
La fabrication numérique au service du médical
Comment la fabrication numérique soutient l'industrie et ce que réserve l'avenir
Au cours des dernières années, la fabrication additive (plus connue sous le nom d’impression 3D) s’est imposée comme un moteur d’innovation dans un grand nombre de secteurs. Outre ses nombreuses applications industrielles (par exemple pour la production de prototypes et de pièces de rechange), l’utilisation de l’impression 3D dans le secteur médical présente de nombreux avantages.
Dès le départ, la variété des pièces imprimées en 3D et de leurs applications dans le domaine médical a été aussi étendue que les possibilités de production et les matières elles-mêmes.
Ainsi, cette technologie idéale pour les prototypes et les pièces de production uniques, on peut par exemple l’utiliser pour la production d’implants.
Dans le présent guide, nous examinerons plus en détail les avantages de la fabrication additive dans le secteur médical, les applications potentielles qui sont déjà habituelles et son importance pour la médecine de demain.


Fabrication additive - Processus de production, avantages et matières
Pour se faire une idée des applications de la fabrication additive dans le secteur médical, il faut avant tout comprendre en quoi consiste le processus d’impression 3D. La fabrication additive est différente des autres méthodes de fabrication. La matière n’est pas coulée, comme c’est le cas pour la fabrication de pièces moulées par injection, ni découpée dans un bloc plus grand, comme cela se produit dans l’usinage CNC.
Comme le suggère le terme « additive », la matière est ajoutée couche après couche. Même si les différentes méthodes de fabrication additive diffèrent quant au processus et aux matières utilisés, la production par couches demeure identique.
Par rapport à d’autres procédés, celui-ci offre une plus grande liberté au niveau de la conception des pièces et des géométries potentielles.
Depuis ses débuts, l’impression 3D s’est considérablement diversifiée, avec un certain nombre de processus de fabrication très différents. Les principaux processus de fabrication utilisés aujourd’hui dans la production de matériel médical sont le frittage laser direct de métal et la stéréolithographie.

Frittage laser direct de métal (DMLS)
En principe, la procédure d’impression des pièces en DMLS ne diffère que légèrement des autres méthodes de fabrication additive. Les structures de support dissipent la chaleur générée pendant le processus et assurent la stabilité des composants. Sans structures de support, le risque serait de balayer la nouvelle matière pendant le processus d’impression.
La DMLS utilise un faisceau laser haute puissance contrôlé par ordinateur pour faire fondre et fusionner des couches de poudre métallique. Ce processus de fusion s’effectue couche par couche, pour produire finalement un composant solide et fini.
Une fois terminé, le composant est séparé de ses structures de support et l’excédent de poudre métallique fait l’objet d’un post traitement en fonction de son application. Un grand nombre de métaux se prêtent à la production par DMLS, notamment les alliages de titane, qui sont essentiels en médecine, notamment pour la fabrication d’implants osseux.
Stéréolithographie
La stéréolithographie est similaire aux autres méthodes de fabrication additive. Elle permet d’imprimer des polymères et des plastiques aux géométries complexes ou de très petites structures qui exigent une rigidité, une résistance aux chocs ou une durabilité particulières.
Comme le DMLS, elle emploie un laser pour effectuer l’impression. Toutefois, contrairement à cette dernière, la matière première ne se présente pas sous forme de poudre, mais plutôt sous forme de polymère composé de photopolymères et d’additifs. Un laser ultraviolet durcit ce polymère pour en faire un plastique thermodurcissable. La plateforme de fabrication est abaissée à chaque étape, de sorte qu’une nouvelle couche de polymère recouvre le composant, qui est ensuite durci par le laser pour lui donner la forme requise.
Une fois la pièce fabriquée, le polymère restant est nettoyé dans le cadre du post traitement et les structures de support sont retirées. Pour finir, les pièces sont soumises à un cycle de polymérisation aux UV pour solidifier complètement leur surface extérieure.
Une nouvelle matière appelée MicroFine™ Green mérite d’être mentionnée. Avec la stéréolithographie, elle permet de produire des structures particulièrement fines et à haute résolution, par exemple des cathéters miniaturisés ou des outils peu invasifs.
APPLICATIONS MÉDICALES DE LA FABRICATION ADDITIVE
Le secteur médical a adopté l’impression 3D peu après son apparition. Au départ, la possibilité de produire facilement des pièces individuelles, telles que des boîtiers de dispositifs médicaux, a constitué un avantage révolutionnaire. Très vite, le secteur a reconnu le potentiel du DMLS et la première production d’implants a eu lieu.
Implants imprimés en 3D
Actuellement, les implants sont les pièces imprimées en 3D les plus répandues dans le secteur médical. Ils offrent toute une série d’avantages, notamment lorsqu’il s’agit de remplacer de la matière osseuse. Ces pièces sont imprimées à l’aide de fichiers CAO, souvent générés par des techniques d’imagerie médicale.
Applications des implants imprimés en 3D
Les implants sont généralement des éléments réalisés sur mesure dans un but bien précis, la fabrication additive est donc la solution idéale, car elle permet de produire des pièces uniques rapidement et à moindre coût. Jusqu’à une date récente, ces types d’implants étaient généralement produits en série, puis adaptés au patient, souvent par le chirurgien. Elle permet de réaliser des pièces simples telles que des implants du fémur ou des os de la hanche adaptés à chaque patient, des articulations, des os zygomatiques et des os de la mâchoire, ainsi que des implants complexes tels que des implants orbitaux, des os crâniens et des implants thoraciques. De plus, l’implantation/fixation de prothèses dentaires est désormais une application standard de l’impression 3D.
Les délais de fabrication relativement rapides de l’impression 3D et la possibilité de produire à la demande (en fonction des besoins en implants) ont conduit le secteur médical à apprécier de plus en plus les avantages de cette technologie. Ainsi, elle est utilisée tant pour des implants standard, tels que des vertèbres individuelles de la colonne vertébrale, que pour des options plus personnalisées.

Avantages des implants imprimés en 3D
Les avantages de l’impression 3D dans le secteur médical sont similaires à ceux des secteurs à caractère plus industriel. Il faut tout d’abord mentionner le large éventail de possibilités qu’offre l’impression 3D pour la conception d’implants individuels. Les autres procédés de fabrication ne peuvent tout simplement pas créer les géométries et les formes que permet l’impression 3D et sont donc moins adaptés. La flexibilité offerte par la fabrication additive dans le processus de fabrication permet également d’intégrer des structures réticulaires et spongieuses. Ces dernières peuvent améliorer considérablement la biocompatibilité des implants et ainsi faciliter leur intégration avec le matériau endogène.
Pour les hôpitaux, le fait que les implants individuels spécialisés soient plus rentables que ceux produits par des méthodes conventionnelles présentent un grand avantage. D’autres procédés de fabrication nécessitent des investissements importants dans des outils et des équipements spéciaux, adaptés dans chaque cas à un implant spécifique. Avec l’impression 3D, ces coûts supplémentaires sont évités grâce à un processus de fabrication plus souple. Les implants spéciaux produits par fabrication additive ne doivent pas être retravaillés à grands frais.
Matières et exigences légales pour les implants imprimés en 3D
La fabrication de pièces par DMLS permet d’imprimer des implants directement à partir d’une matière adaptée aux processus médicaux. Pour des implants tels que les os de la hanche ou les implants orbitaux, le Ti6Al4V, un alliage dont le composant principal est le titane, est le plus utilisé. Cet alliage se caractérise par une biocompatibilité élevée, une résistance et une stabilité considérables, mais aussi une relative légèreté. Une autre matière utilisée dans l’impression 3D médicale est l’acier inoxydable 316L.
Par contre, lors de la production d’implants standard par fraisage ou moulage, les matières utilisées présentent une biocompatibilité moins bonne, ce qui signifie que leur fabrication nécessite l’ajout d’un revêtement en titane.
La production d’implants doit respecter les réglementations en vigueur, notamment en ce qui concerne le choix des matières. Pour le Ti6Al4V, les exigences légales incluent les normes ISO 5832-3, ASTM F1472 et ASTM B348, qui classent la matière et les composants chimiques comme appropriés pour une utilisation en médecine. La certification CE n’est pas nécessaire pour les implants spéciaux. En dernière instance, c’est au médecin concerné qu’incombe la responsabilité et la décision de savoir si un implant peut être utilisé sur un patient et de quelle façon. L’impression 3D présente un autre avantage dans ce domaine : de nombreuses matières sont connues dans le monde médical. Les normes et réglementations strictes auxquelles ces matières doivent se conformer ne sont pas affectées par l’impression 3D. Rien n’empêche donc le secteur médical de les utiliser après le processus de fabrication additive.
Équipements médicaux et produits sur mesure
Un autre domaine clé du secteur médical où l’impression 3D gagne du terrain est celui de la production de dispositifs médicaux individuels et de produits sur mesure. Ces dispositifs sont souvent destinés à une utilisation à court terme pour effectuer des tâches spécifiques. Gabarits spéciaux et pièces individuelles « Les aides chirurgicales sont souvent conçues de manière spécifique pour chaque patient et pour l’opération correspondante, par exemple, des gabarits aident à percer l’os crânien au millimètre près. Compte tenu du niveau de précision élevé des procédés tels que le DMLS (il est possible d’obtenir des caractéristiques individuelles de moins d’un millimètre, selon la biocompatibilité de la matière et l’application prévue), l’utilisation de l’impression 3D présente d’énormes avantages. Des CT scans précis de la zone où un orifice a été effectué peuvent créer des fichiers précis pour produire rapidement des pièces. Les gabarits de perçage basés sur les besoins ainsi obtenus permettent de réaliser un travail plus précis et d’éviter les erreurs dangereuses pendant l’opération. »
La MicroFine™ Green, relativement récente, fait, elle aussi, partie des matières de fabrication additive utilisées dans la production de dispositifs médicaux et de produits
sur mesure. L’utilisation de cette matière vert vif pour créer des structures microscopiques rend possible toute une série d’applications, qui n’étaient pas envisageables auparavant pour l’impression 3D médicale. Des pièces détachées des stimulateurs cardiaques, dont la taille ne dépasse pas une fraction de millimètre, sont tout aussi réalisables que des cathéters miniaturisés ou des injecteurs de liquide et de gaz. Grâce à l’utilisation de procédés tels que le DMLS et la stéréolithographie pour imprimer des géométries complexes, il n’y a pratiquement aucune limite à ce que la fabrication additive peut produire pour le secteur médical.




Instruments médicaux
En plus de fournir des modèles pour des opérations spécifiques, qui diffèrent d’un patient à l’autre, les nouvelles méthodes de fabrication permettent également d’innover dans le domaine des instruments médicaux pour le bloc opératoire. L’impression 3D facilite la production d’instruments qui, auparavant, dans certains cas n’étaient pas réalisables.
Par exemple, le DMLS permet de fabriquer des dispositifs chirurgicaux autorisant des perçages ou des incisions spécifiques, qui peuvent se présenter de manière récurrente. Les applications de la fabrication additive comprennent également d’autres instruments médicaux spécialisés destinés à mieux suturer les plaies chirurgicales ou utilisés comme outils pendant l’opération elle-même. Les instruments spécifiquement adaptés à un chirurgien donné, tels que les manches de scalpels, en sont un exemple. Les pièces fabriquées à partir de plastiques spéciaux par fabrication additive peuvent également être utilisées, par exemple comme supports. Une utilisation aussi étendue de pièces imprimées en 3D dans le secteur médical est possible parce que les matières et les méthodes combinent toute une série d’avantages, notamment la résistance mécanique, la propreté et la facilité de nettoyage et de stérilisation. De plus, la production de pièces conçues pour une seule tâche ou un seul objectif est moins coûteuse que par les méthodes de production traditionnelles.

Prothèses et orthèses
Cela fait longtemps que l’impression 3D est un procédé de fabrication très pratique pour les prothèses et les orthèses spécialement adaptées. Par rapport à d’autres procédés de fabrication, elle permet de produire facilement et rapidement des pièces individuelles spécialement adaptées à un patient, et à moindre coût.
Les pièces doivent être spécialement adaptées pour la production d’orthèses et de prothèses. Cependant, alors que les prothèses remplacent des membres ou des parties du corps manquants, les orthèses ont généralement pour objectif de soutenir ou d’immobiliser des membres ou des articulations spécifiques. Dans les deux cas, la fabrication additive contribue grandement à commercialiser des idées novatrices plus rapidement et de manière plus rentable. Ainsi, les personnes qui ont un besoin urgent de ces aides médicales peuvent en bénéficier plus rapidement.

Le développement plus rapide des exosquelettes (c’est-à-dire d’orthèses), qui offrent aux utilisateurs un meilleur fonctionnement de l’appareil locomoteur, en est un exemple.
Les processus de fabrication tels que le moulage par injection prennent souvent beaucoup de temps, alors que le délai d’attente pour les pièces imprimées en 3D est bien moindre. L’impression 3D présente des avantages similaires pour la production de prothèses innovantes, qui doivent être spécialement adaptées à chaque porteur, ou pour les prototypes et les nouvelles générations de prothèses qui, comme les exosquelettes, doivent encore passer par un cycle de développement de produit
Des modèles pour la planification, la recherche et la formation
Grâce aux techniques d’imagerie modernes, telles que la tomographie et l’IRM, les médecins ont une bien meilleure connaissance du corps humain qu’il y a quelques années.
Ces méthodes ont joué un rôle essentiel pour les praticiens et les ont aidés à diagnostiquer les maladies dans le cadre de leur travail quotidien. Ces techniques d’imagerie diagnostique ont également un impact significatif sur leur préparation aux procédures et opérations compliquées. Et c’est là un autre domaine dans lequel les processus de fabrication additive peuvent s’avérer utiles. Les techniques d’imagerie modernes sont si précises qu’elles peuvent êtrenutilisées pour créer des modèles grandeur nature de l’organe concerné, imprimés en 3D, sur lesquels le chirurgien peut tester l’opération avant la procédure proprement dite. Ces modèles sont également appropriés pour déterminer les approches optimales ou pour tester des procédures plus risquées sans danger pour le patient. Dans la mesure où les matières souples peuvent également être imprimées par fabrication additive, les modèles peuvent également présenter les caractéristiques que l’on attend du matériau biologique.
Des répliques pour la recherche et la formation
Les répliques d’organes et de parties du squelette réalisées dans divers matériaux au moyen de la fabrication additive permettent également aux universités et aux établissements d’enseignement supérieur de mieux comprendre le corps humain. Si les répliques conventionnelles de pièces anatomiques sont souvent coûteuses et présentent une résolution et une qualité médiocres, celles imprimées en 3D constituent aujourd’hui une solution de rechange viable à la modélisation conventionnelle. Les modèles réalisés pour préparer les interventions chirurgicales peuvent être utilisés pour la formation des étudiants en médecine, pour illustrer les dysfonctionnements du corps humain et pour présenter les maladies sous forme d’exemples réalistes.
La reproductibilité de ces exemples est un avantage majeur de l’impression 3D. En particulier dans les cas où une partie du corps ou un organe spécifique est concerné, vous pouvez générer un nombre illimité de modèles pour les facultés de médecine du monde entier.



REGARDER VERS L’AVENIR - APPLICATIONS DE L’IMPRESSION 3D DANS LE SECTEUR MÉDICAL
Au cours des dernières années et décennies, peu de nouvelles technologies ont aussi fortement bouleversé la recherche médicale que la fabrication additive. À l’heure actuelle, le développement des procédés additifs et de leurs potentialités en est encore à ses débuts. Des travaux sont en cours sur une variété de nouvelles applications modernes susceptibles de bouleverser le monde médical et notre compréhension de la guérison et des soins au cours des prochaines décennies.
Recherches actuelles dans le domaine des matières organiques
Jusqu’à présent, les métaux et les plastiques utilisés en médecine sont parfaitement adaptés à l’impression 3D. Ils peuvent faciliter les soins aux patients, mais atteignent rapidement leurs limites lorsqu’il s’agit de matière vivante. Ainsi, les premiers prototypes imprimés en 3D reproduisant des organes entiers, tels que le coeur, ont déjà vu le jour.
Mais comme la matière n’est pas organique, qu’elle n’est pas destinée à demeurer en permanence dans le corps et qu’elle n’est pas conçue pour résister aux fortes contraintes de la vie quotidienne, elle est pour l’instant uniquement utilisée pour des prototypes individuels. Les développeurs et les chercheurs se concentrent désormais sur l’innovation et l’amélioration des processus d’impression de matières organiques pour l’avenir.
Les expériences actuelles se concentrent essentiellement sur l’application de tissu additionnel, à base de cellulose et de matériaux organiques, sur les structures existantes, puis d’implanter ces structures pour créer des tissus fonctionnels. Une fois pleinement développée et utilisable, les avantages d’une telle technologie seront énormes. Les machines pourraient produire des vaisseaux, des organes ou des tissus musculaires à implanter dans le corps humain. Des projets de recherche, tels qu’un cœur artificiel réalisé par impression 3D, ont prouvé que les répliques d’organes entiers fonctionnent et peuvent potentiellement sauver des vies. Le développement et l’amélioration de ces systèmes permettraient de prolonger la durée de vie des implants de quelques heures jusqu’à des intervalles de temps médicalement utiles.
Outre ces recherches, d’autres expériences sont en cours en vue d’améliorer les soins médicaux dans le futur. À titre d’exemple, des travaux sont actuellement menés pour produire de la peau humaine par des procédés dits de bio-impression, pour fabriquer des prothèses biologiques telles que des oreilles et pour imprimer des matières organiques directement sur le patient. Les tissus imprimés en 3D sont également parfaitement indiqués pour les essais et les tests de nouveaux médicaments et
d’applications médicales. Dans le meilleur des cas, les essais sur l’animal et sur l’homme de nouvelles substances actives deviendraient superflus.
La puissance d’innovation de l’impression 3D dans le domaine médical est quasiment illimitée. Cela tient notamment à sa flexibilité, par exemple dans la production de géométries complexes. Cela tient notamment à sa flexibilité, par exemple dans la production de géométries complexes. Il s’agit d’un avantage considérable, surtout
si l’on considère la complexité de certaines applications médicales, qui impliquent généralement de travailler dans des zones difficiles d’accès qui laissent peu de marge d’erreur.

Optimisation des procédés existants
À court terme, les applications de l’impression 3D en médecine porteront sur des procédés qui sont déjà possibles et sur la façon dont la pratique clinique quotidienne peut les intégrer. Actuellement, la fabrication additive est le seul domaine à générer autant d’innovations. Cela s’explique par le fait que le développement constant des procédés et l’amélioration de ceux existants engendrent toujours de nouvelles applications pour l’impression 3D.
Des techniques telles que la stéréolithographie, le frittage direct par laser métallique et le Polyjet sont apparues progressivement et ont constamment évolué pour imprimer une plus grande variété de matières. À l’avenir, d’autres procédés d’impression 3D viendront compléter et optimiser l’éventail des applications possibles. Avec le développement de nouveaux procédés, le choix des matières continuera de s’élargir et de nouvelles solutions seront disponibles. Les avancées futures dans le domaine des matières organiques, les nouvelles méthodes additives et les résultats des recherches futures promettent des innovations de grande envergure.
Comment faire fonctionner l’impression 3D avec les installations médicales ?
En ce qui concerne la fabrication additive et les applications médicales, certains ont suggéré que les hôpitaux et les instituts de recherche pourraient avoir besoin de leurs propres machines et être en mesure de les utiliser, sans aucun problème. Ce n’est pas le cas actuellement. Les entreprises spécialisées sont les principaux fabricants d’implants, d’orthèses, de prothèses, etc. qui sont ensuite envoyés aux hôpitaux ou aux utilisateurs finaux. Il est peu probable que des imprimantes 3D soient bientôt disponibles dans les sous-sols des hôpitaux.
Et cela s’explique surtout par le fait que les machines utilisées pour la production d’implants osseux en titane, notamment, sont très coûteuses en termes d’achat et d’utilisation. De plus, le post-traitement supplémentaire des implants imprimés entraîne encore davantage de dépenses. Ajoutons que l’utilisation de procédés et de machines de fabrication additive exige des connaissances et une formation spécialisées très poussées. La différenciation encore plus marquée de ces procédures à l’avenir et les possibilités de production plus étendues des entreprises spécialisées constituent un autre argument en défaveur de leur utilisation directe dans les hôpitaux.
En revanche, la coopération entre les hôpitaux, le corps médical et les entreprises spécialisées dans les procédés de fabrication modernes pour la production de prototypes et la fabrication additive va se développer et être davantage interconnectée. Étant donné qu’une grande variété de nouvelles applications sont déjà en train d’émerger, l’importance de la fabrication additive dans le domaine médical ne cessera de croître. Les médecins des générations à venir se demanderont comment la médecine a pu se passer de l’impression 3D.

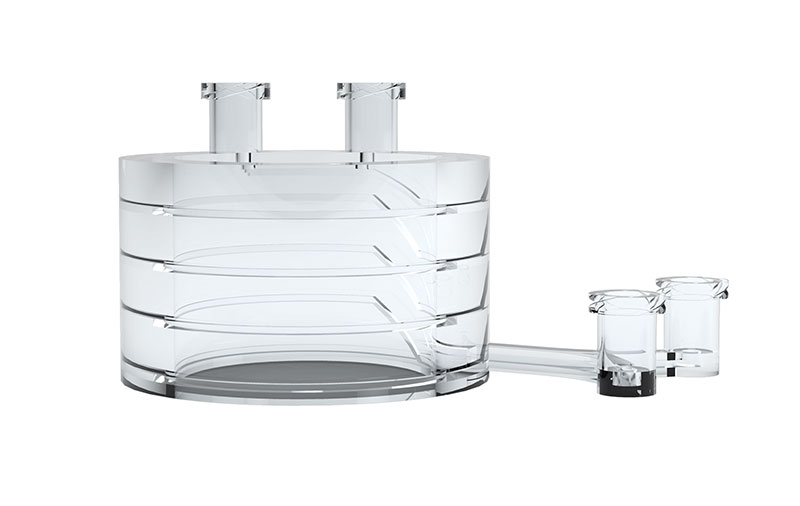
L’IMPRESSION 3D DANS LE DOMAINE MÉDICAL - UNE TECHNOLOGIE POUR AUJOURD’HUI ET POUR DEMAIN
L’impression 3D existe depuis près de 40 ans et n’a cessé d’évoluer, mais l’utilisation de cette technologie de fabrication dans le secteur médical est encore relativement récente. Toutefois, les avantages de l’impression 3D ont été rapidement reconnus par la communauté médicale, et ses applications sont déjà très diverses.
Avec toutes sortes d’implants, des conceptions spécifiques pour les opérations, des instruments médicaux et l’utilisation de pièces imprimées en 3D pour la préparation, la recherche et la formation, les autres technologies sont de plus en plus délaissées. Et maintenant que le système de gestion de la qualité pour les dispositifs médicaux (ISO 13485) est reconnu dans la chaîne d’approvisionnement de l’impression 3D, la fabrication additive peut répondre à des exigences législatives strictes dans le monde entier.
À l’avenir, de nouvelles matières et de nouveaux procédés renforceront l’importance de l’impression 3D pour la médecine, et il sera difficile d’imaginer le quotidien des patients et des médecins sans elle. La science et la recherche appliquée travaillent depuis longtemps sur des applications qui dépasseront les attentes les plus folles de la plupart des médecins. En fait, parler d’un boom de la médecine grâce à la fabrication additive est en dessous de la réalité.
Pour les malades et les blessés, l’impression 3D est une promesse d’amélioration des chances de guérison, d’atténuation de la douleur et de meilleure qualité de vie, ce qui est certainement l’objectif le plus important de tous.
Boîte à outils de fabrication pour le secteur médical

Les prototypes aident les équipes de conception à prendre des décisions bien étayées en obtenant des données inestimables sur les performances de ces prototypes et la réaction des utilisateurs. Plus les données recueillies au stade de la conception du développement du produit sont nombreuses, meilleures sont les chances de prévenir les problèmes de produit ou de fabrication à l’avenir.
Le prototypage accéléré a certes toujours été important dans le développement médical, mais il l’est encore plus aujourd’hui durant la crise du COVID-19 puisque les concepteurs et les ingénieurs créent des dispositifs médicaux essentiels pour lutter contre la pandémie (voir barre latérale).
Chez Protolabs, nous produisons des prototypes pour toute une série de dispositifs médicaux et d’autres produits et assemblages technologiques pour ce secteur. Une stratégie de fabrication bien pensée augmente considérablement les chances qu’un produit soit conforme aux strictes normes de réglementation et de conformité, soit lancé à temps sur le marché, soit accepté, soit fiable et, soit rentable. Nos services et nos processus de qualité vous garantissent d’y parvenir plus rapidement en tirant parti de nos années d’expériences dans le développement de dispositifs médicaux, et de nos processus de fabrication accélérés grâce à une capacité d’itération rapide sur les pièces.
Voici huit façons dont nous pouvons vous aider à améliorer vos pièces lors du développement de dispositifs médicaux.
1. UTILISER L’ANALYSE DE FAISABILITÉ
Une méthode de fabrication courante pour les pièces et composants médicaux est le moulage par injection en petite série, bien que certains prototypes techniques fonctionnels soient aussi imprimés en 3D ou usinés. Chez Protolabs, notre processus de moulage commence par un devis en ligne. Chaque devis est accompagné d’une analyse de faisabilité gratuite, automatisée et interactive (DFM). Pour compléter éventuellement cette analyse interactive en ligne, nous disposons d’ingénieurs spécialisés dans l’examen des conceptions assurant une consultation gratuite pour nos trois services de fabrication : le moulage, l’usinage et l’impression 3D de qualité industrielle (fabrication additive).Tout commence avec le téléchargement de votre fichier CAO.
En outre, dans le secteur des technologies médicales, il arrive qu’une pièce conçue à l’origine pour être imprimée en 3D ou usinée par CNC doive être redessinée pour être moulée par injection. Nos ingénieurs d’application sont à votre disposition pour vous conseiller sur ces types de modifications. Si vous avez besoin d’une assistance plus poussée, Protolabs propose des conseils de conception pour la faisabilité (CDFM), une consultation approfondie pour mettre au point votre produit avec des recommandations et des idées sur la façon d’améliorer les formes pour maximiser la fonction.
Notre objectif est de vous aider à gagner du temps et de l’argent, même si vous devez apporter des modifications que vous n’aviez pas prévues, afin d’éviter des pièces impossibles à fabriquer. La section suivante s’intéresse plus particulièrement au moulage de dispositifs médicaux et autres pièces et produits du secteur médical.
2. TIRER PARTI DU MOULAGE PAR INJECTION POUR LES APPLICATIONS MÉDICALES
Notre service de moulage fait passer rapidement de la conception du prototype à la production des pièces et des composants, ce qui est particulièrement important dans le secteur hautement réglementé de la médecine, car les produits médicaux doivent subir des tests rigoureux depuis la phase de développement jusqu’à la commercialisation. Notre outillage en aluminium de haute qualité, combiné à une analyse DFM automatisée, peut facilement réduire le temps de développement d’un produit, puisqu’il suffit de quelques jours pour fabriquer un moule, ce qui est bien plus rapide que pour un outillage en acier.
Dans cette optique, nos éléments de contrôle de la qualité et de l’outillage comprennent :
- la validation des processus, qui peut être réalisée par un ensemble de qualifications normalisées, par un protocole accepté par l’industrie ou définie par le client
En outre, en ce qui concerne l’outillage, notre logiciel d’analyse de remplissage de moules peut aider à améliorer la conception globale d’une pièce médicale de plusieurs façons, par exemple : en aidant à positionner le ou les points d’injection ; en montrant la position des lignes de plan joint, ce qui permet d’améliorer les propriétés esthétiques et physiques de votre pièce ; en repérant les zones difficiles à remplir dans le moule et en identifiant la matière appropriée.
Des entreprises se sont tournées vers Protolabs pour des projets récents dans le secteur médical, par exemple :
- Pièces et produits en début de développement
- Composants nécessitant des chaînes d’approvisionnement complexes
- Projets pour lesquels une flexibilité de conception est nécessaire tout au long du développement
- Pièces pour lesquelles les enseignements des premiers processus peuvent être utiles lors d’un transfert vers la production
- Essais de vérification de la conception, soumissions d’essais cliniques et demandes auprès des organismes de réglementation
3. AMÉLIORER RAPIDEMENT VOS PROTOTYPES GRÂCE AUX MOULES MULTI-EMPREINTES
Le développement de pièces et de dispositifs pour l’industrie médicale est un défi, car les choses évoluent très rapidement. Cela est particulièrement vrai aujourd’hui, suite à la crise du COVID-19. Pour y répondre, vous pouvez bénéficier de nos solutions de moules d’injection familles et multi-empreintes afin de pouvoir obtenir dans la matière finale plusieurs prototypes, puis tester ces multiples versions pour en choisir la meilleure.
Outre l’avantage des itérations rapides, l’utilisation de moules à empreintes multiples peut également être un moyen efficace d’augmenter le nombre de pièces de production et de réduire leur coût à l’unité. Nous vous proposons un conseil de conception sur les moules multi-empreintes qui détaille cette approche.
L’impression 3D métallique avec le processus DMLS permet d’obtenir des pièces complexes à haute résolution pour des applications médicales.




4. ENVISAGER L’IMPRESSION 3D MÉTAL POUR LES PIÈCES MÉDICALES COMPLEXES
Le frittage laser direct de métal (DMLS) est une technologie de fabrication additive métallique fréquemment utilisée, notamment pour l’industrie médicale. Le DMLS présente plusieurs avantages, par exemple pour l’impression de pièces à haute résolution pour certains instruments. Les matières comprennent l’acier inoxydable (17-4 PH & 316L), l’aluminium (AlSi10Mg), le chrome cobalt (CoCr), l’Inconel (IN718), le cuivre (CuNi2SiCr) et le titane (Ti-6Al-4V).
Prenez par exemple les outils chirurgicaux aux caractéristiques ultrafines et les composants médicaux aux formes organiques. Ces dispositifs peuvent être conçus pour le moulage par injection ou la coulée de métaux, deux procédés dont les coûts d’outillage sont relativement élevés et dont les délais de livraison peuvent s’étendre sur plusieurs semaines.
Avec le DMLS, vous pouvez imprimer un prototype d’outil chirurgical manuel avec le poids et la résistance exacts du produit final et le mettre entre les mains d’un chirurgien en quelques jours. Par ailleurs, notre usine européenne d’impression métallique 3D est certifiée ISO13485, ce qui nous permet de produire des prothèses, des implants ou des instruments médicaux personnalisés destinés à une véritable utilisation. Pour les projets DMLS, consultez nos directives de conception.
5. CHOISIR LES OPTIONS DE FINITION POUR LES PIÈCES MÉDICALES MOULÉES
Les entreprises du secteur médical tirent souvent parti des options de post-traitement pour leurs pièces moulées. Nous proposons un large choix de finitions de surface qui renforcent les pièces, améliorent l’esthétique et permettent la personnalisation. Ces processus de finition comprennent :
- Texture de moule
- Inserts filetés
- Tampographie
- Assemblage thermique
- Gravage laser
- Assemblage basique
Hemosonics, fabricant de dispositifs médicaux s’est récemment tourné vers Protolabs pour des options de finition, complétant nos services de moulage par injection, d’impression 3D et d’usinage. La société a utilisé l’assemblage à chaud et la tampographie pour son analyseur de sang Quantra System.



6. UTILISER LA BONNE MATIÈRE POUR LES PIÈCES MÉDICALES
Nous disposons de matières de qualité médicale adaptées à la plupart des projets de moulage par injection ou d’impression 3D. Le choix de la meilleure matière pour votre projet signifie que vos prototypes correspondront le plus possible aux pièces finales.
Nous proposons également une correspondance personnalisée de couleurs pour les numéros Pantone ou les échantillons de pièces fournis par les clients. Ceux qui disposent de matières propriétaires pour la production finale, courantes dans l’industrie médicale, veulent souvent choisir une matière aussi similaire que possible pour leur prototype en exigeant une correspondance étroite en termes d’élasticité, de dureté, de résistance et d’autres caractéristiques critiques.
Pour vous aider à choisir la matière ou la couleur qui conviendront le mieux à votre commande, vous pouvez également consulter l’un de nos ingénieurs d’application.
Matières courantes pour les applications médicales :
High-temp Plastics (plastiques haute température)
Le PEEK et le PEI (Ultem) offrent une résistance aux températures élevées, au fluage et sont adaptés aux applications nécessitant une stérilisation. Par exemple, les pièces d’un dispositif médical peuvent devoir tolérer la chaleur extrêmement élevée d’un autoclave ou une stérilisation chimique agressive entre chaque utilisation.
Caoutchouc de silicone de qualité médicale
L’Elastosil LR 3003, par exemple, propose une excellente résistance thermique, chimique et électrique, ainsi que des caractéristiques biocompatibles pour le moulage par injection. Il peut généralement être utilisé pour des dispositifs entrant en contact avec la peau.
True Silicone
La matière True Silicone est biocompatible, offre une grande résistance aux conditions environnementales difficiles et les pièces imprimées sont hydrofuges, isolantes et présentent une grande perméabilité aux gaz. Cette matière est généralement utilisée dans des applications de santé comme les prothèses, les bouchons d’oreille ou autres pièces à porter.
Résine micro-résolution similaire à l’ABS
MicroFine™ (vert et gris) est une matière exclusive de Protolabs. Imprimez des pièces complexes en 3D, comme des instruments de précision et des composants de diagnostic, avec des caractéristiques microscopiques de 0,7 mm seulement. La résine MicroFine™ imite un plastique ABS courant et permet une grande liberté de conception.
Matière d’impression transparente similaire à l’ABS
La matière d’impression 3D transparente de type ABS (WaterShed XC 11122) peut recevoir des finitions afin d’obtenir une transparence fonctionnelle pour les pièces microfluidiques et les composants comme les lentilles et les boîtiers, qui sont utilisés dans une variété d’applications médicales.
Alliages médicaux
Des métaux usinés aux métaux imprimés en 3D, il existe plus de 20 options de métaux disponibles pour des composants, instruments et autres applications médicales. Les métaux comme le titane et l’Inconel sont particulièrement résistants à la température, tandis que différents métaux inoxydables permettent d’éviter la corrosion.
Ce guide de comparaison des matières peut vous aider à faire le meilleur choix.
7. S’ASSURER QUE SON FABRICANT DISPOSE D’UN SYSTÈME DE QUALITÉ ÉPROUVÉ
Les fabricants de matériel médical doivent se soumettre à de nombreux contrôles de qualité et autorisations réglementaires avant qu’un produit ne soit mis sur le marché. Nos systèmes de qualité pour le moulage et l’impression 3D s’appliquent tout au long de notre processus de fabrication. Bien qu’ils partagent des similitudes, chaque service a des mesures de qualité uniques.
Plusieurs étapes d’assurance qualité couvrent le processus de moulage par injection :
- Des contrôles stricts des numéros de pièces et des matières garantissent le respect des exigences matérielles
- Les résines thermoplastiques sont séchées selon les spécifications dans un équipement de séchage étalonné
- Les contrôles de qualité dimensionnelle sont effectués au début des commandes et pendant la fabrication, sont documentés électroniquement et font partie du dossier de fabrication
- Des inspections visuelles en cours de fabrication peuvent être effectuées toutes les heures pour s’assurer que les pièces correspondent aux échantillons initiaux et aux normes de fabrication
- Les réglages de la presse sont documentés pour les futurs cycles de production
- Des contrôles de pression et de température sont effectués pour chaque injection dans le processus de moulage
Les systèmes de qualité pour l’impression 3D de qualité industrielle assurent la cohérence et la reproductibilité des pièces :
- Les instructions de fabrication additive sont envoyées à des imprimantes 3D compatibles avec le logiciel
- Avant le début de la construction, les opérateurs vérifient et préparent le matériel à l’aide d’une liste de contrôle détaillée couvrant le chargement, le déchargement et le nettoyage, ce qui permet d’éviter les erreurs.
- Les températures pendant le moulage sont contrôlées et ajustées en conséquence
- Les pièces finales sont suivies numériquement et font l’objet d’une finition ou d’un post-traitement avant d’être acheminées vers les postes d’inspection
- Protolabs est certifié ISO 9001 pour son système de qualité de tous les services d’impression 3D et ISO 13485 pour l’impression 3D en métal.
- Protolabs est certifié ISO 9001 en tant que système de qualité pour tous les services de moulage par injection
8. INSPECTIONS RAPIDES DE LA QUALITÉ
Les inspections portent sur la conformité des pièces. Nos rapports d’inspection pour le moulage par injection sont personnalisés en fonction du service et du niveau d’inspection requis. Des échantillonnages périodiques sur l’esthétique et les dimensions des pièces sont effectués pour garantir la conformité de ces pièces. Les inspections sont assurées par le personnel chargé du contrôle de la qualité et un programme d’étalonnage est en place pour tous les équipements de mesure.
Nous effectuons des rapports d’inspection supplémentaires pour garantir la vérification de la dimension critique et les exigences de documentation de la qualité. Une option d’inspection numérique améliorée, qui permet de vérifier les caractéristiques telles que l’ID/OD (diamètre intérieur et extérieur) plan à plan, et l’emplacement des trous, peut être effectuée dans notre laboratoire de métrologie. Un scanner 3D à grande vitesse fournit une vue en couleur permettant une comparaison directe CAO-scanner pour un rapport de qualité supplémentaire.
Si un rapport encore plus approfondi est nécessaire, notre laboratoire de métrologie peut générer un rapport d’inspection conventionnel en utilisant une machine de mesure des coordonnées (CMM) pour répondre aux exigences de l’inspection du premier article (FAI) ou du processus d’approbation de la pièce de production (PPAP). Le rapport vérifie toutes les dimensions de la pièce, y compris les dimensions non critiques, ainsi que la documentation complémentaire, le cas échéant. Ceci s’applique à tous les types de mesures de dimensionnement et de tolérances géométriques (GD&T).
Pour l’impression 3D, nous offrons une large gamme de services secondaires, allant des essais de traction, à l’analyse de la porosité et aux essais de dureté. Pour une assistance, n’hésitez pas à nous contacter au +33 (0)4 56 64 80 50 ou customerservice@protolabs.fr Pour démarrer aujourd’hui votre projet, il vous suffit de télécharger un fichier CAO 3D afin de recevoir un devis interactif en quelques heures.

Dans le tourbillon du développement de nouveaux produits et de la mise sur le marché, la pression pour valider un modèle peut être énorme. Avec le prototypage d’un produit ou d’un composant, les concepteurs transforment leurs projets virtuels et les faisant passer de l’écran à un objet physique. Est-ce qu’il est adapté ? Fonctionne-t-il comme prévu ? Une pièce imprimée en 3D peut-elle être fabriquée par moulage par injection ? Et dans le cas des prototypes plutôt que des pièces de production, que vont en penser les clients éventuels ?
Sous la pression d’éléments fonctionnels du prototype ou de son esthétique, il est possible deperdre de vue leproduit final. Si vous visez un prototype, vous obtiendrez un prototype, voire plusieurs au fur et à mesure de la progression du modèle.
De plus en plus, les fabricants et leurs équipes de conception regardent au-delà de la phase de prototypage lors de la conception du produit, et réfléchissent en termes de produit final et de caractéristiques désirées.
L’objectif : des prototypes qui vont plus loin que des représentations physiques du modèle, et qui vont aplanir le chemin vers la production finale en fournissant des informations précieuses sur les performances et la conformité du produit.
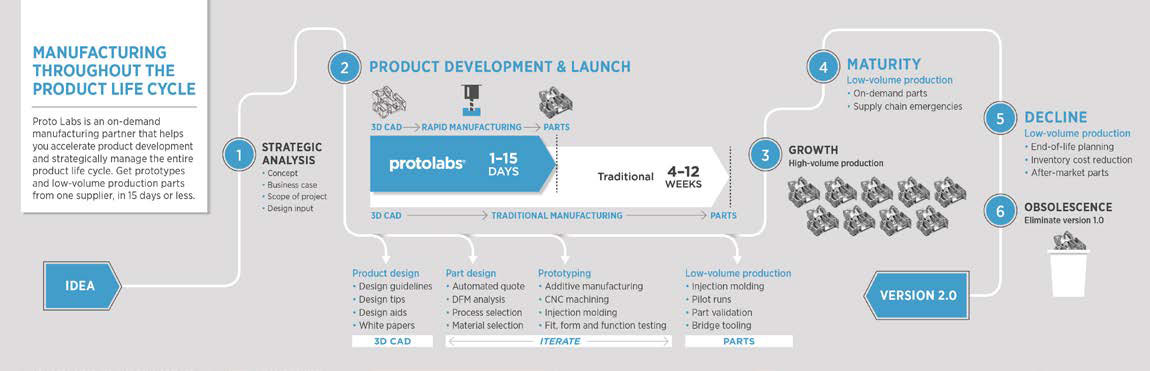
Dans le cycle de développement, les pièces ou produits passent par trois phases successives : d’abord le prototypage ; ensuite, la production en petite série ; et finalement la production en série.
Le prototypage consiste à cristalliser un modèle éprouvé qui fonctionne. Un prototype peut être l’une de plusieurs itérations de ce type, ou simplement une validation finale d’un modèle sur écran. D’autre part, une production en petite série concerne moins le produit lui-même que son processus de production ou de mise sur le marché : cette phase peut aider à améliorer un processus de fabrication, ou bien mettre des produits test sur le marché pour évaluer ou valider la perception des clients. Finalement, les volumes précis
associés à une production en série vont dépendre du produit lui-même et de son marché et varieront en général entre quelques milliers et plusieurs millions par an.
Dans chaque cas, l’objectif est de passer sans encombre d’une phase de développement à l’autre, en améliorant le produit et sa facilité à être produit. Dans l’ensemble, l’objectif consiste à minimiser la durée et le coût total du processus, en amenant le produit de l’idée initiale à la production en série de manière efficace, sans à-coups, aussi rapidement et économiquement que possible.
Dans certaines industries, amener un produit sur le marché demande des tests exhaustifs de conformité, impliquant souvent une certification tierce. Les développements pour l’aérospatiale et la défense, par exemple, demandent un tel niveau de conformité qu’aucun fabricant ne désire achever la conception et passer à la production en série pour découvrir que son produit n’est pas conforme aux exigences en termes de durabilité, cycles d’utilisation ou autres attributs pouvant être testés. Utiliser l’étape de prototypage pour effectuer ces essais - un processus appelé tests de pré-conformité semble donc plus prudent. Dans de telles circonstances, il est judicieux pour le concepteur de demander conseil au fournisseur de prototype qu’il utilise une matière qui apportera des informations précieuses sur des caractéristiques comme la résistance, la flexibilité et la durabilité.

Pour finir, parallèlement à ces étapes de développement et de tests pour mettre un produit sur le marché, un fabricant peut désirer prendre en compte un grand nombre de considérations commerciales. Les décisions sur l’emballage, par exemple, peuvent avoir des conséquences en termes de coûts, de vulnérabilité pendant le transport, et d’encombrement volumique aussi bien des emballages primaires que secondaires. Et bien entendu, l’encombrement volumique affectera les besoins en véhicules et conteneurs, ainsi que les coûts de transport.
Il est donc prudent d’utiliser, à chaque fois que c’est possible, des prototypes du produit pour orienter de manière précoce les décisions d’emballage.
De même, une entreprise peut avoir des objectifs de respect de l’environnement et d’image de marque qui viennent compléter ceux de l’emballage et du transport. L’utilisation d’un moyen particulier d’emballage peut notamment avoir un impact sur les taux d’endommagement, ou sur l’esthétique du produit restant longtemps en stock. Pouvoir recycler des volumes importants de plastique peut être complexe lors du moulage par injection d’une pièce spécifique. La sous-traitance des prototypes et pièces de production dans des pays lointains peut dégrader l’empreinte carbone d’une entreprise tout en entraînant des coûts supplémentaires.
La qualité, la fiabilité et la solidité d’une entreprise sont d’autres considérations importantes. Des compromis sont généralement envisageables : le fournisseur de prototypes le moins cher ne sera pas forcément le plus rapide, ni meilleur en termes de qualité. Le maintien d’une relation commerciale étroite avec un fournisseur de prototypes devient une considération stratégique pour de nombreuses entreprises ; on préfère externaliser auprès d’un fabricant recommandé, qui deviendra un partenaire capable de satisfaire non seulement les besoins en prototypes, mais aussi la production en petite ou moyenne série. Ces fournisseurs offrent une assistance qui comprend parfaitement le besoin d’une analyse de faisabilité qui est essentielle pour écarter toute difficulté de fabrication.
En conclusion, la mise sur le marché réussie d’un nouveau produit peut faire appel à une approche multi-facettes de conception et de développement, incluant un large éventail de problèmes, priorités et compromis. Cet article présente la façon dont une approche intelligente de stratégie de prototypage peut aider à chaque phase du processus de développement. L’objectif : une approche qui raccourcit la durée totale de développement et met sur le marché un meilleur produit avec de meilleures performances, pour un coût total de développement moindre.

CONSIDÉRATIONS DE PROTOTYPAGE AUX PREMIERS STADES DE LA CONCEPTION
Au cours des étapes initiales, le processus de conception vise à combiner les exigences de la Voix du Consommateur (VOC), de la Voix du processus (VOP), qui spécifie les capacités actuelles de fabrication et d’externalisation, ainsi que toutes les exigences d’investissement connues et de la Voix des affaires (VOB) qui détaille les exigences et barrières en termes de retour sur investissement, ventes, commercialisation et exploitation. Les prototypes représentent un investissement important pour les équipes de R&D.
Les prototypes représentent un investissement important pour les équipes de R&D. Quand c’est possible, les fabricants se tournent de plus en plus vers des techniques de prototypage rapide pour raccourcir la durée de développement et réduire les risques en utilisant des technologies comme:
- L’impression 3D
- Multi Jet Fusion (MJF)
- Frittage sélectif par laser (SLS).
- Stéréolithographie (SL)
- Frittage laser direct de métal (DMLS) - L’usinage à contrôle numérique
- Le moulage par injection
Les quantités de prototypes peuvent aller d’un seul par itération, à des centaines, voire des milliers selon les exigences du produit et du projet. Ceci dit, la plage habituelle est entre un et cinq pour la conception initiale, en utilisant l’usinage CNC ou l’impression 3D, jusqu’à quelques centaines en moulage par injection rapide. Toutefois, il ne faut pas réduire ces technologies au seul prototypage. En effet, lorsqu’il ne faut que quelques pièces ou composants, l’impression 3D, l’usinage CNC ou le moulage par injection sont couramment utilisés pour fabriquer des pièces de production.
Chaque technologie de fabrication demande des compromis. La vitesse, le coût et le niveau d’information utile pouvant être fournie par un prototype sont tous pris en compte à la première étape du projet. Les prototypes sont souvent fabriqués en utilisant différentes matières et différents processus qui seraient mis en oeuvre pour la production finale (plastiques d’impression 3D par exemple), et sont tout à fait en mesure de fournir des informations sur l’adaptation, la fonction et l’esthétique. Pour certains projets, notamment pour les dernières itérations de prototypes, les fabricants demandent des pièces de pré-production qui simulent le produit final, en utilisant les mêmes matières et le même processus de fabrication.



CONSIDÉRATIONS DE PROTOTYPAGE POUR LE PASSAGE À LA PRODUCTION EN PETITE SÉRIE
Une fois les prototypes validés en termes d’adaptation, de forme, de fonction et esthétique, le développement peut passer à la production en petite série, avec une chaîne logistique d’approvisionnement à la demande, ou bien avant de lancer une production en grande série. Cette étape de fabrication consiste à produire des lots de pièces, allant de 50 à plusieurs centaines voire plusieurs milliers, prévus pour répondre à une demande commerciale fluctuante. De plus, pour certains projets, la production en petite série peut déjà être la véritable méthode de production.
La stratégie de développement régira la vitesse à laquelle le fabricant veut passer à la production en petite série et quelle sera la durée de cette étape de production. Une telle stratégie doit prendre en compte l’échelle d’une telle production, car en termes de moules, des lots de 50 pièces présentent des contraintes différentes de lots de plusieurs milliers. Le point essentiel pour cette étape est d’obtenir des pièces qui fournissent des informations utiles en termes d’adaptation, de forme et de fonction, tout en étant optimisées pour la faisabilité de production. Une fois encore, avoir un prototype physique qui confirme qu’une pièce ou un produit remplira bien sa tâche est une chose différente que d’avoir un prototype dont les moyens de production ont été optimisés en termes de faisabilité.
Pour la production en petite série, un objectif primordial de la faisabilité de fabrication est de fignoler la conception de telle sorte que les moules puissent être usinés de manière plus rapide ou plus économique, voire les deux. Une fois pris en compte les problèmes de moule, un fabricant désirera généralement obtenir une meilleure aptitude au moulage. On peut citer l’angle de dépouille du moule, dont une légère modification permettra une amélioration notable de l’éjection de la pièce, et donc à la fois un meilleur état de surface et une meilleure qualité.
Comment réussir à atteindre cet objectif ? Dans un monde idéal, le choix par un fabricant de son fournisseur de prototypes et de petites séries de pièces tiendra compte de ces exigences. Il aura en effet sélectionné un partenaire qui peut lui apporter à la fois les compétences de ces ingénieurs d’applications, ainsi que des outils automatiques qui peuvent élaborer une analyse de conception initiale, sans intervention humaine.
En fait, dans de nombreux cas, les outils automatiques d’analyse de conception ont prouvé qu’ils peuvent offrir un degré d’optimisation parfaitement adapté à une production en petite série. Lorsque ces outils sont disponibles sur des puissants serveurs en grappes, cette optimisation peut être rapidement obtenue dans le processus de production, ce qui est généralement important, car une mise rapide sur le marché reste un objectif primordial.
Chez Protolabs, par exemple, lorsque des concepteurs téléchargent un modèle CAO 3D sur le site web, un devis est envoyé en quelques heures, et souligne les sections de la pièce qui ont besoin d’un angle de dépouille, ou même suggèrent des modifications pour améliorer cette dépouille.
CONSIDÉRATIONS DE PROTOTYPAGE POUR LE PASSAGE À LA PRODUCTION EN SÉRIE
Le passage à la production en série pose de nouveaux problèmes qu’une stratégie intelligente doit prendre en compte. Une considération essentielle concerne la vitesse à laquelle un produit donné va passer à la production en série - dans le cas où ce produit est simplement une nouvelle itération d’un concept éprouvé existant, la période de fabrication en petite série peut être minimale, ou alors une approche pour passer en production à la demande, permettant un développement continu du produit tout au long de son cycle de vie. Dans de telles circonstances, il est important pour le prototype de démontrer rapidement la faisabilité de la production en série, car le produit passera moins de temps en phase de validation de petite série qu’il ne la fait dans le tout premier lot de production. Ainsi, tandis que les premiers prototypes peuvent mettre en oeuvre des techniques rapides comme Multi Jet Fusion, le Frittage laser direct de métal, la Stéréolithographie ou le Frittage laser sélectif, il sera judicieux pour les prototypes suivants d’utiliser l’usinage CNC ou le moulage par injection, cohérent avec la technologie de production en série prévue.



Et comme pour la production en petite série, il est préférable de s’adresser à un fournisseur de prototypes à fortes capacités - aussi bien automatiques qu’humaines - pour l’ingénierie d’applications. Avec la production en série, il ne s’agit plus simplement de fabriquer un produit, mais plutôt de rechercher activement une optimisation de la conception permettant sur une longue période de production. Avec une telle optimisation, les fabricants peuvent obtenir des améliorations importantes en termes de rendement, consommation de matières, fréquence d’éjection et finition de surface en affinant une conception pouvant avoir parfaitement fonctionné en petite série, mais qui offre encore la possibilité d’améliorations à long terme.
Les initiatives d’allègement par exemple contribuent non seulement à une réduction de poids, une caractéristique précieuse dans de nombreuses applications - mais peuvent également réduire la consommation de matière et donc les coûts : une règle empirique dit que l’épaisseur optimale des parois des pièces thermoplastiques se situe dans une plage de 1 à 3,5 mm (pour l’ABS), à respecter sur l’ensemble de la pièce. En d’autres termes, des parois plus minces ne réduisent pas seulement les coûts grâce à la réduction de matière, mais aussi grâce à une faisabilité accrue de la pièce. Des sections très épaisses, par exemple, peuvent à la fois augmenter la probabilité de défauts esthétiques comme les retassures et la probabilité de pertes de rendement par déformation pendant le refroidissement. Une attention particulière portée aux rayons d’angle, notamment pour les moules en aluminium, est une bonne manière d’améliorer le rendement sur une longue période de production.
En production en série également, il existe des possibilités de moules multicavités ou moules multipièces pour fabriquer des pièces multiples en un seul cycle d’injection. Les moules multicavités permettent de fabriquer en une seule injection plusieurs pièces identiques ; les moules multi-pièces permettent d’injecter plusieurs pièces différentes. Si cette option semble viable, les experts techniques de Protolabs recommandent généralement de tester la pièce dans un moule mono-cavité, avant de s’engager dans des dépenses supplémentaires pour un moule multicavités ou multipièces.
Une fois la synthèse faite : la vision d’ensemble
La pression pour la mise sur le marché de nouveaux produits le plus rapidement possible peut être très forte. Et dans ce cas, la pression pour fabriquer des prototypes peut être également énorme. Mais prendre un peu de recul en pensant tout d’abord au produit final - et à ses exigences de production et d’essai - peut être bénéfique aussi bien en termes de calendrier que de coûts d’ensemble. Et théoriquement, on récolte aussi des bénéfices de rendement, coût et performances du produit. Si l’on inclut les considérations annexes comme l’emballage, les bénéfices apportés sont encore plus convaincants. Pour être efficace, une stratégie de prototypage doit prendre un peu de temps aux premières étapes du processus de développement. Il s’agit d’un investissement et non d’un coût. Un investissement qui pour être bref, garantira un meilleur produit, avec de meilleures performances, développé à des coûts réduits avec des délais d’ensemble plus courts.
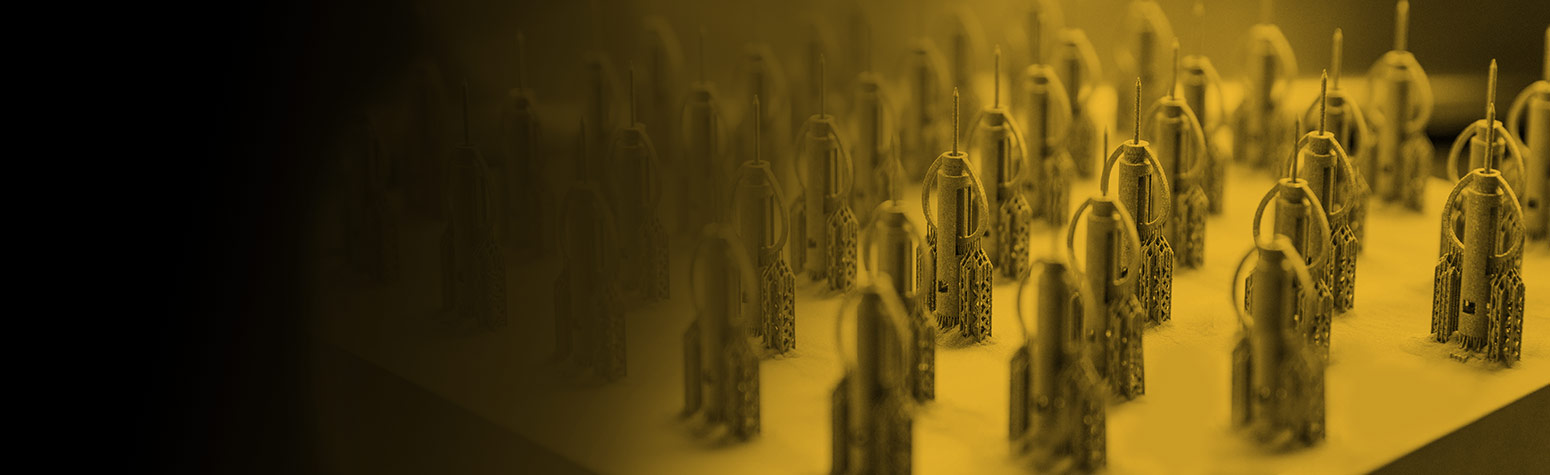