"Lean Manufacturing", qu'est-ce que c'est ?
Quels sont les 5 principes du Lean Manufacturing ?
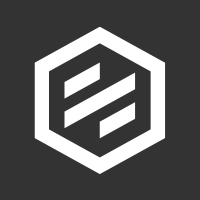
"Lean Manufacturing", également connue sous le nom de "Lean production", est un concept qui existe depuis des années. Mais pourquoi est-il important ? Dans ce blog, nous explorons l'histoire du Lean Manufacturing et détaillons les principes clés qui la sous-tendent.
À quoi pensez-vous lorsque vous entendez le terme "Lean Manufacturing" ? Kaizen ? Amélioration continue ? Réduction des déchets ? Lean Manufacturing est un processus de production qui trouve son origine chez Toyota, au Japon, lorsque le système de production Toyota a été mis au point au milieu du 20e siècle.
L'idéologie du Lean manufacturing s'articule autour des principes de l'amélioration continue, de l'élimination des déchets et d'une approche centrée sur le client - en bref, maximiser la valeur et minimiser les déchets.

Lean manufacturing repose sur cinq principes : la valeur, la cartographie de la valeur, le flux, la traction et la perfection. Examinons chaque principe plus en détail afin de comprendre comment chaque étape contribue à la mise en place d'un système du Lean manufacturing.
Valeur - La première étape consiste à définir la valeur. La valeur est toute action ou tout processus qu'un client est prêt à payer et qu'il juge utile. La "valeur" du client est le point de départ, et vous devez ensuite identifier toutes les activités qui soutiennent ces valeurs. Réfléchissez : quel est le délai de livraison de votre produit/service ? Quel est le prix ? Quelles sont les attentes à satisfaire ?
Cartographie de la valeur - Il s'agit ensuite d'analyser et de cartographier l'ensemble du processus de fourniture de votre produit/service. Depuis le concept initial jusqu'aux mains du client. Si la "valeur" du client est le point de départ, vous devez ensuite identifier toutes les activités qui soutiennent ces valeurs. En établissant la carte de vos valeurs, vous rencontrerez des "déchets" dans votre processus/flux. Ces déchets peuvent être classés en deux catégories : 1) Sans valeur ajoutée mais nécessaire. 2) Non-valeur ajoutée et non nécessaire.
La catégorie 1 doit être éliminée immédiatement de votre processus !
La catégorie 2 doit être réduite au fil du temps.
Flux - Veiller à ce que le flux de travail soit fluide et continu dans l'ensemble de la chaîne de valeur. Une fois les déchets éliminés, l'étape suivante consiste à décomposer les étapes de votre processus. Que peut-on faire pour améliorer ces étapes et veiller à ce qu'elles se déroulent de manière plus fluide ? Il peut s'agir de former les employés, d'adapter le processus de production et les étapes, d'intégrer la robotique et l'IA, etc.
Pull - L'idéal est que les composants soient produits au fur et à mesure de la demande du client. Cette approche juste à temps de la production signifie moins de stocks et d'articles en cours de fabrication tout en garantissant que toutes les matières, tous les processus et toutes les informations nécessaires sont disponibles pour un flux de travail fluide. Cela se traduit par une réduction des déchets et une augmentation de l'efficacité.
Perfection - Le dernier principe du Lean manufacturing. Il s'agit de l'étape où toutes les autres étapes sont achevées, ce qui se traduit par une réduction des déchets et un processus plus fluide et plus efficace.
Une fois ce cycle achevé, la chaîne ne s'arrête pas là. Dans un véritable style d'amélioration continue, nous revenons en arrière et recommençons le processus, ce qui est l'essence même de la production allégée.