Surgical instruments, aids and models and the role of digital manufacturing
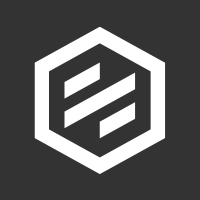

Digital manufacturing is revolutionising surgery. It provides both surgeons and instrument manufacturers with the information and equipment that they need to achieve better results faster and more cost effectively.
In this blog we take a look at how it is transforming three critical areas:
- its use in pre operation modelling for planning;
- the development of bespoke instruments;
- the development of new disposable surgical equipment.
Anatomical models and templates
The development of anatomical models and patient specific templates to aid surgery starts with digital information, in this case from a scan.
Such models of a patient help medical professionals with preoperative planning, intraoperative visualisation, and the sizing of medical equipment for procedures. They are also used to train medical students and to discuss the operation with patients beforehand. Research has shown that using such models has increased patient consent because it aids their understanding.
3D printing significantly reduces the cost of producing these models which makes it an increasingly viable option.
Using the data from CAT scans to create a CAD, 3D printing can also produce specific surgical guides for a patient to help make surgery faster and reduce errors.

Customising surgical instruments
Creating such single-use, procedure-specific, surgeon-matched tools requires a fast response between surgeon feedback and product development. This is where 3D printing can make a real difference using both digital data from scans and feedback from surgeons to reduce development and production times. It is helping drive forwards a new era of customised patient and surgeon centric medicine at a cost-effective price. Ultimately as technology progresses, we will see surgeons freed up from traditional trays that are typically only updated every few years.
These customised 3D-printed surgical instruments such as scalpel handles, forceps or clamps help surgeons perform better and reduce operating time leading to better outcomes for patients.

Reducing development time for disposable surgical equipment.
Another area of huge demand is for single use instruments. Prepackaged, individually wrapped and pre-sterilized, single-use devices offer a convenient, off-the-shelf option.
An obvious benefit for hospitals is that they do not require sterile processing, which can be costly and time-consuming.
The challenge for instrument manufacturers is how to develop new instruments that will meet the rigorous requirements of the medical industry quickly and cost effectively.
The first step is to ensure that the design is manufacturable using your chosen production process. The secret to managing the process quickly and efficiently starts with your CAD.
At Protolabs we have automated this step so that when you upload your CAD into our quoting platform you will get a free analysis alongside a quote within a few hours. If after uploading your CAD you need additional assistance then you can take advantage of our consultative design service where one of our engineers will help you optimise your design for injection moulding.
The next step is prototyping and feasibility testing to check functionality. This may require several iterations in your design. In the early stages you may use rapid prototyping technologies such as 3D printing. But a word of warning; you need to keep sight of what your final production method will be and keep any future iterations manufacturable using this technology.
You will also need to get regulatory approval and this may involve ramping up the number of products you require. For injection moulding it is possible to keep the part cost down during this process and still achieve what you need rapidly – by which we mean getting your parts within 10 -12 days. How is this possible? The answer is by using aluminium moulds instead of steel.
The chances are that you may need to use different technologies for different phases of prototyping and product development; read our whitepaper “Rapid Prototyping Processes” to find out more.
When you are finally ready for production the volume you need will determine the production process. If it is a few hundred then 3D printing or CNC machining could be the answer. When you get up to a few thousand then consider rapid injection moulding such as our on-demand service.
For mass production, where you need hundreds of thousands of parts then you will probably need steel tooling for injection moulding. But even here you could use our on-demand service to bridge the production gap while you wait for the final production tools. This will help you get your product to market faster and earn revenue more quickly.
Digital manufacturing is connecting everyone in the supply chain for surgical instruments and aids. It means that manufacturing is more responsive to the needs of surgeons and patients to deliver products geared to specific needs faster than ever before. This in turn improves patient outcomes and this trend is set to continue as the technology develops, which has got to be good news for all of us.

Thank you for downloading our guide on digital manufacturing for the medical industry. If you have any issues getting your guide, click here to download.