Selective Laser Sintering (SLS) What is the best material for my project?
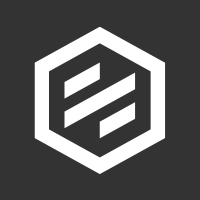
We’re often asked, “What’s the best material for selective laser sintering (SLS)?” Without a little more information, the answer isn’t clear-cut. This is because a number of factors might impact the most suitable material. Continue reading to learn more.
What are the different types of SLS materials?
The number of materials available for the selective laser sintering process is vast, including a large catalogue of thermoplastics, metals, ceramics, composites and speciality materials. The most commonly used SLS material is Polyamide 12 (PA 12), also known as Nylon 12. Polyamide powder can be filled with various additives. This is to improve the mechanical and thermal properties of the SLS part. Examples of filled polyamide materials include PA Carbon filled and PA Glass Filled Nylon.
At Protolabs, we offer six materials for SLS through our factories; 5 of them are PA 12 materials, and the other is a TPU.

How does budget impact choice of material for SLS?
Here are a few examples of how budget can impact the choice of your SLS material:
- Material cost: This is the primary consideration for a material choice. Some thermoplastics (e.g., Unfilled Nylon) are more affordable than metals or specialised polymers (such as glass-filled nylon). If budgets are tight, you may opt for a more economical material choice that still meets the specification requirements for the application.
- Prototype vs. Production: Budget constraints for a prototype may differ greatly from budget constraints for a production piece. It may be possible to select less expensive materials for a prototype to keep costs down during the testing phase. Meanwhile, production part performance and higher-cost materials may be justified.
- Material Properties: Different materials mean different properties. Budget may play a big part in deciding whether to go for a material with superior properties and a higher cost or a material with adequate properties at a lower price point.
- Specialised applications: Do you need a biocompatible or flame-resistant material? These types of specialised materials can often be more expensive.
- Post-processing: Some materials may require additional steps, such as surface finishes or heat treatments, which can add to the overall cost. Budget constraints may influence the selection of materials that require minimal post-processing.
How do product development stages impact material selection for SLS?
During the product design phase, materials with rapid prototyping capabilities, such as low-cost thermoplastics like nylon, are often preferred. These materials allow for quick iteration and testing of design concepts without incurring high material costs.
Once you reach the prototyping and validation phase, your material should closely resemble the properties of the final production material to ensure accurate performance testing.
At the optimisation phase, materials are often chosen based on specific properties such as strength, weight, and manufacturability. Advanced materials may also be selected at this stage, such as filled polyamides for enhanced properties or speciality polymers for specific performance characteristics.
At pre-production, the materials used will mimic the properties of the production-grade materials as closely as possible. High-performance polymers might be selected to validate performance under real-world conditions and assess their suitability for mass production.
Finally, at the production stage, materials are selected with properties optimised for the parts application, considering cost-effectiveness, scalability, and performance consistency.
How does product purpose impact the choice of SLS material?
Materials |
Characteristics |
PA 12 Smooth White |
Impact Resistance Temperature Resistance Durability |
PA 12 Vapour Smooth White |
|
PA 12 Carbon Filled Smooth Black |
High Temperature Resistance Electric Conductivity Lightweight |
PA 12 Flex Pure Black |
Excellent Flexibility Impact Resistance Strength & Resistance |
TPU-88A |
Flexibility Tear and Abrasion Resistance Durability |
Product purpose plays a critical role in determining the most suitable material. From the table above, you can see the materials we offer at Protolabs and their key characteristics. If your part needs to be durable whilst having reasonably good temperature resistance, you might select PA 12 smooth white. If it is key for your part to have high thermal resistance, you may go for a filled material instead, such as PA-12 Glass Filled Smooth White. If High UV resistance were on your list of key characteristics, you’d probably want to consider TPU-88A.
It’s not just properties that may influence your decision here. Aesthetics and surface finish can be key requirements in certain industries or for some parts. If you require a part with a smooth finish, a vapour-smooth material would be ideal. A custom paint might be selected if aesthetic appeal or colour is important.
What are the latest materials available for SLS?
New materials are being added and investigated all the time. Compared with the original Nylon, materials such as glass-filled nylon are somewhat newcomers, only arriving on the scene at the turn of the millennium. A big push in all sectors at the moment is sustainability, and that’s no different for SLS. Research is being done into recycled materials such as recycled polypropylene. 3D systems also showcased the SLS 300 powder recycling stations (PRS) at the end of 2023, which work with the SLS 300 to recycle and mix unused material with fresh material. Biodegradable polymers were introduced into the industry as early as the 2010s when high-performance polymers such as PEEK, PEI and PPS were also introduced.
So, what’s the best SLS material for your part? No one can answer that for you; hopefully, some of the points above have helped direct you. For further information, please don’t hesitate to reach out and speak to one of our technical experts.