
Impression 3D de pièces nylon avec charnières intégrées
Comment la fabrication additive peut vous aider à créer rapidement un prototype et à améliorer vos conceptions de charnières intégrées.
Les prototypes imprimés en 3D grâce au frittage laser sélectif (SLS) ou à la Multi Jet Fusion (MJF) comprennent souvent des charnières intégrées qui seront plus tard moulées par injection. Le moulage par injection permet de créer des charnières intégrées extrêmement fines, mais présentant une longue durée de vie. Il est également possible de créer des charnières intégrées robustes et fonctionnelles avec le SLS ou la MJF, mais en étant très attentif au stade de la conception. Cela peut même demander que la charnière soit conçue d’une certaine manière pour l’étape de prototypage, puis retransformée avant de passer au moulage par injection.
Le premier principe à garder en tête en concevant une charnière intégrée, c’est qu’elle doit rester la partie la plus faible de la pièce. Si elle avait à peu près la même épaisseur que le reste, la pièce se déformerait au moment d’utiliser la charnière.
POURQUOI PRODUIRE PAR IMPRESSION 3D DES PIÈCES AVEC DES CHARNIÈRES INTÉGRÉES ? |
---|
|
La force nécessaire pour faire fléchir une charnière est proportionnelle non seulement à son épaisseur, mais aussi à sa largeur. Pensez éventuellement à transformer votre charnière en plusieurs charnières plus petites. Par exemple, la transformation d’une charnière de 20 mm en trois charnières de 5 mm en laissant 2,5 mm entre chaque charnière non seulement prolongera la durée de vie de la pièce (si une charnière est défaillante, la pièce reste utilisable), mais pourra également améliorer les performances. Car une force moindre sera nécessaire pour faire fonctionner la charnière, avec une contrainte inférieure sur les crochets et sur toute la pièce dans son ensemble.
Notez qu’une charnière intégrée jouera d’une certaine manière le rôle d’un ressort, et exercera une tension constante sur les crochets ou autre fixation maintenant la pièce en position fermée. Ces fixations doivent être assez robustes pour s’opposer à la force du ressort de la charnière.

Matières pour les charnières intégrées imprimées en 3D
Lors de l’impression en 3D de pièces avec charnières intégrées, la matière nylon la plus adaptée est le PA 12 disponible pour la MJF. Les charnières peuvent également être constituées de matières SLS PA 11 Black, et, en second lieu PA 12 White, mais elles auront certainement une durée de vie plus courte, et un soin plus grand devra être apporté à la conception ainsi qu’à la zone environnante de la pièce.
Nous recommandons d’éviter le PA 12 à 40 % de charge fibres de verre pour les pièces à charnières intégrées, car ce nylon est trop rigide, et risque de casser plutôt que de fléchir. Et même si techniquement vous pouvez fabriquer une charnière intégrée dans un élastomère de type TPU, cette matière sera rarement adaptée au reste de la pièce.
Comment calculer la longueur d’une charnière intégrée
Les charnières intégrées sont soumises à une contrainte constante en utilisation. Une partie subit une compression, tandis que l’autre est sous tension. Pour cette raison, les charnières intégrées doivent être aussi fines que possible. Cela signifie que l’épaisseur de la charnière doit être la dimension minimale permise par la technologie (0,508 mm pour la MJF et 0,762 mm pour le SLS). C’est une des raisons pour lesquelles la MJF est la technologie de fabrication additive préférable pour les charnières intégrées.
La formule L = πR est la relation idéale entre la longueur de la charnière et sa position. Cela permet à la charnière de former un demi-cercle en position fermée. Le respect de cette formule permettra de répartir régulièrement la contrainte le long de la charnière et de la minimiser aux points de fixation. L’image suivante démontre la relation entre la longueur de la charnière et sa position.
Dans la figure 1 :
- A – Indique le centre de l’épaisseur de la charnière intégrée.
- B – Indique les surfaces d’accouplement de la pièce.
- R – Indique la distance entre la surface d’accouplement (B), vers le bas le long de la pièce, et l’axe central de la charnière intégrée (A). Cela sera alors le rayon de courbure de la charnière sous flexion.
- L – Indique la longueur de la charnière.
- Noir - indique la section de la pièce/charnière en position non fléchie ou ouverte.
- Jaune - indique la section de la pièce/charnière en position fléchie ou fermée.
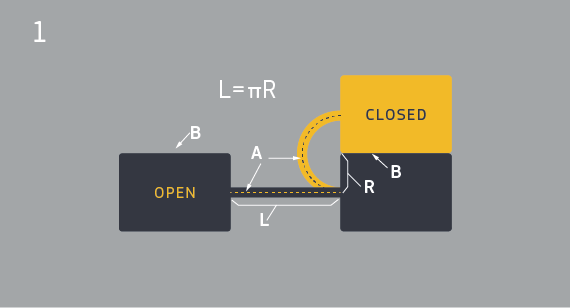
Si la charnière est trop courte, ou si la distance R le long de la paroi vers le point de fixation est trop longue (L < πR), la charnière sera sous tension en position fermée avec la contrainte concentrée aux points de fixation comme le montre la figure 2.1. Si la charnière est trop longue ou si les points de fixation sont trop proches de la surface d’accouplement (L > πR), la contrainte sera concentrée aux points de fixation ainsi qu’au milieu de la charnière. Ceci réduit également la fonctionnalité de la pièce, car la matière en excès de la charnière agira comme un ressort, en écartant les surfaces d’accouplement comme le montre la figure 2.2.
Avec ces concepts en tête, nous avons constaté que la MJF permet de construire des charnières intégrées avec de bons résultats après un recuit jusqu’à la longueur L = 1,27mm en utilisant la formule L = πR. Cela signifie que la distance minimale pour R dans la formule est 0,4064 mm. En raison de la façon dont l’extérieur de la charnière s’étire par rapport à l’axe central, des charnières plus petites (longueur inférieure dans la formule L = πR) exercent une contrainte plus grande sur la matière que des charnières plus grandes.
Ces dernières vont donc exercer une contrainte inférieure sur la matière, et sont censées avoir une durée de vie plus longue. Toutefois, à un certain point la charnière devient trop grande et peut entacher la fonctionnalité et l’esthétique de la pièce.
Une formule pour les charnières intégrées à angle droit et autres
Jusqu’ici, nous n’avons parlé que de charnières ayant une flexion de 180 degrés ; toutefois, tous ces principes peuvent s’appliquer à un autre degré de flexion, par exemple 90°. Donc quelle est la règle générale pour des charnières, quel que soit l’angle ?
Dans le cas d’un angle de 180 degrés (figure 3), il s’agit d’un demi-cercle. Pour 90°, il s’agit d’un quart de cercle. La formule générale pour la longueur d’une charnière intégrée en fonction de son angle de flexion (ou inversement) doit s’appuyer sur la formule précédente : L = πR.
Comme elle donne la bonne réponse pour une flexion de 180°, nous devons considérer la portion de 180° que représente notre flexion. En d’autres termes, nous devons la diviser par 180. La formule s’appliquant à toutes les flexions est donc L = (Flexion°/180)πR.
Il n’y a pas de garantie sur le nombre de cycles de flexion auxquels votre charnière résistera, mais le respect de ces consignes vous aider à maximiser la longévité de votre conception pour l’impression 3D de charnières. Si vous désirez discuter en détail votre concept d’impression 3D, contactez nos ingénieurs d’application au +33 (0)4 56 64 80 50 customerservice@protolabs.fr.
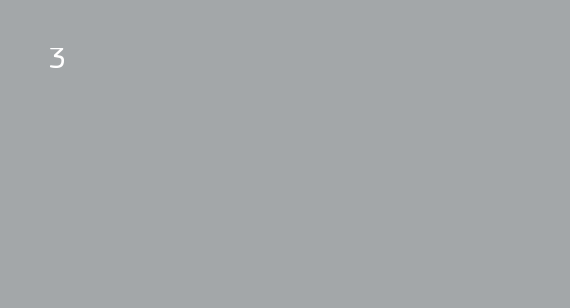