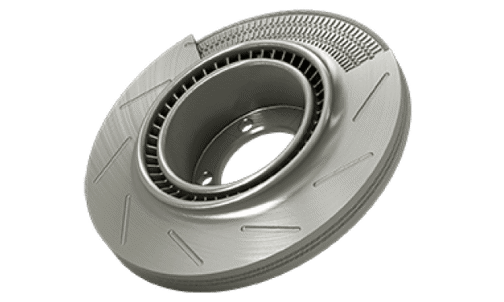
Metal 3D Printing Service
Get quality metal 3D-printed prototypes and production parts. Request an online quote today.
Certifications
ISO 9001:2015 | AS9100D | ITAR Registered
Jump to Section
→ Capabilities
→ Available Alloys
→ Compare Material Properties
→ Surface Finishes
→ Post-Processing
→ Why Metal 3D Printing?
Direct metal laser sintering (DMLS) is an industrial metal 3D printing process that builds fully functional metal prototypes and production parts in 7 days or less. A range of metals produce final parts that can be used for end-use applications.
Metal 3D printing technology is commonly used for:
- Prototyping in production-grade materials
- Complex geometries
- Functional, end-use parts
- Reducing metal components in an assembly

Metal 3D Printing Capabilities
Our basic guidelines for metal 3D printing include important design considerations to help improve part manufacturability, enhance cosmetic appearance, and reduce overall production time.
*At this time, Inconel 718 and Aluminum are the only materials available on our large format, X Line machine
Metal 3D Printing Material Options
Below is our available metal alloys for 3D printing. Various heat treatments are available depending on material.
Stainless Steel (17-4 PH)
expand_less expand_moreStainless Steel 17-4 PH is a precipitation hardened stainless steel that is known for its hardness and corrosion resistance. If needing a stainless steel option, select 17-4 PH for its significantly higher tensile strength and yield strength, but recognize that it has far less elongation at break than 316L. Final parts built 17-4 PH receive vacuum solution heat treatment as well as H900 aging.
Primary Benefits
- Heat treated for full hardness and strength
- Corrosion resistance
Stainless Steel (316L)
expand_less expand_moreStainless steel 316L is a workhorse material used for manufacturing acid and corrosion resistant parts. Select 316L when stainless steel flexibility is needed; 316L is a more malleable material compared to 17-4 PH. Final parts built in 316L receive stress relief application.
Primary Benefits
- Acid and corrosion resistance
- High ductility
Aluminum (AlSi10Mg)
expand_less expand_moreAluminum (AlSi10Mg) is comparable to a 3000 series alloy that is used in casting and die casting processes. It has good strength -to-weight ratio, high temperature and corrosion resistance, and good fatigue, creep and rupture strength. AlSi10Mg also exhibits thermal and electrical conductivity properties. Final parts built in AlSi10Mg receive stress relief application.
Primary Benefits
- High stiffness and strength relative to weight
- Thermal and electrical conductivity
Inconel 718
expand_less expand_moreInconel is a high strength, corrosion resistant nickel chromium superalloy ideal for parts that will experience extreme temperatures and mechanical loading. Final parts built in Inconel 718 receive stress relief application. Solution and aging per AMS 5663 is also available to increase tensile strength and hardness.
Primary Benefits
- Oxidation and corrosion resistance
- High performance tensile, fatigue, creep, and rupture strength
Cobalt Chrome (Co28Cr6Mo)
expand_less expand_moreCobalt Chrome (Co28Cr6Mo) is a superalloy is known for its high strength-to-weight ratio.
Primary Benefits
- High performance tensile and creep
- Corrosion resistance
Titanium (Ti6Al4V)
expand_less expand_moreTitanium (Ti6Al4V) is a workhorse alloy. Versus Ti grade 23 annealed, the mechanical properties of Ti6Al4V are comparable to wrought titanium for tensile strength, elongation, and hardness. Final parts built in Ti6Al4V receive vacuum stress relief application.
Primary Benefits
- High stiffness and strength relative to weight
- High temperature and corrosion resistance

Metal 3D Printing Materials Guide
Learn more about the direct metal laser sinter process and the available materials for DMLS 3D printing.
Compare Material Properties
Materials | Resolution | Condition | Ultimate Tensile Strength (ksi) |
Yield Stress (ksi) |
Elongation (%) |
Hardness |
---|---|---|---|---|---|---|
Stainless Steel (17-4 PH) |
20 μm | Solution & Aged (H900) | 199 | 178 | 10 | 42 HRC |
30 μm | Solution & Aged (H900) | 198 | 179 | 13 | 42 HRC | |
Stainless Steel (316L) |
20 μm | Stress Relieved | 82 | 56 | 78 | 90 HRB |
30 μm | Stress Relieved | 85 | 55 | 75 | 88 HRB | |
Aluminum (AlSi10Mg) |
20 μm | Stress Relieved | 39 | 26 | 15 | 42 HRB |
30 μm | Stress Relieved | 50 | 33 | 8 | 59 HRB | |
40 μm | Stress Relieved | 43 | 27 | 10 | 50 HRB | |
Cobalt Chrome (Co28Cr6Mo) |
20 μm | As Built | 182 | 112 | 17 | 39 HRC |
30 μm | As Built | 176 | 119 | 14 | 38 HRC | |
Inconel 718 | 20 μm | Stress Relieved | 143 | 98 | 36 | 33 HRC |
30 μm | Stress Relieved | 144 | 91 | 39 | 30 HRC | |
30 μm | Solution & Aged per AMS 5663 | 208 | 175 | 18 | 46 HRC | |
60 μm | Stress Relieved | 139 | 83 | 40 | 27 HRC | |
60 μm | Solution & Aged per AMS 5663 | 201 | 174 | 19 | 45 HRC | |
Titanium (Ti6Al4V) |
20 μm | Stress Relieved | 153 | 138 | 15 | 35 HRC |
30 μm | Stress Relieved | 144 | 124 | 18 | 33 HRC |
20 μm = high resolution (HR)
30, 40, and 60 μm = normal resolution (NR)
Materials | Resolution | Condition | Ultimate Tensile Strength (MPa) |
Yield Stress (MPa) |
Elongation (%) |
Hardness |
---|---|---|---|---|---|---|
Stainless Steel (17-4 PH) |
20 μm | Solution & Aged (H900) | 1,372 | 1,227 | 10 | 42 HRC |
30 μm | Solution & Aged (H900) | 1,365 | 1,234 | 13 | 42 HRC | |
Stainless Steel (316L) |
20 μm | Stress Relieved | 565 | 386 | 78 | 90 HRB |
30 μm | Stress Relieved | 586 | 379 | 75 | 88 HRB | |
Aluminum (AlSi10Mg) |
20 μm | Stress Relieved | 268 | 180 | 15 | 46 HRB |
30 μm | Stress Relieved | 345 | 228 | 8 | 59 HRB | |
40 μm | Stress Relieved | 296 | 186 | 10 | 50 HRB | |
Cobalt Chrome (Co28Cr6Mo) |
20 μm | As Built | 1255 | 772 | 17 | 39 HRC |
30 μm | As Built | 1213 | 820 | 14 | 38 HRC | |
Copper (CuNi2SiCr) |
20 μm | Precipitation Hardened | 496 | 434 | 23 | 87 HRB |
Inconel 718 | 20 μm | Stress Relieved | 986 | 676 | 36 | 33 HRC |
30 μm | Stress Relieved | 993 | 627 | 39 | 30 HRC | |
30 μm | Solution & Aged per AMS 5663 | 1434 | 1207 | 18 | 46 HRC | |
60 μm | Stress Relieved | 958 | 572 | 40 | 27 HRC | |
60 μm | Solution & Aged per AMS 5663 | 1386 | 1200 | 19 | 45 HRC | |
Titanium (Ti6Al4V) |
20 μm | Stress Relieved | 1055 | 951 | 15 | 35 HRC |
30 μm | Stress Relieved | 993 | 855 | 18 | 33 HRC |
20 μm = high resolution (HR)
30, 40, and 60 μm = normal resolution (NR)
These figures are approximate and dependent on a number of factors, including but not limited to, machine and process parameters. The information provided is therefore not binding and not deemed to be certified. When performance is critical, also consider independent lab testing of additive materials or final parts.
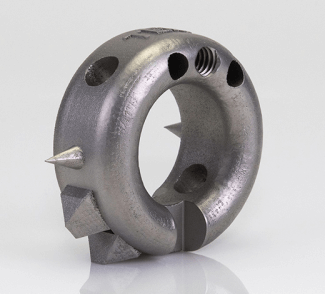
Standard Finish
Expect roughness values of 200 to 400 µin Ra (0.005 to 0.010mm Ra), depending on material and resolution. Support structures are removed and layer lines are visible.
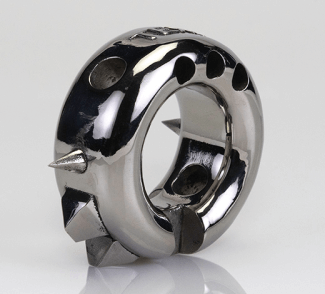
Custom Finish
We offer brushed surfaces in a range of grits and polished mirror finishes. Be sure to indicate if the custom surface finish is for functional or aesthetic purposes so we can best consult you on our custom options.
Post-Processing Capabilities for Metal 3D-Printed Parts
Improve strength, dimensional accuracy, and cosmetic appearance of final metal components with DMLS for production.
Surface Finishing
- 3- and 5-axis milling
- Turning
- Polish (Mirror or Brushed)
- Passivation
- Wire EDM
- Tapping and reaming
- Stress relief
- NADCAP heat treatment
- Hot isostatic pressing (HIP)
- Solution annealing
- Aging
Mechanical Testing
- Tensile
- Rockwell Hardness
Powder Analysis & Material
- Traceability
- Chemistry
- Particle size and distribution analysis
How Does Metal 3D Printing Work?
The DMLS machine begins sintering each layer—first the support structures to the base plate, then the part itself—with a laser aimed onto a bed of metallic powder. After a cross-section layer of powder is micro-welded, the build platform shifts down and a recoater blade moves across the platform to deposit the next layer of powder into an inert build chamber. The process is repeated layer by layer until the build is complete.
When the build finishes, an initial brushing is manually administered to parts to remove a majority of loose powder, followed by the appropriate heat-treat cycle while still fixtured in the support systems to relieve any stresses. Parts are removed from the platform and support structures are removed from the parts, then finished with any needed bead blasting and deburring. Final DMLS parts are near 100 percent dense.
Large Format Metal 3D Printing
We recently added the GE Additive X Line to our fleet of metal 3D printers to build large Inconel 718 and Aluminum (AlSi10Mg) parts. Have a project that might be a good fit? Contact us and we can discuss your requirements.