
6 modi per ottimizzare la progettazione dei pezzi destinati alla fabbricazione con macchine CNC
Per ridurre i costi e i tempi di produzione, è bene soffermarsi su aspetti quali profondità dei fori, filettature, spessore delle pareti o altri dettagli di lavorazione
La fabbricazione rapida e conveniente di prototipi e pezzi da produzione mediante lavorazione CNC è spesso una questione di equilibri complessi, in cui entrano in gioco sia le capacità del processo di produzione, sia le caratteristiche della parte stessa in quanto componente funzionale ottimizzato. Per tale ragione, se si desidera trarre il massimo dal servizio richiesto in termini di costi e tempistiche di lavorazione, vi sono alcuni fattori che è importante considerare durante la fase di progettazione dei pezzi destinati ai processi di fresatura e tornitura Protolabs.
Per ottimizzare i progetti in funzione del servizio di lavorazione, si raccomanda di considerare con attenzione gli aspetti seguenti:
- Profondità e diametro dei fori
- Dimensione e tipologia di filettatura
- Testo sui pezzi
- Altezza delle pareti e larghezza dei dettagli
- Lavorazione con torni motorizzati
- Fresatura multi-asse
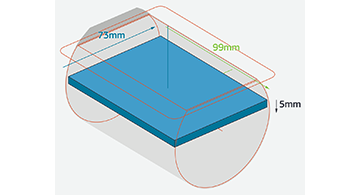
L’immagine illustra le dimensioni massime necessarie per massimizzare lo stock di materiale grezzo nella fabbricazione di un pezzo di 73 mm (larghezza) x 5 mm (altezza).
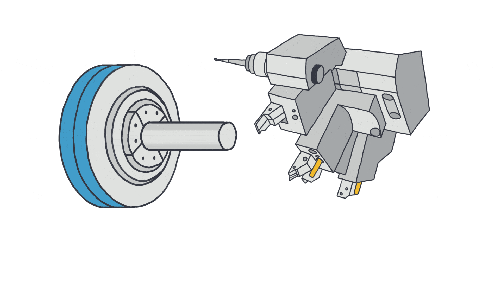
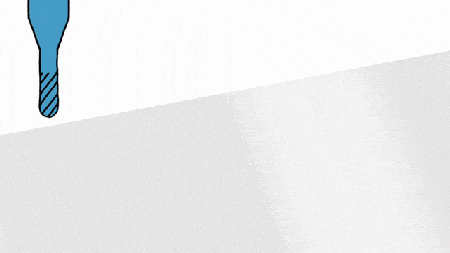
1. La verità sui fori
Chiunque abbia trascorso più di cinque minuti in un’officina sa benissimo com’è fatto un trapano e a cosa serve. Nell’ambito dei servizi di fabbricazione offerti da Protolabs, però, i fori sono praticati con l’ausilio di una fresa piuttosto che perforati con un trapano. Questo metodo di lavorazione offre maggiore flessibilità in termini di dimensioni disponibili, oltre ad assicurare una migliore finitura di superficie rispetto a quella altrimenti ottenuta mediante perforazione. Senza contare che, così facendo, siamo in grado di ricorrere al medesimo utensile per la lavorazione di tasche e scanalature, riducendo i costi e i cicli di lavorazione. L’unico svantaggio di questa tecnica è costituito dalla difficoltà di praticare fori di profondità superiore ai 6 millimetri per via della lunghezza limitata della fresa, rendendo necessario lavorare il pezzo da entrambe le estremità.
2. Un approccio moderno alle filettature
Foratura e filettatura vanno di pari passo. Per modellare le filettature interne, in molti laboratori si ha la tendenza a ricorrere ai “maschi”, ovvero utensili simili a viti “dentate” che vengono inseriti all’interno di fori precedentemente perforati. Noi preferiamo però un approccio più moderno che prevede l’impiego di un’apposita fresa per modellare il profilo della filettatura. Oltre a ottenere un maggiore livello di precisione, tale sistema permette di utilizzare un unico utensile di fresatura per l’applicazione di filettature di qualsiasi dimensione nello stesso passo (ovvero il numero di filettature per pollice), riducendo così i tempi di fabbricazione e configurazione. Il ricorso a questa tecnica ci consente di realizzare filettature UNC e UNF da #2 a 1/2" e filettature metriche da M2 a M12 con la stessa serie di strumenti.
3. Attenzione ai testi
E se occorre aggiungere un numero di componente, una descrizione o un logo ai pezzi lavorati? Gli utensili adoperati da Protolabs sono in grado di inserire praticamente qualsiasi tipologia di testo, a condizione che la spaziatura tra i caratteri e il tratto utilizzato per comporli misurino almeno 0,5 mm. Inoltre, il testo incassato è preferibile rispetto a quello in rilievo e si raccomanda di selezionare caratteri da almeno 20 punti come Arial, Verdana o altri caratteri senza grazie.
4. Pareti e dettagli minuscoli
I nostri set di utensili includono tutti frese al carburo, un materiale dall’elevata rigidità che massimizza la vita utile e la produttività dell’utensile riducendo al tempo stesso la deflessione. La deflessione è però un rischio che interessa non solo gli utensili più resistenti, ma anche i materiali sottoposti a lavorazione (ovvero i metalli ma soprattutto la plastica). L’altezza delle pareti e la dimensione dei dettagli è dunque fortemente legata alla geometria del pezzo e al set di strumenti adoperato. Ad esempio, le dimensioni minime e massime indicate da Protolabs per lo spessore degli elementi di dettaglio sono rispettivamente pari a 0,5 e 51 mm, ma ciò non significa che tale principio sia applicabile a pezzi complessi quali i dissipatori ad alette.
5. Lavorazione con torni motorizzati
Oltre all’ampia gamma di opzioni di fresatura, Protolabs offre anche servizi di lavorazione con utensili motorizzati. Il set di strumenti utilizzato in questo caso è simile a quello impiegato nei nostri centri di lavorazione, anche se non siamo ancora in grado di offrire la tornitura di pezzi in materiali plastici. Questo processo di lavorazione rende possibile l’inserimento di dettagli quali fori decentrati, fori di alloggiamento o scanalature in parallelo o perpendicolari (assiali o radiali) all’asse “lungo” del pezzo tornito (l’asse Z), solitamente seguendo i medesimi principi di progettazione applicati alle parti ortogonali fabbricate nei nostri centri di lavorazione.
La differenza in questo caso è rappresentata dalla forma del materiale grezzo piuttosto che dalla forma dell’utensile. I pezzi torniti, quali pistoni o alberi di trasmissione, sono realizzati a partire da una barra rotonda, mentre quelli fresati (come collettori di scarico, custodie di dispositivi o tappi di valvole) utilizzano di solito blocchi quadrati o rettangolari. Anche in questo caso, però, è possibile superare tali limitazioni. Continua a leggere per scoprire perché...
6. Fresatura a 5 assi
Protolabs mette a disposizione due servizi di fresatura distinti. Nel caso della lavorazione a 3 assi, il bloccaggio del pezzo si realizza dal basso del blocco di materiale, mentre le caratteristiche di dettaglio sono fresate a partire dall’estremità superiore. Si rende pertanto necessaria una diversa configurazione per ciascun lato del pezzo e, nel caso di modelli con dimensioni maggiori di 254 x 178 mm, sarà possibile fresare solo le estremità inferiore e superiore ( non è prevista la lavorazione laterale). La fresatura indicizzata permette però di fresare fino a cinque estremità del pezzo in un’unica configurazione. Questo processo, noto anche come fresatura a 5 assi, prevede l’indicizzazione del pezzo fino a 90 gradi da qualsiasi angolo (nonché da angoli multipli o composti), rendendo possibile un posizionamento complesso e non ortogonale.
I set di utensili utilizzati sono identici in entrambi i casi, l’unica differenza è costituita dal materiale grezzo. In maniera analoga al processo di tornitura, la fresatura indicizzata prevede anch’essa l’impiego di barre di materiale e richiede tutta una serie di interessanti considerazioni matematiche in merito a dimensione, geometria e posizionamento del pezzo all’interno del volume di materiale grezzo (il famoso Teorema di Pitagora studiato alle scuole medie potrebbe tornare utile). Per ottenere esempi più concreti è possibile consultare le figure pubblicate in questo articolo o semplicemente caricare il modello sul sito www.protolabs.com/it-it.
Per ricevere assistenza personalizzata, contatta i nostri tecnici del servizio clienti al numero +39 0321 381211 o all’indirizzo: customerservice@protolabs.it
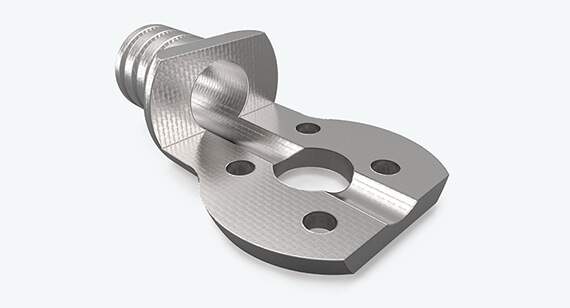
Il pezzo mostrato in figura è stato realizzato con tornio a controllo numerico e utensili motorizzati.
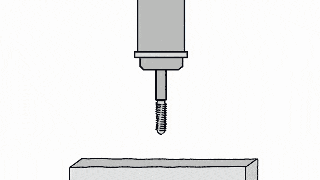
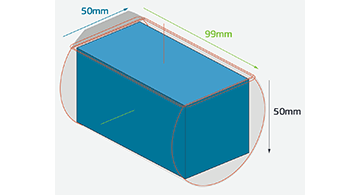
Fresatura a 5 assi: la figura mostra il posizionamento del pezzo all’interno di un blocco di materiale, con dimensioni massimi del pezzo di 50 mm (larghezza) x 50 mm (altezza).