Metal 3D-Printed Turbopump Fuels Space-Shot Rocket
The University of Washington’s Society for Advanced Rocket Propulsion is dedicated to working along the cutting edge of college rocketry. Their drive for innovation has produced groundbreaking technology as well as rocket scientists who go on to work for industry leaders that shape the future of aerospace.
The team is no stranger to a successful launch. It recently completed its “Pacific Impulse” rocket, which is a liquid bipropellant rocket that uses a fuel combination of nitrous oxide and ethanol. The rocket provided vital foundational knowledge to the team. SARP is also putting the finishing touches on its “Short King” rocket, which will compete in the Intercollegiate Rocket Engineering Competition in 2024, with the expectation that it will reach an apogee of 10,000 feet.
Armed with practical knowledge gained from each successful launch, SARP and its more than 200 members are now focused on what might be their magnum opus.
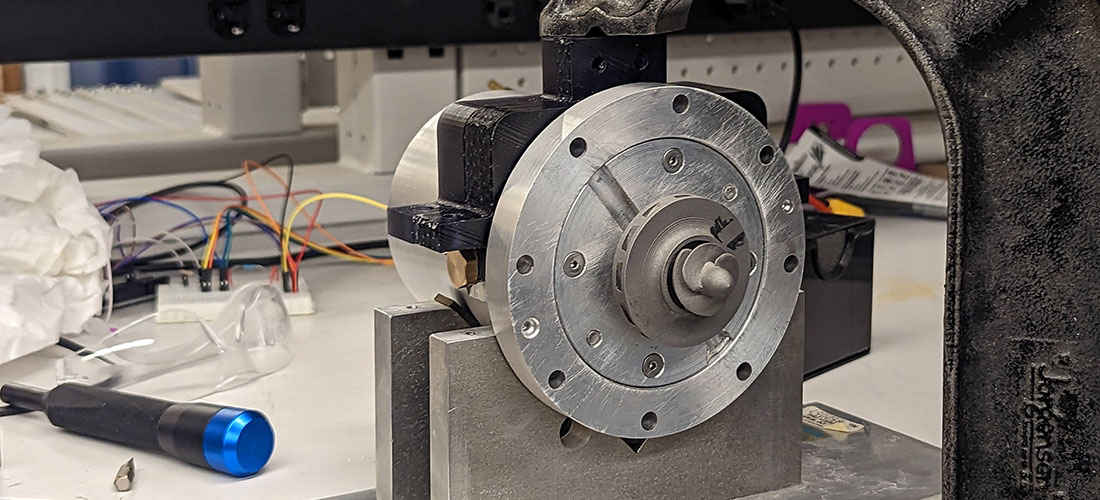
The Washington University Rocketry Team fuel pump set up in a test configuration.
Reaching Space with Industry-leading Technology
Currently under development, the “Stargazer” is a bipropellant rocket shooting for the Kármán line, which is the official dividing line between Earth and space. The monumental achievement would be a first for collegiate rocketry groups and requires technologies that SARP must design from scratch.
The team was tasked with creating internal hardware primarily seen in industry rockets much larger than the Stargazer. The primary component the team is developing involves the creation of an electric turbopump, which is used to transport cryogenic fuel.
“To reach the Kármán line, we would need to move away from the tried-and-true architecture used previously with our rockets,” said Josh Welcher, who started the development of the fuel pump as SARP’s rocket propulsion engineer and now works for SpaceX. “Pumps are traditionally something only meant for the big guys in the industry, so we saw this as a fantastic opportunity to push the boundaries of what students like us could do.”
The fuel pump would trim 60-80 kilograms on a rocket weighing around 200 kilograms without sacrificing an ounce of power. That’s up to a 40% reduction in weight! The endgame was clear but the path to get there was extremely complex.
An industry rocket designed by SpaceX, for example, is much larger than SARP’s Stargazer. The smaller size increases the difficulty of designing the fuel pump because of the need to achieve maximum functionality in a tighter space. While larger versions of the fuel pump could be manufactured out of traditional processes such as CNC machining, the team relied on the design freedom of 3D printing to install the necessary components on a smaller scale.
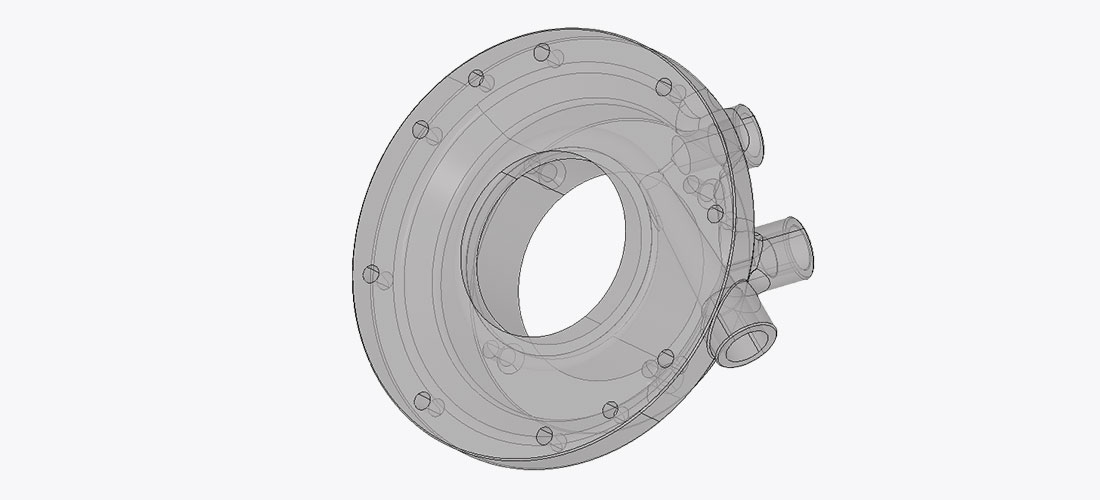
A model of one element of the fuel pump apparatus.
3D Printing Produces Big Power in Small Spaces
The team’s fuel pump design centers around an inner ring that gradually increases in diameter throughout the inner chamber. An impellor spinning at 30,000 revolutions per minute pushes the fluid through the chamber in a highly synchronized route that produces the necessary pressure for the rocket engine to function. Overall, it’s a highly complex process requiring an intricate design, according to Welcher.
“There’s a delicate balance in making sure you are getting enough propellant and system charge going so you can actually ignite—not too little so you get nothing, but not too much where you end up with, essentially, a bomb,” said Welcher.
Michael Gabalis, former SARP project manager and current aerospace engineer for the United States Space Force, said the team relied on advanced modeling software and their own knowledge to design a prototype that could test the efficiency of the design.
Provided with a Protolabs Cool Idea Award manufacturing grant, the team turned to our metal 3D printing technology (DMLS) to create a functional fuel pump that would be able to hit the tight tolerances necessary for success.
“When you are modeling something at our scale, literally millimeters matter when it comes to developing any pressure at all,” said Gabalis.
DMLS proved to be a fit when combined with 17-4 stainless steel for a material, which is strong enough for threading and able to withstand extreme temperatures. These specs will be key in future versions of the fuel pump.
The initial prototype was put through extreme testing with water serving as the test fluid. Mass flow rate was near the desired goal, as were pressure levels, which reached 270 PSI. The team will continue to iterate on the initial design as they move toward the model that will eventually be installed in the Stargazer.
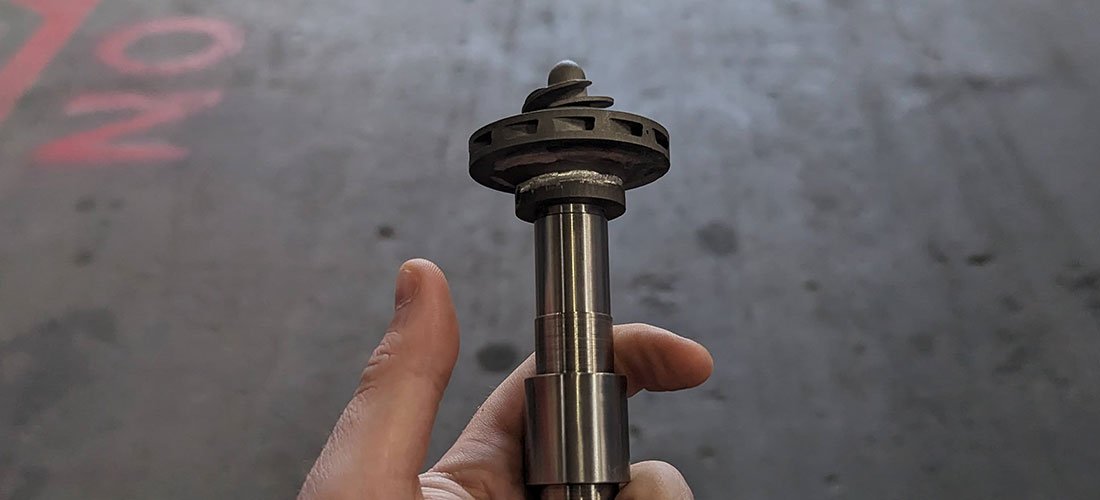
The inner workings of the 3D-printed fuel pump, which was constructed using DMLS.
The Journey to Launch Day
Current SARP Propulsion Lead Nathalie Peterson reported the team is busy building on what they have learned with the initial pump design. The current goal is to integrate the fuel pump into the overall rocket system for a hotfire test this spring. Firing off the engine and measuring its performance will be a milestone for the team, but it is just the first of many key steps. A full launch is expected in 2025, although speed has never been the primary goal for the team.
“We didn’t launch this project with the goal to be the fastest or first to do it; we wanted to do it with technical excellence,” said Welcher. “We aren’t just trying to do cool things—we want to innovate and drive the collegiate sphere forward to make sure we aren’t all just doing the same thing, but rather pushing each other to be the best engineers we can be.”
