
IG Technology
Protolabs helps IG Technology create device that could revolutionise Dvt treatment
Creator: IG Technology
Product: Various parts for Portable Intermittent Pneumatic Compression (IPC) device
Service: Plastic Injection Moulding
Over his 25 years developing medical devices, engineer Ivan Green has spent a great deal of time in the hospital environment. It was during his visits to the wards that Ivan noticed the excessive length of time patients were spending confined to their beds and learned about the dangers of deep vein thrombosis (DVT).
This insight was the impetus for ‘Legacy’, a ground-breaking Portable Intermittent Pneumatic Compression (IPC) device, created in collaboration with world-leading digital manufacturer Protolabs. The Legacy device is a revolutionary way to silently deliver cyclic compression to the calf, mimicking ambulation and preventing venous stasis; it’s a unique, game changing solution that be used in both the hospital and home.
Ivan explains the central motivating factor at the beginning of the project: “When we started looking into this, I was shocked. DVT is the number one preventable cause of death in hospitals. In terms of mortality, it kills the equivalent of breast cancer, MRSA and road accidents put together. And you just don’t hear about it.”
Last year in the UK, 15,000 people died from DVT, and in the U.S. the figure stands at 100,000. However, it’s not just Western developed countries that see these high numbers – India, for example, has a similar prevalence of DVT. And these figures are expected to double across Asia by 2040, primarily due to an aging population but also due to more sedentary lifestyles and unhealthy diets as these populations increasingly adopt Western habits.
In terms of financial cost, according to government figures, preventing and treating DVT is costing the UK health service nearly £1 billion a year. And in the U.S., it’s between $7-10 billion.
Ivan continues: “Whilst visiting hospitals, I saw first-hand what they are offering patients at the moment in terms of DVT prophylaxis. The current devices restrict the movement of patients and are uncomfortable, leading to poor compliance and hence higher risks and costs.”

At A Glance |
---|
IG Technology needed moulded parts for ‘Legacy’, their revolutionary portable Intermittent Pneumatic Compression (IPC) device designed to prevent deep vein thrombosis (DVT). Solution IG Technology made use of Protolabs’ proprietary automated manufacturability analysis tool, as well as discussing potential moulding issues with the Protolabs expert team. They collaborated through a number of iterations and mould modifications before moving into plastic injection moulding production.
Six different parts were produced - two for the outer casing, two for the manifold, and one part each for the port and holster. Samples were shipped quickly for assessment, before tool modifications and final parts were put into production. Approx. 6,000 parts were created altogether and dispatched with Protolabs’ customary rapid speed. |
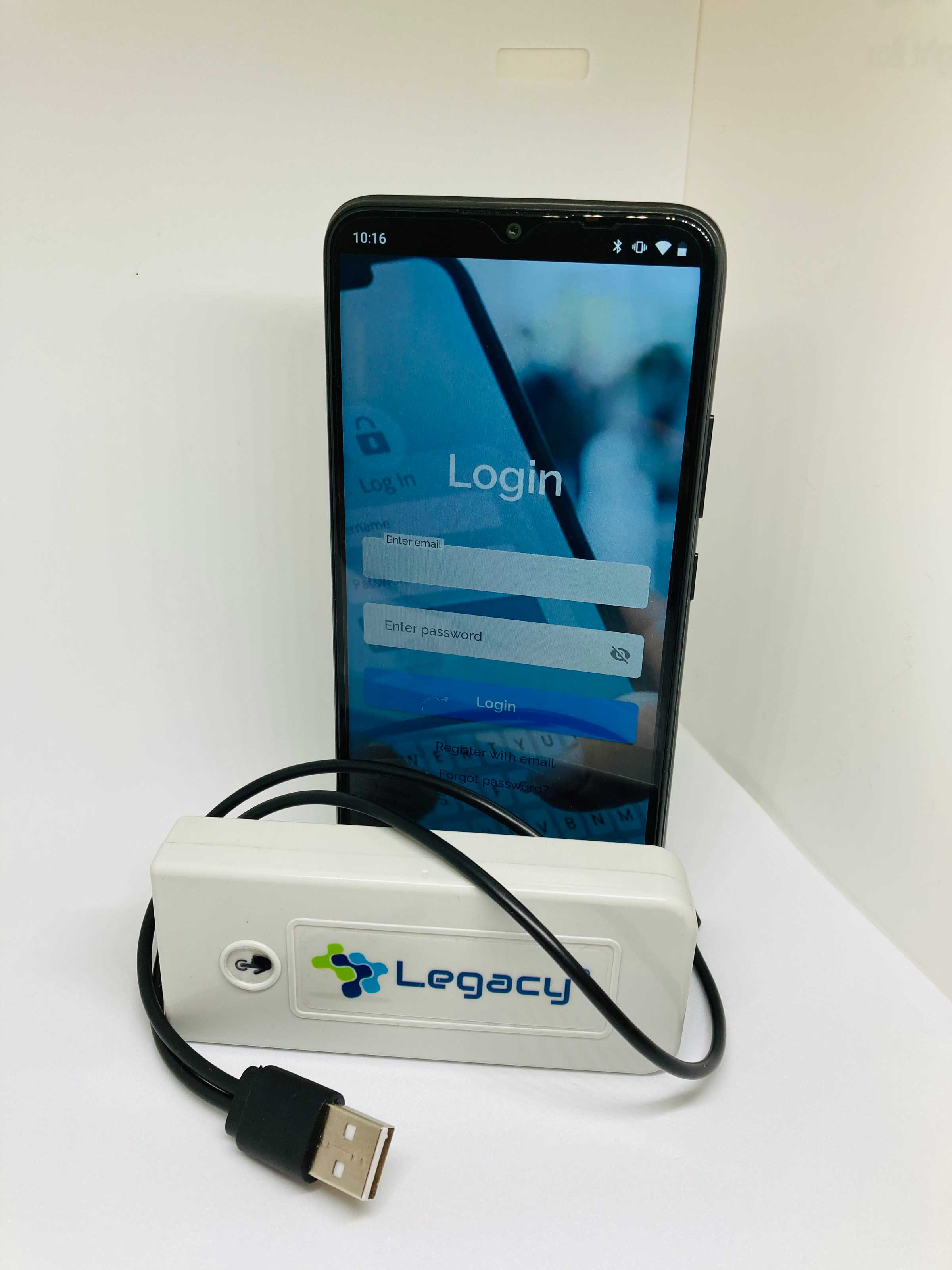
The advantage of Legacy
Current IPC devices are large and cumbersome, noisy and difficult to use. If the patient needs to use the bathroom, due to the size of typical current devices and the way they function, the patient is reliant on the nursing team’s support with removal, including the disconnection of the tubes then reconnection afterwards. In addition to this, every movement of the patient in bed is restricted and poor skin breathability under the device often leads to bed sores.
Moreover, care should not stop at the hospital door as 60% of DVTs occur following discharge from the hospital. However, no current IPC device allows for prophylaxis in the community. Excitingly, this is where the innovative portability and versatility of the Legacy device comes into play, enabling the continuum of care following surgery.
There is also a financial and environmental burden for the health provider with the cost of frequently replacing the heavy single-use plastic components of the current devices – a necessity that is neither cheap nor environmentally friendly.
Resolving all these issues is the reason that Legacy is a revolutionary treatment device for DVT, both from a medical and financial perspective. Being portable and easy to use, Legacy not only increases patient acceptance and participation, leading to vastly improved patient outcome, it also lightens the burden on nursing staff and offers an attractive financial and more environmentally friendly solution to health providers the world over.
Legacy is essentially used to help prevent blood clots in the deep veins of the legs. The device uses cuffs that fill with air to squeeze the soleus and gastrocnemius muscles, simulating the effects of walking. And it works with the Legacy IPC mobile application, which offers a range of benefits for users such as monitoring and tracking therapy sessions, and overall better management and patient adherence to treatment plans.
Moving Legacy into the part production phase
The production of the Legacy device hardware began at the Protolabs website, with the upload of CAD models, the proprietary automated manufacturability analysis tool and the engineering support at the end of the phone.
As Ivan describes: “My experience with the Protolabs website is very good. I like the way you can simply upload CADs, see them, and then the system does the automated analysis explaining what you need to change. But if there is anything you need to discuss, the team are always available to talk. During the project, if the Protolabs team felt there was something tricky or difficult with the mould tooling, they would either drop me an email and then, if necessary, we’d get on the phone, and they’d advise a solution to whatever issue had come up. I really couldn’t fault them.”
Protolabs’ Account Manager, Zuzanna Probert, describes the interaction with IG Technology: “After IG Technology uploaded their parts to the Protolabs website, as their Account Manager I reviewed the automated feedback on the quote and reached out to them directly. We wanted to clarify that they understood the feedback and offer support from myself and one of our Application Engineers. This was to ensure we could mould the part to their requirements and eliminate any roadblocks could prevent effective moulding.
“We discussed mould life options we have on offer and assisted with choosing the best one for the budget and product life.”
Protolabs’ mould life options are based around two injection moulding services: one optimised for prototyping (up to approx. 2,000 parts) and the other for low-volume production of end-use parts (more than approx. 2,000 parts). There are other differences between the two services, such as maintenance, mould storage and ownership, and the level of quality documentation applied to the parts. All these service variations lead to price-per-part options, which are clear in the Protolabs e-commerce platform but can also be discussed with the Protolabs Account Manager. The service option discussed and chosen for Legacy was based on all these things, with a focus on product life, budget and of course, the volume required.

In terms of material selection and finish, this is something the team at Protolabs frequently provide advice and information on. But in the case of IG Technology, as a customer with familiarity of the options available, those discussions were not needed. Zuzanna continues: “As a long-standing customer, I’d previously sent IG Technology a material sample plaque that shows surface finish options, so we did not need to offer this particular assistance on this occasion.”
On the shop floor, following the initial tooling there were some tool modifications required, such as changing the size of one of the parts, but between Protolabs and IG Technology the team worked closely to make the adaptations quickly so that more parts could be pressed with the revised mould tool.
Ivan continues: “Our process was to get parts in the hand quickly for early testing and feedback. Any changes could then easily be made by creating a new tool or simply modify the existing tool. I think there were about three iterations with that.”
The parts moulded for Legacy included two for the outer casing, two for the manifold, and one part each for the port and holster. One thousand parts were created for each of the six different parts. TPU (thermoplastic polyurethane) ‘Pearlthene 11T85 Natural’ was the selected material, and in terms of delivery, the parts were shipped in Protolabs’ customary rapid time.
Ivan Green – CEO, IG Technology

Multi-cavity tooling
Future production of Legacy is to match increasing demand for the product, as Ivan explains: “Excitingly, with recent FDA approval we are just starting a study with the Mayo Clinic, a leading hospital in the U.S. that’s widely regarded as the very best in the world.
“Given the advantages of the Legacy system over current compression systems, it is expected that quantities will increase in the near term and that multi-cavity tooling could be the way forward. We’ve begun a conversation with Protolabs on that.”
Moving from single- to multi-cavity moulds can boost production and reduce part costs, which would serve as a clear advantage considering IG Technology’s future expectations and plans. It’s important to recognise that parts that behave perfectly well in a single-cavity mould may not do so in a multi-cavity mould, at least not without first making some adjustments or tweaks to the part, the process, or even the material. These are considerations and discussions being had between Protolabs and IG Technology at the moment, but the future is looking very bright for Legacy and the partnership will continue to flourish!
Ivan Green – CEO, IG Technology