
Injection Molding Services for Custom Parts
Custom injection molding for plastic prototypes and on-demand production parts in as fast as 1 day. Request an injection molding quote today.
ISO 13485 certification available through Protolabs Network
Injection Molding Processes
Make the move from prototyping to on-demand manufacturing for affordable, high-quality molded parts within days. Better yet, your prototyping tool is free once you shift to an on-demand manufacturing tool. Working with a single supplier that provides free design consultation services also massively speeds up the manufacturing process, allowing for greater supply chain flexibility, more consistent parts, and making qualification a breeze.
Additional Capabilities for Injection Molding Orders
Injection Mold Tooling Options and Quality Reporting
We have two unique offers to meet your needs wherever you are in the product lifecycle. Our prototype injection molding process helps you cut product development cycles by weeks—sometimes months—and bridge to production with injection-molded parts within days. Our On-demand Manufacturing process is designed to meet your production needs, and helps you qualify parts quickly to seamlessly transition into production with scientific molding, in-process CMM inspections with GD&T, and a full suite of secondary operations to make sure that your parts show up and perform as expected.
Prototyping | On-Demand Manufacturing | |
---|---|---|
Objective |
I need to validate my design at Protolabs speeds. I need the flexibility to economically iterate before production. |
I have on-demand production needs at Protolabs speeds. |
Best When |
|
|
Mold Cavities | Single | Single and multi-cavity |
Mold Life | Limited (guaranteed for at least 2,000 shots) | Unlimited |
Mold Storage | Stored for 18 months of inactivity | Stored for 3 years of inactivity |
Mold Ownership | Upon request | Yes |
Quality Documentation | Quality Inspection Report (QIR) verifies Protolabs' manufacturing process controls |
|
Shared Features |
Aluminum molds |
Injection Molding Materials
We have wide selection of more than 100 thermoplastic and thermoset materials. And if you're looking for alternative material options, check out our guide to resin substitutes for ABS, PC, PP, and other commonly molded plastics.
Thermoplastics
- ABS
- Acetal
- Acetal Copolymer
- Acetal Homopolymer/Delrin
- ETPU
- HDPE
- LCP
- LDPE
- PET
- PETG
- PMMA (Acrylic, Plexiglas)
- Polycarbonate
- Polypropylene
- PPA
- PPE/PS
- PS
- PSU
- TPU
Thermosets
- Standard silicone (30, 40, 50, 60, and 70 durometers)
- Medical-grade silicone
- Optical-grade silicone
- Fluorosilicone (fuel and oil resistant)

Why Choose Us for Custom Injection Molding?
Unmatched Lead Times
Reduce your product development cycle by weeks—sometimes months—and bridge to production with injection-molded parts within days. Some injection molding orders can ship in as fast as 1 day.
Design for Manufacturing Feedback
Every quote includes real-time pricing and design analysis. We evaluate your 3D CAD and help identify any features that may pose challenges during the molding process such as difficult to machine undercuts and insufficient draft.
No Minimum Order Quantities (MOQs)
Procuring parts on demand, without MOQs, helps you manage market or demand volatility and provides a cost-effective source for bridge production, line-down emergencies, end-of-life production, or product customization.
Injection Molding Expertise
We'll work with you throughout the course of your project to help you quickly move from prototyping to production, including finishing options and inspection reporting.
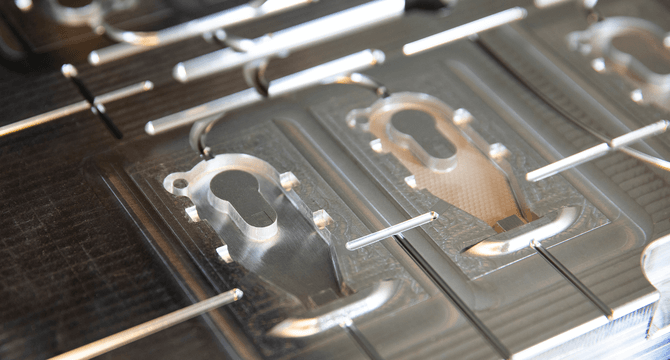

Advantages of Injection Molding
Injection molding is plastic manufacturing process that can produce high quality parts at scale. It's typically used for low- to high-volume production but our aluminum tooling can also make prototyping runs economical.
- Low cost at higher volumes
- Exceptional part cosmetics and surface finish
- Repeatable
- Complex parts
- Low scrap rate
- Large selection of thermoplastic and thermoset materials
Injection Molding Applications
Injection molding is widely used for plastic part production in medical, consumer, and automotive industries. Typical parts include:
- Housings
- Brackets
- Gears
- Single-use medical parts
- Electrical connectors
- Syringes
- Containers

Injection Molding FAQs
How much does injection molding cost?
expand_less expand_moreBecause of the initial capital investment in tooling, injection molding makes sense for higher volumes of parts. Our mold cost starts at $1,495 and will vary depending on part geometry and complexity. Other factors that will impact injection molding cost are lead times and material.
Do you do production molding?
expand_less expand_moreYes, we offer a production tooling option called on-demand manufacturing. This tooling option provides several benefits: lower piece part price, multi-cavity capabilities, guaranteed tooling for the life of the project (we will cut a new tool if it wears out), and first article inspections.
What are your tolerances for molded parts?
expand_less expand_moreIn most cases, we can maintain a machining tolerance of +/- 0.003 in. (0.08mm) with an included resin tolerance that can be greater than but no less than +/- 0.002 in./in. (0.002mm/mm).
What is the maximum part size for injection molding?
expand_less expand_moreThe largest size we can support with plastic injection molding is 18.9 in. x 29.6 in. x 8 in. (480mm x 751mm x 203mm).