3D Printing Bolsters Innovation for Global Manufacturer
Multi Jet Fusion offers design freedom, durable materials to help Nordson Corp. rapidly prototype parts for adhesive dispenser for consumer electronics sector
The innovative ideas we most often hear about are those that hatch new products. Yet the quest for innovation also is central to those engineers and product developers who are re-designing existing products or models as they aim to upgrade and improve those products.
A recent redesign project by an engineering team at Nordson Corporation, which collaborated with Protolabs and used our Multi Jet Fusion industrial-grade 3D printing (additive manufacturing) technology for prototyping, illustrates this point.
The Ohio-based global company designs and manufactures dispensing technology and equipment for consumer and industrial adhesives, sealants, and coatings. Operating in more than 35 countries, Nordson serves a diverse set of industries: medical, aerospace, automotive, consumer electronics, and more.
An engineering team at Nordson’s facility in Duluth, Georgia, had been redesigning a heated adhesive dispenser used by industrial customers manufacturing products in the consumer electronics sector.
“Quality and precision are always our goals and keys to our dispensing technology,” said Chris Chastine, a mechanical designer with 30-plus years of experience at Nordson. “That was certainly the case with this project.”
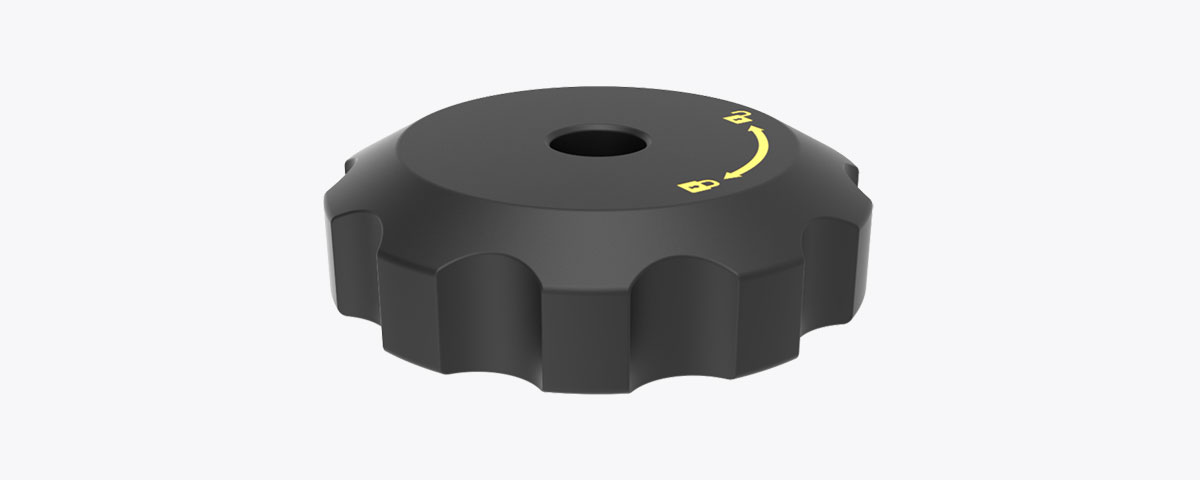
To achieve a more rugged part, Nordson engineers worked with Protolabs and settled on 40% glass-filled PA 12 powder, adding strength and thermal resistance.
Challenges: Design Freedom, Durable Materials, Rapid Turnaround
As Chastine explained, this product applies very small, precise dots of adhesives onto a variety of consumer electronic products. These are items that require a dispenser to apply adhesive in very precise locations and amounts while creating a solid bond.
This product is a high-speed dispenser allowing those using it to either apply small individual dots or to apply many dots closely, effectively creating a continuous bead of glue. “Precision is important. Applying too much adhesive is wasteful and expensive, but applying too little could create a defective product,” Chastine said.
An integral component of the newly designed dispenser would be the adhesive air cap, which would be one of several parts eventually assembled into the adhesive dispenser. The applicator size and shape are intended to reach those small, hard-to-get-to areas of electronic products. “We tried to design this particular dispenser in a way to make it fit into tight areas where needed,” Chastine said. The adhesive dispenser air cap was a part that was to be molded but the engineers knew a few design iterations might be needed. Because of this, and the 10-12-week typical lead time for an injection mold, they needed to find a different solution.
![]() |
---|
At A Glance |
Engineers for Nordson Corporation were re-designing an adhesive dispenser to be used by industrial customers manufacturing products in the consumer electronics sector. The product was designed to apply tiny, precise dots of adhesives onto a variety of electronic products. The dispenser’s air cap was going to be molded but the engineers knew a few design iterations might be needed. Because of this, and the 10-12-week typical lead time for an injection mold, they needed to find a different solution. ![]() Engineers turned to in-house 3D printing for greater design latitude, but their materials selection was limited, and they were facing a swiftly approaching go-to-market deadline. Three solutions were needed: greater design freedom, a wider choice of materials, and quick turnaround. Enter Protolabs. Our Multi Jet Fusion industrial-grade 3D printing (additive manufacturing) technology could readily handle the complex design, offered an array of material options, and could meet the tight deadline.
The deadline was met, with several iterations of 3D-printed prototypes delivered in days instead of weeks, saving Nordson engineers nearly 10 weeks of development time. Those parts included the adhesive air cap and an overall exterior cover for the dispenser. The product is now on the market and available to Nordson’s customers.
|
The team’s early design iterations called for the air cap to be injection-molded, but design issues emerged because of some required undercuts, Chastine recalled. Adding to the design challenge was the relatively small size of the air cap itself, which is 0.75 in. (19mm) tall, with the biggest diameter of the part being 2.3 in. (58mm).
As a result, the engineers considered using their own, in-house 3D printer, which has provided great design latitude, but their printer has a limited selection of printable materials.
“We needed a durable material, and we didn’t have it,” Chastine said. “Durability was a major requirement for this part because it would see some wear, and the part would also need to be threaded in one area as well.” When used, the cap needs to be turned clockwise to lock it in place and counterclockwise to remove the cap and replace the syringe of adhesive contained inside of the heated applicator. Air pressure is required for this applicator so the heated adhesive can be pushed toward the exit point of the applicator. The air pressure comes in through a fitting in the top of the printed cap.
Beyond the design freedom and durable materials issues, the engineering team faced a swiftly approaching go-to-market deadline to compete with other companies. That’s when Chastine and his team turned to Protolabs digital manufacturing services.
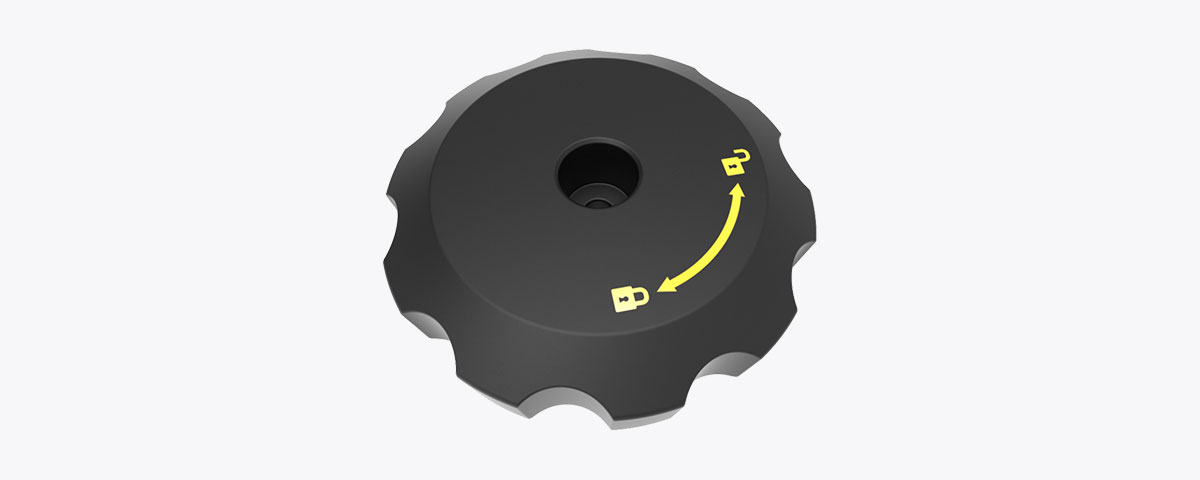
The yellow user directions were added to the final part using pad printing, a post-processing technique that uses special inks to add text and/or shapes.
Manufacturing Solution: Multi Jet Fusion
For more than a dozen years Chastine had used our services for several injection molding projects and knew of our quick-turnaround capabilities that also included 3D printing. Accordingly, the Nordson team sought help from Protolabs, starting where most companies start with us: using our quoting and design analysis system for the air cap.
As they did with their original designs, the team first submitted models that were intended to be molded. However, as was the case with their original models, our design analysis revealed manufacturability issues. As a result, with further design analysis—plus some technical and training support from us—the Nordson team opted for our Multi Jet Fusion 3D printing technology. MJF could readily handle the complex design of the air cap. The technology—which can produce functional nylon prototypes and end-use production parts—builds parts with complex and organic geometries. Those MJF-produced parts exhibit quality surface finishes and fine feature resolution, plus have consistent isotropic mechanical properties.
Along with MJF, we could offer Nordson a range of materials to choose from, including more durable options. The team settled on PA 12 40% glass-filled, which is a polyamide powder packed with glass spheres that add stiffness and dimensional stability, has higher thermal resistance than unfilled polyamides, and exhibits long-term wear resistance. For most parts, we can achieve tolerances of ±0.012 in. plus ±0.002 in./in. for each additional inch, although they may change depending on part geometry.
The material’s stiffness and temperature resistance make it suited for components such as armatures and mounting plates, and, in Nordson’s case, an adhesive air cap prototype. Nordson engineers made five prototypes to start with, and then tweaked designs after that, Chastine explained.
Finally, through all those iterations, our MJF technology delivered parts rapidly.
Outcome: Deadlines Met, Development Time Saved
The ultimate outcome of this prototyping project? The swiftly approaching deadline Nordson engineers were facing was met. Those several iterations of 3D-printed prototypes were delivered in days instead of weeks, saving Nordson nearly 10 weeks of development time, Chastine said.
Those parts included the adhesive air cap and an overall exterior cover for the dispenser. After our prototyping work was completed, the parts moved to another manufacturer for high-volume, injection molding, end-use production parts, and then eventually were assembled onto the dispenser itself.
The heated adhesive dispenser is now on the market and available to Nordson’s customers in the consumer electronics industry.