Online CNC Machining Service for Custom Parts
Manufacture prototypes in 1 day and scale to production in a single place. Get started with a free instant quote and interactive design analysis.
shield_locked All Uploads are Secure and Confidential
ISO 9001:2015 | ISO 14001:2018 | JOSCAR
Trusted By | ![]() |
![]() |
![]() |
![]() |
We offer the most comprehensive custom machining service, from prototypes in a single day to complex parts at production volumes, available via online platforms that can instantly quote most orders. Continue reading to find out more

Consultation with a Technical Expert
Our in-house technical experts are waiting to support you with a whole host of requirements such as:
- Technical consultation for your project
- Design tips
- Our quoting platform and its design analysis software
Book a free consultation today, to discuss your part.
Book a MeetingDesign Guidelines for CNC Machining
Please contact us for any project that requires:
- Additional features not covered in this table
- Controlled goods, such as subject to dual use & military trade compliance. Please read and acknowledge our code of conduct and trade compliance policy.

Aluminium 6082 Golf Ball
expand_moreSurface Finish: As Machined

Aluminium 6082 - Hexagon
expand_moreSurface Finish: As Machined

Aluminium 6082 - Mini CNC Machine
expand_moreSurface Finish: Bead Blasted

Aluminium 6082 - Ball in Cube
expand_moreSurface Finish: Bead Blasted
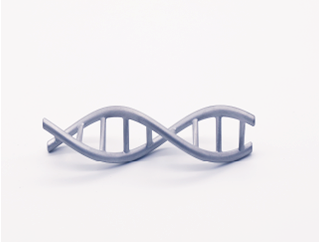
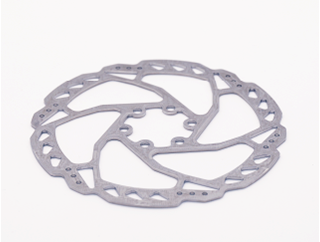
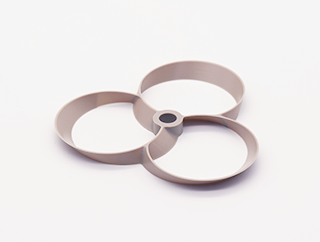
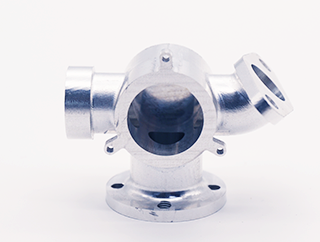
CNC Machining FAQs
What are the advantages of CNC Machining?
expand_less expand_moreThe subtractive process of CNC machining provides multiple benefits for both prototyping and low-volume production parts.
- Precision and repeatability
- Tight tolerances
- Production-grade materials
- Quick-turn parts within 1 day
- Robust post-processing to improve cosmetics and material properties
What are the applications of CNC machining?
expand_less expand_moreCNC machining is widely used throughout the aerospace, medical, automotive industries for its ability to rapidly manufacture precise parts in production-grade materials. Typical CNC parts, include:
- Housings and enclosures
- Brackets
- Fixtures for manufacturing
- Gears and bearings
- Internal mechanical components
- Medical instrumentation
Why choose Protolabs for CNC Machining?
expand_less expand_moreFast Reliable Delivery - Iterate part designs quickly and accelerate product development with quick-turn parts. Our automated design analysis will help spot any difficult to machine features before your design is sent to the manufacturing floor and save you from costly reworks further down the product development cycle.
Design for Manufacturability Feedback - When you upload your 3D CAD file to request a quote, we'll analyse your part geometry to identify any features that may be difficult to machine such as tall, thin walls or holes that cannot be threaded.
European Production and Support - Work with a trusted European based manufacturer and eliminate the risk of sending parts overseas. You can also call or email us at any time and we'll help with ordering parts, design feedback, material recommendations, and answer any questions.
Infinite Capacity - Eliminate downtime spent waiting for parts and safeguard in-house machining with on-demand relief and infinite manufacturing capacity.
Material Selection - We stock more than 30 engineering-grade plastic and metal materials that are suitable for various part applications and industries. Materials range from plastics like ABS, polycarbonate, nylon, and PEEK to aluminium, stainless steel, magnesium, and copper.
CNC Flexible Lead Time Option -
Our new CNC Flexible Lead Time option puts you in control of when you want your CNC parts shipped and how much you pay. If you can wait between 6 and 12 days then you will get a discounted price by using our flexible manufacturing option, which is still a far quicker guaranteed lead time than most other suppliers.
Alternatively, you can opt for our standard delivery of just 3 days, or if you have an urgent deadline to meet then we can ship your parts in as little as 1 day, using our expedited manufacturing service. Whichever you choose, you can now work to turnaround times that are best for your project.
How much does CNC Machining Cost?
expand_less expand_moreCosts vary based on complexity, quantity and lead time. The best way to find out is to submit a 3D CAD model and get an interactive quote with design for manufacturability (DFM) feedback. Because we use proprietary software and automated fixturing processes, there are no up front non-recurring engineering (NRE) costs. This makes purchasing quantities as low as 1 to 200 parts cost effective. Prices compared to 3D printing are comparable to somewhat higher, but machining offers improved material properties and surfaces.
What types of threading options are available?
expand_less expand_moreWe offer UNF, UNC, and metric threads for machining along with coil and key inserts (but do not supply or install the inserts). These are available on both milled or turned CNC parts. View this page to see our complete threading options.
What is the maximum part size for CNC Machining?
expand_less expand_moreAt our factory maximum part size will vary based on your selected material. Our largest part size offered is 559mm x 356mm x 95.25mm and is available in Aluminiums. View this table to see maximum dimensions by material.
For anything larger you can use our partner network.
Where can I learn more about CNC design?
expand_less expand_moreWe have a variety of resources on CNC machining and how to design parts for the process. Here are some of our favorites:
What is the Protolabs digital network?
expand_less expand_moreOur global network of premium manufacturing partners powered offers expanded capabilities, tighter tolerances, volume pricing, and the ability to handle more complex parts. You can view full capabilities of our partner network here.
What Secondary Operations are available for CNC Machining at Protolabs?
expand_less expand_moreWe have a wide selection of finishing optopmns for CNC machining that strengthen parts, improve cosmetic appearance, provide customisation, and other benefits. To learn more about the finishes available, you can review our finishing options for CNC machined parts page.
What CNC Machining Surface Finishes are available at Protolabs?
expand_less expand_more
Material: ABS Black
Finish: As machined with sharp edges removed
Material: ABS Natural
Finish: As machined with sharp edges removed
Material: Aluminium
Finish: As machined with sharp edges removed
Material: Aluminum
Finish: Light bead blast
What are the CNC Machining Tolerances Guaranteed at Protolabs and Protolabs Network?
expand_less expand_moreTolerances guaranteed by Protolabs
Typically, Protolabs will maintain a general machining tolerance of ±0.1 mm or better.
The tolerance will be clearly stated on your quote, at this stage it is not possible to select tigher tolerances for factory options made in a few days, but our partner network can produce to tighter tolerances.
Parts may be as thin as 0.5 mm in regions as long as nominal part thickness is above 1 mm. Maximum tool depth that can be milled is 50 mm from any side of the part. For specific milling dimensions by material, see maximum part extents for machining.
Surface finish: Typically, Protolabs offer a surface finish of < 1.6 µm Ra (Roughness average) across the range of CNC materials. Ra 6.3 µm to Ra 0.8 µm are typical for general CNC machining. Optional bead blasting will result in a slightly rougher, but uniform, matt finish. See the surface finish guide for detailed images.
All components are inspected and measured, using calipers, micrometres, pin and thread gauges. Dimensional Inspection Reports (DIRs), using high accuracy Coordinate Measurement Machines (CMM’s) are also available on request.
ISO are the International Organisation for Standardisation and issue global standards to harmonise manufacturing. ISO 2768 defines three tolerances classes, fine, medium and course. Each class has a tolerance band proportional to the nominal dimension being measured. The main benefit of using a general tolerance, like ISO 2768-f, is that components can be produced directly from 3D CAD without the need for a 2D drawing. It also greatly simplifies producing a 2D drawing, as every dimension already has a tolerance applied, fewer tolerances need to be added to define critical dimensions.
Tolerances guaranteed through our digital network
Through our digital network of manufacturers, we guarantee that our partners follow ISO 2768 standards for all CNC machined parts. For metal parts you have the choice of ISO 2768-m (medium) or ISO 2768-f (fine). Parts machined from plastics will follow 2768-m (medium). Geometric tolerances down to ±0.010 mm are possible but must be clearly indicated in technical drawings. Our network can achieve tighter tolerances on shafts and holes, with up to H7 fits (ISO 286-2), and on occasion even tighter tolerances via manual quoting. Find out more about our digital network.
All network partners follow ISO 2768 standards for CNC machining. It is possible to select medium or fine for metals. Further accuracy can be requested using 2D drawing tolerances.
Our factory will either follow ISO 2768 standards for CNC machining or provide a general tolerance of ±0.1 mm. There are no selectable options, so 2D drawings are not required.
Factory only | Network metals only | Network plastics or metals | |
Internal corner radii | Detailed on 3D quote | R2 mm as standard* | R2 mm as standard* |
Tolerance method nominal dimension# | General Tolerance | ISO 2768-f fine | ISO 2768-m medium |
0.5mm** to 3mm | ±0.1 mm | ±0.05 mm | ±0.1 mm |
Over 3mm to 6mm | ±0.1 mm | ±0.05 mm | ±0.1 mm |
Over 6mm to 30mm | ±0.1 mm | ±0.10 mm | ±0.2 mm |
Over 30mm to 120mm | ±0.1 mm | ±0.15 mm | ±0.3 mm |
Over 120mm to 400mm | ±0.1 mm | ±0.20 mm | ±0.5 mm |
Over 400mm to 1000mm | ±0.1 mm | ±0.30 mm | ±0.8 mm |
Over 1000mm to 2000mm | Not applicable | ±0.50 mm | ±1.2 mm |
Over 2000mm to 4000mm | Not applicable | Not applicable | ±2.0 mm |
# ISO 2768 is feature based: the tolerance band will apply to each and every feature on your part and is not related to overall part size.
*A radii of 2 mm will be applied to sharp internal corners as standard, more options can be requested.
** Please clearly indicate tolerances for nominal sizes below 0.5mm on your technical drawing