
Sheet Metal Finishes and Post-Processing
Our sheet metal fabrication service offers a broad range of surface finish treatments and post-processing options to customize your projects.
Certifications ISO 9001:2015 | ITAR
Get the Look You Want with One or More Production Quality Finishes
We offer over 100 finishing options to customize your sheet metal component or assembly. Designed to enhance the functional or aesthetics elements of your design, these finishes are available with short lead times, applied by experts who deliver high quality results.

Free Finishing Consultation for Fabricated Projects
Take advantage of a free 30-minute virtual finishing consultation with one of our sheet metal applications engineers. it's a perfect opportunity to review your finishing requirements to ensure your project arrives to your specifications.
Schedule NowOrbital Sander
This is the most common surface finish for sheet metal parts and involves using a random orbital sanding device to remove dross and other surface debris and build-up from the last cutting process. Orbital sanding is not recommended for cosmetic applications and is best used for internal components or situations where form, fit, and function is the priority.
Straight Grain/Brushed
This surface finish involves applying a sanding belt in a uniform direction/pattern to the surface of the sheet metal. Designs with a grain direction are usually for cosmetic or end-user facing purposes. Straight grain can be applied to your part in three ways:
- Perpendicular to the longest bend (when formed) or edge (when flat)
- Parallel to the longest bend or edge
- At a 45-degree angle to the longest bend or edge
A note on welded parts: weld beads leave a raised surface at the weld site. Our process involves blending the weld bead into the metal material, leaving a uniform edge.
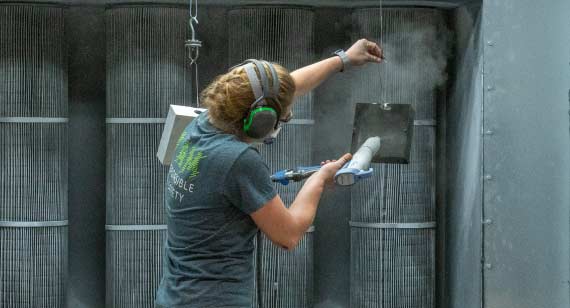
Powder Coating
Powder coating applies a dry powder to the surface of sheet metal parts. Then, they are cured in a large oven to create a hard finish that is tougher than conventional paint. This process improves durability to parts and adds custom color for aesthetic purposes.
Choose from 50 stocked colors for the fastest turnaround time. Various texture and gloss levels are available.
Learn more about powder coating
Plating and Coatings
Plating or coating can provide corrosion resistance, remove contaminants from the metal surface, enhance durability, and add functional benefits. Review the table below for the most selected options. Please note:
- All finish types shown below are available in additional MIL or ASTM specifications.
- We can source your coating through a NADCAP-certified supplier, if necessary.
If your project falls into one or both of these categories, please contact your account representative for more information.
Sheet Metal Plating and Coating Options
Finish | Descriptive Name | Specification | Compatible Material Types | Example | Additional Information |
Anodizing | Clear Anodizing | MIL-A-8625, Type II, Class 1 | Aluminum | ![]() |
|
Black Anodizing | MIL-A-8625, Type II, Class 2, Black | ||||
Color Anodizing | MIL-A-8625, Type II, Class 2, "Color" | Request your color choice in the "custom option" selection of your online quote. You can request any color. | |||
Hardcoat Anodizing | Clear Hardcoat Anodizing | MIL-A-8625, Type III, Class 1 | Aluminum | Minimum coating thickness 0.020in. (0.508mm) | |
Black Hardcoat Anodizing | MIL-A-8625, Type III, Class 2, Black | ||||
Hardcoat Anodizing with Teflon | MIL-A-63576, Type I | ||||
Chromate | Yellow Chromate (Chem-Film) | MIL-DTL-5541, Type I, Class 3 | Aluminum | ![]() |
Hexavalent chromate |
Clear Chromate (Chem-Film) | MIL-BTL-5541, Type II, Class 3 | RoHS, non-hexavalent chromate | |||
Electroless Nickel | Electroless Nickel, EN | ASTM-B733, Type IV, SC1, Class 1 |
Aluminum Steel** Stainless Steel** |
Minimum coating thickness 0.0002 in. (0.005mm). **ASTM specifications for these materials are not listed on this table, but you can find them in your online quote. |
|
Passivation | Nitric Passivation | ASTM-A967, Nitric 2, Practice D | Stainless Steel | ![]() |
|
Citric Passivation | ASTM-A967, Citric 3, Practice D | ||||
Zinc | Zinc | ASTM-B633, Type I, FE/ZN 5 SC1 | Steel | ![]() |
Zinc with no supplementary treatment; minimum coating thickness 0.0002 in. (0.005mm) |
Yellow Zinc | ASTM-B633, Type II, FE/ZN 5 SC1, Yellow | Zinc with colored (yellow) chromate; minimum coating thickness 0.0002 in. (0.005mm) | |||
Black Zinc | ASTM-B633, Type II, FE/ZN 5 SC1, Black | Zinc with colored (black) chromate; minimum coating thickness 0.0002 in. (0.005mm) | |||
Clear Zinc | ASTM-B633, Type III, FE/ZN 5 SC1, Clear | Zinc with colorless chromate; minimum coating thickness 0.0002 in. (0.005mm) | |||
Tin | Tin | ASTM-B545, Class A | Copper |

Sheet Metal Surface Finish Guide
Check out our sheet metal guide for a quick snapshot of our Standard and Cosmetic finishing options available for various sheet metal materials.
Download GuideWet Paint
With wet paint, a liquid coating is applied to your part to provide an aesthetically appealing finish. The process is offered in virtually any color and is commonly paired with a primer layer to improve paint adhesion and durability.
Wet paint is often used in situations where the visual consistency of the finish across parts is an important consideration, which is why you primarily see it on automotive or consumer electronics products.
Our wet paint options are available with or without primer.
To ensure we can meet your specifications exactly, we ask you provide the full paint specification (including color and texture). These details can be conveyed two ways. Pick the option that is easiest for you. It's not necessary to submit both ways:
- Submit a 2D-drawing with the wet paint specifications included.
- In the "Coating" section of your online quote, depending on your project needs, select "Wet Paint" or "Wet Paint with Primer" from the drop-down menu.
- In the "Spec" field, enter the wet paint specifications as described above.
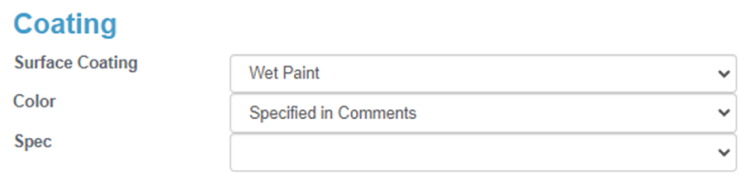
Wet paint special considerations:
- Quotes with wet paint service may take slightly longer than 24 hours.
- If masking is required as a component of your finished product, please submit a 2D-drawing.
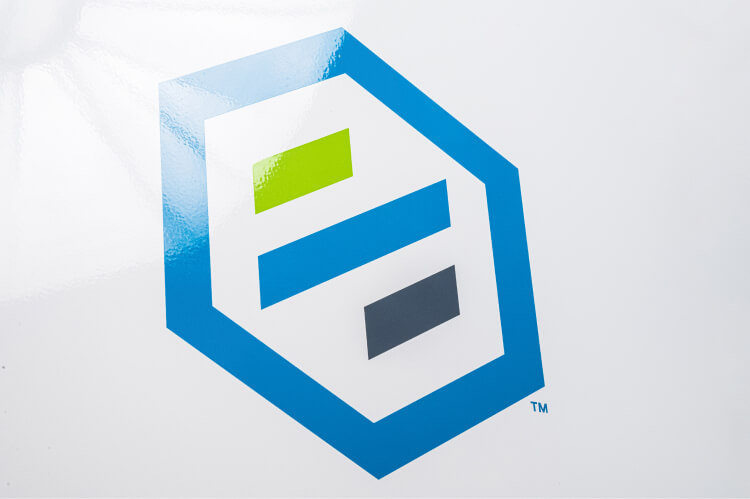
Silk Screening
Silk screening on sheet metal involves forcing ink through a fine mesh screen containing a stencil that blocks off areas in order to achieve the desired design. Ink is transferred to areas not covered by the stencil onto the metal surface. This process is often used for adding labels, instructions, or decorative patterns to fabricated metal products.
Requesting silk screening on your next project is easy. Just submit the following information:
- An image saved as an .ai, .dxf, or .PDF file
- Part location for the silk-screened artwork
- Color data based on the Pantone Matching System (PMS)
Additionally, please note these silk screening considerations:
- Minimum screen size: 1 in. (25.4 mm) square
- Maximum screen size: 24 in. (609.6mm) by 14 in. (355.6mm)
- Screening internal faces requires at least 1 in. (25.4mm) margin from bends and other part features
Masking
Masking is a common step in the finishing process when it comes to sheet metal components, assemblies, or electrical enclosures. We use tape, rounds, and plugs to allow for selective application of finishes on your design. Some key benefits of masking include:
- Protection of functional areas of the part such as hardware inserts, threaded holes, or surfaces
- Solid dimensional tolerances with the unfinished state. Finishing processes add to the thickness of your part, which may affect fit or function of certain designs.
- Avoiding coating applications in areas where electrical conductivity is needed
- Improved aesthetic appeal of the overall design
Request masking in a 2D drawing submitted with your CAD file. The 2D drawing should include the location of masked areas, as well as which holes/inserts are to be plugged.
We offer a range of tape and rounds (discs):
Tape | Rounds/Discs |
---|---|
0.250 in. | 0.3125 in. |
0.500 in. | 0.375 in. |
0.675 in. | 0.500 in. |
0.750 in. | 0.625 in. |
1.000 in. | 0.750 in. |
2.000 in. | 1.000 in. |
Tape | Rounds/Discs |
---|---|
6.35mm | 7.938mm |
12.7mm | 9.525mm |
17.145mm | 12.7mm |
19.05mm | 15.875mm |
25.4mm | 19.05mm |
50.8mm | 25.4mm |
If your supply chain requires all parts to be uniquely marked for traceability purposes, we offer a stenciling process that can provide:
- Part number
- Revision level
- Vendor code/ID
- Cage code
To include part marking with your part or project, submit a 2D drawing including:
- Location on part for marking placement
- Font size (minimum 12 pt., maximum 16 pt.)
- Color
- Information to be marked (choose from list on the left)
Standard and Cosmetic Parts
Whether you're developing a prototype to check form, fit, or function, or you need quick-turn cosmetic parts for your next trade show, we have you covered. Use this guide to choose the best option for your project.
Standard | Cosmetic | |
---|---|---|
Description | When lower cost is a greater priority than appearance | Functionally cosmetic parts that make you and your parts look good to stakeholders |
Use Cases | Form, fit, function prototyping; internal components | Testing or demonstration units, trade show parts, external components |
Part Applications | Internal brackets and mounts, heat shields, support structures, washers, spacers, electrical components | Housings, covers, face plates, external brackets and mounts |
Surface Finish | Protolabs' discretion | Customer specified (grain direction, orbital sanded) |
Safe Handling | Yes | Yes |
Cost | $ | $$ |
Quantity | 1-100+ parts | Best for 1-25 parts |
Related Resources