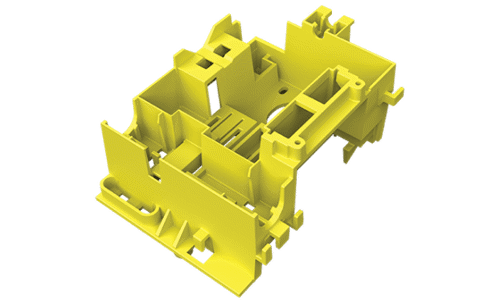
Custom Plastic Injection Molding
Get custom plastic parts within days. Request an online quote.
Certifications
ISO 9001:2015 | ITAR Registered | Critical to Quality Inspections
Jump to Section
→ Capabilities
→ Materials
→ Surface Finishes
→ Quality Inspections
→ Finishing Options
→ About Plastic Injection Molding
What is Plastic Injection Molding?
Injection molding is a manufacturing process that consists of filling a metal mold cavity with liquid plastic resin, which then cools and forms a plastic part.
It's most often used for the manufacturing plastic parts at scale due to its low material waste and low cost per part. It’s an ideal manufacturing process for industries like medical devices, consumer products, and automotive.
Our plastic injection molding process produces custom prototypes and end-use production parts with lead times as fast as 1 day. We use aluminum molds that offer cost-efficient tooling and accelerated manufacturing cycles, and stock about 200 different thermoplastic resins.
Common applications for plastic injection molding:
- low-volume production
- bridge tooling
- pilot runs
- functional testing and prototyping
It has been very enlightening to us here at HP that we are able to get parts so rapidly out of the actual materials that we're going to use in the final production.
Plastic Molding Capabilities
Our basic guidelines for plastic injection molding include important design considerations to help improve part moldability, enhance cosmetic appearance, and reduce overall production time. View our design guidelines page for more details.
US | Metric | |
SIZE | 18.9 in. x 29.6 in. x 8 in. | 480mm x 751mm x 203mm |
VOLUME | 59 cu. in. | 966,837 cu. mm |
DEPTH | 4 in. from parting line | 101mm from parting line |
Up to 8 in. if parting line can pass through the middle of the part | Up to 203.2mm if the parting line can pass through the middle of the part | |
PROJECTED MOLD AREA | 175 sq. in. | 112,903 sq. mm |
Tolerances: Typically, Protolabs can maintain a machining tolerance of +/- 0.003 in. (0.08mm) with an included resin tolerance that can be greater than but no less than +/- 0.002 in./in. (0.002mm/mm).

Grab a Design Cube
Want to learn more about injection molding? Sign up to receive a Design Cube. This physical aid demonstrates how to properly design features commonly found on molded parts.
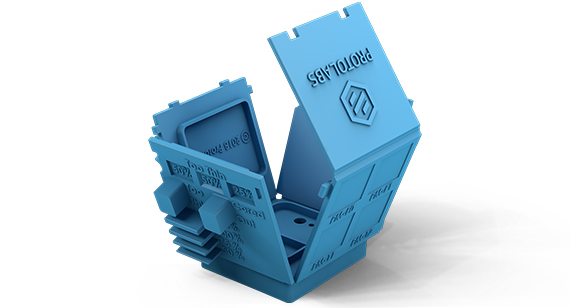
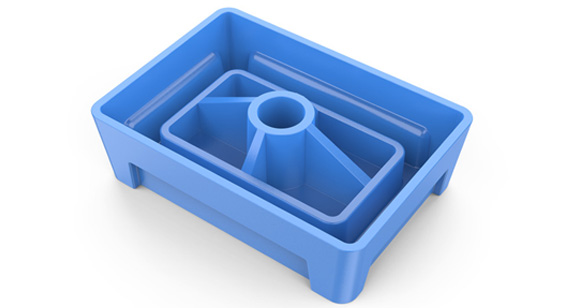
Thermoplastic Materials
We have wide selection of more than 100 thermoplastic and thermoset materials. And if you're looking for alternative material options, check out our guide to resin substitutes for ABS, PC, PP, and other commonly molded plastics.
- ABS
- ABS/PC
- Acetal
- Acetal Homopolymer/Delrin
- ETPU
- HDPE
- LCP
- PET
- PETG
- PMMA (Acrylic, Plexiglas)
- Polycarbonate
- Polypropylene
- PPA
- PPE/PS
- PS
- PSU
- TPU
Surface Finish Options
Draft angle requirements will vary by requested finish. Industry standard Mold-Tech finishes are also available.
FINISH | DESCRIPTION |
---|---|
PM-F0 | non-cosmetic, finish to Protolabs' discretion |
PM-F1 | low-cosmetic, most toolmarks removed |
PM-F2 | non-cosmetic, EDM permissible |
SPI-C1 | 600 grit stone, 10-12 Ra |
PM-T1 | SPI-C1 + light bead blast |
PM-T2 | SPI-C1 + medium bead blast |
SPI-B1 | 600 grit paper, 2-3 Ra |
SPI-A2 | grade #2 diamond buff, 1-2 Ra |
Quality Inspections and Finishing Options for Custom Molded Parts
Depending on your application's requirements, you can choose from the following when requesting an injection molding quote.
Quality Inspections available for on-demand manufacturing orders
- Designing for Manufacturability Feedback (DFM)
- Scientific molding process development report
- In-process CMM inspection and machine monitoring
- First article inspection (FAI) and process capability report with GD&T
|
|
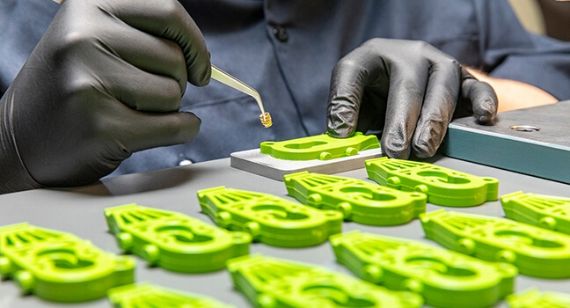
Prototyping or On-demand Manufacturing?
While the molds themselves are similar, part quantities, lifetime maintenance, quality documentation, and pricing vary depending on which service option is chosen. The right one depends on your project needs.

Design for Moldability Toolkit
No one ever said that designing and manufacturing molded parts was easy. Our goal is to get you through it quickly and with quality parts. A good starting point is our Design for Moldability Toolkit.
Check Out the ToolkitHow Does Plastic Injection Molding Work?
The manufacturing process for molded parts is complex. Before your parts are even molded, we're there to help you with comprehensive manufacturability feedback and consultative design services, so you can avoid mold design pitfalls before the resin hits the mold. From there, our production process is documented and optimized using scientific molding so you get high-quality parts consistently and reliably with every production run.
Critical-to-quality (CTQ) dimensions you call out on models let us know what areas are most crucial to the success of your parts. Once the parts start molding, the process and samples are qualified using automated inline CMM technology, generating a detailed FAI and process capability study with no additional lead time.
Our thermoplastic injection molding is a standard process involving an aluminum mold with no heating or cooling lines running through it, which means cycle times are a bit longer. As part of the scientific molding process, our molders independently optimize and monitor fill speed, hold pressure, and hold time, and periodically inspect part quality and cosmetics. During the molding process, we use an automated inline CMM to ensure dimensional accuracy, as well as generate a detailed process capability study and FAI report.
Resin pellets are loaded into a barrel where they will eventually be melted, compressed, and injected into the mold’s runner system. Hot resin is shot into the mold cavity through the gates and the part is molded. Ejector pins facilitate removal of the part from the mold where it falls into a loading bin. When the run is complete, parts (or the initial sample run) are boxed and shipped shortly thereafter.