Questions de matière : Comment choisir une matière
Ce guide s’adresse aux ingénieurs qui prévoient d’effectuer l’analyse quantitative d’une pièce, de déterminer les charges, les contraintes, les déformations et les environnements, et de choisir la meilleure matière possible sur la base de cette analyse. Lorsque la sécurité des personnes est en jeu ou lorsque la fiabilité ou l’efficacité est absolument nécessaire, chaque pièce doit faire l’objet d’une étude, et les matières seront sélectionnées en conséquence. En parcourant ce document, vous réaliserez combien de facteurs sont à prendre en compte et comment l’environnement et l’application influent sur la sélection de la matière. Vous comprendrez alors, sans doute, la réticence d’un ingénieur à recommander une matière particulère pour la pièce de quelqu’un d’autre.
Toutefois de nombreux clients de Protolabs ne sont pas ingénieurs et de nombreuses applications des pièces produites par Protolabs sont parfaitement inoffensives et peuvent rester dans le cadre d’utilisation des plastiques courants. Si votre application est en permanence à température ambiante, n’implique pas de charges importantes et si vous êtes prêt à produire quelques pièces et à les attaquer à grands coups de marteau afin de voir si elles sont assez solides pour votre utilisation, reportez-vous à la section « Ne m’obligez pas à faire le calcul » à la fin de ce guide. Vous y trouverez des suggestions simplifiées pour la sélection des matières.
- La fiche technique standard d'une matière
- Ce qu'il faut savoir sur la température maximum d'utilisation à court terme
- Résistance à la déformation et à la traction
- Ce qu'il faut savoir sur la relation contraintes-température
- Ce qu'il faut savoir sur la relation température-vieillissement
- Le module
- Fissuration sous contrainte
- Effet de la vitesse de déformation sur le module et la contrainte au seuil d'écoulement
- Variations du module avec la température
- Impact Resistance
- L'indice de fluidité
- Autres propriétés des matériaux
- Ne m'obligez pas à faire le calcul!
Choisir une matière peut être un véritable casse-tête. Tout d’abord, la relation fondamentale entre la structure interne de la matière et ses propriétés est généralement mal comprise. D’autre part, on ne consacre souvent pas assez de temps ni d’attention à la définition précise des exigences d’une application. Enfin, même lorsqu’on arrive à surmonter ces deux premiers obstacles, il est parfois difficile de trouver des informations précises sur les propriétés des matières.
Plus de 85 000 options commerciales de matières plastiques sont répertoriées dans des bases de données sur les matières, et leur nombre réel dépasse probablement 90 000. On peut classer ce vaste ensemble d’options en environ 45 familles de polymères ou de mélanges, et ces 45 familles peuvent elles-mêmes se subdiviser en deux grandes catégories : les thermodurcissables et les thermoplastiques. Bien que les thermodurcissables aient été les premiers polymères à être commercialisés, leur utilisation a diminué au point qu’ils ne représentent plus que 15% environ des matières traitées. C’est pourquoi ce guide traite principalement des thermoplastiques.
La fiche technique standard d’une matière
La fiche technique standard d’une matière contient presque exclusivement des caractéristiques mesurées à température ambiante. En outre, ces caractéristiques sont associées à des contraintes qui ne sont pas considérées comme acceptables pour des pièces mécaniques en plastique. La contrainte en traction au seuil d’écoulement et l’allongement à la rupture sont des mesures standard de caractéristique des matières mais ne représentent pas la résistance réelle des pièces en plastique placées sous charge.
Le choix de la matière qui convient à votre application finale implique que vous fassiez la synthèse d’informations provenant de différentes sources. La principale source d’informations est la fiche technique et vous devez apprendre à en extraire autant d’informations que possible.
On trouve parfois des informations plus détaillées susceptibles de compléter les données des fiches techniques dans les guides de conception et les notes d’application publiés par des fournisseurs de matières. Ces informations supplémentaires sont plus souvent disponibles pour les matières spéciales et les matières plastiques techniques hautes performances que pour les matières de base. Pour vraiment comprendre une matière, il faut être prêt à faire une petite enquête.
Ce qu’il faut savoir sur la température maximum d’utilisation à court terme
La température maximum d’utilisation à court terme est peut-être le plus important paramètre d’une fiche technique. Il s’agit traditionnellement de la température de fléchissement sous charge (DTUL), également appelée température de déformation à la chaleur (HDT). La température de ramollissement Vicat est un autre paramètre associé. Comme la température de fléchissement sous charge mesure la flexion mécanique et que le point Vicat est plus proche du point de fusion ou de ramollissement du polymère, la valeur Vicat est généralement plus élevée. Pour une matière semi-cristalline tel que le PBT renforcé verre présenté dans le Tableau 1, toutes ces valeurs seront très proche du point de fusion à savoir 223°C. Toute application qui implique un dépassement même momentané de cette température éliminera ce polymère de la liste des matières envisageables.
La limite maximum de température des polymères amorphes, renforcés ou non, peut également être obtenue en examinant la température de déformation à la chaleur (HDT) ou température de fléchissement sous charge (DTUL). Ainsi par exemple, pour le polycarbonate non renforcé, les valeurs de température de déformation à la chaleur varient entre 130 et 140°C selon la qualité de la matière. Les points de ramollissement Vicat éventuellement indiqués sont supérieurs de quelques degrés. Les polymères amorphes ne présentent pas de structure cristalline significative en se solidifiant, ils n’ont donc pas de point de fusion. Ils présentent toutefois ce qu’on appelle la « transition vitreuse. Dans la pratique, la température de transition vitreuse est la température à laquelle les polymères amorphes perdent la propriété de supporter les charges.
Pour le polycarbonate cette valeur est d’environ 153°C lorsqu’on la mesure par des méthodes mécaniques dynamiques, soit quelque degrés de plus que le point de ramollissement Vicat et de 10 à 20°C de plus que la température de fléchissement sous charge selon la géométrie de l’éprouvette et la manière dont la température de fléchissement est mesurée. Les valeurs des températures de ramollissement Vicat et de fléchissement sous charge ne doivent jamais être utilisées comme des caractéristiques de performances à long terme. On peut toutefois les utiliser comme mesures de la résistance à la chaleur à court-terme, si l’on définit le court-terme en minutes. Tout environnement d’application qui impliquera des déviations de température au-dessus de ces propriétés éliminera cette matière de la liste des matières envisageables quels que soient ses attributs par ailleurs.
Résistance à la déformation et à la traction
Lorsqu’une matière est soumis à des contraintes permanentes, les performances à long terme font intervenir une propriété appelée « résistance au fluage » ; si la contrainte est périodique, la considération principale sera la résistance à la fatigue. Les relations entre contrainte, temps et température sont compliquées et il est rare que l’on dispose de suffisamment d’informations pour prendre, en connaissance de cause, des décisions concernant le comportement à long terme d’une matière sous charge. Cette fois encore, la fiche technique peut fournir une limite supérieure. Pour les matières ductiles, la limite supérieure est la résistance de la matière au seuil d’écoulement et pour les matières fragiles cette limite est la contrainte de rupture. Ces deux valeurs définissent le point de défaillance catastrophique de la matière. Tout environnement qui implique des contraintes et des déformations supérieures à ces valeurs éliminent la matière de la liste des matières envisageables, même à court terme. Après élimination par ce premier filtre très simple, vous devrez examiner les effets à long terme de la température.
Table: 1 Résistance à la traction et module d'un nylon 6/6 renforcé verre à 43% à plusieurs températures | |
---|---|
Température(°C) | Résistance à la traction (psl) |
-40 | 251,6 |
-5 | 206,8 |
25 | 120,6 |
49.5 | 86,1 |
Ce qu’il faut savoir sur la relation contraintes-température
Les prévisions de performances à long terme à températures élevées nécessitent un accès à plusieurs points de données. À mesure que la température ou la durée de vie souhaitée du produit augmente, les niveaux de contraintes admissibles pour l’utilisation de la matière diminuent selon une fonction qui dépend des propriétés thermiques et mécaniques de la matière concernée. Des corrélations entre performances à court et à long terme ont indiqué que les niveaux de contraintes admissibles à long terme pour un thermoplastique se situent généralement entre 20 et 40% de la résistance au seuil d’écoulement ou de l’élongation à la rupture de la matière. Les matières non renforcées tendent à se situer vers le bas de la fourchette tandis que les matières fortement renforcées tendent à se situer vers le haut. Les coefficients de sécurité applicables à un produit donné réduisent encore ces valeurs et, si la température d’utilisation se rapproche des valeurs de la température de fléchissement sous charge, il est possible que les contraintes admissibles ne représentent que 3 à 5% de la valeur figurant sur la fiche technique. Certaines fiches techniques indiquent les valeurs de résistance à la traction et de module de traction ou de flexion à plusieurs températures. La disponibilité éventuelle de ces données permet d’éliminer beaucoup de test et d’itérations. Le Tableau 1 présente un exemple des valeurs de résistance à la traction d’un nylon 6/6 renforcé de fibre de verre, à plusieurs températures.
Ce qu’il faut savoir sur la relation température-vieillissement
À long terme, tous les polymères présentent une sensibilité à l’oxygène et cette sensibilité augmente à plus haute température. La dégradation associée au vieillissement est quantifiée par une propriété appelée « indice relatif de température » ou IRT. Cette valeur est obtenue par un essai homologué et réalisé par Underwriters Laboratories (UL). Il représente actuellement le meilleur moyen de mesure des effets à long terme du vieillissement sur les propriétés mécaniques et électriques des polymères. Pour cet essai IRT, on commence par mesurer les principales propriétés de base telles que la résistance à la traction, la résistance au choc Izod sur éprouvette entaillée et la résistance à l’arc. Les éprouvettes sont ensuite soumises à un vieillissement à plusieurs températures et la diminution de leurs propriétés de base est surveillée jusqu’à ce qu’elles atteignent 50% des valeurs d’origine. Le temps nécessaire pour atteindre une performance de 50% est appelé « durée de vie avant défaillance ».
Si l’on utilise trois ou quatre températures de vieillissement et on trace un graphe de la durée de vie avant défaillance en fonction de la température réciproque, les points obtenus peuvent être placés sur une droite. Par extrapolation de cette ligne, on obtient la température prévue pour causer une défaillance au temps standard (généralement huit ans) appelé l’indice relatif de température. Pour la plupart des thermoplastiques les valeurs IRT sont inférieures aux valeurs de fléchissement sous charge et de ramollissement Vicat. C’est le cas du PBT renforcé verre dans l’exemple de fiche technique présenté dans le Tableau 1 où les valeurs des températures de fléchissement sous charge et Vicat dépassent toutes 200°C alors que les valeurs IRT sont de 140°C. Il est toutefois possible pour certaines matières tendres et flexibles ayant une bonne stabilité par oxydation (le PTFE par exemple) d’avoir des valeurs IRT supérieures à leurs valeurs de température de fléchissement sous charge.
Les valeurs IRT peuvent être utilisées pour anticiper les performances lorsque le vieillissement est un souci majeur. Le processus de vieillissement suit une règle empirique qui relie la dégradation à la température. Le taux de dégradation double à chaque fois que la température augmente de 10°C. Comme cette relation est exponentielle, un changement de 20°C augmentera la vitesse de dégradation d’un facteur de 22 ou 4 et un changement de 30°C l’augmentera d’un facteur de 23 ou 8. Comme l’IRT est indexé sur une période d’environ huit ans, on peut estimer qu’une matière pourra survivre pendant quatre ans à une température supérieure de 10°C à l’IRT, deux ans à un point dépassant de 20°C l’IRT et un an à un point dépassant de 30°C l’IRT. Des coefficients de sécurité doivent être pris en compte dans ce calcul. Des études ont en effet indiqué que, bien que la valeur nominale du facteur d’accélération soit de 2, elle peut en pratique varier de 1,8 à 2,5.
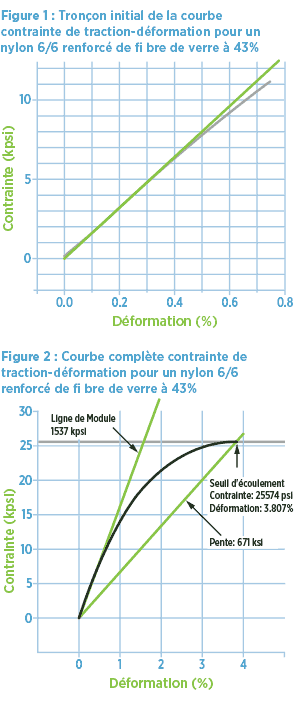
Le module
Le module figure sur pratiquement toutes les fiches techniques. Cette information est généralement indiquée sous forme de module en traction ou de module en flexion. Le module se définit comme le rapport de la contrainte sur la déformation et peut être considéré comme une mesure de la rigidité. Dans la plupart des cas le module est calculé dans la région linéaire de la courbe contrainte-déformation. La linéarité disparait souvent avec de très faibles déformations. La Figure 1 présente une vue agrandie d’un tronçon initial de la courbe contrainte-déformation pour un nylon 6/6 fortement renforcé de fibre de verre. Bien que le module de cette matière, à température ambiante, soit indiqué comme 10600 MPa (1 537 000 psi), le tracé contrainte-déformation s’écarte de la linéarité à environ 0,4%. Au-delà de ce point chaque augmentation incrémentielle des contraintes produit une déformation correspondante progressivement plus importante.
La Figure 2 montre que même si la pente de la ligne de module reflète la valeur indiquée sur la fiche technique, la pente efficace de la ligne qui relie l’origine au seuil d’écoulement ne représente que 40% de cette valeur indiquée. C’est pourquoi, lorsqu’on utilise le module comme propriété de sélection, il est important de bien comprendre la position des contraintes de l’application sur la courbe contrainte-déformation.
Lorsque les contraintes d’une application se rapprochent du seuil d’écoulement, la durée de vie attendue du produit diminue. Le Tableau 2 montre la contrainte maximum admissible pour un polycarbonate en fonction du temps à deux températures différentes. À des temps très brefs (moins d’une heure), la limite de contrainte est pratiquement la même que la contrainte au seuil d’écoulement à la température donnée. Au fur et à mesure que la durée sous charge de l’application augmente, la contrainte maximum admissible diminue.
Fissuration sous contrainte (cause la plus courante de défaillances sur site pour les pièces en plastique)
La présence d’un produit chimique dans l’environnement de la pièce susceptible de provoquer un phénomène appelé « fissuration sous contrainte » réduit la contrainte maximum admissible. Le Tableau 3 présente la contrainte maximum admissible pour le polycarbonate du Tableau 2 lorsque les contraintes permanentes sont associées à la présence d’un fluide agissant comme un agent de fissuration. Il montre que les caractéristiques mécaniques du matériau diminuent lorsque le produit chimique est présent. La défaillance d’un plastique sous l’influence combinée de contraintes et d’un agent chimique s’appelle « fissuration sous contrainte environnementale » et représente la cause la plus fréquente de défaillance sur site pour les pièces en plastique.
Tableau 2 : Contrainte maximum admissible en fonction du temps pour le polycarbonate à deux températures | ||
---|---|---|
Temps (heures) | Contraintes admisible à 23°C (psi) | Contrainte admissible à 60°C (psi) |
0,01 | 63,6 | 49,6 |
0,1 | 61 | 48,2 |
1 | 58,2 | 47,2 |
10 | 55,7 | 44,4 |
100 | 53 | 41,7 |
1.000 | 51,1 | 39,9 |
10.000 | 48,9 | 35,1 |
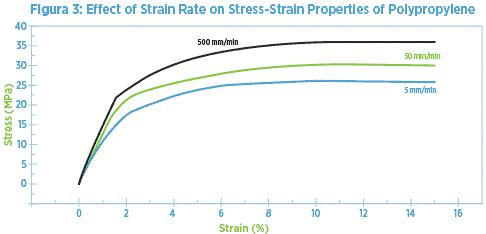
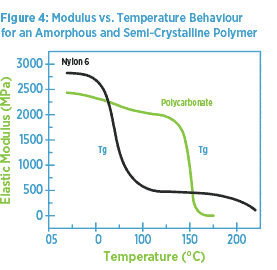
Effet de la vitesse de déformation sur le module et la contrainte au seuil d’écoulement
Certaines propriétés des matières dépendent de la vitesse de déformation. La vitesse à laquelle la matière est contraint aura une influence sur le module ainsi que sur la contrainte au seuil d’écoulement comme l’illustre la Figure 3. Les vitesses de déformation élevées produisent des valeurs supérieures pour le module et la contrainte au seuil d’écoulement. Bien qu’il soit souhaitable que tous les fournisseurs d’un type de matière donnée utilisent les mêmes vitesses de déformation dans les essais, ce n’est pas toujours le cas et il pourra exister des écarts dans les propriétés des fiches techniques en raison de ce défaut d’harmonisation.
Variations du module avec la température
Le module varie avec la température. Une fiche technique qui indique des valeurs de module pour plusieurs températures comme dans le Tableau 1 créera une image plus complète du comportement d’un matériau. Toutefois, il est rare de trouver des données pour plus de quatre températures, et ces données peuvent couvrir une plage de températures de 150 à 200°C. Ceci laisse donc planer beaucoup d’incertitude en ce qui concerne le comportement de la matière entre ces points ou en dehors de la plage définie par ces points. L’analyse mécanique dynamique (DMA) permet de mesurer continuellement le module sur une large plage de températures. La Figure 4 illustre les courbes module vs température pour le polycarbonate, un polymère amorphe et le nylon 6, un polymère semi-cristallin.
Ces deux matières présentent un comportement typique de leur structure respective. Ils possèdent tous les deux une transition vitreuse qui représente le début d’un mouvement moléculaire dans les régions amorphes de la structure. Dans le polycarbonate amorphe, ce phénomène cause la perte complète de toutes les propriétés mécaniques utiles sur une plage de températures relativement étroite. Cependant, dans le nylon, la baisse du module, bien que significative, n’est pas catastrophique et il conserve 20% de ses performances à température ambiante. Ceci met en évidence l’influence de la structure cristalline du polymère. Tous les polymères amorphes présentent un comportement d’interdépendance avec la température similaire à celui du polycarbonate, et toutes les matières semi-cristallines présentent un profil propriétés températures similaire à celui du nylon. Les différences essentielles se situent au niveau des températures de transition exactes pour chaque polymère.
La résistance au choc
L’évaluation de la résistance au choc à partir des valeurs typiques de la fiche technique n’est pas évidente car l’industrie utilise de nombreuses méthodes pour effectuer les essais de résistance au choc et pour indiquer les résultats. La méthode la plus courante pour évaluer la résistance au choc est l’essai Izod sur éprouvette entaillée. Cet essai s’effectue sur une éprouvette comportant une entaille vive usinée et utilise les oscillations d’un mouton pendule afin de transmettre l’énergie nécessaire pour produire la rupture.
Le rayon minimal de l’entaille Izod amplifie souvent les différences de ductilité du fait des différences de sensibilité à l’entaille entre les matières. Le polycarbonate, par exemple, et le polyester amorphe PET possèdent tous les deux une bonne ténacité. Le polyester PET a une plus grande sensibilité à l’entaille que le polycarbonate. Par conséquent les valeurs de choc Izod entaillé pourront être bien plus élevées pour le polycarbonate à température ambiante que pour certaines qualités de polyester PET et pourront donner l’impression que la ténacité du polycarbonate est bien supérieure. L’image de la performance au choc sera plus complète si on peut obtenir les résultats de différents types d’essais de résistance au choc.
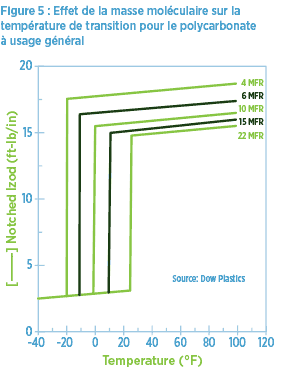
Les essais par chute de masse tels que l’essai Gardner ou l’essai de choc instrumenté peuvent fournir des points de données supplémentaires. Ces essais utilisent des éprouvettes ne comportant aucune concentration des contraintes usinée dans la pièce et donnent un reflet plus précis des performances que l’on peut attendre d’une pièce bien conçue.
Les propriétés de résistance au choc sont également influencées par la température. Les basses températures ont tendance à modifier un comportant ductile en un comportement fragile dans une matière. La transition entre ces deux comportements peut être très soudaine. Il peut être difficile de trouver une image complète de ce type de comportement du fait de la réticence des fournisseurs de matières à signaler des caractéristiques de performances défavorables. Une recherche peut toutefois produire des résultats utiles même s’ils ne sont pas disponibles pour toutes les matières. La Figure 5 présente le comportement au choc Izod entaillé pour différentes qualités de polycarbonate en fonction de la température. Ces résultats illustrent le changement rapide entre comportements ductile et fragile qui se produit généralement en fonction d’une baisse de température. Ce graphique montre également que la transition entre performances ductiles et fragiles est liée à la masse moléculaire du polymère. Les plus basses valeurs d’indice de fluidité sont associées à des qualités de matière ayant une masse moléculaire moyenne plus élevée. Cette propriété a une influence significative sur la température à laquelle les performances de résistance au choc changent.
L’indice de fluidité
L’indice de fluidité est une propriété indiquée sur la plupart des fiches techniques. Il tente de quantifier un aspect important du comportement des matières avec un seul chiffre. L’indice de fluidité est souvent utilisé par les transformateurs pour évaluer la manière dont une matière s’écoulera pendant l’injection. C’est son rapport avec la masse moléculaire moyenne du polymère qui rend la valeur d’indice de fluidité significative. Les plus basses valeurs d’indice de fluidité sont associées à des matières ayant une masse moléculaire moyenne plus élevée. Une masse moléculaire plus élevée fournit des propriétés améliorées, tout particulièrement en ce qui concerne la résistance au choc, les performances en matière de fluage et de fatigue et les propriétés de barrière.
Les comparaisons entre matières basées sur l’indice de fluidité ne sont valables que si on les effectue au sein d’une même famille de polymères. En outre, les conditions d’essai de certaines matières sont multiples. L’ABS, par exemple, peut être testé dans différentes conditions définies par la température et la charge appliquée à la matière. Ces conditions d’essai sont présentées dans le Tableau 4 ainsi que les différences de résultats généralement associées à chaque condition. Lorsqu’on compare deux qualités de matière, il est important de noter les paramètres de test et de procéder aux ajustements correspondants.
Tableau 4 : Effet des conditions d'essai sur l'Indice de fluidité de l'ABS | |
---|---|
Conditions d'essai | Indice de fluidité nominal (grammes / 10 minutes) |
200°C / 5.0 kg |
1,5 |
230°C / 3.8 kg | 4.5 |
220°C / 10.0 kg | 18,0 |
Tableau 5 : Valeurs du coefficient de dilatation pour un nylon 6/6 renforcé verre à 43% sur plusieurs plages de températures | ||
---|---|---|
Plage de Températures (°C) | CLTE* (In / In / °F) | |
-40 à 23 | 0,0000612 | |
23 à 55 | 0,0000792 | |
55 à 160 | 0,0001278 |
Autres propriétés des matières
En dehors des propriétés thermiques et mécaniques, d’autres propriétés peuvent être importantes dans certaines applications. Ce sont en particulier les propriétés électriques telles que la constante et la résistance diélectriques, la résistivité superficielle et la résistivité volumique, et le coefficient de dilatation thermique. Les mesures standard du coefficient de dilatation thermique sont effectuées entre - 30°C et +30°C. Certains fournisseurs, toutefois, indiquent des valeurs sur plusieurs plages de températures telles que celles que présente le Tableau 5. Lorsque cette image plus complète est disponible, elle montre que ce type de propriétés dépend aussi de la température et que les valeurs tendent à augmenter avec la température.
On considère généralement que les plastiques sont d’excellents isolants électriques excepté lorsqu’un compound est spécialement produit pour dissiper l’électricité statique ou pour être quelque peu conducteur en y ajoutant du carbone ou de l’acier inoxydable par exemple. Par conséquent, les valeurs de résistivité sont très élevées pour la plupart des matériaux et sont comprises entre 1010 et 1016 ohms ou ohm-cm respectivement pour la résistivité superficielle et volumique.
Des contraintes électriques prolongées peuvent entraîner la rupture diélectrique d’une matière après un certain temps. Ce comportement dépendra de l’amplitude de la tension appliquée. Il est caractérisé très efficacement par des propriétés qui figurent parfois sur la fiche technique standard mais seront souvent plus facilement obtenues dans la base de données d’Underwriters Laboratories dans le cadre du système Yellow Card. Cette méthode applique des valeurs numériques à des propriétés telles que l’ignition à haute intensité, la résistance à l’arc et le cheminement du courant de fuite. Les valeurs les plus basses obtenues par chaque type de mesure indiquent les meilleures performances et les valeurs les plus élevées sont associées aux plus bas niveaux de performances.
Ne m’obligez pas à faire le calcul !
En général, un ingénieur ne recommandera pas une matière sans avoir connaissance de l’intégralité des exigences de l’application d’une pièce et sans effectuer une analyse de conception du modèle 3D de la pièce.
Il n’est pas toujours économique de faire une étude complète de la pièce uniquement pour sélectionner une matière. Si vous souhaitez éviter l’ingénierie des matières et acceptez de prendre un risque bien informé dans le choix d’une matière, voici quelques règles générales qui pourront vous être utiles:
1 Essayez l’ABS. L’ABS est adapté à de très nombreuses applications. Son prix est raisonnable, il est résistant, d’apparence agréable, relativement résilient et tolérant même lorsqu’on ne respecte pas toutes les règles standard de conception des pièces plastiques. Son point de fusion est relativement bas. Toutes les pièces du moule démo Protolabs sont en ABS.
2 Si vous recherchez l’économie et la rigidité, et si l’apparence n’est pas très importante, essayez le polypropylène (PP). Le cube démo Protolabs est en PP.
3 Si vous avez besoin de quelque chose d’un peu plus résilient que l’ABS ou qui puisse supporter une température un peu plus haute, essayez le polycarbonate (PC). Le PC est moins tolérant que l’ABS si vous ne suivez pas les règles standard de conception des pièces en plastique.
4 Si votre pièce doit être belle et transparente, essayez l’acrylique (PMMA). Le PMMA peut être un peu fragile. Un PC transparent sera plus résilient que le PMMA mais d’apparence un peu moins bonne.
5 Si les règles 1 à 4 ne vous orientent pas vers un choix, vous devrez faire le calcul.
Si vos pièces doivent être moulées par injection, pourquoi ne pas essayer de produire quelques pièces d’essai dans la matière cible en utilisant le service d’usinage CNC de Protolabs avant de vous engager sur un moule. Les moules sont conçus pour correspondre au taux de retrait d’une matière particulière. C’est pourquoi il n’est pas toujours possible d’utiliser plusieurs matières dans un même moule sans risquer des problèmes de taille, de tolérance et/ou de dimensions.