
3D Printing for New Industries
Your masterclass in product design and development
Protolabs’ Insight video series
Our Insight video series will help you master digital manufacturing.
Every Friday we’ll post a new video – each one giving you a deeper Insight into how to design better parts. We’ll cover specific topics such as choosing the right 3D printing material, optimising your design for CNC machining, surface finishes for moulded parts, and much more besides.
So join us and don’t miss out.
Insight: 3D Printing in New Industries
Transcript
Hello and welcome to this week’s Insight.
Now, if you’ve been watching these videos for a while you’ll know that most of the time we like to talk about novel bits of technology, making the most of your materials, interesting and efficient processes… that kind of thing.
Today, though, we’re going to talk about something a little bit different. We’re going to take a look at some of the more unexpected places that 3D printing tech has been cropping up, and maybe have a bit of a ponder about why that might be.
Now, what do I mean by unexpected places?
Well, when we usually think of 3D printing our minds turn to intricate medical devices, to hi-tech automotive parts, or to rapidly prototyping products that are going to go into mass production. However, over the past few years we’ve seen the technology used in plenty of other sectors – and projects – too.
Just to grab some off our own list of case studies, we’ve had PepsiCo ask us to make incredibly detailed replicas of the Black Panther mask that could be attached to drink cans as part of a promotional campaign.
We’ve seen the beauty company IEVA reach out to us to use 3D printing to create their beautiful Twin-C smart jewellery.
We’ve even used our tech to help make a range of printed clothing that made its way onto the red carpet at the Met Gala. I don’t know about you, but I think that’s an amazing example of just how far the technology has come over the years.
It’s easy to dismiss these as side-shows or diversions, but in each and every case the customer has decided to go with 3D printing technology for many of the same reasons that our more conventional, more industrially minded clients have.
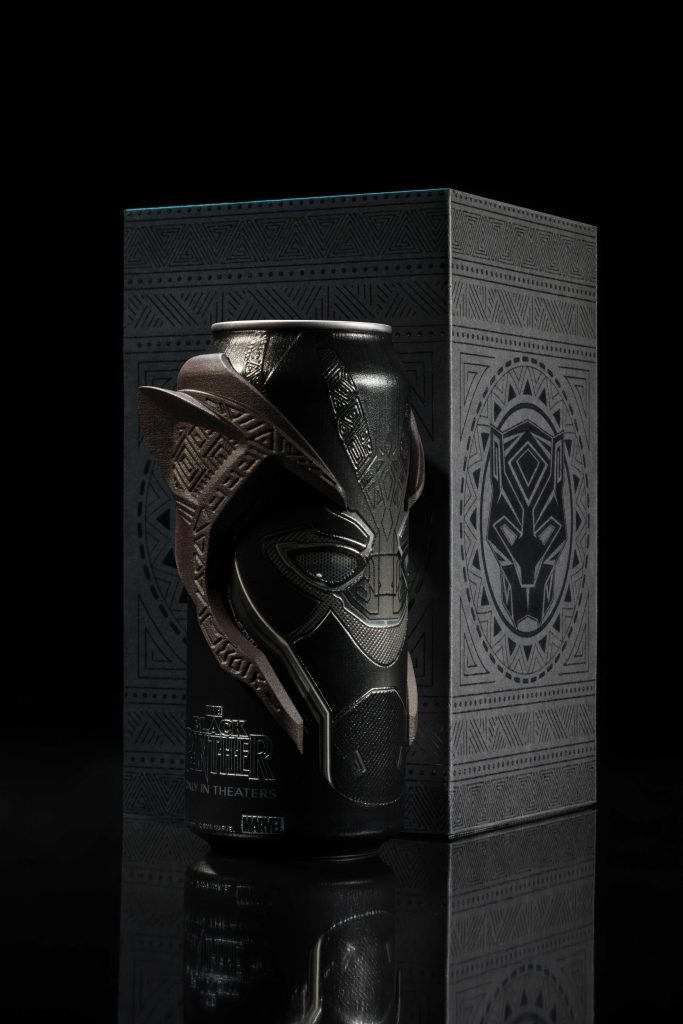
Take the Black Panther mask, for example.
Here, PepsiCo had a pretty definite list of requirements. They wanted the masks to be incredibly detailed and high-quality, they wanted to be able to control the design, and they wanted to produce them in relatively small numbers – in the end, only about 250 units in total. Each of these are requirements that 3D printing can absolutely nail.
They needed to make sure that all the tiny details were correct – this was simple when you are able to ensure that features are correct down to the micrometre.
They needed to make it easy to modify the design – again, making changes is simple when you just need to tweak a few numbers in your CAD design. No need to make new moulds or fiddle about with machining.
As mentioned, they also needed low volumes. Perfect. Again, one of the big advantages of 3D printing is that you don’t need to invest in moulds or machining – your cost per unit doesn’t really change all that much whether you’re making 250 masks or 25,000 of them.
Another big plus was that the exact process PepsiCo ended up using – multi jet fusion – produces a wonderful finish. Which is something especially useful in a product that will hopefully end up as a collector’s item.
Actually, the quality of the finish was also a big tick-mark on the IVEA smart jewellery too. Obviously, appearance is rather important when it comes to items you’re going to have on your wrist, or hanging from your bag, all day. On top of this, when they were making the initial prototypes, another of 3DP’s big advantages came into play – its speed.
With no need to machine, you can get the first designs there and into the hands of your testers very quickly. Apparently, it only took three days for the prototypes to be ready – not bad considering all the tech that had to be jammed into them!
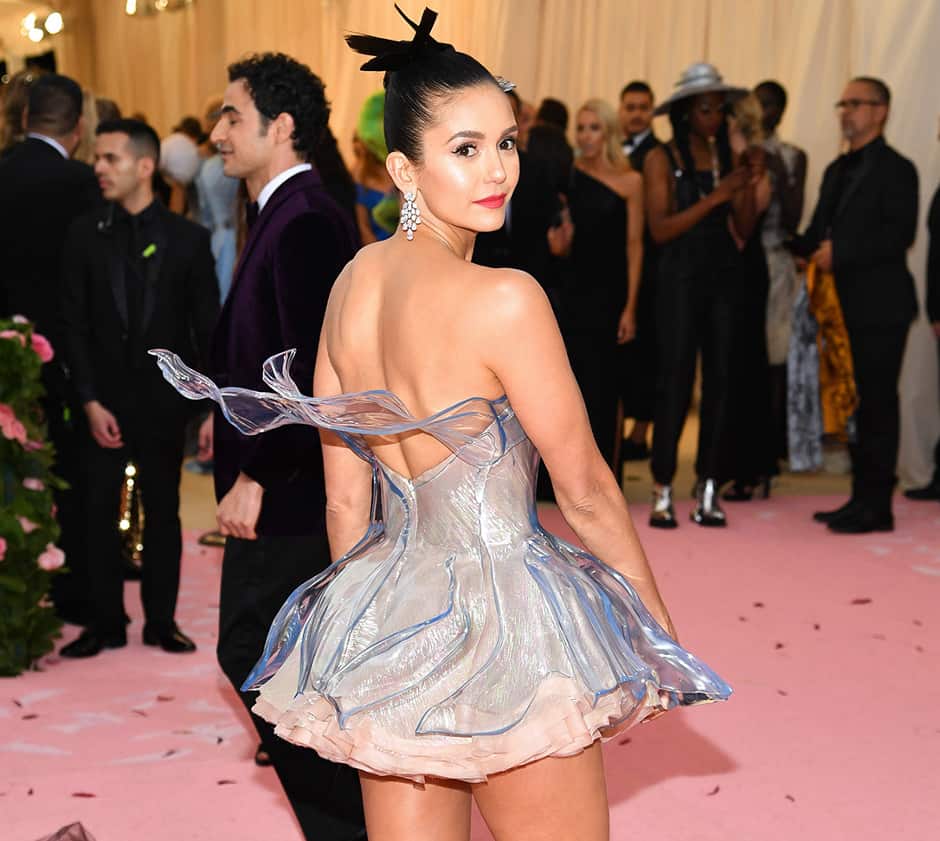
Finally, the dress. Or, at least, the dress’ bustier. Why on earth would you want to make a fashion item with 3D printed materials?
Well, one of the big draws was the fact that it allowed the designers to ignore the limitations you have in traditional manufacturing – things like whether you can get tools in to cut a particular shape, or whether it can support its own weight mid-build. With 3D printing all of that can be handled pretty easily. It allows you to bump up the complexity of your designs without having to worry about the nitty-gritty of how you’re going to make it, which means you can let your imagination run wild with the designs – something that the fashion industry seems to appreciate.
And there you have it. A handful of reasons why so many industries outside of traditional manufacturing are taking the time to get to grips with 3D printing.
That’s it for this week. I look forward to seeing you again next Friday.
With special thanks to Natalie Constable.