Talk with Our Production Team
Hello! We just need a few bits of information then a manufacturing expert will reach out to you directly to see we how can partner on a future production project.
Thank you! We've received your request and a member of our team will reach out shortly.
Aerospace Component Manufacturing for Prototyping and Production
Reduce risk, get to launch faster, and streamline your supply chain with rapid prototyping and on-demand production.
Certification + Compliance
ISO 9001:2015 | AS9100D | ITAR
How Do Aerospace and Defense Companies Use Protolabs?
Rapid PrototypingTake advantage of design for manufacturability (DFM) feedback in our instant quotes to make adjustments to part design before any aerospace manufacturing begins, then navigate quickly through early- and late-stage prototyping with ease. |
End-to-end Product DevelopmentMove quickly through iterative development with our rapid prototyping and low-volume production services. When ready, work with our team of applications engineers to meet all of your production needs for end-use aerospace applications. |
Jigs and FixturesGet durable, production-grade jigs and fixtures, and other aids within days so development and workflow remain forward moving.
|
Quality Certifications and TraceabilityTake advantage of our AS9100- and ISO9001-certified machining and 3D printing processes for high-requirement parts. Aluminum traceability is also available on projects that qualify. |
Aerospace MaterialsChoose from high-temperature plastics, medical-grade silicone rubber, and 3D-printed micro-resolution and microfluidic parts, among hundreds of other plastic, metal, and elastomeric materials. |
We are the fastest and most comprehensive digital manufacturer in the industry with more than 25 years of experience developing products for innovative aerospace companies around the world. | 100% of Fortune 500 Aerospace Companies Served |
750 Million Parts Manufactured |
300,000 Customers Served |
Full Production Support Team
We have a team of manufacturing experts working behind the scenes to fulfill your production order—we manage the entire process and keep you updated along the way. |
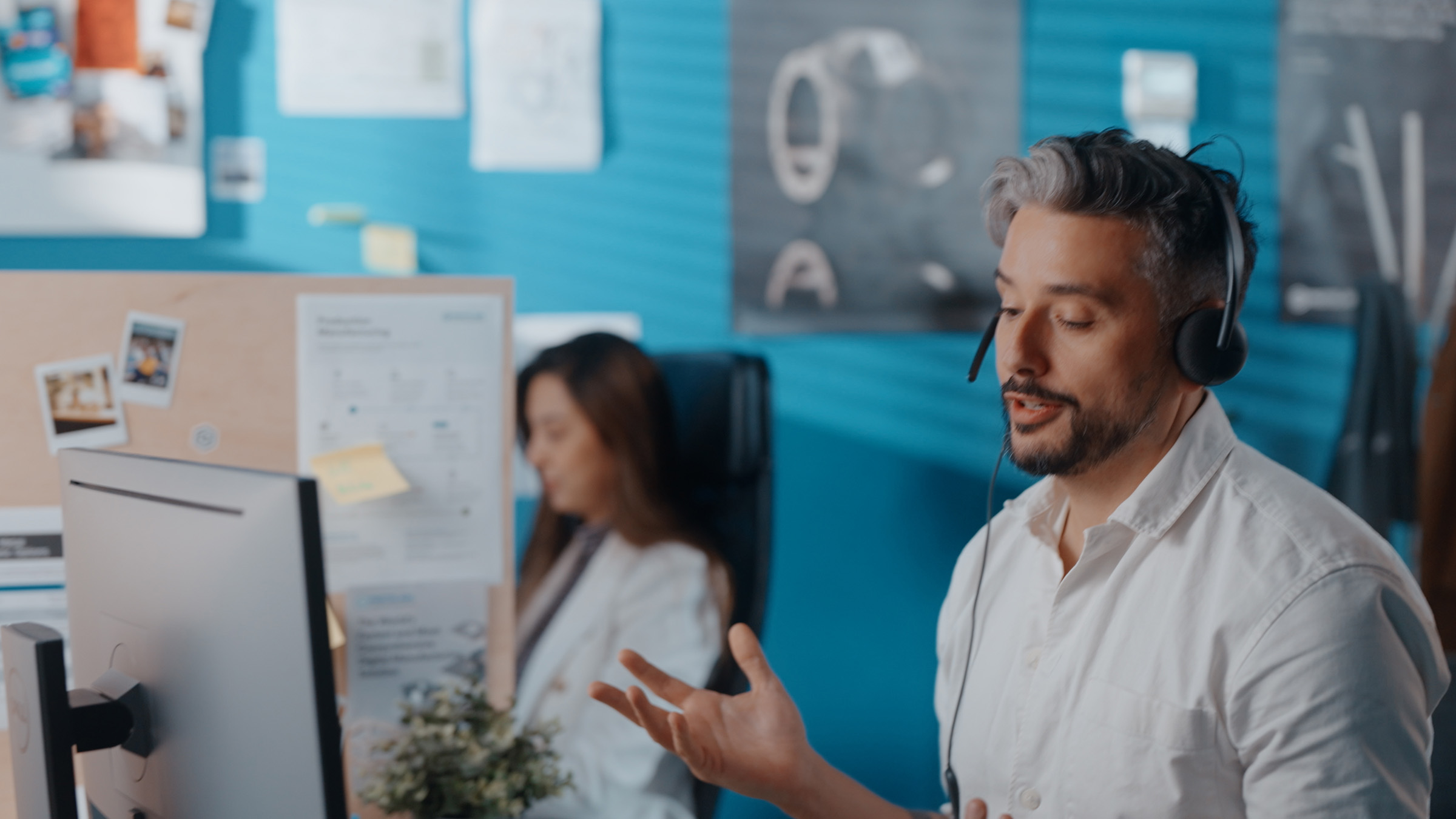
Account ManagerA dedicated account manager provides support, including assistance with platform and file uploads. |
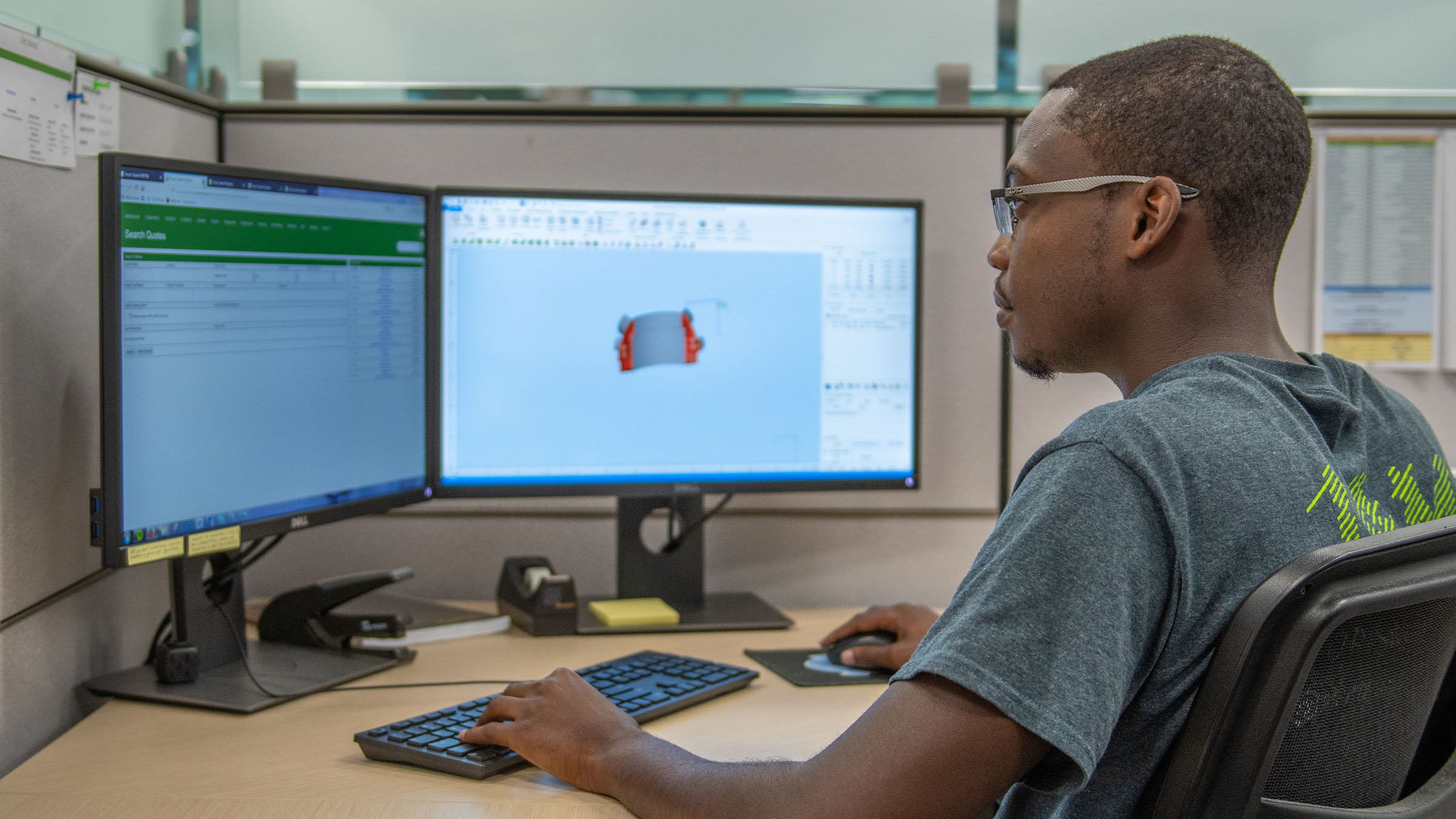
Application EngineersExpert CAD solutions and cost-reduction strategies tailored by in-house applications engineers to optimize your designs. |
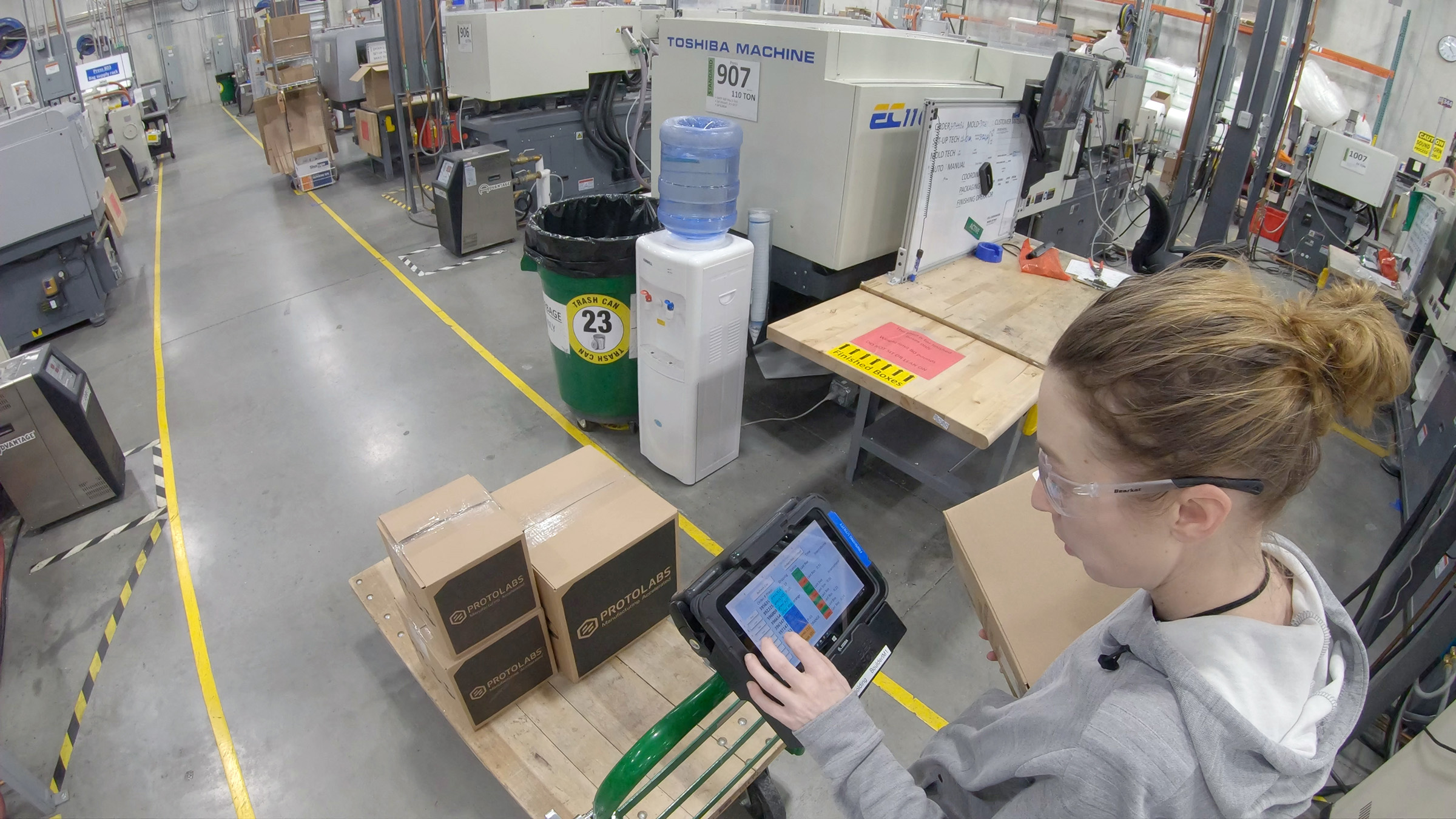
Logistics |
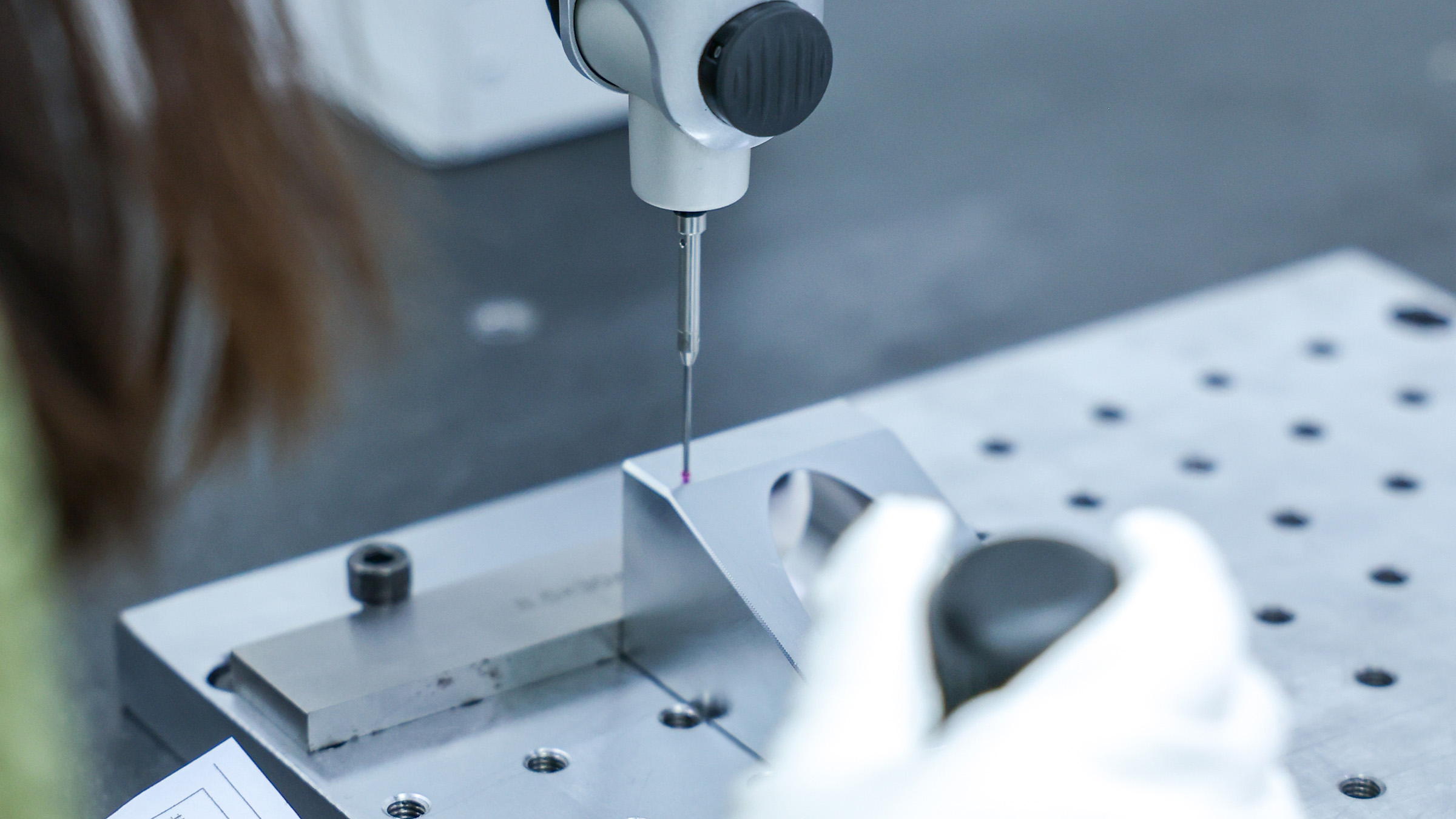
Quality Control |
Manufacturing Services for Aerospace Products
CNC Machining
Leverage the same speed, precision, and reliability in machining that you’re accustomed to at Protolabs but unlock advanced machining capabilities like tighter tolerances and volume pricing through our manufacturing network.
- Machined parts in as fast as 1 day with optional plating and anodizing in as fast as 6 days
- Cost-efficient machined parts at higher volumes
- Tolerances down to ±0.001 in. (0.020 mm) through our digital network, with tighter tolerances available upon request
3D Printing
Want quality parts and additive expertise at a single 3D printing source? Choose from seven different additive manufacturing technologies for cost-effective prototyping and highly precise, repeatable production parts.
- Additive technologies include metal 3D printing, SLA, SLS, FDM, and more
- 30 plastic and metal materials in a range of finishes
- 25 years of additive manufacturing expertise
Injection Moulding
Get affordable, high-quality moulded parts and bridge tooling within days. With our free moldability consultation, the design and moulding process is rapidly accelerated to save you time and money.
- Low-volume moulding up to 100,000+ parts with volume pricing available—no MOQ required
- 100+ plastic, elastomeric, and silicone rubber materials
- Automated CMM for fast, in-house quality documentation
NASA Generative Design x Quick-Turn ManufacturingThe government organization that has been making the impossible world of space travel possible for more than six decades, NASA, is now exploring a more earthbound frontier. It has become a testing ground for generative design—using artificial intelligence (AI) to create novel CAD designs. Watch how quick-turn manufacturing enabled highly iterative design for the aerospace giant. |

Quality Measures for the Aerospace Industry
Our industry-standard procedures and certifications guarantee quality and regulatory compliance.
CMM inspection report | First article inspection (FAI) |
Material test reports and certificates | PPAP quality management system |
REACH and RoHS Certificates of Conformance (CoC) | Full dimensional inspections |
Materials for Aerospace Components
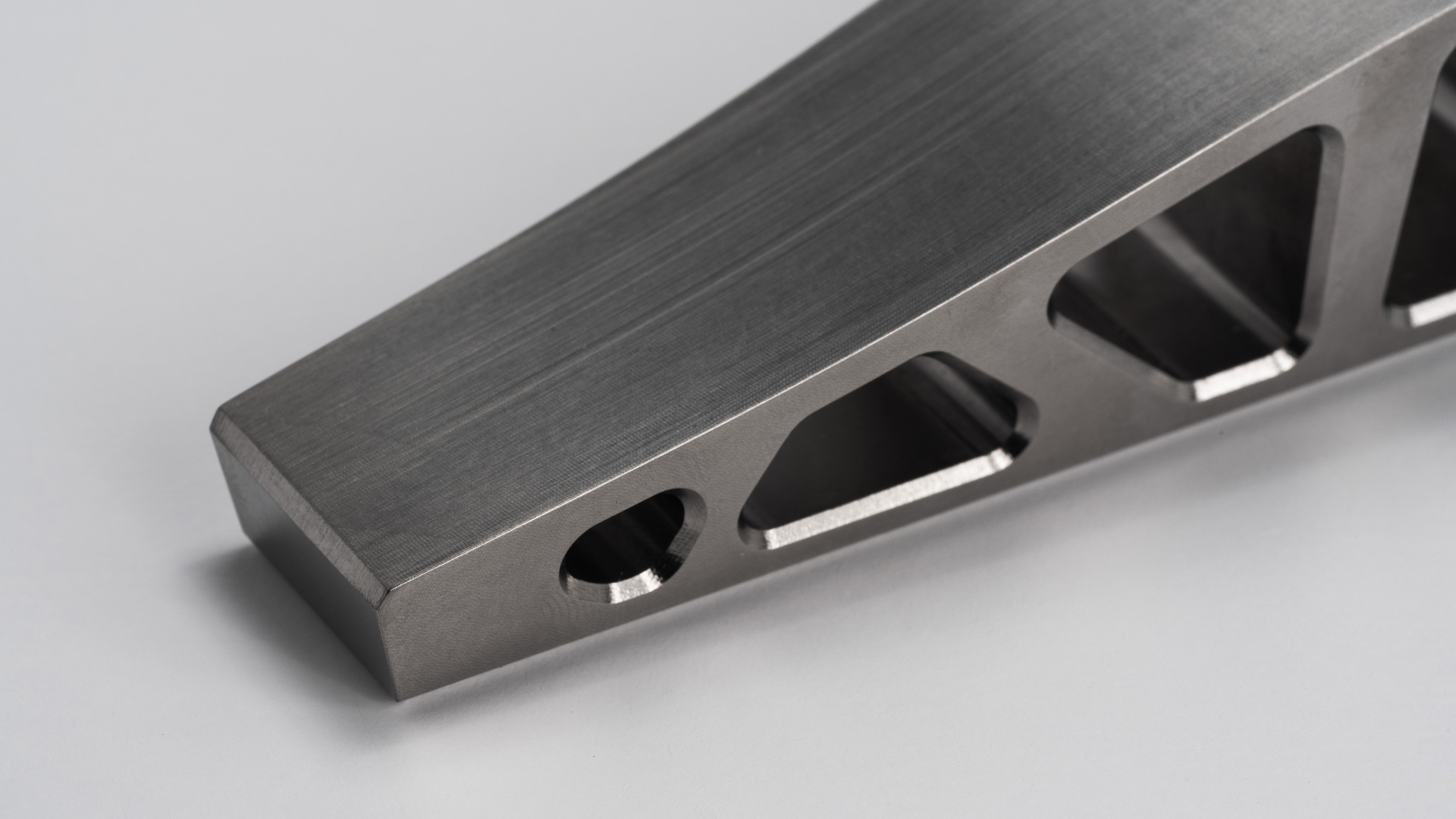
TitaniumAvailable through machining and metal 3d printing services, this lightweight and strong material offers excellent corrosion and temperature resistance. |
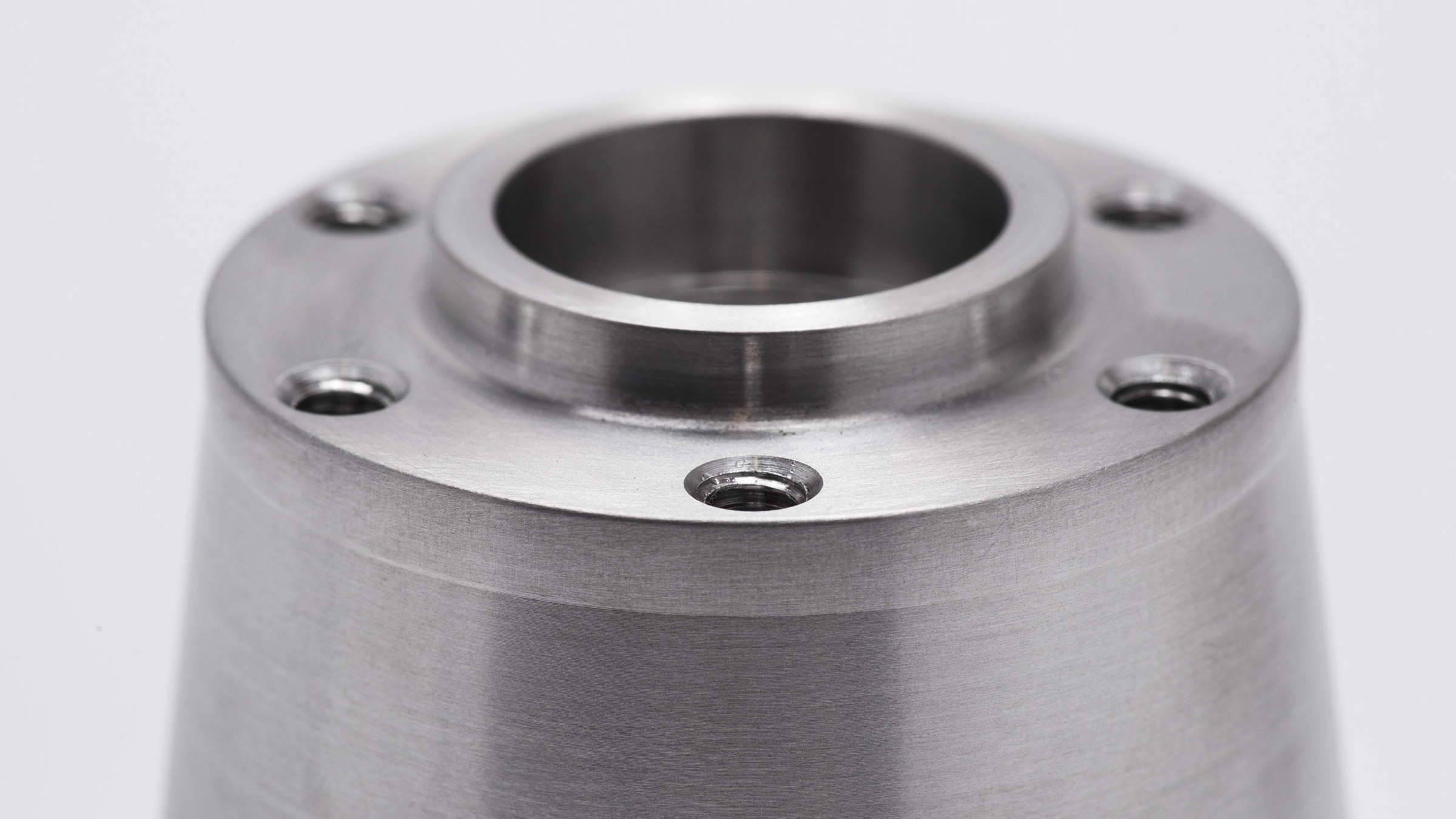
AluminumThis metal’s high strength-to-weight ratio makes it a good candidate for housing and brackets that must support high loading. Aluminum is available for both machined and 3D-printed parts. |
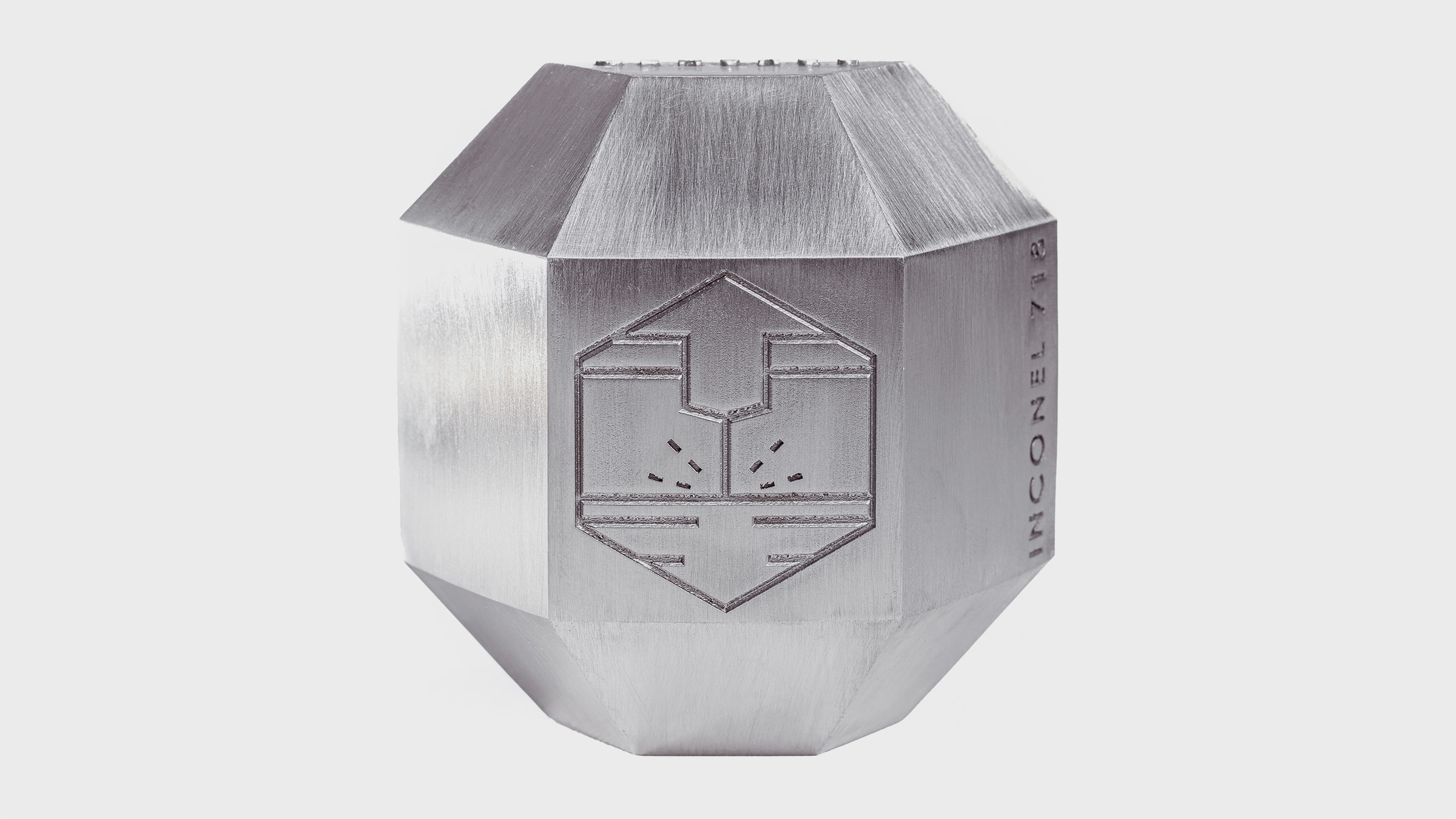
InconelThis 3D-printed metal is a nickel chromium superalloy ideal for rocket engine components and other applications that require high-temperature resistance. |
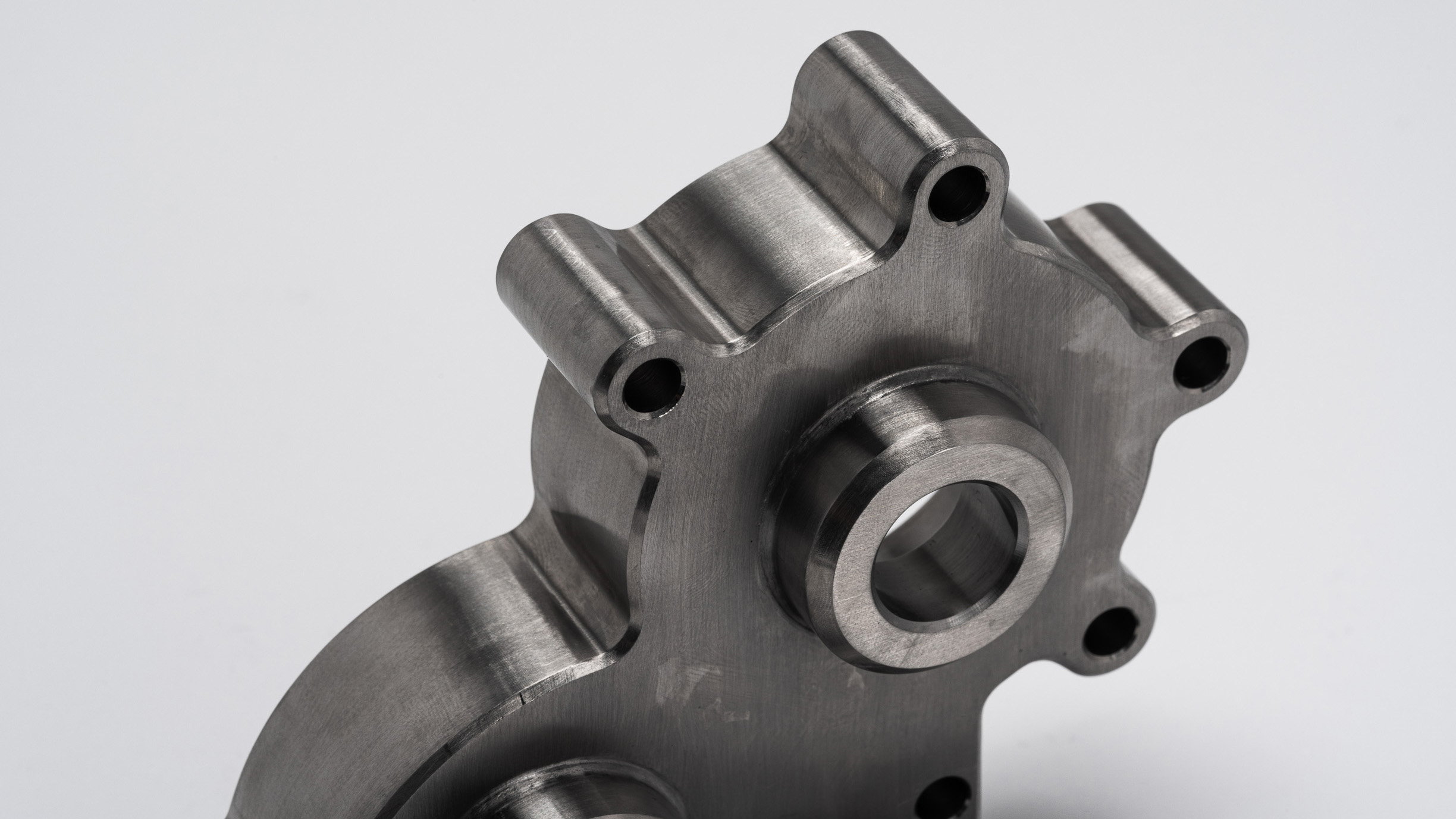
Stainless SteelSS 17-4 PH is widely used in the aerospace industry due to its high strength, good corrosion resistance, and good mechanical properties at temperatures up to 600°F. |
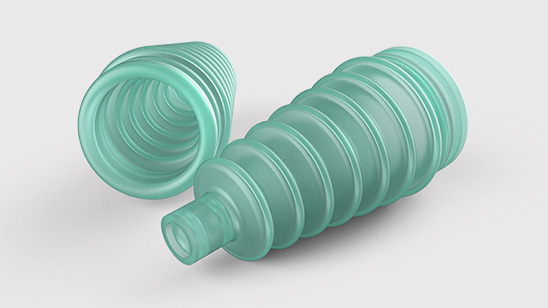
Liquid Silicone RubberOur elastic fluorosilicone material is specifically geared towards fuel and oil resistance while our optical silicone rubber is a great PC/PMMA alternative. |
Common Aerospace Applications
We have several capabilities within our manufacturing services catered to the aerospace industry. Here are a few applications we frequently see.
|
|
Resources for Aerospace Manufacturing