Materiales plásticos para aplicaciones y dispositivos médicos
La seguridad y la vida útil son dos aspectos clave en esta lista de plásticos para uso médico

¿Te dedicas al diseño de piezas médicas? Al igual que hay innumerables tipos de procedimientos médicos, en el mercado actual también hay innumerables tipos de polímeros. ¿Cuáles son los mejores para mi aplicación médica? Buena pregunta. En esta sugerencia de diseño intentaremos ofrecerte alguna orientación, pero es importante empezar con la siguiente advertencia: el término "uso médico" es ambiguo en el mejor de los casos.
Los fabricantes de dispositivos médicos deben conocer y cumplir una serie de estándares, pero para este análisis, el ISO 10993 es el principal. Tiene casi dos docenas de partes, de las cuales cuatro se refieren específicamente a la selección de materiales y, de estas, el ISO 10993-13 es probablemente el más relevante para los polímeros.
Unfortunately, there’s no catalogue or book that lists which polymers meet which standards, or even which polymers are biocompatible. Compounding matters is the sheer number of resins, pellets, powders, and bulk forms like rod and sheet from which to choose, each with multiple manufacturers that may or may not meet the necessary Desafortunadamente, no existe ningún catálogo o libro que enumere qué polímeros cumplen qué estándares o incluso qué polímeros son biocompatibles. Para complicar las cosas, hay muchísimas resinas, granulados, polvos y formas a granel, como varillas y láminas, entre los que se puede elegir, y cada uno tiene diversos fabricantes que pueden cumplir o no los requistos necerrarios para los dispoditivos médicos. Mientras que uno puede proporcionar un ABS para uso médico, otro puede fabricar un ABS adecuado para piezas de LEGO y carcasas de herramientas eléctricas.
Lógicamente, en una entrada de blog no se puede tratar todo lo que necesitas saber sobre los plásticos para uso médico, así que recuerda que puedes consultar las estadísticas en nuestra página de comparación de materiales. Dicho esto, estos son seis polímeros esenciales que debes tener en cuenta para tu próximo proyecto de piezas médicas.
Comparación de plásticos para piezas médicas
Por lo general, los diseñadores y fabricantes de dispositivos médicos deben buscar polímeros resistentes a la corrosión, al ataque químico y a las altas temperaturas. Estos deben ser no absorbentes e inertes y deben ser capaces de soportar repetidos ciclos de esterilización en autoclave. Por supuesto, no deben reaccionar con los fluidos corporales y los tejidos humanos, ni provocar irritación o crear sensibilidades en la piel. ¿Hemos mencionado la resistencia y la durabilidad? Todo esto puede parecer muy complicado, pero la buena noticia es que hay bastantes polímeros que cumplen al menos la mayoría de estos requisitos.
PC
A menudo se necesita un polímero ópticamente transparente para los procedimientos médicos y el policarbonato es el material idóneo. Cumple todos los requisitos habituales en cuanto a resistencia, estabilidad dimensional, resistencia química y al calor, y capacidad de esterilización. Aunque no lo encontrarás dentro del cuerpo humano, el PC se suele utilizar para ver cómo fluyen la sangre, los medicamentos y otros fluidos a través de un dispositivo. Muchos de los clientes médicos de Protolabs imprimen en 3D sus diseños con materiales similares al PC, como Acura 5530 y PerFORM, y luego pasan a utilizar policarbonato mecanizado o moldeado por inyección, como Makrolon 2458, a medida que aumentan las necesidades de producción.
UHMW-PE
Y ya que hablamos de implantes ortopédicos, aquí hay otro polímero importante que hay que tener en cuenta: el polietileno de peso molecular ultra alto. Si te has sometido a una prótesis de rodilla o de cadera, es muy probable que hayan usado este material. El UHMW-PE es un miembro de la familia del polietileno muy denso y de baja fricción. Si estás buscando componentes médicos mecanizados (o piezas de maquinaria resistentes al desgaste), el UHMW-PE tiene una excelente resistencia al impacto y a la abrasión y, de nuevo, es claramente biocompatible. Y para aplicaciones un poco menos exigentes, el polietileno "normal" (PE) y el polietileno de alta densidad (HDPE) son buenos polímeros para una amplia gama de aplicaciones médicas, especialmente para productos de un solo uso y para los equipos de protección individual (EPI) que tanto se han usado en los últimos años.
PEI
Al igual que la PEEK, la polieterimida pertenece a la familia de los superpolímeros. Más conocida por su nombre comercial Ultem, la PEI es un polímero rígido, semitransparente y resistente al calor (180 °C), de color ámbar y con una gran resistencia a la tracción. Dado que también tiene altas características dieléctricas y resistencia a las llamas, se utiliza mucho en componentes electrónicos, médicos o de otro tipo. La PEI se mecaniza y se moldea por inyección en diversas formas, con usos potenciales como mangos para instrumental quirúrgico, carcasas de dispositivos médicos, aislantes, conectores eléctricos, etc. Por último, la PEI se esteriliza fácilmente mediante autoclave y radiación gamma.
PSU
Otro polímero de color ámbar es la PSU, abreviatura de polisulfona. Reconocida por su resistencia y rigidez a temperaturas elevadas, la PSU es menos resistente que la PEI, pero más resistente a los impactos. Se puede mecanizar o moldear en carcasas de filtros, puertos de catéteres, bandejas de instrumental quirúrgico y dispositivos de dimensionamiento para su uso durante la sustitución de válvulas cardíacas. Se dice que la polisulfona es uno de los pocos polímeros capaces de resistir más de 1.000 ciclos de esterilización por vapor (al igual que la PEEK y la polifenilsulfona o PPSU, pariente de la PSU, que es aún más resistente al impacto y al calor).
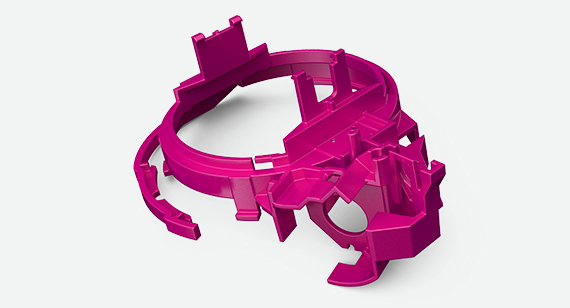
Este componente médico de IDEXX Laboratories, Inc. forma parte de un instrumento que los veterinarios utilizan para analizar la sangre y la orina.
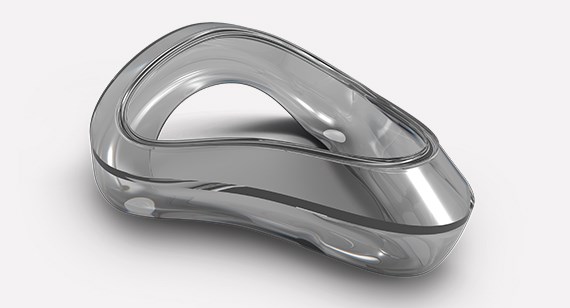
Pieza moldeada fabricada con silicona líquida (LSR) de uso médico.
PEEK
La polieteretercetona es un buen punto de partida. Considerada durante mucho tiempo como un termoplástico "técnico", la PEEK se utiliza mucho en el sector médico. Los cirujanos ortopédicos la utilizan para la fijación de traumatismos, implantes de columna y reemplazo de articulaciones, mientras que los dentistas la utilizan en coronas y puentes. La PEEK es ligera y resistente, es radiopaca (es decir, aparece en las radiografías) y mantiene su resistencia y estabilidad dimensional a altas temperaturas. Y dado que la PEEK suele introducirse en el cuerpo humano durante largos períodos de tiempo, no hace falta decir que es biocompatible y esterilizable. Protolabs somete rutinariamente la PEEK a mecanizado CNC y moldeo por inyección de plástico para componentes mecánicos como engranajes, superficies de rodamiento y colectores, así como para otras muchas piezas médicas.
Silicone
La silicona, que es el material de los adhesivos resistentes a la intemperie y de los utensilios de cocina, es también una excelente opción para muchos componentes médicos. La silicona está disponible en varios niveles de dureza, desde la blanda y elástica, como una goma elástica, hasta la rígida, como la banda de rodadura de un neumático. Soporta temperaturas desde bajo cero hasta el calor del horno (de -55 °C a 210 °C), es hidrofóbica (repele el agua), resistente a los disolventes y ácidos, y tiene una buena permeabilidad al vapor, lo que la convierte en una de las favoritas para los dispositivos protésicos. Protolabs imprime en 3D una gran variedad de componentes médicos, como sellos, juntas y modelos quirúrgicos, y moldea por inyección todo tipo de prototipos y piezas de producción de uso final utilizando silicona líquida (LSR).
Puedes incluso imprimir en 3D en silicona, una gran opción para la creación de prototipos con este material para piezas complejas o antes de pasar al moldeo por inyección para las tiradas de producción. Además, también existe un grado óptico de silicona líquida (LSR), el OSLR, que goza de unas propiedades de refracción y transmisión de la luz superiores a las de sus alternativas de PC o PMMA (acrílico). Por tanto, se utiliza mucho en lentes y aplicaciones de iluminación, o en cualquier lugar en el que se necesite un polímero biocompatible transparente, que no amarillee y que sea resistente al calor y a los productos químicos.
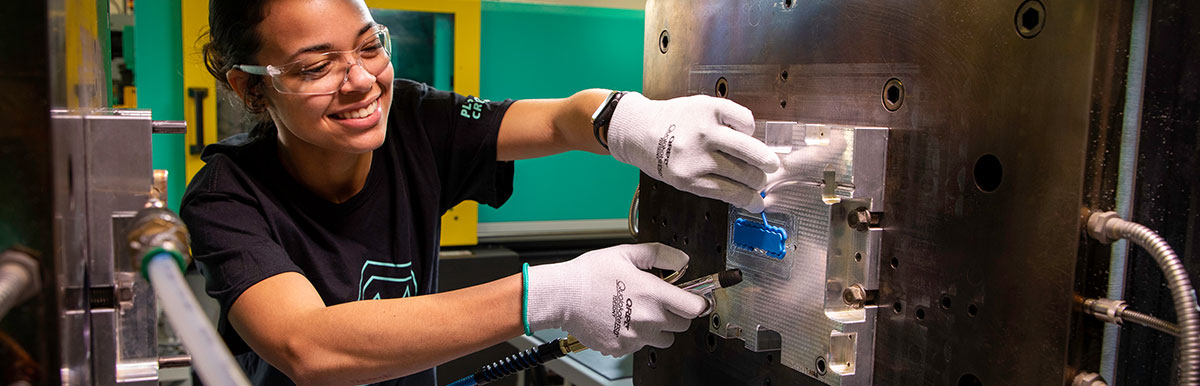
An operator removes a silicone part from the LSR press. Due to the elasticity of silicone parts, manual removal is necessary.
Más opciones a tener en cuenta
Estos seis polímeros de uso médico son solo el punto de partida. No podemos dejar de mencionar el PTFE, más conocido como teflón, un polímero superlubricante que se utiliza en todo tipo de productos, desde catéteres y stents hasta máquinas de circulación extracorpórea. El acrilonitrilo butadieno estireno (ABS), resistente a los impactos y a los productos químicos, a veces se utiliza para sustituir los componentes estructurales metálicos de los equipos médicos, al igual que el acetal (quizá lo conozcas como Delrin), mientras que el policloruro de vinilo (PVC) podría considerarse una versión flexible del policarbonato en determinadas aplicaciones. El tereftalato de polietileno (PET) resiste los ataques de los microorganismos, por lo que es adecuado tanto para envases de refrescos como para sensores portátiles. El polipropileno (PP) (aunque se considera un plástico básico) se utiliza mucho en frascos de muestras, envases de medicamentos y jeringuillas hipodérmicas desechables (también es una gran opción para piezas en la que vendría bien una bisagra flexible).
Como en cualquier aplicación de fabricación, la elección del mejor material para un dispositivo médico se reduce a sus requisitos físicos, químicos y eléctricos, sin olvidar su entorno de funcionamiento. También hay que tener en cuenta la fabricabilidad y todas las normas de diseño relacionadas. Y al final del proceso de diseño y creación de prototipos, solo queda esperar el calvario de la aprobación por parte de la FDA. Puede que todo este proceso te parezca muy complicado, así que te animamos a cargar un archivo, obtener un presupuesto y llamarnos para hablar de las opciones disponibles. Hemos ayudado a innumerables personas que alguna vez estuvieron en tu lugar.