When you’re looking for a supplier for prototyping or production, your choice can make the difference between a project’s success or failure. You’ll need to be certain the option you pick fits your needs exactly – whether you want someone to handle your project as a one-off, or hope to develop a long-term relationship. In this week’s post we’re going to take a look at the different types of manufacturing source and the pros and cons of working with each type
Service broker
Brokers exist to help companies that can’t, or don’t want to, spend time and resources evaluating suppliers. A good service broker will match their clients with an appropriate manufacturer.
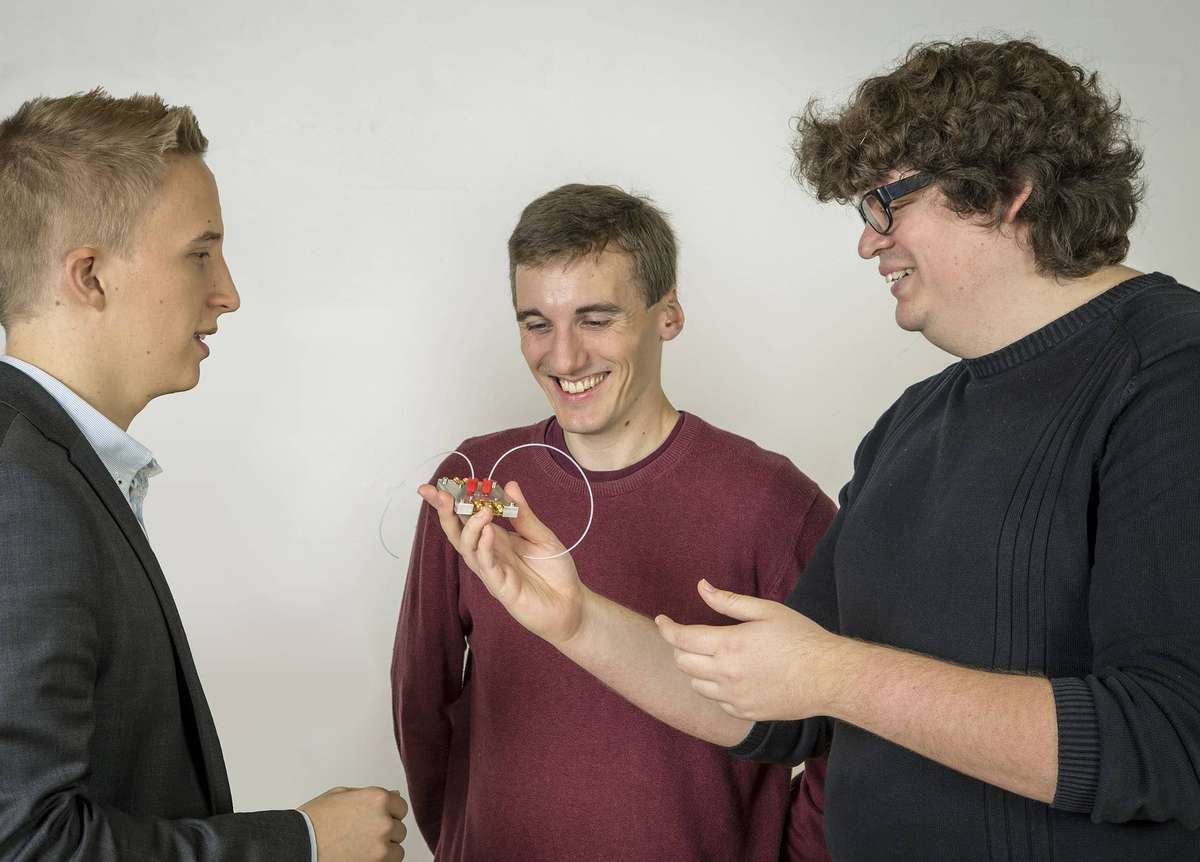
Pros | Cons |
---|---|
|
|
Independent machine shop
This type of supplier is often quite small and specialised. Some machine shops can be skilled at working with difficult or unusual materials, but could be more expensive for basic aluminium parts. They can be among the best in their specific area of expertise, but perhaps not as proficient in others.
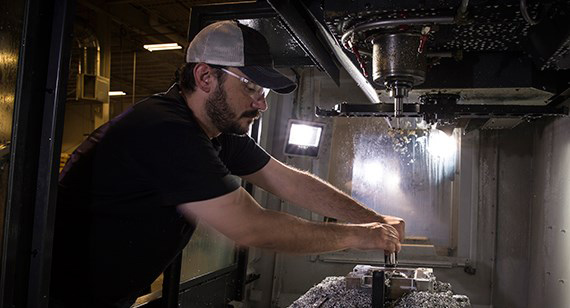
Pros | Cons |
---|---|
|
|
High-volume production house
High-volume production houses tend to focus on injection moulding and CNC machining, and keep unit prices down by manufacturing thousands or millions of parts. They excel at saving seconds and pennies through high-speed repetition, but upfront engineering expenses can be high.
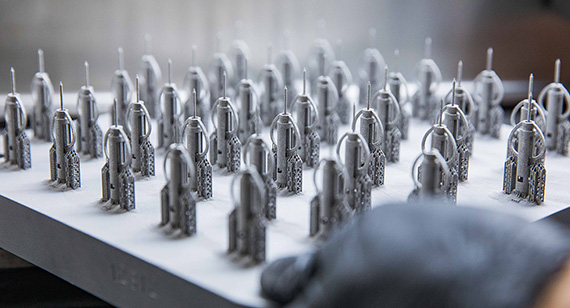
Pros | Cons |
---|---|
|
|
In-house production
This option offers convenience, but capabilities will be limited to the equipment a company has invested in. For this option, upfront capital investment is required, plus purchase and storage of materials, and recruitment of skilled staff to operate the machines.
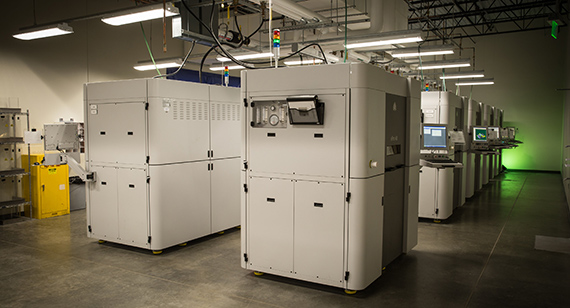
Pros | Cons |
---|---|
|
|
On-demand manufacturing service
Usually with a wide range of technologies, on-demand manufacturing services offer a suite of processes, such as injection moulding, CNC machining and 3D printing. This type of service provider also often provides automated online quoting, and design-for-manufacturability analysis. And they have the resources and expertise to work with you throughout the design and development process, and the entire life of your product. Most importantly, the good ones understand how to make the most appropriate use of their processes and materials to benefit your specific part or product.
Pros | Cons |
---|---|
|
|
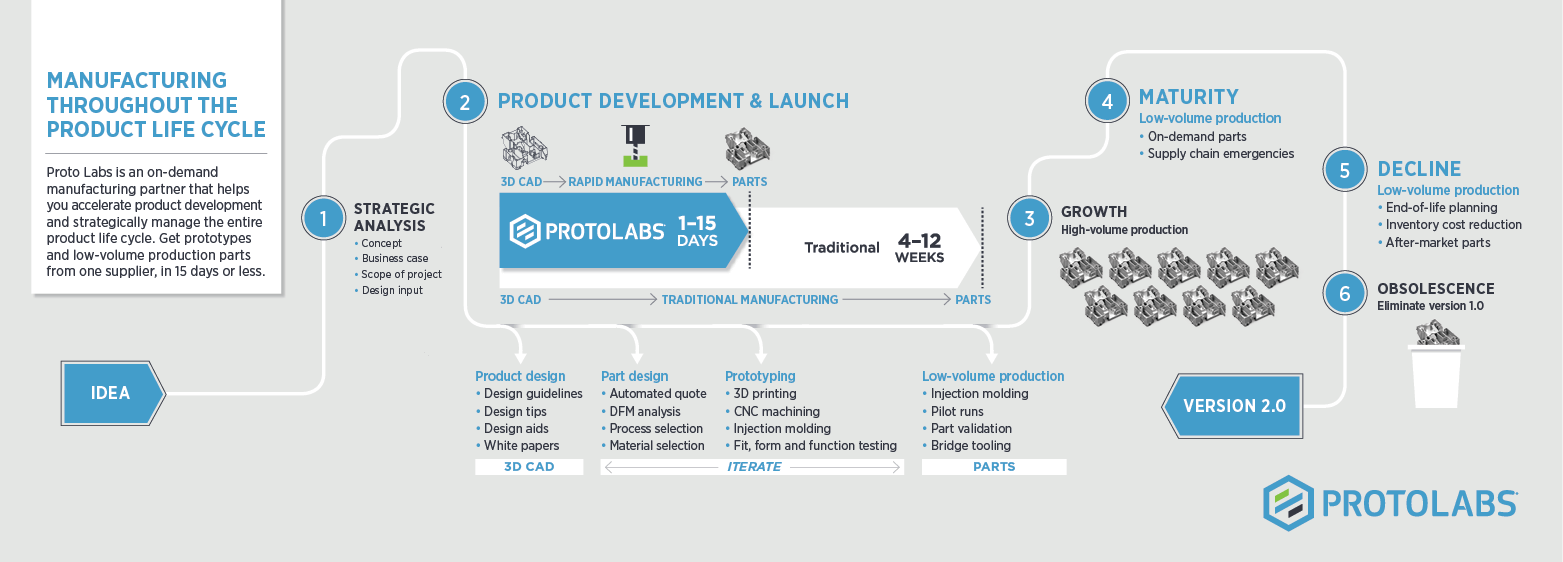