Metal 3D printing has been around for roughly 30 years, yet the technology can still turn heads. At trade shows, for instance, the printed metal parts we have on display at our booth often elicit surprise from those stopping by for a closer look, slightly stunned that parts can, in fact, be 3D printed from metal.
We use direct metal laser sintering (DMLS), an industrial-grade, metal 3D printing technology that builds fully functional metal prototypes and end-use production parts from a range of materials, including stainless steel (17-4 PH and 316L), aluminum (AlSi10Mg), Inconel 718, cobalt chrome (Co28Cr6Mo), and titanium. Metal 3D printing is commonly used for:
- Prototyping in production-grade materials
- Creating custom parts that require complex geometries
- Building functional end-use parts
- Reducing the number of metal components in an assembly
Within the context of metal 3D printing materials, a part’s density is an especially key physical property for both engineers and product designers. In engineering, density may refer to one of two separate but related concepts: Bulk density is expressed in grams per cubic centimeter, and porosity is expressed as a percentage of fill. We cover both in this article.
Let’s take a look at both factors, but first some brief background on DMLS.
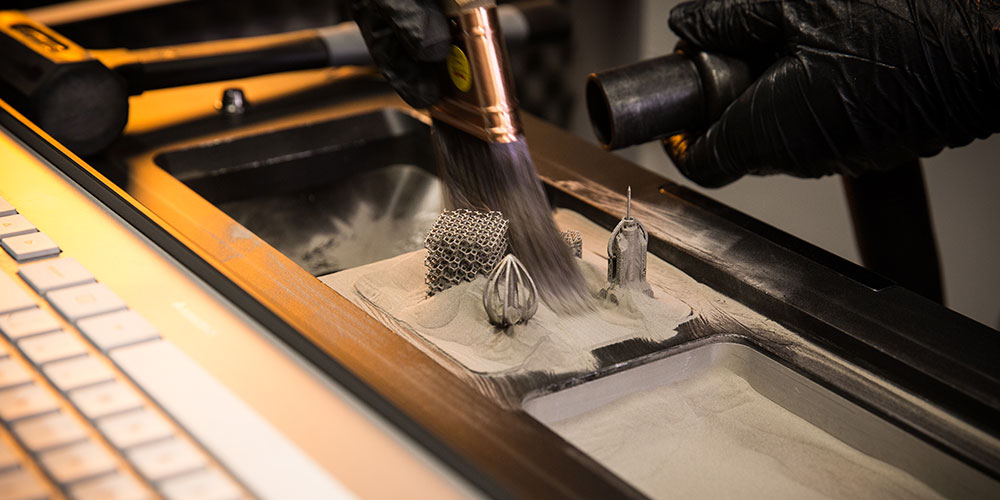
DMLS starts with a metal powder that is melted in layers to form the part.
What is Metal 3D Printing? From Metal Powder to Liquid State to Finished Part
Direct metal laser sintering is really direct metal laser melting—DMLS is DMLM. That is, the sintering part of this additive process is really a melting process. We start with metal powder, then our machines use high-powered lasers to melt layers of that powder—to liquify it—to create complex 3D geometries directly from our customer’s CAD file. After a cross-section layer is created, the build platform lowers and a re-coater blade moves across the platform to deposit the next layer of powder into an inert build chamber. The process is repeated layer by layer until the build is complete. The main goal is to produce metallic parts with 100% density. More on density percentages later in the section on material strength.
Part sizes vary for our metal 3D printing. Minimum part size is 0.006 in. (0.15mm). Yes, tiny parts can be made with metal 3D printing, something that’s especially applicable in the medical sector. Maximum size is 9.6 in. x 9.6 in. x 13 in. (245mm x 245mm x 330mm), though you can print even larger with our X Line 2000R DMLM machine. It can produce large-format functional parts, systems, and technical prototypes as large as 31.5 in. x 15.7 in. x 19.7 in. (800mm x 400mm x 500mm).
These days, we see a range of industries turning to metal 3D printing for prototype and production parts, especially aerospace, automotive, and medical/health care, producing components with varying types of metal materials, from jet engine fuel nozzles and rocket engine parts to automotive motor mounts and medical surgical tools.
At least two of those sectors—aerospace and automotive—are especially concerned with the weight of their parts, which leads us to the next section.
Part Density and Weight Factors in Metal 3D Printing
The density of a metal will determine how much a part of a particular size weighs. As mentioned, weight is an important consideration, especially in aerospace and automotive applications. Engineers and designers in those industries are always looking for ways to reduce component weight to meet emission standards, cut fuel consumption, consolidate many parts into fewer parts, and streamline overall product design.
As satellitetoday.com has reported, a 3D-printed metal bracket for an aircraft could see a weight reduction of 50 to 80%, saving roughly 2.5 million gallons per year in fuel. Airbus developed a spacer panel, located alongside the overhead storage compartments of its A320 commercial aircraft, which is 15% lighter than the original.
Engineers and designers looking for lower-weight parts might turn to materials or alloys that are less dense. They should be cautious, though, because then they must consider the strength-to-weight ratio.
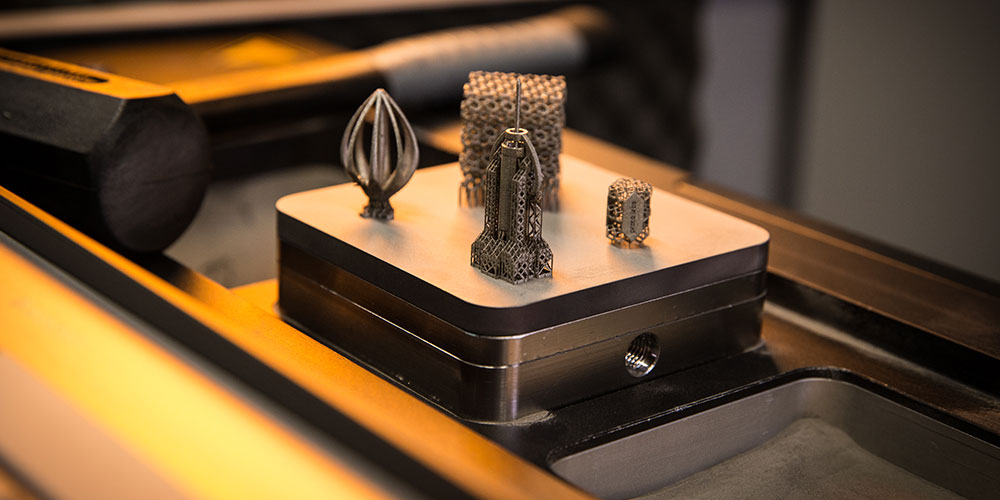
DMLS produces dense parts strong enough for numerous industrial applications.
Part Density and Strength Factors in Metal 3D Printing
Dense materials make strong parts—the more density, the more strength—which is why the percentage of density of a part’s material is so crucial. Density is essentially the concentration of a given material in a given space.
The DMLS process generally produces parts that are nearly 100% dense, although a small amount of porosity is typically present. We expect our DMLS parts to meet or exceed 99.5% density through our standard process. For applications that require the highest mechanical performance and fatigue resistance, the small amount of porosity present in a printed component can be reduced even further through a post-processing heat treatment called hot isostatic pressing (HIP). HIP reduces much of the remaining internal micro-porosity by applying high heat (more than 2,000° F or 1093° C) and very high gas pressure 15,000psi) on all sides to fully solidify the part.
As always, if you have any questions, feel free to contact one of our applications engineers at [email protected] or 877-479-3680.

If you have any issues getting your guide, click here to download.


Need custom 3D-printed parts? Upload your CAD file for an instant online quote.
Get Printed Parts