When 3D Printing is the Double-edged Sword that Leads to the ‘Manufacturability Talk’

Let’s start with a common conversation I have with my engineering students at Duke:
Me: “How are you going to make that?”
Engineering student team: “3D printing.”
Me: “We need to talk…”
At our current point in time in the evolution of additive manufacturing, 3D printing serves as both a blessing and a curse with young engineers; thankfully, Protolabs gets it.
Every fall around 40 students, fresh from undergraduate engineering degrees enter my Advanced Design & Manufacturing class that forms part of the Medical Device Design Certificate in the Duke Biomedical Engineering Master’s program. This incoming class is invariably smart, eye-wateringly so in fact, but the majority of the time, incoming students have two giant blind-spots—manufacturing medical devices at scale and manufacturing by any process other than 3D printing.
First, I take them through a simple “how many of your brilliant new medical doohickey do we need to make in an average year for the U.S. market based on the number of hospitals, cases, and market penetration?” Answer: It’s a big number. We then crunch those numbers and determine that this translates into making 75 devices per hour with no lunch; I now have their attention; “no lunch?!?!?” We noodle a little longer and determine that we would need a string of 3D printers halfway from Durham to Atlanta. My point is made.
Today, 3D printing is not a high-volume manufacturing process and certainly not in the medical device industry where IQOQPQ, a quality management department, and occasionally the FDA walk the halls.
Now my students are baffled, because all they have ever really done is design in slick 3D CAD packages and then 3D print their designs on exciting new platforms. But I just demonstrated that 3D printing won’t work, at least not for the next few years until the technology takes another couple of quantum leaps.
Me: “Ever heard of injection molding?”
Engineering student team: “Yeeees…” *nervously*
Me: “We’re probably going to need to mold these to hit the numbers and quality.”
Engineering student team: “Great, let’s send our CAD file to an injection molding machine”
Me: “We need to talk some more…”
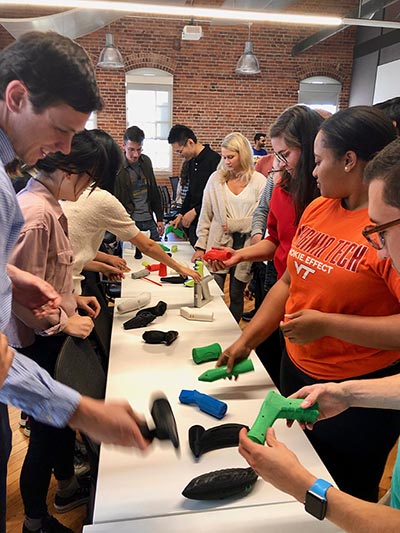
While the majority of my students can describe what injection molding is, they can’t tell me how to design for it, or more specifically how to design a component so that the molding tool needed to make it does not have to contravene several laws of geometry and physics (or worse, prompt grumpiness from their future toolmakers).
The problem I see every semester is that when students design in the virtual world of 3D CAD and then 3D print, they are lulled into a (currently) false sense that anything goes and “someone else” will just make the parts per the design on their screen or what the FDM machine printed. Many seasoned industry folks reading this article are probably now chuckling.
Here at Duke University, in close partnership with Protolabs, we are working to fix this.
I begin by explaining how processes like extrusion, casting, and injection molding actually work and how the mold (tool) forms the final component. In the case of injection molding, I start with a blueberry muffin, progress to a flower pot, and then a flower pot with a giant dent in the side.
Me: “What happens if I eject that?”
Engineering student team: “Erm, something is going to break.”
Me: “Yup, and in a battle between hardened tool steel and plastic, the steel generally wins.”
Me again: “So will your nicely 3D-printed doohickey come out of a steel mold?”
Engineering student team: “Ummmm, yeah, no.”
Now they are leaning in.
In the following weeks we explore the wonders of draft angles, side-actions, up-and-aways, ejectors, sprues, hot tips, heating and cooling, multiple-shots and more. Protolabs puts its Design Cube, Demo Mold, material samples, selectors and Injection Molding for Dummies book in hands of every student. Protolabs “gets it.” They know that designing for volume manufacturing is a continuum, and delusion in the early stages only prompts re-designs (and lost time and money) later down the product development path—“design with your target processes in mind and save much heartburn.” Vicki Holt and now Robert Bodor, former and current CEOs, respectively, also appreciate that the future of innovation and design is in the hands of the students of today, and Protolabs helps drive that.
Before long our (notice how I have switched to our) students are using 3D printing to check their design, visualize their tooling options, assess fit, function, and critical tolerances, but end with a true production-ready design that will hopefully at least prompt an approving nod from a less grumpy toolmaker who now wants to talk about how to make it even better for production. Before the pandemic, the crew at Protolabs even opened the doors of its Cary, NC facility where our students could see and touch what commercial 3D printing can really do to help the design process, and what it can’t do. We look forward to those Friday afternoons again.
By the end of all of this, we give the students a three-week project to design a new medical device for the market.
Me: “How are you going to make that?”
Engineering student team: Two snap-fit Injection moldings with a coextrusion for the thribblewidget.”
Me: “You’re ready.”
End scene.
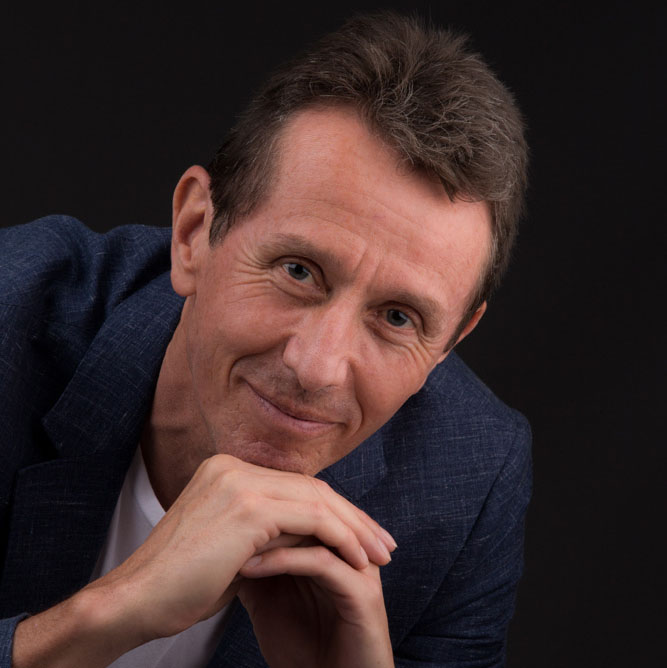
Paul Fearis is an Associate Professor of the Practice in the Department of Biomedical Engineering at Duke University. With Prof. Eric Richardson, he teaches medical device design to industry bound MEng and MS students.
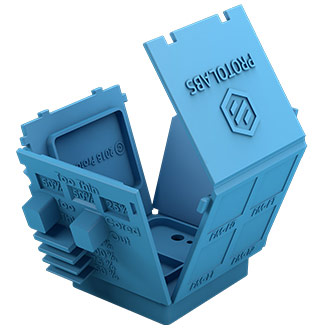
Now that you've heard all about the Design Cube, grab one for yourself. It shows part features that are too thin or too thick, bad bosses, right and wrong ribs, and other considerations when designing parts for molding. Get a free Design Cube.