
T+A elektroakustik
Casques d'écoute de luxe développés grâce au service de moulage par injection de Protolabs
Pour mettre au point ses écouteurs de qualité supérieure, T+A elektroakustik fait appel à Protolabs. Les résultats de cette collaboration sont impressionnants : une technologie de pointe créée grâce à des méthodes de fabrication ingénieuses.
Le terme « excellence » est réservé à très peu de produits. Lorsqu'il est question d'excellentes réalisations technologiques et de produits brillamment planifiés et mis en œuvre, on imagine plutôt des produits de luxe, notamment des yachts, des voitures ou d'autres objets de design.
T+A elektroakustik GmbH est une entreprise qui fournit des produits de la plus haute qualité dans son secteur d'activité. Fondée par Siegfried Amft en 1978, cette société basée à Herford emploie près de 80 salariés et s'est fixé pour objectif depuis ses débuts d'offrir à ses clients la meilleure expérience acoustique possible. Les chefs-d'œuvre de cette entreprise Hi-Fi sont principalement distribués en Europe et en Amérique du nord par un réseau de distributeurs spécialisés et bénéficient d'une réputation très spéciale chez les audiophiles.
Cela s'explique notamment par le fait que T+A elektroakustik ne se considère pas comme un fabricant de composants électroniques destinés à une écoute occasionnelle de la musique. Au contraire, conformément à la philosophie de la maison, les salariés se voient comme des scientifiques cherchant à extraire toutes les nuances musicales des matières disponibles, de la technologie de pointe et des derniers progrès de l'électronique.
Un ajout au portefeuille
Pour produire toute la gamme d'équipements électroniques pour le plaisir des oreilles, l'entreprise s'appuie autant que possible sur sa propre expérience et son propre savoir-faire depuis ses débuts. Ainsi, les haut-parleurs, les systèmes audio et les amplificateurs produits par T+A sont conçus et fabriqués de manière indépendante par les salariés de tous les services techniques et électroniques correspondants. Rien d'étonnant donc à ce que l'entreprise emploie ses propres ingénieurs, techniciens spécialisés, experts en acoustique, artisans de production et développeurs de logiciels, qui prennent personnellement en charge près de 90% de la conception, du développement, de la production, de l'assemblage et de la finition dans sa propre usine.
Le fait que les salariés constituent l'un des principaux atouts de l'entreprise, ainsi que leur passion commune pour une expérience d'écoute optimale, est également illustré par leur ancienneté au sein de cette dernière. « Le taux de renouvellement du personnel est très faible chez T+A elektroakustik » nous confie Sebastian Kobelt, ingénieur de conception et chef de projet chez T+A elektroakustik GmbH. « Certains de nos collaborateurs sont en poste depuis plus de 20 ans et de ce fait, ils ont accumulé de nombreuses connaissances. Bien entendu, cela nous aide énormément à développer de nouveaux appareils. »
Pour compléter sa gamme existante de produits, T+A a décidé en 2019 de mettre en œuvre une idée qui était en germe depuis un certain temps. Un casque répondant aux critères de qualité habituels de T+A qui permettrait aux audiophiles, qui veulent s'adonner à leur hobby sans gêner leur entourage, de profiter des équipements Hi-Fi haut de gamme de T+A elektroakustik. Pour produire ce son remarquable, il fallait parvenir à faire de la place pour un diaphragme complexe et sophistiqué, en plus des autres composants critiques. Ainsi, il apparut très clairement dès la phase de planification de ce produit exceptionnel qu'est le Solitaire, que les méthodes de production conventionnelles ne suffiraient pas.
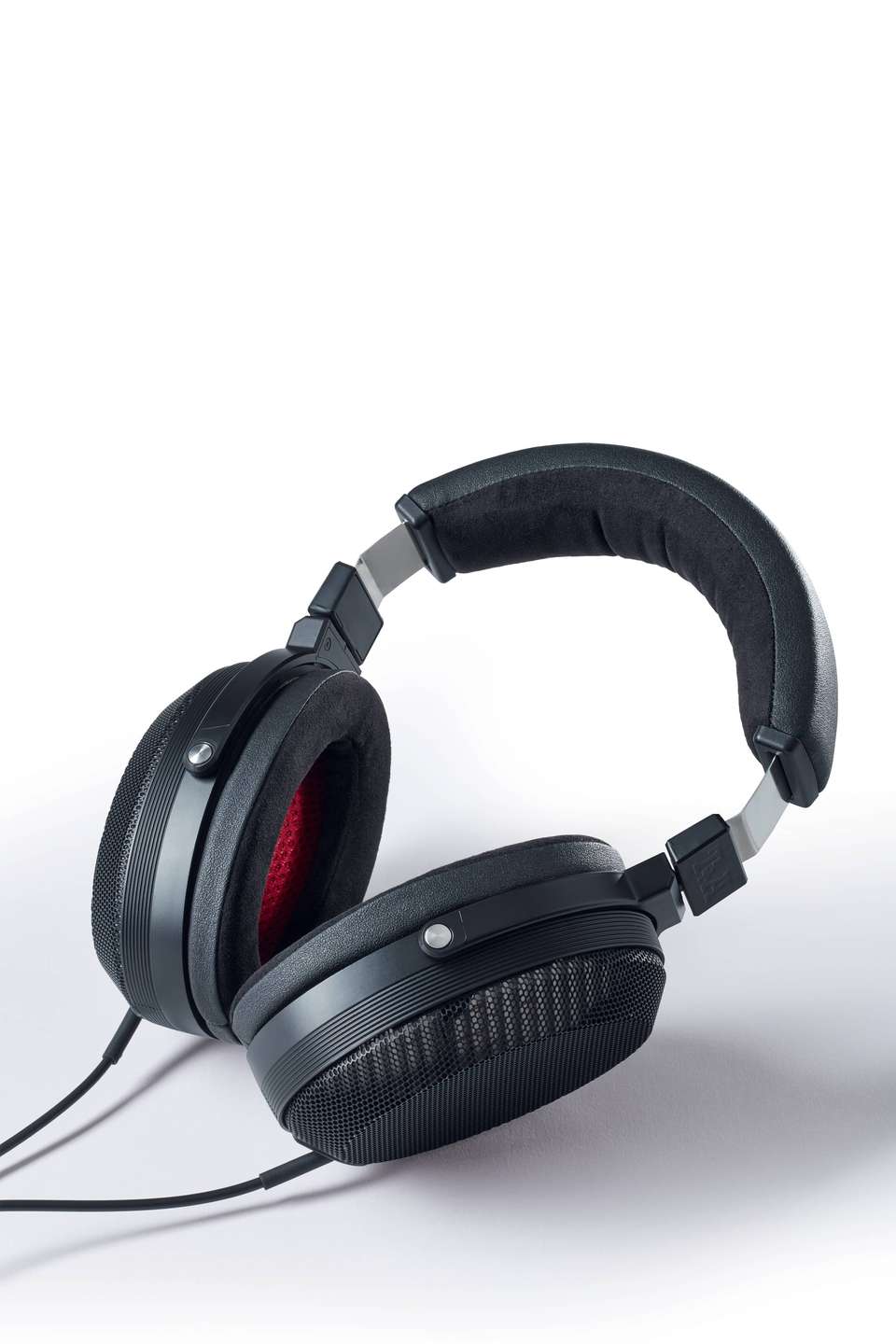
Résumé |
---|
Développer deux paires d'écouteurs à la pointe de la technologie, fondés sur les principes du luxe et de la qualité audio, qui utilisent des composants de haute qualité.
T+A elektroakustik devait trouver un moyen de créer une coque de casque conforme à la vision de qualité et de luxe du projet, tout en accueillant les aimants et les diaphragmes qui constituent les composants internes du casque. La société s'est tournée vers le service de moulage par injection de Protolabs pour créer les pièces nécessaires au projet.
En travaillant ensemble, Protolabs et T+A elektroakustik ont développé deux paires d'écouteurs différentes qui nécessitaient toutes deux des approches uniques. Le résultat ? Deux appareils haut de gamme qui établissent une nouvelle norme en matière de qualité audio. |
Assistance au développement de produit et à la production en série
Pour pouvoir concrétiser sa vision des casques Solitaire sans renoncer à la qualité et à la performance, T+A a donc décidé de se mettre en quête d'un partenaire adéquat capable de l'aider à fabriquer la coque du casque. Les premiers prototypes se composaient d'une pièce unique en aluminium dont la conception complexe empêchait la fabrication par fraisage CNC. La seule option était la fabrication additive et il fallut envisager une collaboration avec un fournisseur de services de production qualifié.
« Lors de la sélection d'un partenaire, il était important pour nous de pouvoir choisir parmi un large éventail de matières. De plus, nous tenions à disposer de la possibilité d'utiliser des pièces moulées par injection pour réaliser une production en série dès la fin de la phase de prototypage », explique Kobelt. « Protolabs remplissait toutes ces exigences, et c'est pourquoi il nous a été facile de les choisir comme partenaires de fabrication. »
Outre le casque original haut de gamme, le Solitaire P, qui se distingue par son boîtier en aluminium, une version un peu plus économique, le Solitaire P-SE, a été prévue dès le début. Ce dernier devait être fabriqué en plastique ABS, PCABS et nylon et étoffer la gamme de produits de luxe du fabricant avec un modèle d'entrée de gamme pour accompagner le Solitaire P.
« L'un des critères décisifs pour le Solitaire P et le Solitaire P-SE était que les composants utilisés devaient être les plus homogènes possible. Les différences devaient être réduites au minimum, car un grand nombre de composants importants devaient tenir dans un espace très réduit », souligne Viktor Pöss, responsable de compte chez Protolabs. « Le défi de ce projet n'était pas tant dans la conception des composants, qui avait été déjà brillamment résolue par T+A. »
Si la coque en aluminium de l'écouteur du Solitaire P a été fraisée en moins d'une heure et si Protolabs a également fourni d'autres composants mineurs au projet, la mise en œuvre du Solitaire P-SE s'est avérée bien plus difficile.
"L'interaction humaine et la compétence des employés de Protolabs - tant en termes de compréhension de l'ingénierie que de préoccupations administratives - sont convaincantes, purement et simplement".
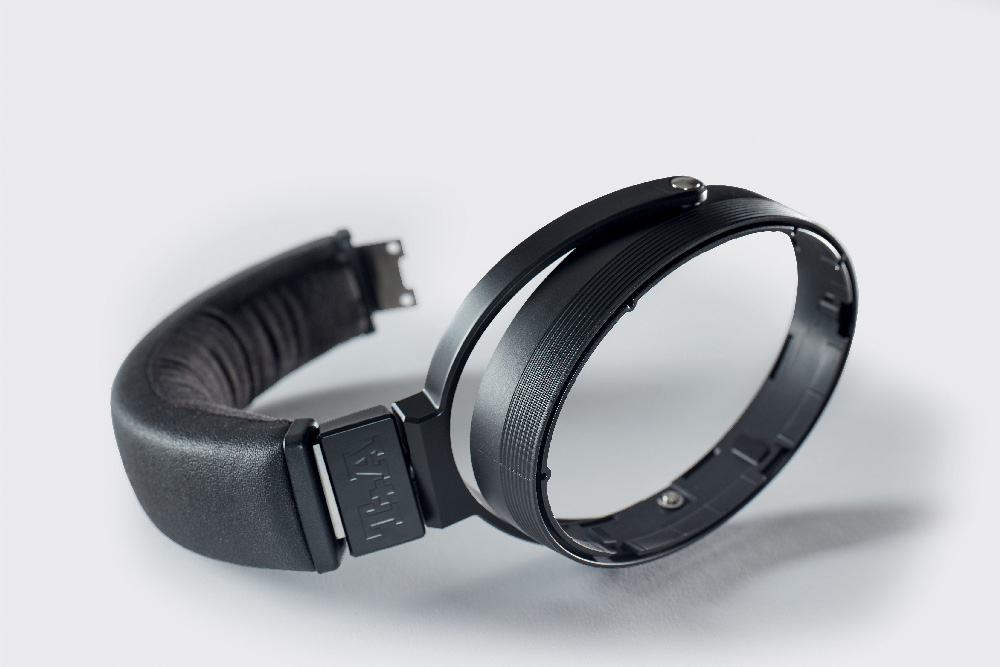
Experts de la mise en œuvre de géométries complexes grâce au moulage par injection
Le Solitaire P contenait cinq petites pièces moulées par injection dans la coque de l'écouteur et dans la coque en aluminium elle-même, mais le Solitaire P-SE devait être produit en grande série sans aucune pièce en aluminium. Cependant, dans la mesure où l'abandon de l'aluminium au profit des pièces en plastique ne devait avoir qu'une influence minimale sur la conception, tant Protolabs que T+A ont dû faire preuve de créativité.
« L'un des avantages de l'impression 3D réside dans l'énorme flexibilité dans la conception des composants », déclare Viktor Pöss. « En revanche, dans la production par moulage par injection, c'est-à-dire quand les composants doivent être créés à partir d'un moule en creux, de nombreux aspects doivent être pris en compte dans la conception des moules pour mettre en œuvre les contredépouilles et éviter les marques de retassure. »
« J'ai moi-même l'expérience de la fabrication de moule et j'avais parfaitement conscience de la complexité de la mise en œuvre de la coque de l'écouteur du Solitaire P-SE », ajoute Sebastian Kobelt. « C'était d'autant plus gratifiant de pouvoir travailler avec Protolabs d'égal à égal. La coopération a été très agréable du fait du grand savoir-faire des deux parties, et nous avons pu lancer la fabrication des moules d'injection après seulement quelques itérations. »
L'un des principaux défis dans la conception de la coque de l'écouteur résidait dans le fait qu'elle devait contenir un grand nombre d'aimants et de diaphragmes différents. De plus, ces composants centraux devaient s'harmoniser avec 13 autres composant dans le Solitaire P-SE, dont la production par moulage par injection a été également confiée à Protolabs. En outre, la conception devait également inclure les points d'attache pour les coussinets.
Tempo du développement ? Allegro !
L'efficacité du partenariat entre T+A elektroakustik et Protolabs ne se reflète pas seulement dans la mise en œuvre réussie du produit de luxe fini. Le temps de développement incroyablement court des composants du Solitaire P-SE prouve également le degré d'harmonie qui a régné durant cette collaboration. Par exemple, six mois seulement se sont écoulés entre le premier contact concernant le projet en juillet 2020 et la vente des premières unités Hi-Fi haut de gamme en janvier de l'année suivante.
« L'interaction humaine et la compétence des salariés de Protolabs, tant en ce qui concerne leur maîtrise de l'ingénierie que de la part administrative, sont purement et simplement bluffantes », ajoute Sebastian Kobelt pour conclure. « Avec Protolabs, nous avons eu un partenaire à nos côtés dans ce projet, grâce auquel nous avons réussi à restreindre considérablement le temps de développement. Nos équipes ont également pu en permanence échanger des idées et répondre à des défis sur un pied d'égalité, ce qui a rendu le travail en commun très agréable. »
Le résultat de ce projet en partenariat est un produit dont nous pouvons être fiers et qui a déjà séduit les mélomanes du monde entier par son acoustique unique, même si bien peu d'entre eux se rendront compte de la prouesse d'ingénierie discrètement dissimulée à côté de leurs oreilles.