
Frittage laser direct de métal (DMLS)
Obtenez des prototypes et des pièces de production de qualité en métal imprimés en 3D. Demandez un devis en ligne dès à présent.
shield_locked Tous les téléchargements sont sécurisés et confidentiels
Certifications ISO 9001:2015 | ISO 14001:2015 | ISO 13485 (Protolabs Network) | Qualification de fabrication DNV pour l'Inconel 718 | JOSCAR
Jump to Section
→ Conseils de conception
→ Matières
→ Post-production
→ Certifications
→A propos de la DMLS
Le frittage laser direct de métal (DMLS) est un processus d'impression 3D industriel permettant de produire des prototypes et des pièces de production en métal entièrement fonctionnelles dans un délai de 7 jours ou moins. Des métaux divers produisent des pièces finales pouvant être utilisées pour des applications finales.
L'impression 3D de métal est principalement utilisée pour :
- le prototypage des matières adaptées à la production
- les pièces aux géométries complexes
- les pièces fonctionnelles destinées à une utilisation finale
- réduire le nombre de composants d'un ensemble
CONSEILS DE CONCEPTION : FRITTAGE LASER DIRECT DU MÉTAL

Finitions de surfaces pour pièces imprimées en 3D
Vous souhaitez améliorer la résistance, la transparence ou l’aspect de vos pièces imprimées en 3D ? Choisissez des matières spéciales microfluidique/microrésolution, un réusinage ou bien une finition sur mesure (peinture).
Options de matières pour impression 3D métal
Acier Maraging
expand_less expand_moreL'acier Maraging 1.2709 est un acier pré-allié à très haute résistance sous forme de poudre fine. Sa composition correspond à la classification américaine 18% Ni Maraging 300, européenne 1.2709 et allemande X3NiCoMoTi 18-9-5. Ce type d'acier a la particularité d'avoir de très bonnes propriétés mécaniques et d'être facilement traitable thermiquement à l'aide d'un simple procédé thermique de durcissement par vieillissement pour l'obtenir.
Principaux avantages
- Haute résistance
- Dureté élevée
- Bonne résistance aux hautes températures
Acier inoxydable (316 L)
expand_less expand_moreL'acier inoxydable 316L est une matière performante utilisée pour la fabrication de pièces résistantes à l'acide et à la corrosion. Choisissez le 316L lorsque vous avez besoin d'un acier inoxydable flexible ; le 316L est plus malléable que le 17-4 PH. Les pièces de production finales en 316L reçoivent un traitement de relaxation des contraintes.
Principaux avantages
- Résistance à l'acide et à la corrosion
- Forte ductibilité
Aluminium (AlSi10Mg)
expand_less expand_moreL'aluminium (AlSi10Mg) est comparable à un alliage de la série 3000 utilisé dans les processus de moulage et de coulée sous pression. L'Al présente un bon rapport résistance/poids, une haute résistance à la température et à la corrosion, ainsi qu'à la fatigue, au fluage et à la rupture. Le AlSi10Mg offre également des propriétés de conductivité thermique et électrique. Les pièces de production finales en AlSi10Mg reçoivent un traitement de relaxation des contraintes.
Principaux avantages
- Fortes rigidité et résistance comparé au poids
- Conductivité thermique et électrique
Inconel 718
expand_less expand_moreL'Inconel est un superalliage de nickel-chrome solide et résistant à la corrosion, idéal pour les pièces qui seront soumises à des températures extrêmes et à des charges mécaniques. Les pièces de production finales en Inconel 718 reçoivent un traitement de relaxation des contraintes. Un traitement et un vieillissement par AMS 5663 sont également possibles pour accroître sa résistance à la traction et sa dureté.
Principaux avantages
- Résistance à l'oxydation et à la corrosion
- Hautes performances en matière de résistance à la traction, à la fatigue, au fluage et à la rupture
Titane (Ti6Al4V)
expand_less expand_moreLe titane (Ti6Al4V) est un alliage robuste. Comparé au Ti grade 23 recuit, les propriétés mécaniques du Ti6Al4V sont similaires à celles du titane forgé quant à la résistance à la traction, l'allongement et la dureté. Les pièces de production finales en Ti6Al4V reçoivent un traitement de relaxation des contraintes sous vide.
Principaux avantages
- Fortes rigidité et résistance comparé au poids
- Forte résistance à la température et à la corrosion
Comparer les propriétés des matières
Matériaux | Résolution | Condition | Résistance à la Traction (MPa) |
Contrainte de Rendement (MPa) |
Allongement (%) |
Dureté |
---|---|---|---|---|---|---|
Acier Inoxydable |
20/50 μm | Tel Quel | 570 MPa +/- 30 MPa | 470 MPa +/- 30 MPa | 40 +/- 5% | 85m+/- 5 HRB |
20/50 μm | Traitement Thermique | 570 MPa +/- 30 MPa | 33 +/- 5 MPa | 35 +/- 5% | 85 +/- 5 HRB | |
Aluminium (AlSi10Mg) | 30/60 μm | Tel Quel | 360 MPa +/- 30 MPa | 240 MPa +/- 30 MPa | 6 +/- 5% | 120 +/- 5 HBW |
30/60 μm | Traitement Thermique | >267 MPa | >200 MPa | 10 +/- 2% | - | |
Inconel 718 | 50/60 μm | Tel Quel | 960 MPa +/- 50 MPa | 600 MPa +/- 50 MPa | 30 +/- 5% | Ca. 30 HRC |
50/60 μm | Recuit | 980 MPa +/- 50 MPa | 630 MPa +/- 50 MPa | 30 +/- 5% | Ca. 30 HRC | |
50/60 μm | Recuit & Vieilli | >1240 MPa | > 940 MPa | 12% | Ca. 47 HRC | |
Titanium (Ti6Al4V) |
20/30/60 μm | Tel Quel | 1200 MPa +/- 50 MPa | 1050 MPa +/- 50 MPa | 8 +/- 2% | 33 +/2 HBW |
20/30/60 μm | Traitement Thermique | > 930 MPa | > 860 Mpa | >10% | 33 +/-2 HBW |
Ces chiffres sont approximatifs et dépendent d'un certain nombre de facteurs, y compris, mais sans s'y limiter, les paramètres de la machine et du processus. Les informations fournies ne sont donc pas contraignantes et ne sont pas considérées comme certifiées. Lorsque les performances sont essentielles, il convient également d'envisager des essais en laboratoire indépendants sur les matériaux additifs ou les pièces finales.
Capacités de production pour l'impression 3D métal
Vous recherchez une solution de fabrication additive pour vos projets ? Grâce à notre technologie d'impression 3D métal, vous pouvez choisir parmi plusieurs processus secondaires tels que l'usinage post-processus, le taraudage, l'alésage et les traitements thermiques qui produisent des pièces de production à usage final. Pour garantir la qualité des pièces, nous proposons également l'analyse des poudres, la traçabilité des matériaux, la validation des processus et les rapports d'inspection.
Notre processus d'impression 3D par frittage laser direct de métaux (DMLS) est certifié ISO 9001 et ISO 13485 (Protolabs Network). Il s'agit d'une impression 3D industrielle conçue pour répondre à vos besoins, qu'il s'agisse de prototypage ou de production.
1. Expertise
Devis et retour d'information sur la conception de votre pièce de la part de notre équipe d'ingénieurs. Fiabilité d'un fabricant qui a imprimé en 3D des millions de pièces aux géométries uniques au cours des deux dernières décennies.
2. Gestion de projet
Une assistance dédiée à la gestion de votre projet pour tous vos besoins de production, de la conception des pièces aux processus de finition.
3. Echelle
Plus de 100 imprimantes 3D de qualité industrielle, en métal et en plastique, utilisant cinq technologies de fabrication additive et prenant en charge des projets de production dans diverses matières.
4. Qualité
Les contrôles rigoureux des processus et le personnel d'ingénierie sont concentrés sur la réalisation de pièces présentant des tolérances faibles, une précision dimensionnelle et des propriétés mécaniques robustes.
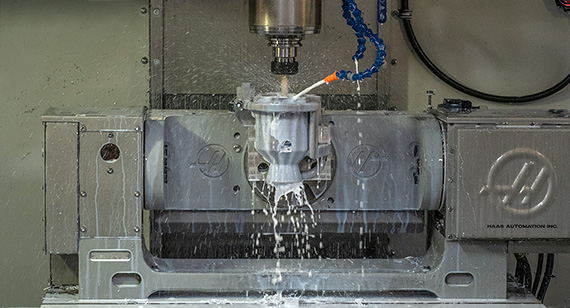
Obtenez des tolérances serrées tout en bénéficiant de la liberté de conception de la fabrication additive.
- Fraisage 3 - 5 axes
- Tournage
- Electroérosion
- Taraudage
Analyse des poudres et traçabilité matériaux
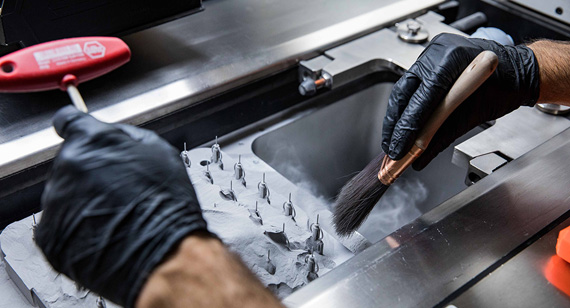
Analyse de la poudre et traçabilité fournisseur pour répondre aux exigences de production.
- Traçabilité
- Chimie
- Analyse de la taille et de la distribution des particules
Essais mécaniques

Essais certifiés pour confirmer les exigences mécaniques des pièces de production.
- Essai de traction
- Essais de dureté
- Fatigue
- Vibration
Traitement thermiques
Les procédés de traitement thermique améliorent les propriétés mécaniques des pièces en éliminant les contraintes internes qui se développent pendant le processus de frittage.
- Soulagement des contraintes
- Pressage isostatique à chaud (HIP)
- Recuit de mise en solution
- Vieillissement
Inspections et rapports de qualité
Validation de la géométrie des pièces et évaluation de la structure des matériaux pour établir des rapports de qualité.
- Inspections dimensionnelles avec rapport
- Inspection du premier article (FAI)
- CMM, balayage optique et CT scan
- Rayons X
- Analyse de la rugosité de surface et de la porosité
- Certificat de conformité avec suivi des pièces
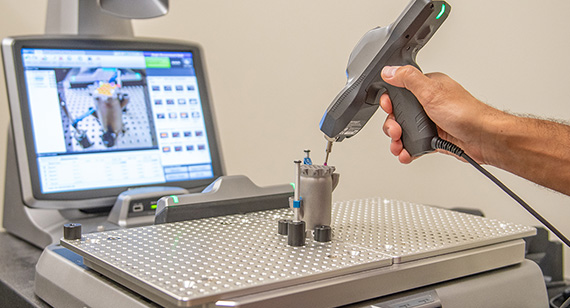
Pourquoi utiliser le frittage laser direct de métal (DMLS) ?
Les matières utilisées en DMLS sont bien souvent égales ou supérieurs à celles des matières forgées. La technologie DMLS est également idéale lorsque la géométrie ou la structure de la pièce n'est pas possible avec un autre procédé (pour les conceptions permettant de réduire le poids en utilisant des structures en nid d'abeille ou en latice, par exemple).
Protolabs peut aussi produire des pièces pour des applications médicales d'implants. Nous proposons par ailleurs un certain nombre de services secondaires tels que la peinture, le post-usinage et la mesure et l'inspection, afin d'améliorer la finition de la conception de votre pièce imprimé en 3D.
OBTENIR UN DEVISRessources
