Trending Topics in Manufacturing: Taking the Pulse of the Industry

For a sector in a state of rapid reinvention, the manufacturing industry is increasingly looking for new solutions to stay competitive. In 2025, there are mounting pressures on supply chains, and economic uncertainty is keeping manufacturing investment lower than in previous years. Be that as it may, tough conditions are where innovation thrives. Find out which matters are top of mind for manufacturing leaders today, and how they’re rising to the challenges.
Increased Digitalisation Across the Board
Various approaches to digital optimisation are in play as manufacturing undergoes major change. More and more companies are incorporating new technology and applying data-driven insights into their manufacturing operations.
In fact, the manufacturing industry is using data like never before. Aptean’s Manufacturing Trends & Technology Report concludes that “52% of manufacturers plan to implement emerging technologies and data solutions in 2025, while 48% aim to update or integrate their legacy systems.”
Recent advancements in data analytics are giving users more information and better value information, helping them become more agile, identify cost-saving opportunities and constantly innovate during turbulent times. Following the automotive industry’s success with high-tech solutions that measure the performance of fleets of vehicles, manufacturing has been alerted to the benefits of predictive maintenance and optimised processes. Then there’s the increased availability of smart factory software and after-market sensors, which are simultaneously becoming more affordable, providing more reliable data and helping businesses to lower their costs.
The Big One – Where Are We at with AI?
The manufacturing industry is becoming one of the most significantly affected by artificial intelligence (AI). Many different industries have quickly embraced AI, driven by the cost and labour-saving potential of the new technology. Manufacturing was no exception. According to the World Economic Forum, 68% of manufacturers across all sectors have implemented some form of AI in their operations.
But as the initial excitement has somewhat lessened, research by Deloitte shows that businesses have moved their focus towards critically analysing how AI can contribute to revenue goals, improve productivity and replace repetitive manual processes. Organisations will look to generative AI to speed up their manufacturing processes. According to a recent article by Forbes, “by leveraging the power of generative design, it will be possible to create stronger, lighter components that make more efficient use of available materials.”
In the world of additive manufacturing, “3D printing is capitalising on the excitement around next generation AI and automation tools,” says François Minec, Global Head of 3D Polymers, HP Personalization and 3D Printing at HP in the Protolabs 2024 3D Printing Trend Report. “Advancements in 3D hardware, firmware, and software are bringing data analytics and KPI monitoring to the forefront, enabling scalability for even more manufacturers.”
While over at NASA, crowdsourced generative design helped engineers to significantly speed up their product development process.
Going forward, businesses will be weighing up which AI practices have the biggest return on investment. “The future of manufacturing isn't just about automation and AI – it's about creating smarter, more sustainable, and more adaptive production systems”, says Forbes.
The Complex One – Strengthening Supply Chains
Addressing supply chain complexities is high on the list of considerations for innovative companies right now. More and more manufacturers are taking steps to mitigate risks and protect supply chains from vulnerabilities and costs associated with things like tariffs.
Organisations are also embracing data in new ways to help drive supply chain decision-making. Recent technological developments include data-driven inventory management, more accurate forecasting with real-time data and automation opportunities, which help businesses to adapt their supply chains in accordance with market conditions.
“Manufacturers can use data to more quickly adapt to the uncertainties of the supply chain landscape and work to minimise disruptions, which continue to be unpredictable. Utilising the blockchain to manage this data brings traceability, while the advent of real-time supply chain tools can help manufacturers stay on top of everything”, ATS reports.
The speed and flexibility inherent within Protolabs’ distributed manufacturing model provides an ideal solution for lessening the impact of global and economic shifts. Read more about onshoring and navigating supply chain disruptions with digital manufacturing.
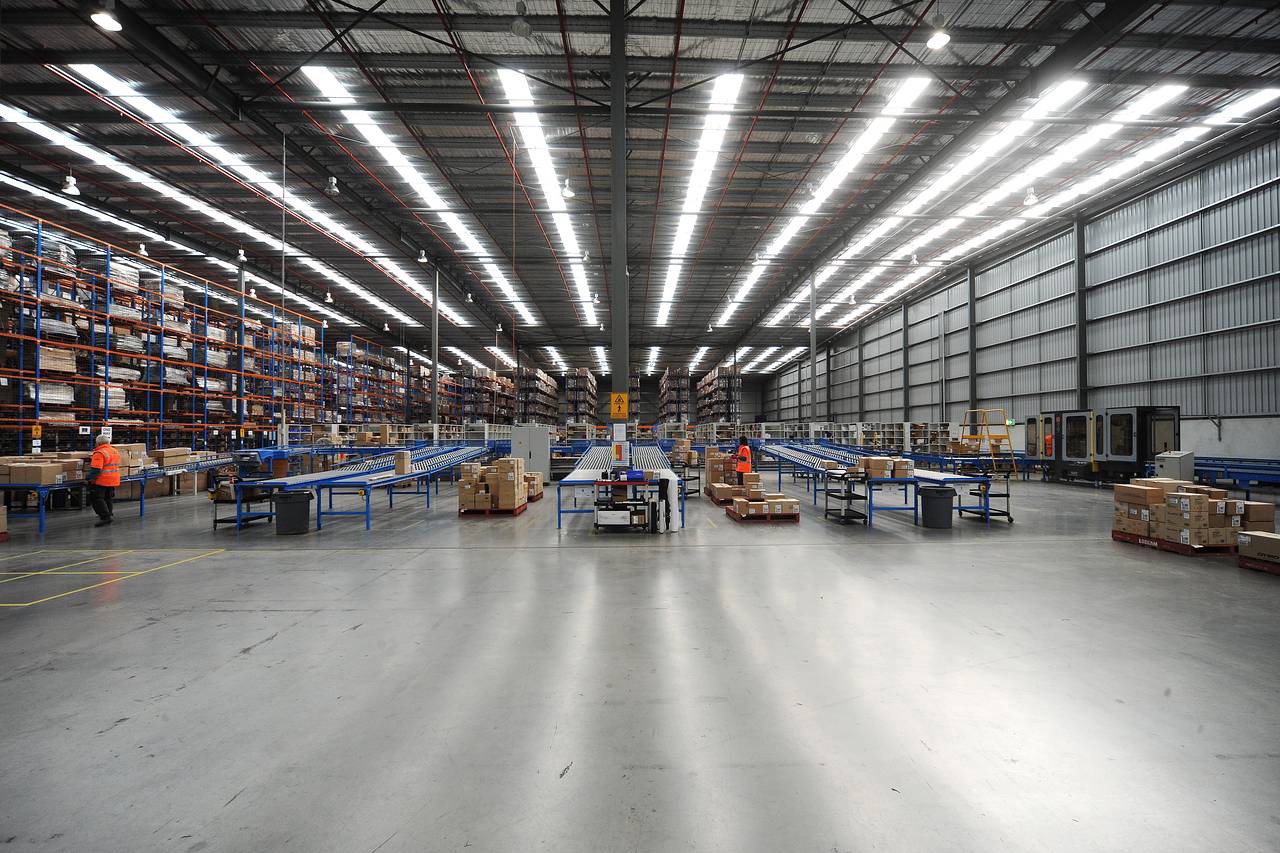
The Green One – Sustainability
As climate change grows increasingly urgent, so does pressure to manufacture more sustainably. For those wondering whether reduced manufacturing investment will see companies put sustainability initiatives on pause, in general this is currently not the case. According to Deloitte’s 2025 Manufacturing Industry Outlook, strong investment in clean technology manufacturing continued throughout 2024, but has decelerated since 2023.
At the same time, customer demand for lower-emission products remains steady, and green manufacturing will continue to serve that need. For example, the electric vehicle market alone is expected to reach $5 trillion by 2030. “Customers seem to remain intent on lowering their operating emissions, which should continue to drive demand for lower-emission products,” Deloitte reports.
Companies are thinking strategically when it comes to green manufacturing, considering options such as recycled materials, which offer mechanical properties similar to traditional materials, and adopting lean manufacturing practices.
The Humanoid One – Working with Robots & Cobots
Manufacturing was one of the first industries to integrate robots into its daily operations. Thanks to recent advancements in industrial robotics, now they’re more capable of working alongside human counterparts. Robots can work around the clock, be configured to achieve high levels of consistency, and avoid instances of human error.
While their introduction initially raised concerns about replacing human labour, in actuality, they’re more likely to support it. Using top-of-the-range sensors and AI motion control, collaborative robots or “cobots” are being used for repetitive or hazardous tasks, filling gaps in the workforce and increasing productivity as a result.
The Safety One – Cybersecurity & Data Protection
As all of this digitalisation takes hold, maintaining and protecting data systems is more important than ever. Manufacturing will likely seek to improve its data management and cybersecurity, especially as it becomes increasingly reliant on AI.
The World Economic Forum reports that the manufacturing industry has been a top target for cybercrime in recent years, and the threats remain present.
“The transition from isolated systems to interconnected ones alongside the rise of the internet and then cloud computing has heightened cybersecurity challenges for industrial organisations. The result is that cyber risk is systemic, contagious and often beyond the understanding or control of any single entity.” In response, organisations are prioritising the implementation of robust cyber resilience practices.
Where to From Here
A conclusion from the World Economic Forum’s Annual Meeting 2025 compares the “pivotal moment” manufacturing is currently experiencing with the rise of the internet a generation ago. “We are witnessing the emergence of a new industrial paradigm where sustainability, intelligence and resilience are not competing priorities, but mutually reinforcing strengths.”
Along with the pressures of transformation, and heightened focus on resilience, adopting digitally innovative manufacturing practices will enhance operational efficiency, promote environmentally responsible practices and see the sector go from strength to strength.