Talk with Our Team
Hello! We just need a few bits of information then a manufacturing expert will reach out to you directly to see we how can partner on a future production project.
Thank you! We've received your request and a member of our team will reach out shortly.
Accelerating Medical Device Prototyping and Production
Get to market faster and streamline your supply chain with rapid prototyping and on-demand production of medical components
Certification + Compliance
ISO 9001:2015 | ISO 13485:2016 | ITAR
How Do Medical Companies Use Protolabs?
Rapid PrototypingCreate prototypes in production-grade materials for functional and regulatory testing, or use our 3D printing service to print models and organ scans to preview before medical procedures. |
Low-Volume ProductionRamp up production to get quality end-use parts to market fast and use batch production to reduce financial risk with no minimum order quantity (MOQ) and low total cost of ownership (TCO). |
On-Demand ProductionBuild agility into your supply chain by ordering quick-turn parts when needed, regardless of what stage of development you’re in. |
Quality CertificationStreamline development of FDA Class I and II devices, or non-implantable components, with molding capabilities geared towards high-requirement applications and ISO 13485 quality certification. |
Medical MaterialsChoose from high-temperature plastics, medical-grade silicone rubber, and 3D-printed micro-resolution and microfluidic parts, among hundreds of other plastic, metal, and elastomeric materials. |
We are the fastest and most comprehensive digital manufacturer in the industry with more than 25 years of experience developing products for innovative medical companies around the world. | 96% of Fortune 500 Medical Companies Served |
700 Million Parts Manufactured |
300,000 Customers Served |
Full Production Support Team
We have a team of manufacturing experts working behind the scenes to fulfill your production order—we manage the entire process and keep you updated along the way. |
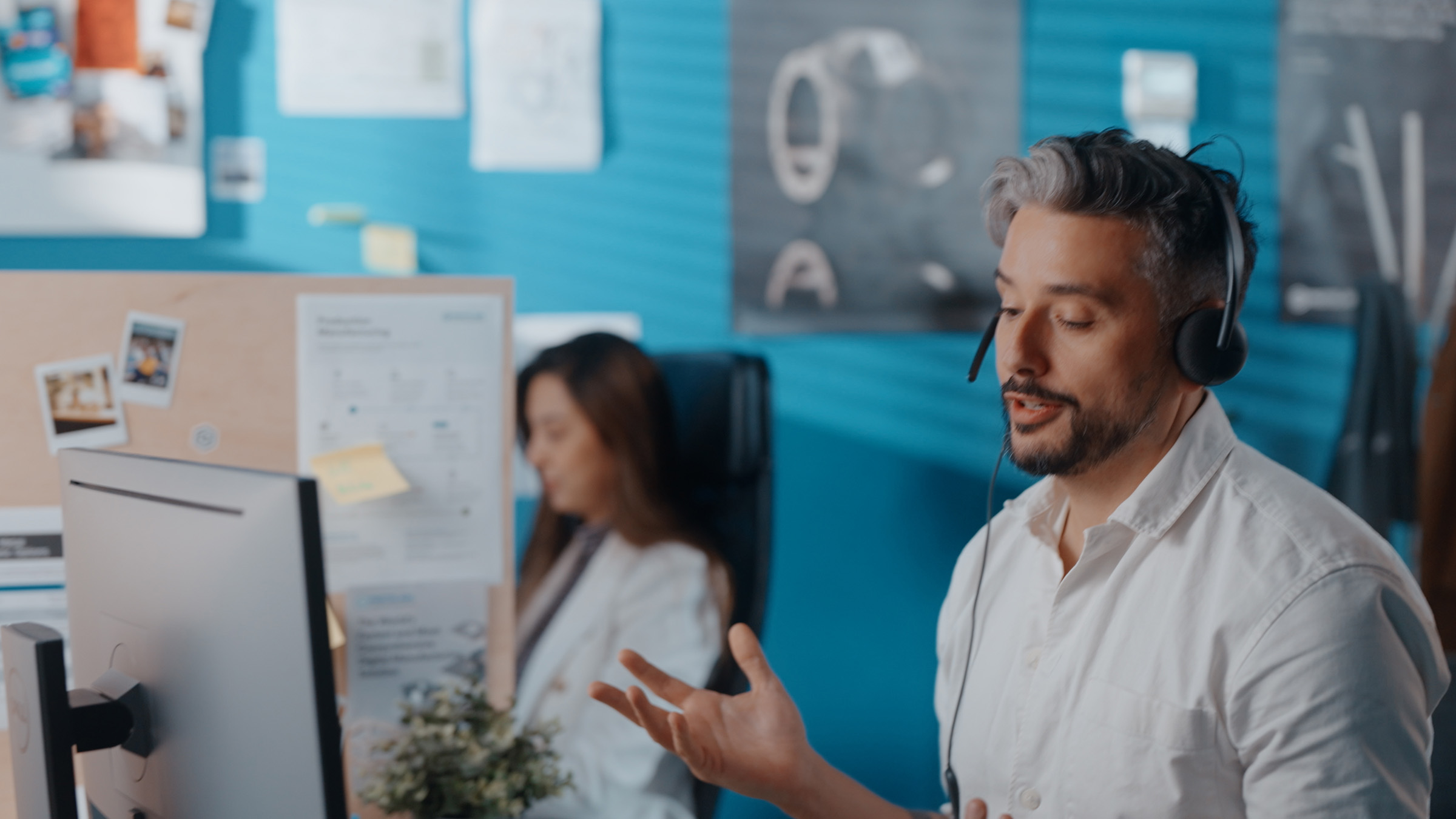
Account ManagerA dedicated account manager provides support, including assistance with platform and file uploads. |
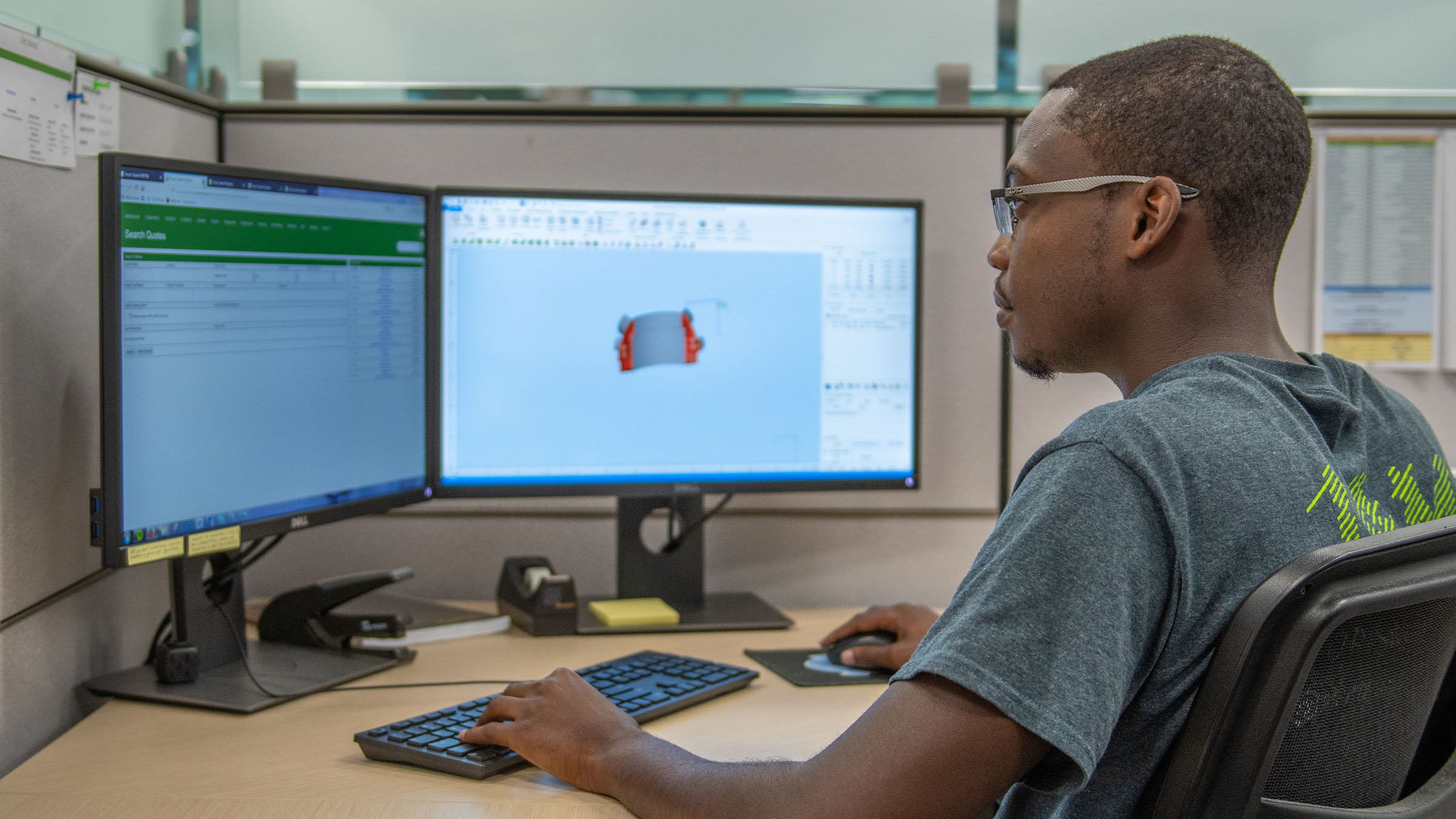
Applications EngineersExpert CAD solutions and cost-reduction strategies tailored by in-house applications engineers to optimize your designs. |
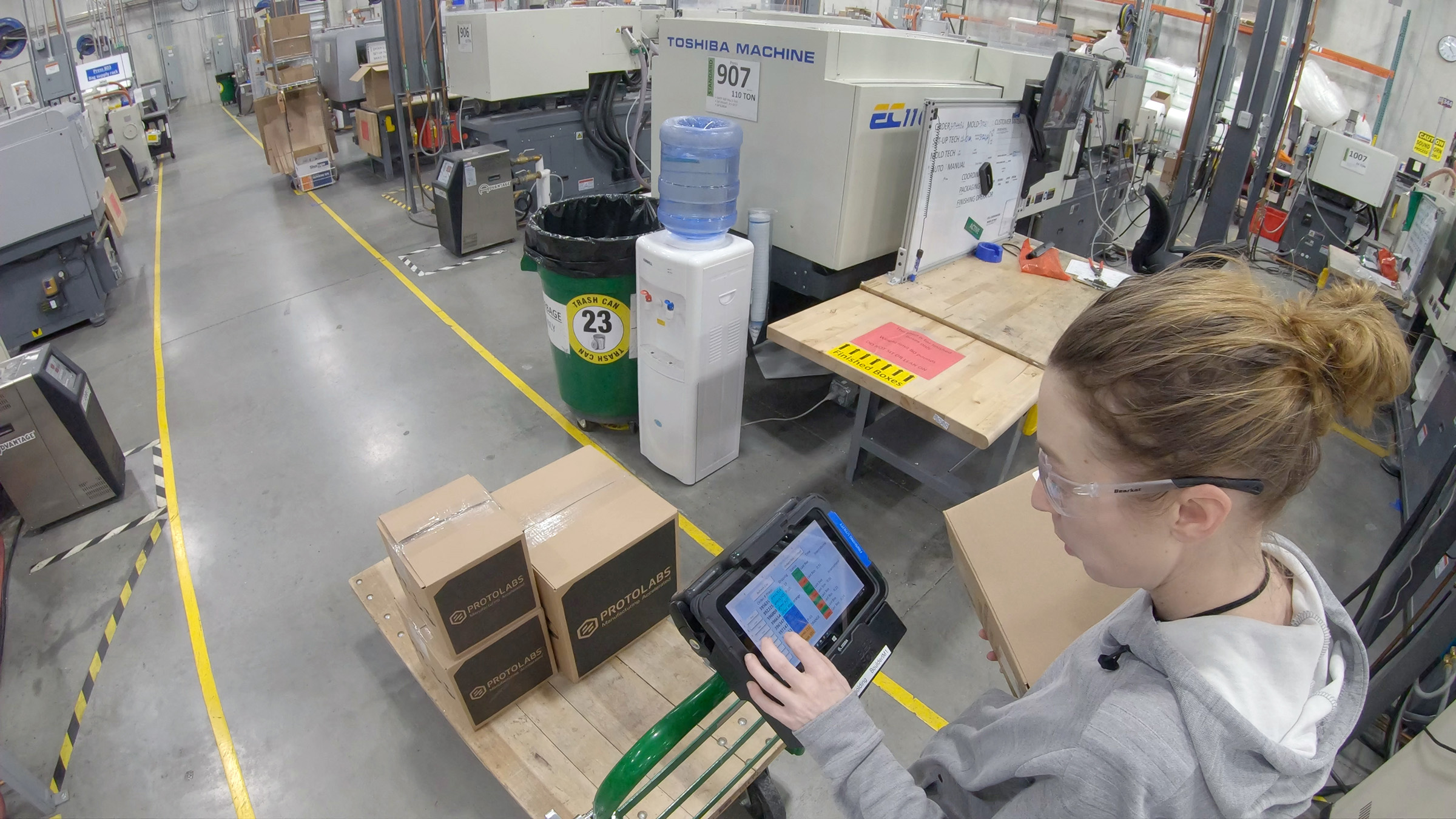
Logistics |
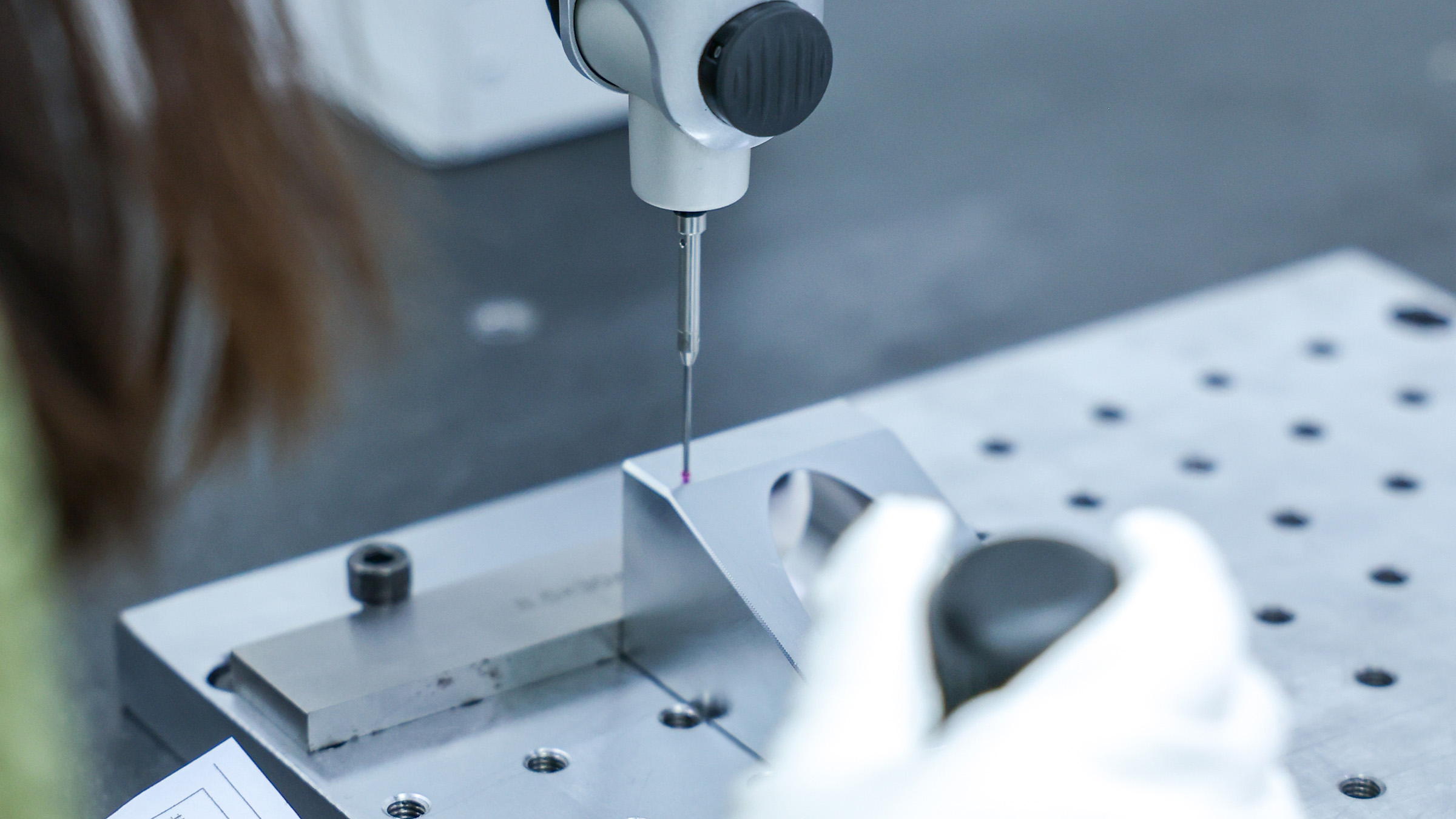
Quality Control |

Manufacturing Services for Medical Products
Injection Molding
Get affordable, high-quality molded parts and bridge tooling within days. With our free moldability consultation, the design and molding process is rapidly accelerated to save you time and money.
- Low-volume molding up to 100,000+ parts with volume pricing available—no MOQ required
- 100+ plastic, elastomeric, and silicone rubber materials
- Automated CMM for fast, in-house quality documentation
CNC Machining
Leverage the same speed, precision, and reliability in machining that you’re accustomed to at Protolabs but unlock advanced machining capabilities like tighter tolerances and volume pricing through our manufacturing network.
- Machined parts in as fast as 1 day with optional plating and anodizing in as fast as 4 days
- Cost-efficient machined parts at higher volumes
- Tolerances down to ±0.001 in. (0.020mm) through our digital network
3D Printing
Want quality parts and additive expertise at a single 3D printing source? Choose from seven different additive manufacturing technologies for cost-effective prototyping and highly precise, repeatable production parts.
- Additive technologies include metal 3D printing, SLA, SLS, FDM, and more
- 30 plastic and metal materials in a range of finishes
- 25 years of additive manufacturing expertise
Sheet Metal Fabrication
From easy quoting to quick-turn production and finishing options, get up to 500 quality sheet metal parts in your hands in days from a single supplier.
- Instant quotes with interactive manufacturability feedback
- Six sheet metal materials including aluminum, stainless steel, steel, brass, and copper
- Finishing options from welding and hardware insertion to powder coating and silk screening
Your Trusted Partner in Medical Product DevelopmentSpeed, quality, and technical expertise are built into our entire process. Partnering with us helps ensure your design is optimized, your development timeline is accelerated, and that you're supported from prototyping through end-use production. |

Quality Measures for the Medical Industry
Our industry-standard procedures and certifications guarantee quality and regulatory compliance.
CMM inspection report | First Article Inspection (FAI) |
Dimensional Inspection Report (DIR) | PPAP |
Material Certificates + Certificate of Analysis | Conflict Minerals Reporting |
REACH + RoHS Certificates | Prop65 |
Industry Certifications: ISO 9001 and AS 9100 | Certificate of Conformance (CoC) |
Industry Certifications (Protolabs Network): ISO 13485, ISO 14001, ISO 45001, and ISO TS16949 |
Materials for Medical Applications

High-temp PlasticsPEEK and PEI (Ultem) offer high-temperature resistance, creep resistance, and are suited for applications that require sterilization. |
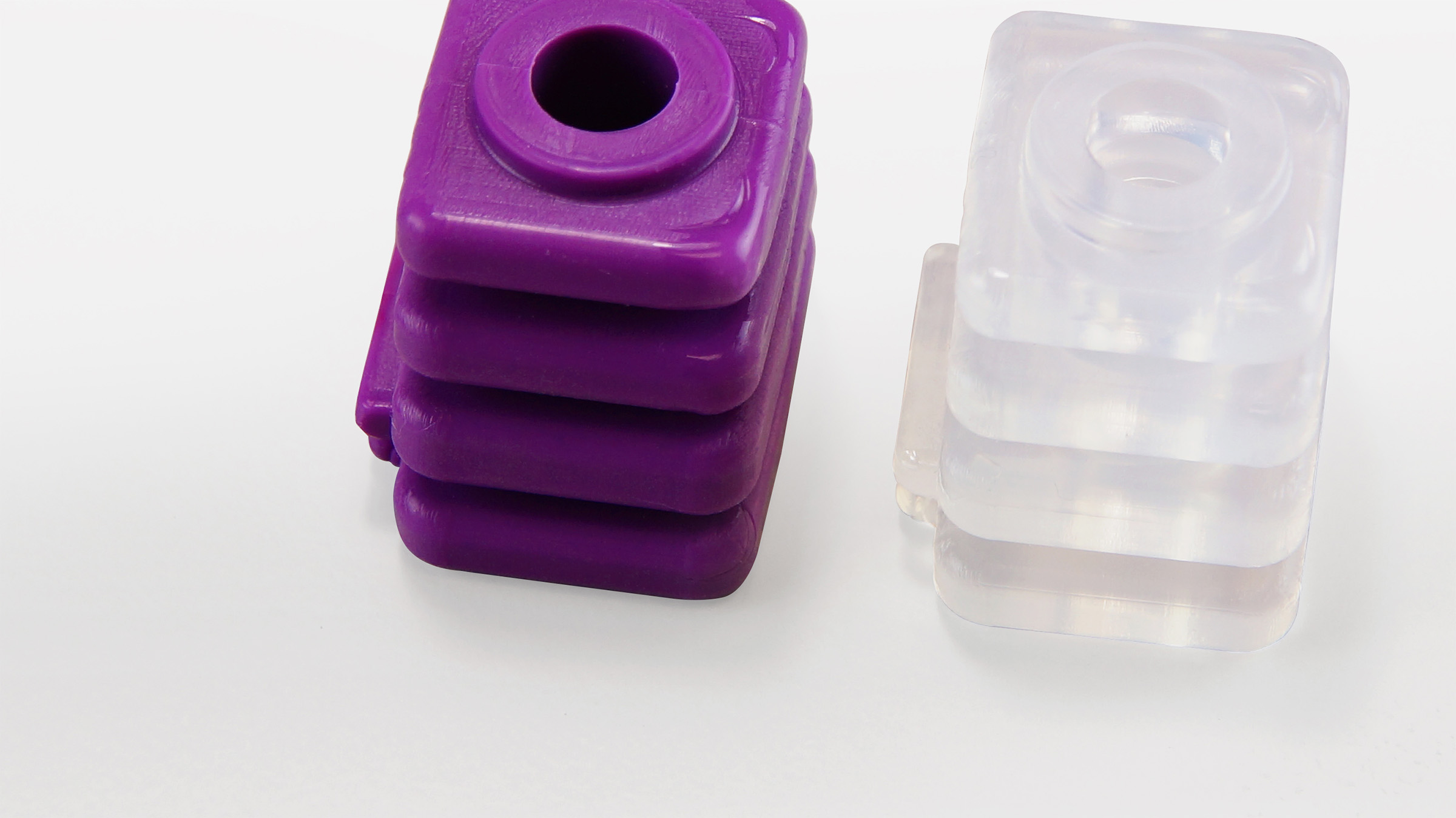
Medical-grade Silicone RubberDow Corning’s QP1-250 has excellent thermal, chemical, and electrical resistance. It’s also bio-compatible so can be used in applications that require skin contact. |
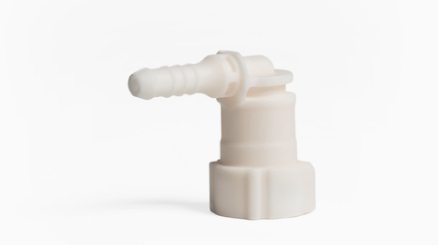
Advanced PhotopolymersTough Black and ceramic-filled are production-grade materials available through our Hybrid Photosynthesis (HPS) technology, ideal for late-stage prototyping or end-use devices. |
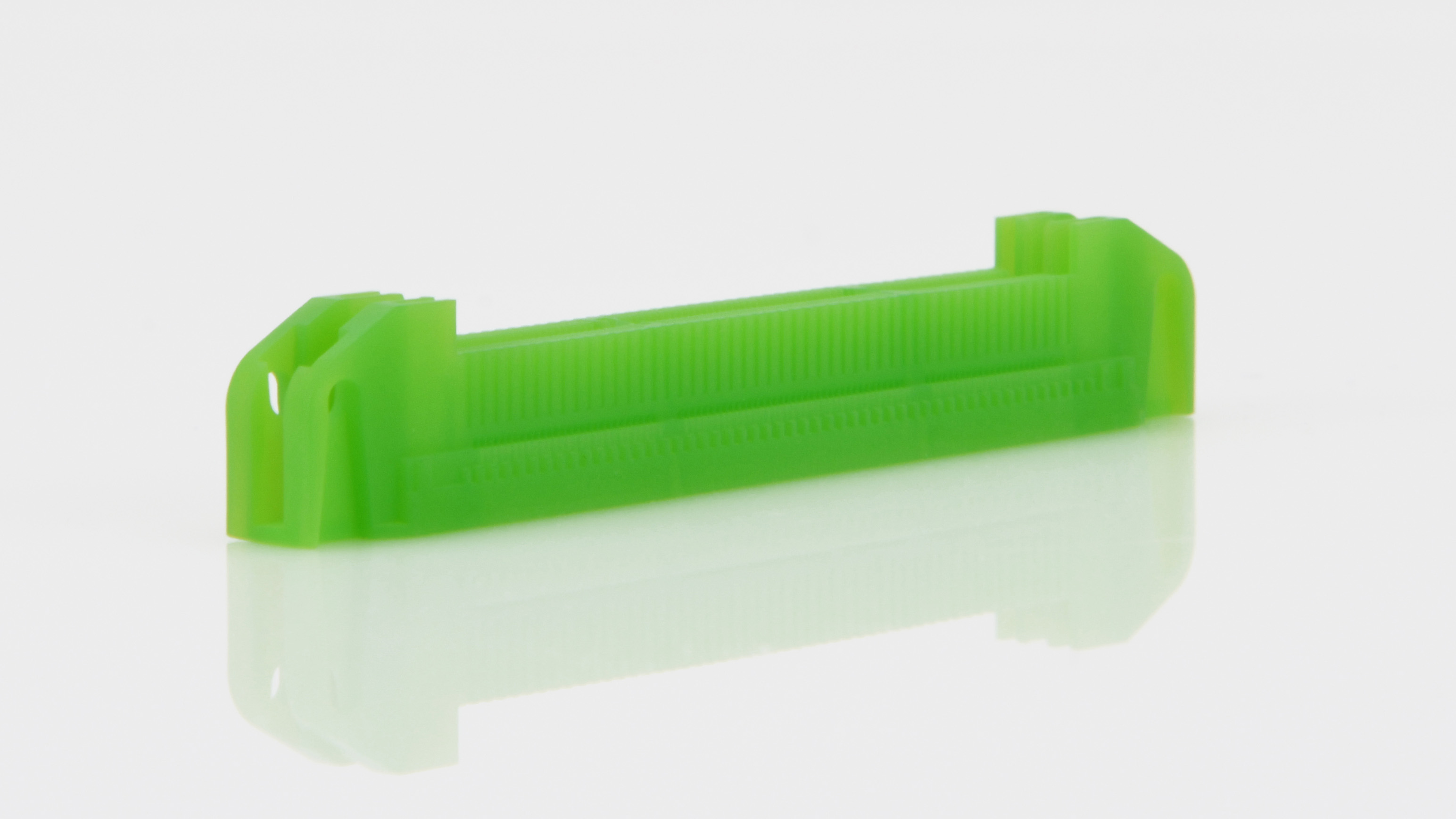
Micro-resolutionMicroFine™ (green and gray) is a proprietary material developed by Protolabs to build complex 3D-printed parts with micro-sized features as small as 0.0025 in. |

MicrofluidicsWatershed (ABS-like) and Accura 60 (PC-like) are clear materials can be used for microfluidic parts and transparent components like lenses and housings. |
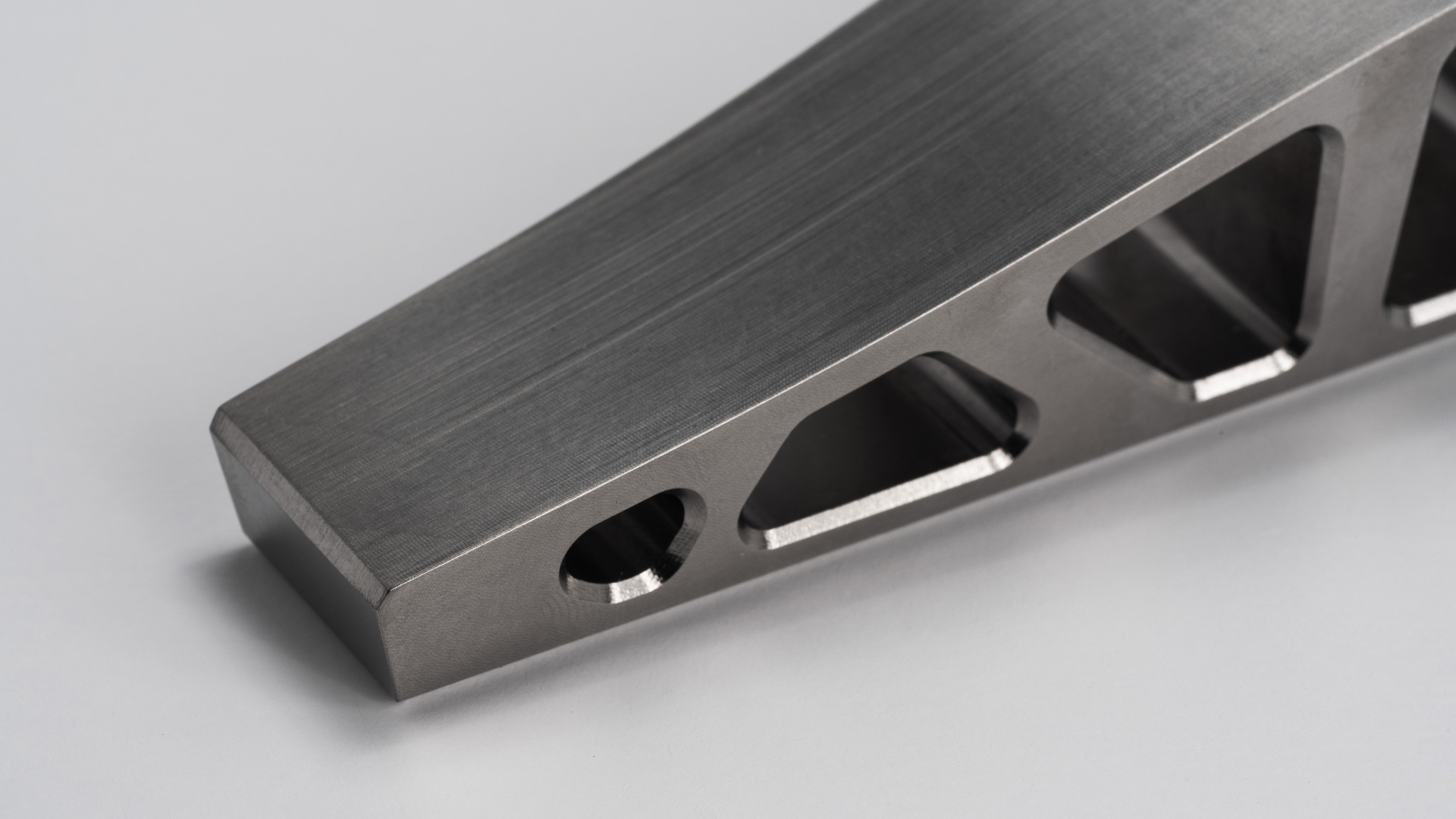
Medical AlloysBetween machined and 3D-printed metals along with sheet metal, there are more than 20 metal material options available for medical components, and other applications. |
Common Medical Applications
We have several capabilities within our manufacturing services catered to the medical industry. Here are a few applications we frequently see.
|
|

Parker Hannifin Brings Robotic Exoskeleton to Life with Protolabs
Engineers at motion and control tech leader, Parker Hannifin, needed to accelerate development speed and reduce design risk of their robotic exoskeleton. A combination of digital manufacturing technologies and automated quoting enabled a high iterative design process without sacrificing time to market. |