
Digital Manufacturing for Early Prototyping to Final Production
We are the fastest and most comprehensive manufacturer in the world. Get an online quote for parts within days or talk with a production expert for solutions across your entire product life cycle.
Certifications ISO 9001:2015 | AS9100D | ITAR Registered
Talk with Our Team
Hello! We just need a few bits of information, and then a manufacturing expert will reach out to you directly to see how we can partner on a future production project.
Thank you! We've received your request and a member of our team will reach out shortly.
Our Manufacturing Services
Injection Moulding
Get affordable, high-quality moulded parts and bridge tooling within days. With our free mouldability consultation, the design and moulding process is rapidly accelerated to save you time and money.
- Low-volume moulding up to 100,000+ parts with volume pricing available—no MOQ required
- 100+ plastic, elastomeric, and silicone rubber materials
- Automated CMM for fast, in-house quality documentation
- Moulds from £995
CNC Machining
Leverage the same speed, precision, and reliability in machining that you’re accustomed to at Protolabs but unlock advanced machining capabilities like tighter tolerances and volume pricing through our manufacturing network.
- Machined parts in as fast as 1 day with optional plating and anodising in as fast as 6 days
- Cost-efficient machined parts at higher volumes
- Tolerances down to ±0.020mm through our digital network
3D Printing
Want quality parts and additive expertise at a single 3D printing source? Choose from seven different additive manufacturing technologies for cost-effective prototyping and highly precise, repeatable production parts.
- Additive technologies include metal 3D printing, SLA, SLS and more
- 30 plastic and metal materials in a range of finishes
- 25 years of additive manufacturing expertise
What’s New at Protolabs?
MANUFACTURE LIKE A PRO™
We're your single resource from prototyping to production. Partner with Protolabs to accelerate product development and get to market faster than ever before. When you're ready for production, get complete program management with a team of manufacturing experts who will help optimise your project around cost, quantity, and quality.
How to Work With Us
Upload a CAD File
To start, simply select a manufacturing process and upload a 3D CAD file.
Get Quote with DFM
Within a few hours we'll send you design for manufacturability (DFM) analysis and real-time pricing.
Manufacturing Begins
Once you review your quote and place your order, we'll start the manufacturing process. We also offer finishing options.
Parts are Shipped!
Our digital manufacturing process allows us to produce parts in as fast as 1 day.

Design and Engineering Support
We offer both automated and live manufacturing support. With every quote, you get free interactive manufacturability (DFM) analysis to quickly improve part design, but if you have additional questions, applications engineers are always available to talk through your project at +44 (0) 1952 683047 or customerservice@protolabs.co.uk.
Schedule a Free Design ReviewDigital Manufacturing Across Your Product Life Cycle
Full Product Life CycleWhether you need prototype parts in one day of full-service production, you can partner with us across your entire product life cycle for speed, quality, and cost-efficiency in every project. |
Rapid PrototypingTake advantage of DFM feedback in our instant quotes to make adjustments to part design before any actual manufacturing begins, then navigate quickly through prototyping with ease. |
On-Going ProductionYou’ll find complete program management at Protolabs with a team of manufacturing experts who will help optimize your project around cost, quantity, and quality. |
Short-Term ProductionTap into our production capabilities for short-term needs like jigs, fixtures, and industrial components, or managing inventory and financial costs towards the end of the product life cycle. |
Major Industries Served
We work with more than 90% of Fortune 100 companies from our target industries.
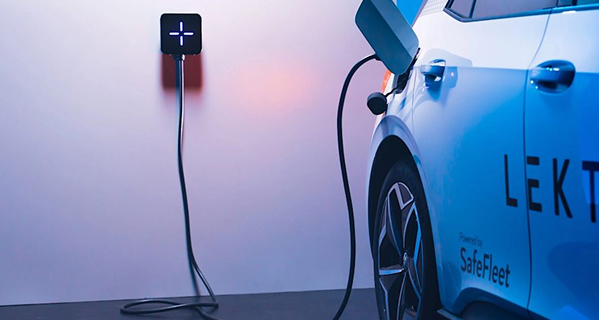
AutomotiveRapid prototyping and ramp-up production for traditional, electric, and autonomous vehicles |
Learn More |
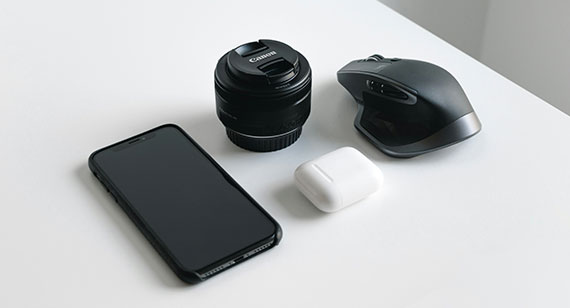
Consumer ElectronicsFunctional prototyping and on-demand production of consumer and computer electronics parts |
Learn More |
Manufacturing Resources
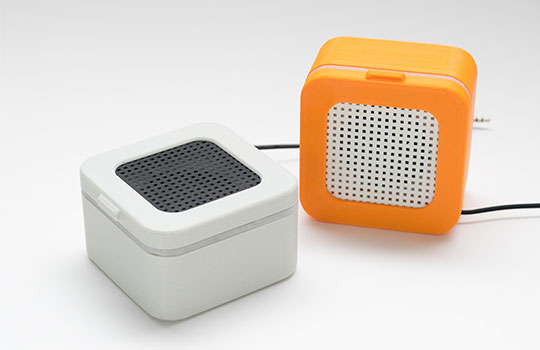
Selecting a Rapid Prototyping Process
Compare the advantages and disadvantages of common rapid prototyping processes in order to make the best decision for your project.
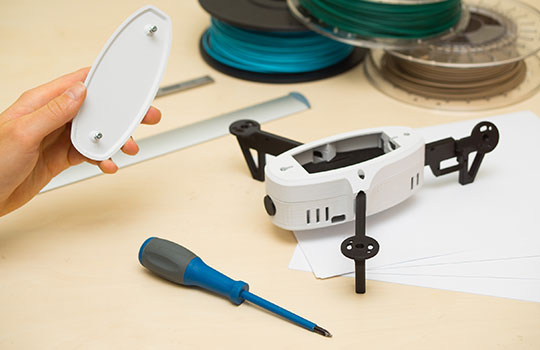
Design for Mouldability Toolkit
Get in-depth design advice to optimise your plastic parts for injection moulding. Designing with mouldability in mind can accelerate production time and reduce production costs.
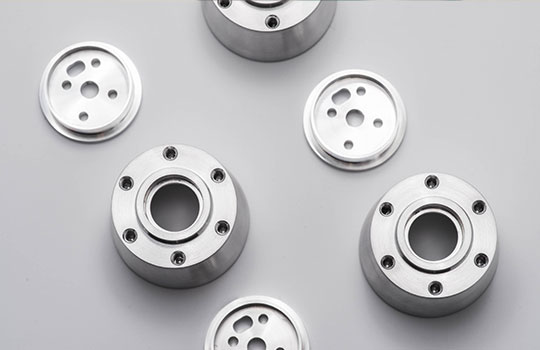
How to Reduce CNC Machining Costs
Incorporate a few design and material considerations to reduce your machining expenses.