Données, fil numérique et industrie 4.0
Comprendre comment la technologie et les logiciels accompagnent la transformation numérique de l’industrie manufacturière et ses avantages pour les chefs d’entreprise
Dix ans avant la guerre d’indépendance des États-Unis, James Watt, fabricant d’instruments scientifiques à Glasgow, se voit confier la réparation d’une machine à vapeur appelée « machine de Newcomen ». Constatant rapidement qu’elle peut être perfectionnée, il la dote d’un condenseur externe, ce qui améliore considérablement le rendement thermique. La machine à vapeur de Watt s’impose très vite dans l’industrie minière, dans le textile et dans d’autres secteurs. La première révolution industrielle en est à ses balbutiements : les usines sortent de terre, les travailleurs quittent les campagnes pour les villes et la société agraire mondiale se transforme peu à peu en une société mécanisée.
Mais le développement industriel est rapidement freiné par la pénurie d’acier bon marché. À nouveau, c’est une invention simple qui vient changer la donne : l’injection d’air comprimé dans un four rempli de fonte en fusion. L’inventeur de ce procédé, l’Anglais Henry Bessemer, fait breveter son invention en 1856, avant de l’utiliser pour fabriquer de l’acier dans des délais beaucoup plus rapides et à un coût bien moindre que les procédés concurrents. La percée de l’électricité et l’invention du travail à la chaîne par Henry Ford au début des années 1900 viennent nourrir cette deuxième phase de la révolution industrielle, jetant les bases de notre société industrielle moderne.
En 1958, Jack Kilby, nouvel employé de Texas Instruments, travaille pendant la période de fermeture estivale (il n’a pas encore le droit de prendre de congés) sur la miniaturisation des composants électroniques fabriqués par son employeur. Son idée de combiner ces transistors, ces résistances et ces condensateurs sur une même plaque de germanium aboutira aux circuits intégrés qui sont au cœur de tous les appareils, automobiles, ordinateurs, téléphones portables et télévisions que nous utilisons aujourd’hui. Sans eux, les machines-outils à commande numérique (CNC) et les logiciels qui pilotent nos usines de fabrication n’existeraient tout simplement pas. Kilby est bel et bien le père de la troisième révolution industrielle.
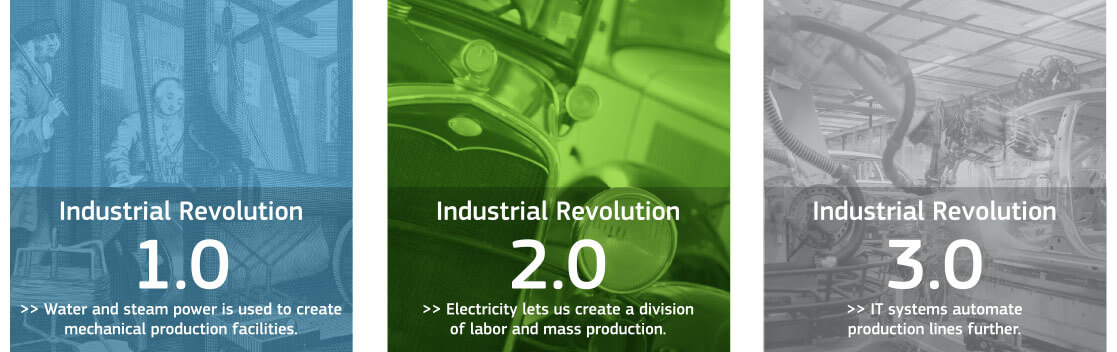

L’industrie 4.0, nouvel horizon
En 2007, l’économiste allemand Klaus Schwab déclare, lors d’une assemblée du Forum économique mondial (dont il est le fondateur), que le monde est en train de vivre une quatrième révolution industrielle1 qui « a le pouvoir d’augmenter les niveaux de revenus mondiaux et d’améliorer la qualité de vie des populations à l’échelle de la planète ». Klaus Schwab fait ici référence à une révolution numérique qui vient bouleverser plusieurs décennies de progrès dans l’électronique et l’informatique, avec des niveaux inédits de stockage de données à bas coût, d’intelligence artificielle, d’informatique mobile, de logiciels en tant que service (SaaS) et d’informatique dans le cloud. Que retrouve-t-on derrière tout cela ? L’internet des objets (IoT), une technologie qui nous fait la promesse de tout intégrer harmonieusement grâce à des dispositifs intelligents qui collecteront des données, prendront des décisions et nous tiendrons informés des problèmes.
Mais dans son discours, Klaus Schwab nous met également en garde contre certains risques. D’une part, le marché du travail sera très probablement affecté par l’évolution des technologies de fabrication. D’autre part, les processus législatifs et les règlementations gouvernementales risquent de ne pas pouvoir emboîter le pas à la croissance exponentielle de l’innovation numérique, créant un décalage entre les entreprises qui adoptent ces technologies et les décideurs politiques qui essaient de les comprendre. Enfin, malgré des effets positifs prévisibles, la révolution qui s’annonce soulève des questions de fond en matière de sécurité nationale et de protection de la vie privée, voire d’armes autonomes et de cyberattaques. Des sujets qui deviendront de plus en plus sensibles à mesure que les machines, les dispositifs et les logiciels commenceront à penser et à agir seuls. Cette révolution, plus que n’importe quelle autre, a le pouvoir de transformer l’industrie ; c’est évident. Mais elle risque aussi de bouleverser notre quotidien.
Ce sont deux contemporains de Klaus Schwab, Siegfried Dais (vice-président du comité de direction de Robert Bosch GmbH) et Henning Kagermann (président de l’académie des sciences et techniques allemande), qui emploient le terme « industrie 4.0 » pour la première fois lors de la foire de Hanovre de 2011. Deux ans plus tard, leur groupe de travail sur l’industrie 4.0 formule des recommandations2 à l’intention du gouvernement allemand, expliquant comment l’industrie manufacturière du pays doit exploiter l’internet des objets et services pour améliorer la compétitivité nationale, et soulignant que la prochaine étape de la révolution industrielle sera le développement d’usines intelligentes utilisant la « mise en réseau directe et universelle d’objets intelligents par internet », en d’autres termes l’internet des objets industriels (IIoT).
Un réseau mondial d’appareils intelligents
Mais qu’est-ce que l’internet des objets, au juste ? Comment s’est-il industrialisé ? Quand les objets sont-ils devenus intelligents ? Voici quelques questions essentielles auxquelles votre ado ou le mordu d’informatique de votre entreprise pourra facilement répondre, du moins en partie. Montre de fitness connectée, voiture autonome, thermostat autoapprenant… notre quotidien est rempli d’objets intelligents qui utilisent des technologies complexes pour nous simplifier la vie.
Alors que certains relèvent du pur gadget commercial, d’autres ont le pouvoir de changer radicalement notre monde. Vu sous un angle national ou régional, l’internet des objets donne des moyens aux gouvernements pour mesurer automatiquement le niveau de pollution, contrôler la qualité de l’eau distribuée, suivre les espèces en voie de disparition et arrêter les braconniers, prévenir le public en cas de séisme, d’incendie ou d’attaque terroriste, surveiller les infrastructures comme les ponts et les routes, et améliorer considérablement les performances des réseaux électriques.
Quelque part entre le consommateur et les villes se trouve le principal moteur de l’économie : le commerce et l’industrie. C’est là que l’internet des objets industriels entre en jeu. Les gains que l’on peut en tirer sont tels que, dans un rapport de 2013, le fournisseur mondial de technologies de mise en réseau Cisco3 prédisait une croissance de 14,4 trillions de dollars en valeur (bénéfices nets) d’ici 2022 pour les entreprises du secteur privé, grâce à des améliorations dans cinq domaines clés : utilisation des actifs, productivité des employés, chaîne logistique, expérience client et innovation. Cisco annonçait également que le nombre de dispositifs mis en réseau atteindrait 21 milliards d’ici 2018, soit une hausse de près de 50 pour cent en à peine cinq ans. Des chiffres impressionnants, tant en matière de gains financiers que de nombre de connexions.
Suivre le fil numérique
L’industrie 4.0 et la révolution de l’IIoT vont bien au-delà des gadgets intelligents et des machines-outils parlantes. Le secteur le plus frappé par ce séisme industriel est probablement la « fabrication numérique », ce moyen relativement nouveau de mettre les données en commun tout au long du cycle de vie des produits afin de limiter les coûts, réduire les délais de fabrication et améliorer la qualité des pièces. Des entreprises comme Siemens et PTC travaillent actuellement à l’élaboration de plates-formes logicielles intégrées réunissant tous les aspects de la fabrication, des premières phases de conception à l’aménagement des usines en passant par les avis clients après livraison. Ce « fil conducteur numérique » permet d’éliminer les silos d’informations qui entravent les échanges de données entre différents logiciels : il intègre chaque composante du processus de fabrication, notamment les outils de modélisation et de visualisation pour CAO 3D, les logiciels d’analyse de faisabilité (DFM), la fabrication assistée par ordinateur (FAO), la productique et les systèmes de collecte de données en usine.
Correctement intégré, ce subtil mélange de solutions logicielles suit toutes les étapes du fil numérique : conception, modèle, prototypage, fabrication, puis reprise de conception. Il suffit d’y ajouter les fils annexes liés au processus de fabrication, comme les achats, la logistique, le stockage ou la comptabilité (qui sont généralement gérés par le système ERP — acronyme anglais désignant un progiciel de gestion intégré), pour compléter le cycle numérique.
Ces logiciels ne se contentent pas d’échanger des données ; ils permettent d’éliminer une grande partie des interventions humaines nécessaires à leur traitement. C’est ce que l’on appelle l’automatisation (rien à voir, ici, avec les robots) ; l’essence, pour ne pas dire la quintessence, de la fabrication numérique. C’est exactement ce que Larry Lukis a en tête lorsqu’il fonde l’entreprise de fabrication rapide Protolabs en 1999. À l’époque, Bill Gates est encore PDG de Microsoft, Google fait ses premiers pas et l’objet qui se rapproche le plus d’un smartphone est le BlackBerry. L’objectif visé par Larry Lukis ? Produire des pièces moulées par injection dans des délais et à des coûts nettement réduits par rapport aux procédés traditionnels.
Il est conscient que le processus devra être largement automatisé, mais pas comme la plupart des gens l’imaginent. Pour lui, la solution passe par la réduction des délais initiaux nécessaires à la complexe élaboration des devis, à la conception des moules et à la programmation des trajectoires d’outils, ceux-là mêmes qui lui empoisonnaient la vie lorsqu’il travaillait chez le fabricant d’imprimantes LaserMaster. Aucun logiciel n’étant alors capable de remplir cette mission, Larry et son équipe développent un logiciel sur mesure, suivi d’un procédé de fabrication propriétaire.
Convergence entre automatisation logicielle et automatisation matérielle
Depuis, Protolabs s’est emparée de cette idée et n’en démord plus. Lorsque l’entreprise commence à développer ses activités d’usinage CN rapide en 2007, elle prend la décision de contourner son système de planification de type ERP au profit d’un système développé en interne parfaitement adapté à la fabrication numérique. Les systèmes intégrés d’établissement de devis et de calcul des trajectoires d’outils partagent automatiquement leurs données avec les ateliers de fabrication, où des écrans vidéo permettent aux ouvriers de visualiser en temps réel les travaux en attente, les paramètres de configuration, les données de production ainsi que des indicateurs de qualité. De même, l’état d’avancement est collecté automatiquement à chaque étape du processus de fabrication, pour être réinjecté dans les systèmes de planification des besoins et de tenue des stocks.
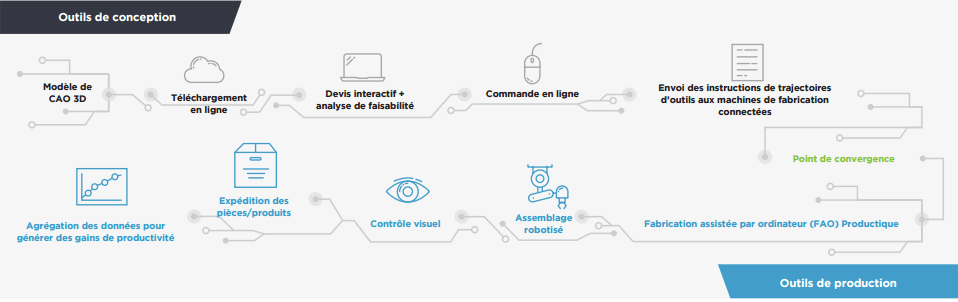
Ce système en circuit fermé nécessite moins d’interventions humaines à l’atelier et davantage devant les ordinateurs. Il permet de réduire les coûts de fabrication, d’augmenter la production et de fournir les informations tant convoitées par la direction pour éclairer ses décisions. Grâce à lui, Protolabs est aujourd’hui une entreprise de 2400 employés (au niveau mondial) et de 430 millions de dollars de chiffre d’affaires, spécialisée dans le moulage, l’usinage et l’impression 3D et capable de livrer des pièces en plastique, en métal et en silicone liquide en seulement quelques jours. Telle est l’essence de la fabrication numérique.
Une stratégie avant-gardiste
Larry Lukis n’est pas seul à « tirer » sur le fil numérique. Siemens PLM définit la fabrication numérique comme une façon de permettre aux ingénieurs de « définir l’intégralité d’un processus de fabrication dans un environnement virtuel en incluant les outils, les chaînes d’assemblage, les postes de travail, l’aménagement des usines, l’ergonomie et les ressources ». Elle permet de produire davantage, d’éliminer les contraintes de faisabilité et de prendre des décisions éclairées plus rapidement. Pour preuve, l’américain Waltonen Engineering, client de Siemens, a fait appel à la fabrication numérique pour réduire ses coûts dimensionnels de près de 50 pour cent. Le fabricant de meubles Swerve s’est quant à lui associé à son fournisseur de machines-outils et à Siemens pour améliorer l’intégration entre son logiciel de gestion du cycle de vie des produits (PLM) et son système de fabrication assistée par ordinateur (FAO), aboutissant à un développement de ses activités et à une meilleure prise en charge des travaux ayant des tolérances serrées. Enfin, le géant de l’aérospatiale Pratt & Whitney a modernisé ses différents systèmes de gestion de la configuration au profit d’une solution Siemens unifiée pour la gestion des données pilotées par CAO, diminuant de 75 % ses coûts de développement produit.

Mais il ne s’agit pas là de cas isolés. D’après le cabinet de conseil CIMdata, les efforts entrepris dans le domaine de la fabrication numérique permettent de réduire les délais de mise sur le marché de 30 %t, de diminuer les efforts de planification et les coûts d’équipements de 40 % et d’augmenter la production globale de 15 %. Pour Patrick Michel, vice-président des solutions industrielles et du marketing DELMIA chez Dassault Systèmes : « Les entreprises qui mettent en place des solutions de fabrication numérique globales souhaitent pouvoir réaliser des visites virtuelles de leurs usines, limiter les risques inhérents à la planification de l’aménagement, identifier les effets que l’aménagement des usines aura sur les ouvriers qui y travailleront un jour, éviter d’avoir à retravailler la conception des équipements, optimiser l’utilisation des ressources et supprimer les prototypes. Grâce à la fabrication numérique, un processus manuel, lent et très exigeant en termes de ressources peut s’adapter à la réalité du XXIe siècle. »
La rapidité de la fabrication numérique offre également d’autres avantages : des réductions de coûts pendant la phase de développement des produits, car les cycles de développement sont plus courts ; des gains d’efficacité avec la fabrication à la demande ou en petites séries qui est possible, là encore, grâce à la numérisation ; et des itérations de conception plus rapides, pour toujours plus d’innovation de la part des concepteurs, grâce à la rapidité du processus d’établissement de devis et d’analyse.
La plupart des entreprises ont peur du changement. La moindre interruption de la chaîne d’approvisionnement ou de la production peut se révéler catastrophique, tant pour les fabricants que pour leurs clients. Comment s’y prendre, alors, pour réformer en profondeur vos infrastructures et vos procédés industriels ? Vous pouvez commencer par redéfinir les attentes de votre entreprise. Demandez à votre personnel de penser autrement. Travaillez avec vos employés, vos clients et même avec vos concurrents pour réfléchir à la situation actuelle et faire table rase. N’oubliez pas non plus de collaborer étroitement avec des fournisseurs experts en technologies numériques. Exploitez leur agilité tactique et misez sur leurs techniques de fabrication basées sur les données pour améliorer vos propres performances numériques. Soyez conscient que le chemin de la transformation numérique est souvent semé d’embûches. Tous ceux qui ont franchi la frontière du numérique vous le diront : il n’existe aucune règle en la matière. Ce n’est qu’en adoptant une nouvelle stratégie et en embrassant le changement que l’entreprise peut se réinventer.
”La fabrication numérique et l’IIoT offrent des possibilités telles pour redresser l’économie américaine que le président Obama a décidé d’entrer en jeu. Entendant la menace que constituent la concurrence étrangère et la délocalisation dans les pays à bas coûts de main-d’œuvre, il a chargé les ténors de l’industrie, les universitaires et le gouvernement de trouver des solutions pour redynamiser le secteur manufacturier américain. Le National Network for Manufacturing Innovation (NNMI) est né de ces efforts. Cette organisation couvre différents domaines, notamment le développement de technologies innovantes comme la fabrication additive, le développement de métaux légers, dont le magnésium et le titane, la fabrication de composites innovants ou les nanotechnologies, mais l’un de ses domaines de prédilection est la « création d’une infrastructure de fabrication intelligente et de méthodes intégrant des capteurs à bas coût dans les processus de fabrication ».
Bon nombre de ces initiatives portent sur la fabrication additive ou impression 3D. Protolabs a adopté cette technologie avec tout un éventail de techniques d’impression 3D industrielles comme la stéréolithographie (SL), le frittage sélectif par laser (SLS) et le frittage laser direct de métal (DMLS) qui lui permettent de créer des pièces dans pratiquement toutes les formes possibles et imaginables. De même qu’avec ses procédés de fabrication plus traditionnels, le fil numérique y est bel et bien présent. Les données sont partagées entre les deux extrémités du processus de fabrication ainsi qu’à chacune des étapes intermédiaires : conception, téléchargement du modèle, impression, finition et livraison. Par ailleurs, en intégrant deux techniques traditionnellement opposées dans l’industrie manufacturière (l’additif et le soustractif), Protolabs a considérablement amélioré sa flexibilité et offre de nouvelles solutions pour réduire les coûts de production et les délais de fabrication. Des solutions dont peuvent profiter les entreprises qui développent rapidement de nouveaux produits et qui en assurent la maintenance après le lancement.
Faire tomber les barrières, exploiter les données
Les fabricants de matériel soustractif peuvent également surfer sur la vague de l’IIoT et des procédés de fabrication numérique. En 2013, le fabricant de machines-outils Okuma Corporation inaugure son usine DS1 (Dream Site 1) à Oguchi (Japon), dévoilant au monde entier ses processus de fabrication et de contrôle de production entièrement automatisés. Depuis, cette usine affiche une productivité deux fois plus élevée, des délais de fabrication divisés par deux et des frais d’électricité en recul de 30 %. L’année suivante, son concurrent Mazak annonce le lancement de son concept d’usine iSMART4, « intégration numérique complète » de ses 10 usines de fabrication avec des équipements de pointe et des pratiques de fabrication innovantes. Aujourd’hui, ces deux fabricants sont fins prêts à partager l’essentiel de cette technologie d’avenir avec leurs clients par l’intégration de machines-outils et la communication de machine à machine (M2M) afin d’améliorer encore la productivité et la qualité des pièces jusque dans les plus petits ateliers.
Mais si la communication entre deux machines différentes est aujourd’hui possible, c’est essentiellement grâce à une innovation plus récente connue sous le nom de MTConnect. Ce protocole open source est à l’usine ce que le langage HTML est aux pages internet. Sans lui, le partage d’informations entre les dizaines de fabricants de dispositifs de commande existants relèverait de l’exploit et l’internet des objets liés à l’industrie manufacturière subirait un coup d’arrêt.
Le fournisseur de technologies de communication industrielles MEMEX Inc., partenaire commercial de Cisco, Okuma et Mazak, entre autres, fait partie des entreprises qui exploitent les énormes quantités de données disponibles au niveau des ateliers de fabrication. Comme le souligne son directeur général, David McPhail, le cabinet international de conseil en gestion Accenture estime que les investissements dans l’IIoT et les gains de productivité qui devraient en découler pourraient accroître le PIB cumulé des États-Unis de 6 100 milliards de dollars d’ici à 2030. « Les montants en jeu sont considérables, et pour nous, l’IIoT n’est rien de moins que la prochaine révolution industrielle ».

Emboîter le pas à GE
Une autre entreprise qui cherche sans cesse à se réinventer est General Electric (GE). Son PDG, Jeff Immelt, compare l’internet industriel à un tabouret à cinq pieds combinant l’hyperconnectivité, des machines extraordinairement intelligentes, la démocratisation des données, des algorithmes prédictifs améliorant les analyses, et des personnes travaillant d’arrache-pied avec toutes ces technologies. Profondément attachée à ces concepts, GE a été la première entreprise à utiliser des composants imprimés en 3D dans ses réacteurs. Elle a également mis la communauté de la fabrication additive au défi de retravailler la conception de l’un de ses supports aéronautiques et invite régulièrement les sociétés tierces à soumettre des propositions de nouvelles techniques de fabrication. Enfin, elle a officiellement approuvé le mouvement de l’IIoT en introduisant Predix, son « système d’exploitation pour l’internet industriel »5.
Dans le cadre de son programme Digital Alliance, GE a ouvert la plate-forme de développement Predix aux intégrateurs systèmes, aux fabricants de machines, aux opérateurs de télécommunications et, pour ainsi dire, à quiconque souhaitant développer des solutions logicielles sûres pour les environnements industriels.
L’adjectif « sûr » contenu dans la phrase précédente revêt une importance particulière pour les fabricants qui franchissent la porte du numérique. En effet, la grande majorité des ateliers et des petites entreprises de fabrication actuels ne disposent pas d’un responsable informatique local dédié — et encore moins d’un expert en sécurité des réseaux. Pourtant, le risque que des hackers piratent leur système informatique ne cesse de s’accroître avec l’augmentation du nombre d’ateliers connectés. C’est pourquoi Cisco et d’autres entreprises travaillent à l’élaboration de solutions permettant de simplifier l’infrastructure nécessaire à la sécurisation des systèmes informatiques industriels, afin d’éviter aux propriétaires d’ateliers de passer des nuits blanches en pensant à la sécurité de leurs usines connectées flambant neuves.

L’usine de demain
Acier, machines à vapeur, chaînes d’assemblage ou circuits intégrés, les piliers des précédentes révolutions pouvaient être vus, touchés et humés. Rien de tel avec l’IIoT et le fil numérique, confluence virtuelle de données, de logiciels et de capteurs où différents réseaux de technologies coopèrent pour rationaliser les processus de conception et de fabrication existants. L’IIoT et l’industrie 4.0 ont pourtant un véritable point commun avec les précédentes révolutions industrielles : la promotion et le perfectionnement de cette institution moderne fondamentale qu’est l’usine. La prospérité d’un pays repose sur son industrie manufacturière et les fabricants doivent donner le meilleur d’eux-mêmes en proposant des capacités et des procédés optimaux pour que les entreprises puissent fabriquer leurs produits.
Sources:
cisco.com, dmdii.uilabs.org, ge.com, memex.ca
1. weforum.org/agenda/2016/01/the-fourth-industrial-revolution-what-it-means-and-how-to-respond
3. cisco.com/c/dam/en_us/solutions/industries/docs/gov/everything-for-cities.pdf
4. mazakusa.com/discover2015/ismart-factory/