10Mg también tiene una buena conductividad térmica y eléctrica. Las piezas de AlSi10Mg se someten a un tratamiento térmico después de la soldadura láser.
Si tiene alguna pregunta sobre las aleaciones de aluminio, otros materiales o cualquiera de nuestros servicios de fabricación en Protolabs, póngase en contacto con un ingeniero de aplicaciones en customerservice@protolabs.es o en el +34 932 711 332
