Process traceability is becoming increasingly important in the manufacturing industry, particularly in higher volume processes like injection molding. We'll delve into the significance of traceability in the injection molding process and examine how we use a unique digital thread approach along with advanced molding techniques and inspection methods to track parts from customer upload to shipment.
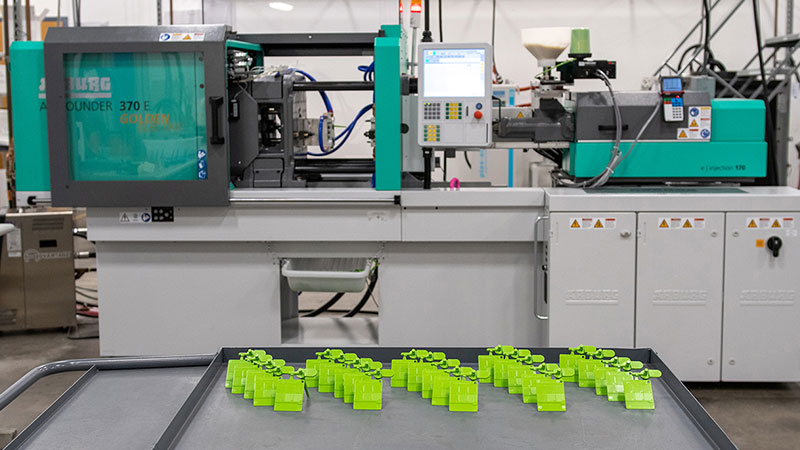
What is Process Traceability?
Process traceability generally refers to the ability to track and trace the manufacturing cycle of a product. In the context of injection molding, this means tracking individual aspects of a part's production, production parameters, and quality control measures.
The Benefits of Process Traceability in Injection Molding
There are multiple reasons why process traceability has become a vital element of the manufacturing process.
- Quality Assurance. Tracking production parameters and quality control data throughout the molding process enables manufacturers to maintain consistent product quality, quickly detect and correct any deviations or defects, and minimize product non-conformance.
- Regulation Compliance. As regulations in various industries grow more stringent, process traceability is becoming crucial for manufacturers to demonstrate compliance with safety and quality standards, as well as consistency and robustness of a process.
- Intellectual Property Protection. In an era of increasing data and intellectual property (IP) concerns, process traceability helps product developers and manufacturers protect IP from things like counterfeiting or theft and pinpoint the source if an unforeseen event does occur.
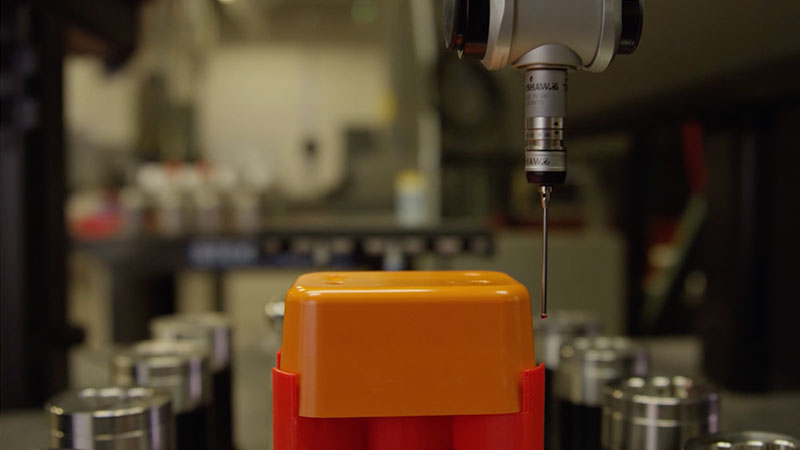
Advanced Molding Techniques and Process Traceability
We have developed a unique process that incorporates advanced molding techniques such as scientific molding (two-stage decoupled molding) and automated coordinate measuring machine (CMM) inspection. During that process we're able to track a part from your upload all the way through to part shipment by way of digital thread that tethers everything together. All along the digital thread, there are multiple points at which data from the process is recorded, timestamped, and verified before moving on to the next stage of the process. Some of these are:
- Automated Quoting and Design for Manufacturability (DFM) Analysis. Our customers upload their 3D CAD models into our unique online quoting platform, from which they receive a quote with detailed DFM analysis. This initial data is stored in your user account and serves as the foundation for the digital thread.
- Material and Process Selection. Once your DFM feedback is approved and your design is manufacturable, you can choose from a range of materials and specify the service level in which your part will be manufactured. We offer different service levels for prototyping and end-use parts, and it’s important to choose the best process for your volume and quality requirements. Check out the table for more information about service levels.
- Scientific Molding. In our on-demand manufacturing (ODM) service, we offer scientific molding, which means that your parts will go through robust molding process development before we begin your run. The digital thread captures essential data points from these stages, including mold temperatures, injection pressures, and cycle times, ensuring accurate tracking and traceability. When the run is complete, you’ll receive a molding process development report with the optimized parameters that were used to manufacture the parts. This information is also added to the digital thread, ensuring all relevant data is recorded and can be referenced on your next run.
- Quality Control and Automated CMM Inspection. We implement quality control measures throughout the production process and the results are recorded in the digital thread. We conduct automated CMM inspections with each ODM mold order. These include a three-part first article inspection (FAI) on five critical dimensions and a 30-part capability report on the same dimensions. This critical-to-quality inspection ensures dimensional verification and traceability, which helps to maintain consistent product quality.
- Part Shipment and Documentation. Once the parts are ready for shipment, the digital thread generates all necessary documentation, including a Certificate of Conformance (CoC), as well as the aforementioned molding process development and dimension inspection reports. These provide customers with a detailed record of their parts' production journey, as well as lessons learned throughout the process!
Better Molded Parts Through Documentation
Process traceability transforms the injection molding industry by improving quality assurance, regulatory compliance, and intellectual property protection. The digital thread connected to advanced molding techniques like scientific molding and automated CMM inspection, exemplifies how end-to-end traceability benefits the injection molding process, manufacturers, and their customers. As the industry continues to evolve, embracing these advanced technologies and traceability methods will become increasingly essential for companies to stay competitive and meet customer demands.

If you have any issues getting your guide, click here to download.

Need custom parts? Upload a 3D CAD file to get an online quote.
Get Custom Parts