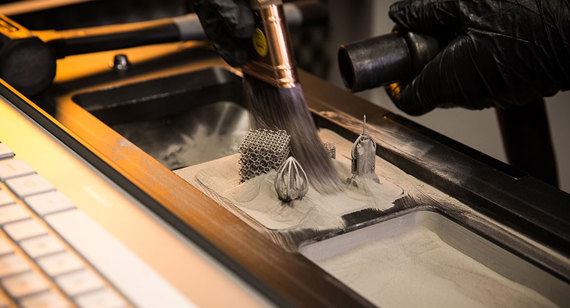
For the layman, we imagine 3D printing to be simple. It's the same as opening a document and hitting print, right? In reality, 3D printing is immensely technical and requires considerable knowledge to create, set up, and finish a complete 3D printing product. This blog explores some of the most common technical terminology in 3D printing, including the intricacies of Additive Manufacturing, CAD, G-Code, Extruders, and more.
Additive Manufacturing also known as 3D printing, refers to creating three-dimensional objects by adding material layer by layer. As the name suggests, it is an additive process rather than a subtractive process such as CNC machining. Various additive manufacturing technologies exist, including stereolithography (SLA), direct metal laser sintering and Multi Jet fusion. Additive manufacturing offers flexibility, speed, and the ability to create complex geometries that might otherwise be challenging or impossible to achieve using traditional manufacturing methods.
Build Plate the surface upon which the object is constructed on.
CAD (Computer-Aided Design) refers to using computer technology to create, modify, analyse, or optimise designs for various purposes. CAD software allows designers, engineers, architects, and other professionals to produce precise two-dimensional (2D) and three-dimensional (3D) objects or systems.
Deposition refers to the process of adding material layer by layer to build a three-dimensional object. This technique involves depositing successive layers of material to a digital design or model created using CAD software. A thermoplastic filament is fed into a heated nozzle in deposition-based 3D printing technologies like Fused Deposition Modelling or Fused Filament Fabrication. The material is melted and extruded onto the object's build plate or previous layers in precise paths determined by the digital model. As each layer is deposited, it fuses or solidifies with the preceding layers, gradually forming the final part.
Extruder is the mechanism responsible for melting and depositing the filament material onto the build plate to create the object layer by layer—a critical component in deposition printing such as FDM (Fused Deposition Modelling).
Filament the material used as the primary substance for creating parts (using deposition printing), fed into a 3D printer’s extruder. Filaments come in various types and compositions, such as ABS, PETG, TPU and Nylon.

G-Code a set of instructions or commands in a standardised language that tells the (FDM) 3D printer how to create a part. A sequence of alphanumeric codes that control movement, speed, temperature and other necessary parameters to produce a 3D-printed part. Generated from slicing software (which converts a 3D model into a printable layer). G-code-specific commands guide the printer’s extruder and build plate, including instructions for movements along the X, Y, and Z axes, extrusion rates, heating and cooling temperatures, fan speeds and other settings relevant to the printing process. Here is an example of what some G-Code commands might look like
- G0/G1 – Move to a specific position at a certain speed
- G28 – Home all axes (return to the reference point)
- G92 – Set current position to specified coordinates
- M104 – Set extruder temperature
- M140 – Set bed temperature
- M106 – Control fan speed
Heated Bed is a platform on which the object being printed is built layer by layer. The bed is heated to a specific temperature, which is usually between 50 to 100 degrees Celsius or higher, depending on the filament material used. The main purpose of the heatbed is to prevent warping and improve adhesion between the first layer of the print and the bed itself.
Infill the internal structure of a printed part. Typically a pattern of lines, grids, or triangles. You can adjust the infill density, specifying how much of the interior space is filled with material. This is instead of printing a solid part, which would use more material and take longer, it also affects the weight of the part. The choice of infill will depend heavily on what is required of the part. If a part requires a high level of structural integrity or will bear a lot of weight, it might benefit from higher infill percentages for added strength. Adjusting infill density allows for a balance between strength, material usage, and printing time.
Jams are when the filament (material used for printing) gets stuck or blocked in the extruder, nozzle or another part of the 3D printer’s feeding system, disrupting the process. Several factors contribute to jams, such as filament issues (tangles, knots or irregularities), extruder problems (clogged or partially blocked), print settings, and mechanical issues.
Kapton Tape a heat-resistant adhesive tape, commonly used in (FDM) 3D printing. It’s a polyimide file tape that can withstand high temperatures, typically 200 to 300 degrees Celsius (or even higher in some cases). Kapton tape will often be applied to the print bed, particularly for printers that don’t have a built-in heated bed for materials that require higher bed temperatures. The primary purpose of the tape is to provide a flat, durable, and heat-resistant surface for the first layers of the print to adhere to. This will help prevent warping and promote better adhesion, especially with materials such as ABS that tend to warp if the print bed isn’t sufficiently heated. Kapton tape has excellent thermal conductivity, which allows it to distribute heat evenly across the print surface.

Layer Height refers to the vertical thickness of each layer that makes up a printed object. When using 3D printing your part is built in a printer layer-by-layer. The layer height determines the thickness of each of these layers. So, if the layer height is set at 0.2mm, each layer of the printed part will be 0.2mm thick. The smaller the layer height the finer the detail. It should be noted that smaller layers can increase the time it takes to print the part (because the printer has more to create.)
Microstepping is a technique that is used to improve control and attain a smooth print.
It breaks a single step into smaller steps, resulting in smaller increments of movement.
If a stepper motor has 200 steps per revolution, and microstepping divides each of these full steps into 16 smaller microsteps. The stepper motor is then making 3,200 microsteps per full revolution.
So why use microstepping? Microstepping can be beneficial for several reasons, such as, smooth movement, and improved precision.
Nozzle is the part responsible for depositing and shaping the material used to create the layers that form the final part. The nozzle is typically made of brass (though occasionally other heat-resistant materials are used). They come in various sizes ranging from 0.2mm to 1mm in diameter, with 0.4mm being the most common. The nozzle size impacts the level of detail, print speed, and material flow rate. Smaller nozzles are suitable for intricate part designs that require fine detail. Larger nozzles can speed up the printing process.
Overhang refers to material that extends beyond the previous layer without any support from the below. Essentially, it’s an area where the printer lays down material in mid-air. They can pose challenges because the molten material tends to droop or sag when printed in mid-air. Without the proper support, these sections may not print accurately. Most 3D printers can handle minor overhangs without additional support up to a certain angle (usually 45 degrees) without compromising the print quality. However, as the angle of overhang increases beyond the printer’s capability to print without support, "support structures" become necessary.
Support structures are used to provide temporary support to overhangs during the print process (they literally hold them up). These supports are later removed manually or by dissolving them once the print is complete.

Print Bed Levelling ensures the build surface of the 3D printer is perfectly aligned and parallel to the nozzle/s. A level print bed is essential for adhesion and consistent layer height. If the bed is uneven or too far/too close to the nozzle, it can cause adhesion issues, leading to poor print quality or even failure to print. Proper bed levelling also helps maintain a consistent layer height across the entire build surface. This ensures uniformity and accuracy in the printed part.
Quality Control a series of processes and measures implemented to ensure that the printed objects meet certain standards, specifications and desired characteristics. At Protolabs, we use and offer a vast array of quality checks and certifications, such as ISO 13485 for medical parts, powder analysis & material traceability, quality inspection and much more. Learn about our other quality control processes here.
Raft refers to a supplemental structure printed underneath the actual part. It’s an additional layer or series of layers that serve as a foundation or support structure. The raft is printed directly onto the print bed and is a stable base for the first layers. Rafts can help by improving adhesion, providing support for overhangs, levelling, and calibration.
Slicer is software that converts a 3D model (typically in STL or OBJ file format) into instructions (G-code) that the 3D printer can understand and execute. It slices the 3D model into thin horizontal layers, generating a set of instructions for the printer on how to build each layer to create the final printed object. The slicer software allows users to adjust various parameters and settings influencing the printing process, including layer height, print speed, infill density, support structures, brim raft or skirt and print temperature.
Toolpath refers to the specific path that the print head (or extruder) follows while depositing material, creating each layer of the printed part. The toolpath determines how the printer will move over each layer, it also determines infill patterns, perimeter (outer walls), top and bottom layers, and support structures. Optimising the toolpath is crucial to achieving an accurate print with the desired surface finish, strength, and dimensional accuracy.

UV Curing is a post-processing technique used predominantly in resin-based 3D printing processes like stereolithography. This process uses liquid photopolymer resin, which solidifies or cures when exposed to specific wavelengths of ultraviolet (UV)light. When the a part using resin-based material finishes it's print cycle it typically isn't fully solidified. It remains in a semi-solid state and may have excess, uncured resin on its surface. UV curing exposes the part to additional UV light to fully harden and solidify the resin. This UV curing ensures that the object achieves its maximum mechanical properties.
UV curing enhances the strength, durability, and surface finish of 3D-printed parts.
Viscosity refers to the measure of a material’s resistance to flow. Depending on the 3D printing surface used "viscosity" can have a different affect. For example, fused deposition modelling (FDM) viscosity affects how smoothly the material flows through the printer’s extruder nozzle. Filament with a higher viscosity may struggle to flow, leading to clogging, which will lead to inconsistent flow. Whilst low viscosity may lead to excessive flow, which can mean stringing or drooping between sections. In resin-based printing methods such as stereolithography (SLA), viscosity affects how the material spreads across the build platform and solidifies when exposed to light. Resins with a higher viscosity tend to spread less, resulting in less detailed parts or difficulties achieving smooth surfaces. Resins with lower viscosity will flow easily, enabling better detail in intricate prints, but could potentially cause overflow or inaccuracy, if not appropriately controlled.
Warping is deformation or lifting of the edges or corners of a printed part occuring during or after the part is printed. It occurs when areas of the printed part contract or lift away from the print bed, resulting in a warped or distorted final part shape. Several factors contribute towards warping, including temperature fluctuations, poor bed adhesion, printing on large flat surfaces, and high print temperatures. Warping can be mitigated by employing several techniques, such as the use of a heated print bed, enclosure, use of adhesion aids and optimising print settings.
X-Axis Typically the horizontal axis that runs from left to right, perpendicular to the Y and Z axes.
Y-Axis Typically the horizontal axis that runs from the front to the back of the printer, perpendicular to both the X and Z axes.
Z-Axis Typically the vertical axis that runs up and down, perpendicular to the X and Y axes.
There are many other 3D printing terms you are likely to hear; to learn more, please visit our glossary.