
SLS 3D Printing Service
Order custom SLS parts suitable for rapid prototyping, functional testing, and end-use production.
Certification + Compliance
ISO 9001:2015 | ISO 13485:2016 | AS9100D | ITAR
Jump to Section
→ Capabilities
→ Materials
→ Surface Finishes
→ SLS 3D Printers
→ About Selective Laser Sintering
Selective laser sintering (SLS) is an industrial 3D printing process that produces accurate prototypes and functional production parts in as fast as 1 day. Multiple nylon-based materials and a thermoplastic polyurethane (TPU) are available, which create highly durable final parts that require heat resistance, chemical resistance, flexibility, or dimensional stability. With SLS 3D printing, no support structures are required making it easy to nest multiple parts into a single build and an economical solution for when higher volumes of 3D-printed parts are required.
Common uses for selective laser sintering are:
- jigs and fixtures
- housings
- snap fits and living hinges
Why Use SLS?
See how SLS uses actual thermoplastic and elastomeric materials to produce parts with good mechanical properties. Final parts can be used to test future injection molding designs or as functional, end-use components.

Vapor Smoothing is Here!
Vapor smoothing is now available for select 3D-printed nylon parts. The process eliminates rough surfaces and leaves a glossy, aesthetic finish on parts.
Learn More
Selective Laser Sintering (SLS) Materials
PA 11 Black (PA 850)
expand_less expand_morePA 11 Black (PA 850) provides ductility and flexibility without sacrificing tensile strength and temperature resistance. These characteristics make PA 850 a widely used general-purpose material for functional and moving parts.
Primary Benefits
- Highest elongation at break of all additively manufactured nylons
- Uniform deep-black color that showcases features and provides a clean appearance
PA12 Black
expand_less expand_morePA12 Black has all-around great mechanical properties and chemical resistance and is ideal for functional parts and prototypes.
Primary Benefits
- Highly isotropic mechanical properties
- Economical material choice
PA 12 White (PA 650)
expand_less expand_morePA 12 White (PA 650) is a go-to material for general-purpose applications like functional and end-use parts. PA 650 is the strongest of the unfilled nylon materials and it is slightly stiffer than PA 11 Black.
Primary Benefits
- Economical material choice
- Strength and stiffness
PA 12 Value
expand_less expand_moreThis sustainable and highly cost-effective material is made from recycled powder. It has an off-white hue but otherwise behaves much like PA12 White, offering high impact and temperature resistance plus stability under a wide range of environmental conditions and near isotropic mechanical properties. PA12 Value is a great choice for functional and prototype parts.
Primary Benefits
- Sustainability
- Durability
- Versatility
PA12 Mineral-Filled (PA620-MF)
expand_less expand_morePA12 Mineral-Filled (PA620-MF) is a 25% mineral fiber-filled PA powder. The fiber content significantly increases stiffness and HDT (up to 363 °F). It is a good material option when stiffness and high temperature resistance are important requirements.
Primary Benefits
- Highest stiffness of all additively manufactured nylons
- Temperature resistance
PA12 40% Glass-Filled (PA614-GS)
expand_less expand_morePA12 40% Glass-Filled (PA614-GS) is a PA powder loaded with glass spheres that make it stiff and dimensionally stable. This material is an ideal candidate for parts that require long term wear resistance properties. Due to the glass additive, it has decreased impact and tensile strengths compared to other nylons.
Primary Benefits
- Long-term wear resistance
- Increased stiffness
Polypropylene Natural
expand_less expand_morePolypropylene Natural offers chemical resistance properties that are top among the SLS and MJF material offerings. This tough and durable, yet flexible, material offers resistance to most acids and is a low weight material option.
Primary Benefits
- Chemical resistance
- Durable, low weight material
TPU 70-A
expand_less expand_moreTPU 70-A is a white thermoplastic polyurethane that combines rubber-like elasticity and elongation with good abrasion and impact resistance properties. The rubber-like quality of this material make it ideal for seals, gaskets, grips, hoses, or any other application where excellent resistance under dynamic loading is required.
Primary Benefits
- High elongation at break
- Flexibility
Compare Material Properties
Material | Color | Tensile Strength | Tensile Modulus | Elongation |
---|---|---|---|---|
PA 11 Black (PA 850) |
Black | 7.54 ksi | 261 ksi | 30% |
PA12 Black | Dyed Black | 6.7 ksi | 276 ksi | 13% |
PA 12 White (PA 650) |
White | 7.25 ksi | 290 ksi | 11% |
PA12 Value | Off White | 6.7 ksi | 276 ksi | 13% |
PA 12 Mineral-Filled (Duraform HST) | Light Gray | 5.51 ksi | 450 ksi | 3% |
PA 12 40% Glass-Filled (PA 614-GS) |
White | 7.25 ksi | 522 ksi | 5% |
Polypropylene Natural | Natural | 2.61 ksi | 123 ksi | 15% |
TPU 70-A | White | 580 psi | 210% |
Material | Color | Tensile Strength | Tensile Modulus | Elongation |
---|---|---|---|---|
PA 12 White (PA 650) |
White | 50.0 Mpa | 2,000 Mpa | 11% |
PA12 Black | Black | 46 Mpa | 1,900 Mpa | 13% |
PA 11 Black (PA 850) |
Black | 52 Mpa | 1,800 Mpa | 30% |
PA12 Value | Off White | 46 Mpa | 1,900 Mpa | 13% |
PA 12 Mineral-Filled (Duraform HST) | Light Gray | 38 Mpa | 3,100 Mpa | 3% |
PA 12 40% Glass-Filled (PA 614-GS) |
White | 50 Mpa | 3,600 Mpa | 5% |
Polypropylene Natural | Natural | 18 Mpa | 848 Mpa | 15% |
TPU 70-A | White | 4.0 Mpa | 210% |
These figures are approximate and dependent on a number of factors, including but not limited to, machine and process parameters. The information provided is therefore not binding and not deemed to be certified. When performance is critical, also consider independent lab testing of additive materials or final parts.
Surface Finish for SLS Parts
Surface finish on SLS parts is typically rougher than other 3D printing technologies—it can range from 100-250 RMS. We also bead blasts the majority of customers’ parts to remove loose powder and create a smooth matte finish. Vapor smoothing is a post-processing option available for PA11 Black parts, which will result in surface finish roughness between 64 – 100 μin RA.
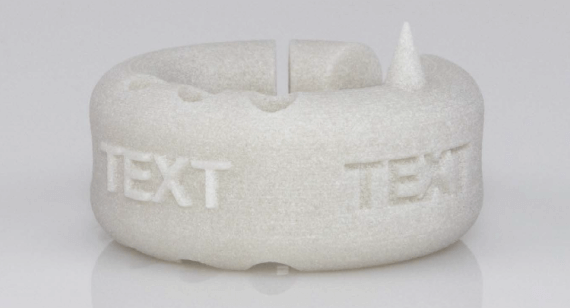
Material: PA12 40% Glass-Filled (PA614-GS)
Resolution: Normal (0.004 in. layer thickness)
Finish: Standard
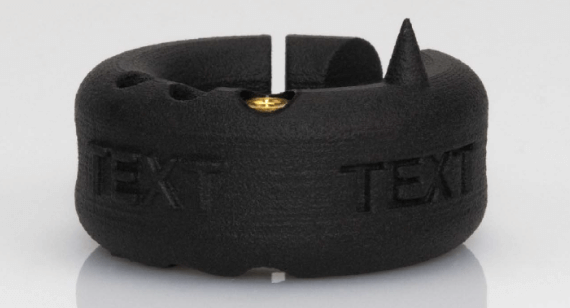
Material: PA11 Black (PA850)
Resolution: Normal (0.004 in. layer thickness)
Finish: Standard
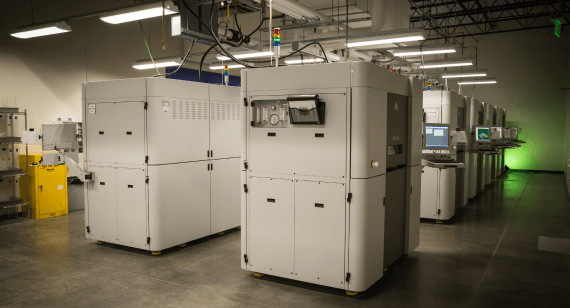
Our SLS 3D Printers
Our SLS equipment includes sPro140 machines, which have the world’s largest sintering build volume, and feature fully digital high-speed scanning systems, unparalleled process consistency, and closed systems for powder blending and delivery for reliable part quality. We also use sPro60 machines, which allow for multiple materials and high throughput.
How Does SLS 3D Printing Work?
The SLS machine begins sintering each layer of part geometry into a heated bed of nylon-based powder. After each layer is fused, a roller moves across the bed to distribute the next layer of powder. The process is repeated layer by layer until the build is complete.
When the build finishes, the entire powder bed with the encapsulated parts is moved into a breakout station, where it is raised up, and parts are broken out of the bed. An initial brushing is manually administered to remove a majority of loose powder. Parts are then bead blasted to remove any of the remaining residual powder before ultimately reaching the finishing department.
Tour Our 3D Printing Facility
Take a quick tour through our additive manufacturing facility in North Carolina, one of the largest 3D printing operations in the world, to see how we build high-quality prototypes and fully functional end-use components and assemblies.