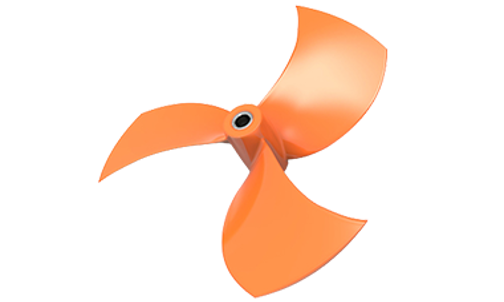
Overmoulding and Insert Moulding
Get custom plastic parts molded with two materials or metal inserts. Upload a part to get an online quote.
ISO 9001:2015 | ISO 14001:2018 | Critical to Quality Inspections
Our overmoulding and insert moulding processes produce custom prototypes and on-demand production parts in as fast as 15 days. We use aluminium moulds that offer cost-efficient tooling, producing parts from a range of thermoplastic and liquid silicone rubber materials.
Overmoulding and insert moulding are frequently used for:
- low-volume production parts
- bridge tooling
- pilot runs
- functional prototyping and testing
Overmoulding Material Bonding
Chemical bonding between overmoulded materials is possible, but material compatibility should be considered in order to achieve desired bond strength. Incorporation of an adequate mechanical bond is strongly recommended if bonding is critical to your application. An undercut is a good example of a mechanical bond.
Substrate Material | ||||||
---|---|---|---|---|---|---|
Overmould Material | ABS POLYLAC PA-717C | ABS/PC BAYBLEND T65 XF | PC MAKROLON 2458 | PBT CELANEX 2002-2 | PP MOPLEN RP348R | NYLON 66 ZYTEL 70G30HSLR |
TPU Pearlthane 11T85 | C | C | C | C | M | M |
TPV Sarlink 3170 | M | M | M | M | C | M |
TPE Thermolast K TC6 MLZ | C | C | C | M | M | M |
LSR Elastosil 3003/30 AB/B | - | - | M | M | - | M |
TPC Hytrel 4068FG | C | C | C | C | M | M |
M = mechanical bond (recommended)
C = chemical bond
Insert Moulding for threading
Instead of a mould that produces a final part using two separate shots like overmoulding, insert moulding generally consists of a preformed part—often metal—that is loaded into a mould, where it is then overmoulded with plastic to create a part with improved functional or mechanical properties.
One way insert moulding is used is with threaded inserts, which reinforce the mechanical properties of plastic parts’ ability to be fastened together, especially over repeated assembly. Bushings and sleeves are another great way to increase part durability for mating components that need more abrasion resistance due to moving parts.
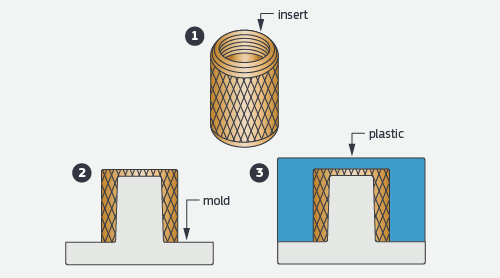
Insert Moulding - Protolabs Stocked Inserts
Managing supply chains can be complex and can easily become expensive in terms of time and money. Using Protolabs-supplied inserts means you can focus on what matters, allowing you to reduce the risks around your project.
At Protolabs, we use Tappex HiMould inserts. If you are already using Tappex HiMould inserts, you won't need to make any changes to your designs to use PLSI, we can quote straight away!
If you are NOT already using Tappex HiMould inserts for a standard threaded brass insert, you can make minor changes and retain the threaded feature without the headache of adapting your supply chain.
Type A
Size | Pitch | Diameter External 'B' | Length 'L' | Bolg Engagement 'E' | No. of Full Threads | Counterbore 'S' | Type | Part Number |
---|---|---|---|---|---|---|---|---|
M3 | 0.50 | 4.15 | 6.40 | 3.70 | 6.80 | X | A | 116M3 |
M3.5 | 0.60 | 5.00 | 7.90 | 4.90 | 7.60 | X | A | 116M3.5 |
M4 | 0.70 | 5.90 | 8.70 | 5.45 | 7.00 | X | A | 116M4 |
M5 | 0.80 | 6.60 | 9.50 | 6.45 | 7.00 | X | A | 116M5 |
M6 | 1.00 | 10.00 | 12.50 | 8.30 | 7.50 | X | A | 116M6 |
Currently we are only providing threaded brass inserts within a defined range as Protolabs supplied inserts. Contact us if you require the CAD model of any of these inserts on +44 (0) 1952 683047 or email [email protected]
Type B
Size | Pitch | Diameter External 'B' | Length 'L' | Bolg Engagement 'E' | No. of Full Threads | Counterbore 'S' | Type | Part Number |
---|---|---|---|---|---|---|---|---|
M2 | 0.40 | 3.40 | 3.925 | X | X | X | B | 017M2 |
M2.5 | 0.45 | 4.15 | 4.725 | X | X | X | B | 017M2.5 |
M3 | 0.50 | 4.15 | 4.725 | X | X | X | B | 117M3 |
M3.5 | 0.60 | 5.00 | 5.875 | X | X | X | B | 117M3.5 |
M4 | 0.70 | 5.90 | 7.125 | X | X | X | B | 117M4 |
M5 | 0.80 | 6.60 | 7.825 | X | X | X | B | 117M5 |
M6 | 1.00 | 9.25 | 9.925 | X | X | X | B | 117M6 |
Currently we are only providing threaded brass inserts within a defined range as Protolabs supplied inserts. Contact us if you require the CAD model of any of these inserts on +44 (0) 1952 683047 or email [email protected]
Type C
Size | Pitch | Diameter External 'B' | Length 'L' | Bolg Engagement 'E' | No. of Full Threads | Counterbore 'S' | Type | Part Number |
---|---|---|---|---|---|---|---|---|
M2 | 0.40 | 3.40 | 5.60 | 3.75 | 6.30 | 0.85 | C | 018M2 |
M2.5 | 0.45 | 4.15 | 6.50 | 4.10 | 6.00 | 0.95 | C | 018M2.5 |
M3 | 0.50 | 4.60 | 7.45 | 4.75 | 6.30 | 1.10 | C | 118M3 |
M3.5 | 0.60 | 5.00 | 9.30 | 6.25 | 7.20 | 1.35 | C | 118M3.5 |
M4 | 0.70 | 5.90 | 10.30 | 7.05 | 6.80 | 1.60 | C | 118M4 |
M5 | 0.80 | 6.60 | 11.30 | 8.35 | 6.70 | 1.75 | C | 118M5 |
M6 | 1.00 | 10.00 | 14.50 | 10.35 | 7.00 | 1.85 | C | 118M6 |
Currently we are only providing threaded brass inserts within a defined range as Protolabs supplied inserts. Contact us if you require the CAD model of any of these inserts on +44 (0) 1952 683047 or email [email protected]
Insert FAQs
What are Protolabs Supplied Inserts (PLSI)?
expand_less expand_morePart inserts are used to provide features and properties unachievable through the moulding process. 50% of the part inserts that our customers request are threaded, and it is this customer requirement we are addressing with PLSI.
Why do Protolabs Provide PLSI?
expand_less expand_moreSometimes if you are supplying your own inserts this can cause delays to design and production. Protolabs Supplied Inserts will be stocked on site and will reduce lead times and make the process a lot easier leading to a better experience and faster process time.
What are the benefits of PLSI?
expand_less expand_moreWhen Protolabs provide the threaded inserts, you don’t need to worry about having to order inserts and the delays it causes. You don’t need to be concerned over scrappage rates or rejected stock. Removing unexpected costs and awkward situations relating to inserts.
How can you request PLSI?
expand_less expand_moreWhen configuring your part please ensure you request an "insert moulding" quote. There will be a section labelled "insert". Here, enter the insert code (eg. PLSI 116M4) into the “insert type“ box, then you can proceed as normal.
About Overmoulding and Insert Moulding
What is overmoulding?
expand_less expand_moreWith overmoulding, the production of the substrate parts is a standard injection moulding process involving an aluminium mould with no heating or cooling lines running through it. Cycle times are a bit longer, which allows our moulders to monitor fill pressure, cosmetic concerns, and the basic quality of the parts. When the total run of substrate parts are moulded, overmould tooling is then assembled to the press. The substrate parts are placed by hand into mould where each part is overmoulded with either a thermoplastic or liquid silicone rubber material.
What is insert moulding?
expand_less expand_moreInsert moulding is a similar process but instead uses a preformed part—often metal—that is loaded into a mould where it is then overmoulded with a thermoplastic resin to create a final component. When the run is complete, parts are boxed and shipped shortly thereafter.
How do overmoulding and insert moulding work?
expand_less expand_moreFrom left to right, the components of an overmoulding press include: ram (1), screw (2), hopper (3), barrel (4), heaters (5), materials (6), nozzle (7), overmould tooling (8), and overmoulded part (9).
With overmoulding, the production of the substrate parts is a standard injection moulding process involving an aluminium mould with no heating or cooling lines running through it. Cycle times are a bit longer, which allows our moulders to monitor fill pressure, cosmetic concerns, and the basic quality of the parts.
When the total run of substrate parts are moulded, overmould tooling is then assembled to the press. The substrate parts are placed by hand into mould where each part is overmoulded with either a thermoplastic or liquid silicone rubber material.
Insert moulding is a similar process but instead uses a preformed part—often metal—that is loaded into a mould where it is then overmoulded with plastic to create a final component. When the run is complete, parts are boxed and shipped shortly thereafter.
Why choose overmoulding or insert moulding?
expand_less expand_moreWhile overmoulding requires more complex design, processing, and materials choice than single-shot injection moulding, it offers significant benefits:
- It allows materials to be combined to provide characteristics that no single resin can deliver.
- It can eliminate assembly steps, saving both time and money.
- It can meld materials in a way that assembly processes cannot match.
- Inserts add strength and durability to parts.
We offer a number of additional secondary services to support your project.
Resources
