
How to Achieve Design for High Speed CNC Milling
Follow these design guidelines to achieve an optimal design for fast and economical production of your CNC milled parts
This page is dedicated to helping you understand the key principles of part design for CNC milling. Utilise our virtual CNC Design Cube as a resource to help interpret the core principles and key features that drive efficient part design, as well as to gain valuable insights into the techniques and strategies that can transform the success of your project. Continue reading to learn more
HOLES
- No maximum, but some holes will be flat bottomed.
Avoid deep drill holes. - Minimum hole diameter 0.5mm.
FINISHES
- As a machined finish, all sharp edges removed.
- Bead blast, fine matt finish
(will be applied to whole component) - Options to anodise or laser mark.
SLOTS
- Maximise radii to allow for bigger diameter tools with deeper reach. Maximum slot depth 50 mm.
- Minimum slot width 0.75mm. Using 1.25mm will allow for greater depth and speed.
These features require side-setup. Designing for top/ bottom access will minimise cost (mini cube).
THREADS
- HELICOIL® - In metric and UN (in a range of common sizes).
- Counter bore - DfA and extrended thread depth to more than Ø x 2.5.
- Unified (inch) coarse and fine threads: General rule depth = Ø x 2.5.
- Metric threads: M1.6 to M12. Selection of metric fine. General rule depth = Ø x 2.5.
Cube sides are 90mm, and manufactured in aluminium 6082.
DESIGN FOR FUNCTION
These features show off capabilities, but take longer to machine.
CONTOURED SURFACES
- Ball milling provides 5-axis like contoured surfaces using 3-axis machining.
- Note the lofted radius - tool access from above
COMPLEX DETAILING
- Text is possible but using smaller cutters takes longer. Using rounded text and adding radii will help.
POCKETS
- The smaller the radius, the smaller the tool, and so shallower the pocket.
- Either add a radius (and chamfer the insert)
- Or relieve (extend the cutter diameter beyond the corner) 2 options shown.
WALLS, BOSSES AND RAISED FEATURES
- A minimum wall thickness of 0.5mm is possible. Keep material stiffness in mind - the thicker the better, particularly for plastic/ ductile metals.
- Try and avoid raised/ embossed features (the whole of this face is removed to create it).
- Consider an insert (stud or dowel) as milling a hole or thread is more cost effective than a raised feature.
From CAD to Component... In Hours
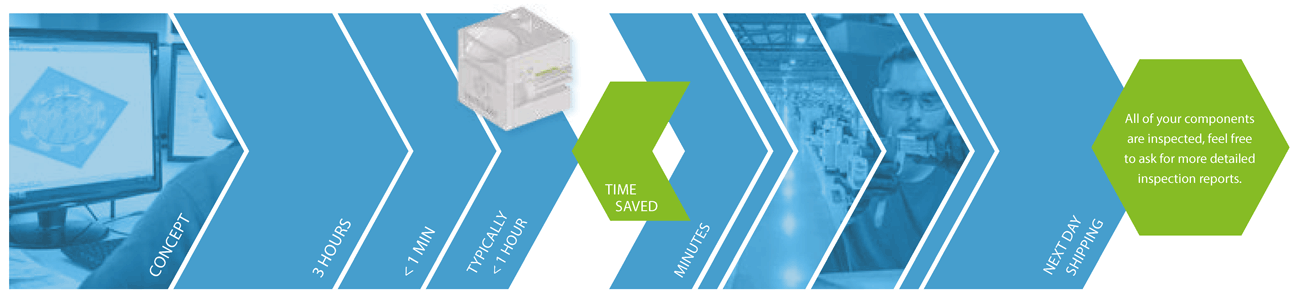
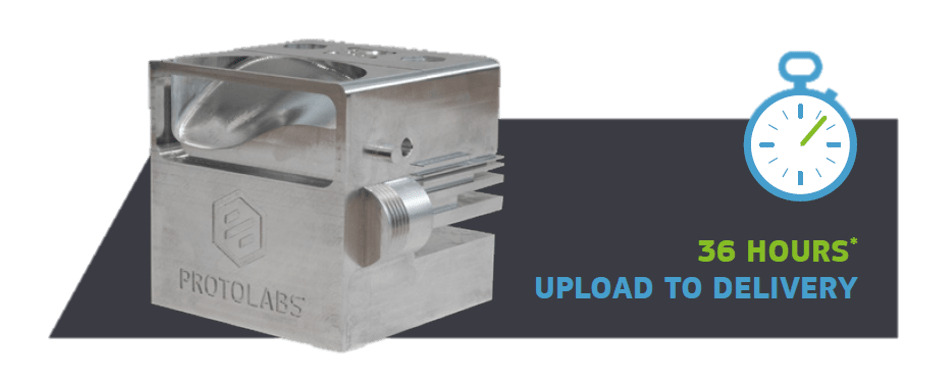
* Expedite and shipping fees apply, our standard and typical manufacturing time is 3 working days + 1 day shipping. Times are applicable to this sample in aluminium, Bigger/more complex parts and different materials may take longer. Upload now for price and delivery time.