
9 conseils pour réduire les coûts de moulage par injection
Faites des économies en appliquant ces quelques conseils de conception pour le moulage par injection
Tout le monde désire réduire les coûts de fabrication de ses pièces. Rien de plus simple à première vue. Pour réduire le coût unitaire des pièces moulées par injection, l’un des moyens les plus faciles consiste à augmenter la quantité de pièces fabriquées. En effet, les coûts initiaux de conception et d’usinage du moule s’amortissent sur la quantité de pièces produites.
Vous n’envisagez de mouler qu’une toute petite quantité de pièces? Pas de problème. Protolabs fabrique des moules économiques pour des séries de seulement 25 pièces, en seulement quelques jours après votre commande.

Hormis le coût unitaire, vous devez aussi tenir compte du matériau. De nombreux plastiques présentent des fonctionnalités et une résistance mécanique similaires, mais certains d’entre eux sont naturellement plus faciles à mouler. Vous pouvez expérimenter différents matériaux sur le devis interactif que vous recevez lorsque vous téléchargez votre conception sur le site de Protolabs.
Voici neuf règles de conception pour le moulage par injection qui vous permettront de diminuer vos coûts de fabrication :
1. Supprimez les contre-dépouilles
2. Débarrassez-vous des éléments superflus
3. Privilégiez une approche à empreinte centrale
4. Soyez attentif à vos choix de finition
5. Concevez des pièces appariées
6. Modifiez et réutilisez les moules
7. Exploitez au maximum l’analyse de faisabilité
8. Utilisez un moule multi-empreinte ou un moule famille
9. Tenez compte de la taille de la pièce
Contre-dépouilles
Les éléments à contre-dépouille rendent l’éjection de la pièce difficile, voire impossible. Si vous le pouvez, supprimez-les. Mais cela n’est pas toujours possible, notamment si vous avez besoin d’un tiroir ou d’un insert manuel. Une solution peut consister à utiliser des noyaux traversants ou à modifier le plan de joint et les angles de dépouille pour que le moule soit plus simple à fabriquer. Outre l’augmentation des coûts de fabrication liée à l’utilisation d’inserts manuels, cela peut également se répercuter sur votre prix unitaire du fait de l’allongement des temps de cycle et du fonctionnement manuel du moule.

Éléments superflus
Les surfaces texturées, les références d’article moulées et les logos sont certes « tendance », mais sachez que ces éléments non indispensables vous feront débourser un peu plus. Cela dit, les références d’article permanentes sont obligatoires pour de nombreuses applications aéronautiques et militaires. Utilisez une police qui convient au fraisage, comme Century Gothic Bold, Arial ou Verdana (polices sans-sérif), choisissez une taille supérieure à 20 pt et n’allez pas au-delà de 0,25 mm à 0,38 mm de profondeur. Sachez aussi que vous devrez augmenter la dépouille si l’éjection de la pièce pose problème.
Empreinte centrale
Si vous avez besoin d’un boîtier électronique ou d’une pièce de forme similaire, vous pouvez soit creuser des empreintes profondes pour former les parois dans la base du moule, ce qui nécessite des outils longs et fins pour usiner des nervures dans le moule, soit usiner l’aluminium autour du noyau et mouler la pièce autour de celui-ci. Connue sous le nom d’approche à empreinte centrale, cette dernière technique est beaucoup plus économique pour le moulage des parois hautes et des surfaces nervurées. Mieux encore, elle facilite l’obtention d’états de surface lisses, permet un bon dégazage, améliore l’éjection et évite d’utiliser des angles de dépouille très prononcés.
Aspect cosmétique
Les belles pièces sont esthétiques, mais elles nécessitent souvent un microbillage ou un moule à haut poli pour atteindre un haut niveau cosmétique, ce qui augmente les coûts d’outillage. Tout état de surface au-delà d’une finition PM-F0 (après usinage) requiert des opérations manuelles, jusqu’au poli-miroir SPI-A2 avec polissage diamant de qualité 2. Évitez d’utiliser des états de surface aussi fins, à moins que votre application l’exige.
Pièces appariées
Vous concevez un coffret refermable pour des composants médicaux ou deux moitiés d’une radio portative à assembler ? Pourquoi fabriquer deux pièces complémentaires quand vous pouvez n’en fabriquer qu’une seule ? Vous pouvez revoir la conception des attaches pour que les deux moitiés s’assemblent dans n’importe quel sens et fabriquer ainsi une pièce dite « universelle ». Un seul moule suffit, ce qui réduit les coûts de production initiaux. Cette méthode permet par ailleurs de mouler deux fois plus d’exemplaires d’une même pièce (au lieu de deux pièces en deux fois moins d’exemplaires).
Modifications des moules
Il est relativement facile de retirer du métal dans un moule métallique existant. En ajouter, en revanche, peut se révéler difficile, voire impossible dans la pratique, en moulage par injection. Si l’on se place du point de vue de la pièce, on peut ajouter du plastique, mais on ne peut pas en enlever. Lorsque cet aspect est pris en compte dans la conception, on parle de modifications « metal safe ».
Certaines pièces moulées par injection passent par plusieurs itérations, jusqu’à l’émergence d’une conception finale réalisable. Au lieu d’acheter un nouveau moule à chaque révision de conception, une planification mieux pensée vous permettra d’utiliser plusieurs fois le même moule. En partant de la conception la plus petite et la plus basique, moulez autant de pièces que nécessaire ; réusinez ensuite le moule de façon à y inclure des éléments complémentaires ou une version plus grosse et plus haute de la même pièce, puis moulez-y de nouvelles pièces. Ce n’est pas une science exacte, mais si la pièce est bonne, cette technique de réutilisation permet de diminuer les coûts d’outillage.
Analyse de moulabilité
Tous les devis de pièces moulées par injection établis par Protolabs sont accompagnés d’une analyse de faisabilité gratuite. Cette analyse identifie les zones potentiellement problématiques ou les améliorations de conception envisageables. Angles de dépouille insuffisants, éléments non usinables, géométries impossibles : voici quelques exemples de situations où vous pouvez et devez améliorer la conception de votre pièce avant de cliquer sur le bouton Accepter. Lisez ces suggestions attentivement et contactez un expert de Protolabs si vous avez la moindre question sur la conception de votre pièce.
Moules multi-empreintes et moules familles
Vous cherchez peut-être à fabriquer de plus grandes séries ? L’utilisation de moules en aluminium peut toujours vous permettre de fabriquer de grandes séries, avec des moules en aluminium à deux, quatre ou huit empreintes selon la taille et la géométrie de la pièce. Cela peut réduire votre prix unitaire malgré des répercussions sur vos coûts d’outillage.
Vous disposez d’une famille de pièces qui s’assemblent entre elles ? Ou vous envisagez d’effectuer plusieurs moulages simultanément ? Vous n’avez aucune raison de construire un moule pour chaque pièce, mais pour cela, A) toutes les pièces doivent être fabriquées dans le même plastique, B) elles doivent toutes avoir plus ou moins la même taille (par exemple, des temps de traitement similaires) et C) elles doivent toutes entrer dans la même empreinte sans entraver le fonctionnement du moule.
Vous pouvez réunir certaines de ces pièces avec une charnière souple ? Il s’agit là d’un excellent moyen, par exemple, de mouler les deux moitiés d’un récipient double coque. Sans cette solution, il faudrait prévoir un assemblage par goupille pour que ces pièces puissent s’ouvrir et se fermer. La seule consigne à respecter ici est l’utilisation d’un matériau souple et solide, comme le polypropylène (PP).
Taille de la pièce
Dans le même ordre d’idées, tenez toujours compte des limites de votre pièce. En termes de moulage, cela signifie que vous devez évaluer la taille de la pièce et vous assurer qu’elle entrera confortablement dans le moule en laissant suffisamment de place pour les carottes, les canaux d’alimentation, les éjecteurs et tous les autres éléments nécessaires au bon fonctionnement du moule. Chez Protolabs, les dimensions maximales des pièces pour le moulage par injection sont de 480 mm x 751 mm. En fonction de la dimension on peut également aller à une profondeur maximale de 101 mm par rapport au plan de joint. On notera toutefois que des pièces aussi grandes nécessitent un moule plus grand, ce qui peut se répercuter sur vos coûts d’outillage et sur votre prix unitaire.
Comme toujours, si vous avez la moindre question, n’hésitez pas à contacter l’un de nos experts au +33 (0)4 27 50 29 47 ou à l’adresse customerservice@protolabs.fr.
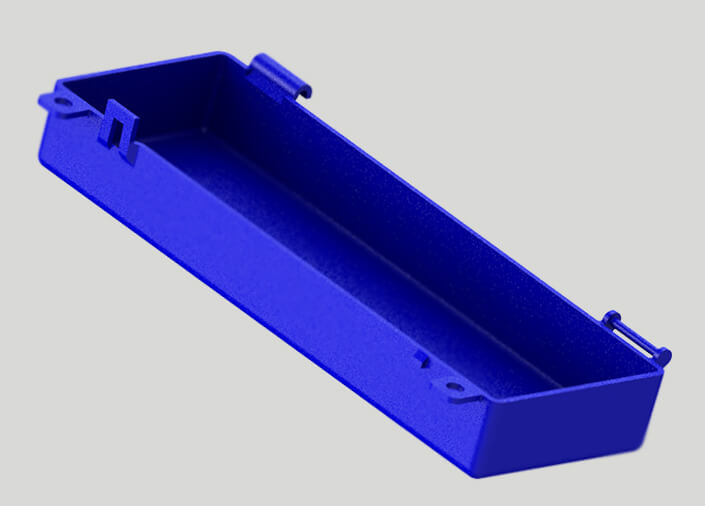
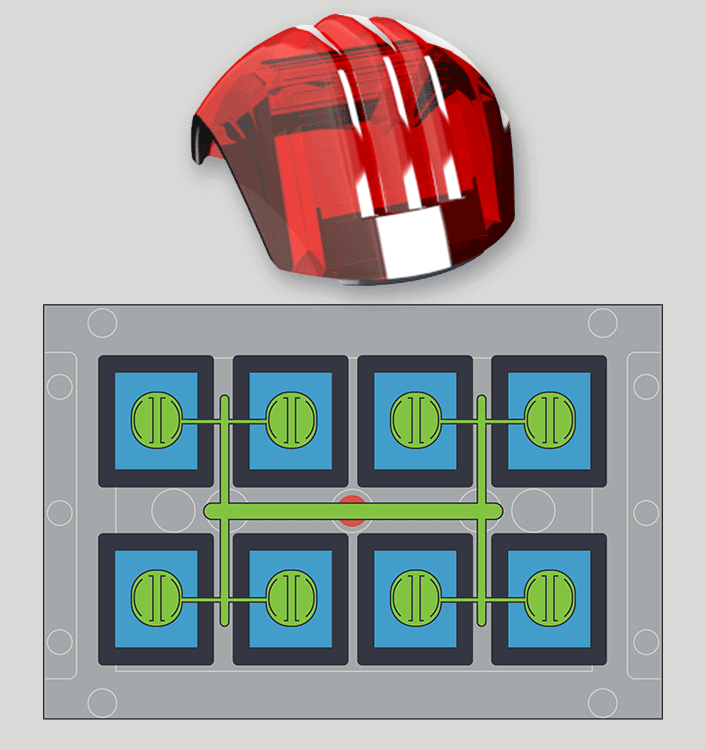
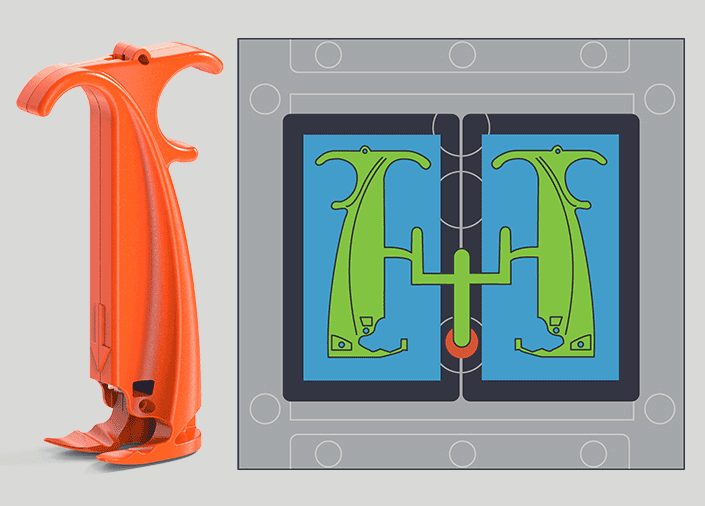