Vapor Smoothing for
3D Printing
Vapor smoothing eliminates rough surfaces and leaves a glossy, aesthetic finish on parts
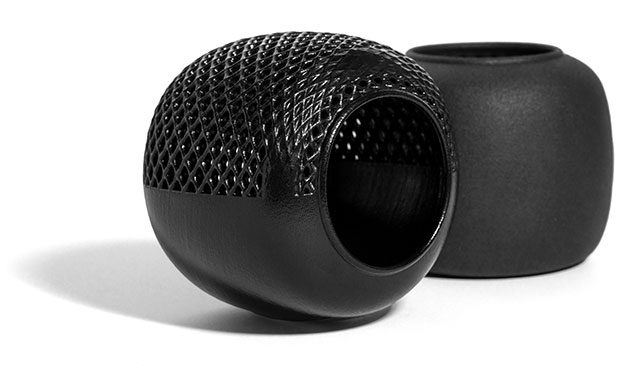
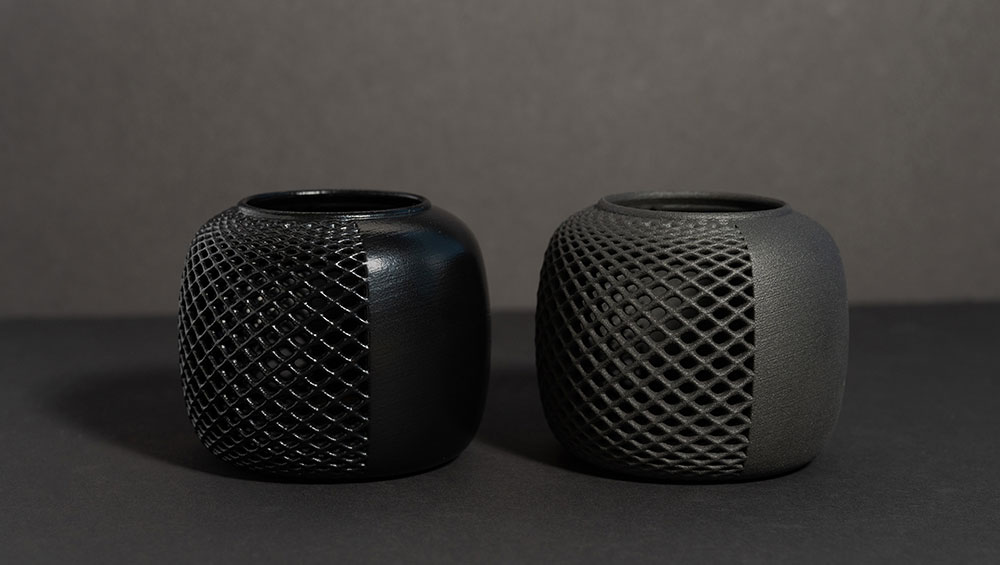
The left part has been vapor smoothed. The right part has a standard finish.
How Vapor Smoothing Works
After the parts have been 3D printed, they are transferred into a smoothing chamber. Using controlled evaporation, a vaporized smoothing agent condenses on the parts’ surfaces creating a controlled chemical melt.
This process reduces peaks and troughs on the surface by liquifying and redistributing material evenly in a carefully controlled atmosphere. Once finished, the equipment evacuates the finishing agent to a collection vat so there is no residue left on the parts.
Benefits of Vapor Smoothing
![]() |
Uniform color that showcases features and provides a clean appearance |
![]() |
Improved cosmetics over standard finish SLS and MJF parts |
![]() |
Significant reduction of surface roughness from 250+ μin RA (as-printed) to 64 – 100 μin RA (after smoothing) |
![]() |
Sealed surfaces that are liquid resistant and easy to clean |

Vapor Smoothing Design Guidelines for Printed Parts
Maximum part size
10.6 in. x 12.6 in. x 16.0 in. (269mm x 304mm x 406mm)
Wall thickness
- Radiused internal features work best for vapor smoothing
- Consistent wall thickness will yield more consistent smoothing and better aesthetics
- Minimum wall thickness: 0.030 in. (0.762mm)
Part features
Ideally, the part would have a through hole with a minimum diameter of 0.04 in. (1mm) or an exterior wall with a thickness between 0.04 in. (1mm) and 0.20 in. (5.1mm) so that the part can be easily hung from a rack. We can still smooth almost any part, regardless of its features, but we may have to add a small sacrificial feature that would be removed after smoothing, leaving a small ~2m diameter non-smoothed mark on the part’s surface.
Tolerances
For well-designed parts, tolerances of ±0.010 in. (0.25mm) plus 0.1% of nominal length can typically be achieved. Note that tolerances may change depending on part geometry.
Minimum feature size
0.03 in. (0.762mm)
Warpage
Larger part sizes (>7 in.) and parts with thin features are the most susceptible to warp. We recommend maintaining a uniform thickness of 0.125 in. (3.175mm) to ensure stability.
Post-process finishing
Vapor smoothing can be combined with additional post-processing steps such as tapped or threaded inserts or painting.
Applications for Vapor-Smoothed Parts
Vapor smoothing on printed medical parts enables aesthetic designs that are comfortable, easy to clean, and sweatproof. It’s also ideal for automotive and industrial machinery as it produces smooth, tactile, leak-proof 3D-printed parts. These properties allow for a wide range of applications, from concept modeling to prototyping testing and end-use parts.
Typical use cases include:
- custom medical devices
- wearables
- liquid reservoirs and tanks
- fluid transfer pipes and manifolds
- ducts
- valve covers
- oil sumps
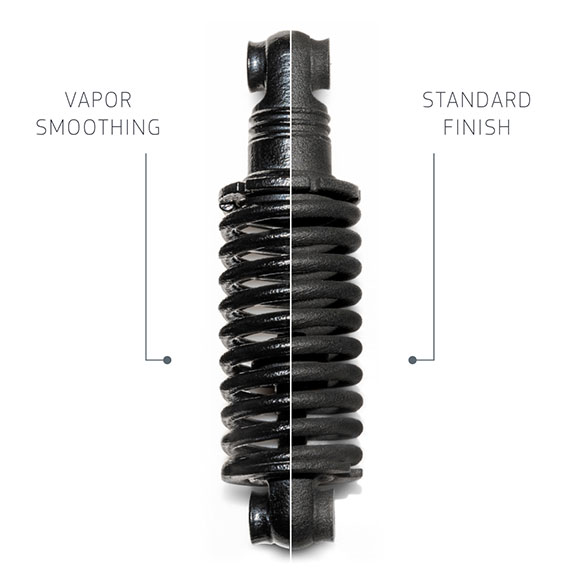