Aluminum Alloys: Go-to Materials for Automotive, Aerospace, and More
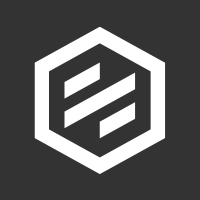
Aluminum is a common and popular metal that’s found everywhere and used in a stunningly wide range of parts and products: automotive parts, aerospace components, boat and marine gear, consumer electronics including smart phones, industrial machinery parts, HVAC systems, the list goes on.
Engineers and product designers frequently turn to aluminum and many of its alloys to design both prototypes and end-use parts in a variety of industries. This post takes a look at why aluminum is so common, why there are so many aluminum alloys, and takes a brief glimpse at the main alloys we use here at Protolabs.

Why is Aluminum So Popular?
Aluminum has a high strength-to-weight ratio, making it lightweight, yet strong and flexible. It’s also affordable, corrosion-resistant, and works well in a multitude of applications.
Aluminum alloys are often used in cars because of the material’s versatility. Aluminum’s formability and corrosion resistance make it easy to work with and shape, but its structural soundness addresses the most important requirement for car bodies. Strength is important, but car bodies must be lightweight, affordable to produce, resistant to rust, and have the attractive qualities consumers seek, such as exceptional surface finishing characteristics. Aluminum nicely fits the bill.
The same holds true with aerospace parts. Aluminum alloys are often a preferred material for aerospace designs and required by engineering, again because of aluminum’s corrosion-resistance properties and high strength capabilities. Compared to steel it is a lightweight option, and an ideal material for a wide range of aircraft components and aerospace applications.
Lightweighting is a core need of both the automotive and aerospace industries.
With cars, lightweighting helps reduce emissions and meet improved fuel economy standards.
For aerospace, the use of aluminum alloys dramatically decreases the weight of an aircraft because it is significantly lighter than steel, allowing aircraft to either carry more weight or increase fuel efficiency. For instance, a 20% weight reduction in a Boeing 787 is expected to generate a 10–12% improvement in fuel efficiency. Along these lines, common applications in aerospace abound—many, but not all, of which, are metal: Fuel nozzles, heat exchangers, manifolds, turbo pumps, liquid and gas flow components, conformal cooling channels, fasteners, and more.
Why So Many Metal Alloys?
Aluminum, as a pure element, presents many desirable properties. However, by itself, aluminum might not be strong enough for a high-durability use or purpose. Accordingly, aluminum can be combined with other elements to form alloys, which are more durable and suitable for industrial applications.
And what do all of those numbers in the alloy name signify? The aluminum series names elements with four numerical digits where the first digit represents the principal alloying element, the second digit indicates a modification of a specific alloy, and the third and fourth digits are arbitrary numbers assigned to specific alloys in the series.
Material |
Process |
Tensile Strength |
Elongation |
Hardness |
Al 6061-T651 |
CNC Milling CNC Turning Sheet Metal Fabrication |
40 ksi (276 MPa) |
17% |
95 HBW 10/500 |
Al 7075-T651 |
CNC Milling CNC Turning |
83 ksi (572 MPa) |
11% |
85 HBW 10/500 |
Al 5052-H32 |
Sheet Metal Fabrication |
33.34 ksi (228 MPa) |
12% |
60 HBW |
Al (AlSi10Mg) |
3D Printing: DMLS High resolution (20 μm) |
39 ksi (268 MPa) |
15% |
42 HRB |
Al (AlSi10Mg) |
3D Printing: DMLS Normal resolution (30 μm) |
50 ksi (345 MPa) |
8% |
59 HRB |
Al (AlSi10Mg) |
3D Printing: DMLS Large Format (40 μm) |
43 ksi (296 MPa) |
10% |
50 HRB |
Al 6061
The most commonly used aluminum alloy at Protolabs, Al 6061 is used for CNC machining and sheet metal fabrication. It is generally selected where welding or brazing is required or for its high corrosion resistance in all tempers. Formability is excellent in O temper and good in the T4 temper. It is used for automotive parts, boat and marine gear, furniture, consumer electronics, and more.
Al 7075
This alloy adds chromium to the mix to develop good stress-corrosion cracking resistance. It is the go-to alloy for aerospace parts, bicycle equipment, camping and sports gear because of its lightweight yet strong characteristics.
Al 5052
Used in our sheet metal fabrication division, this alloy has good workability, very good corrosion resistance, high-fatigue strength, weldability, and moderate strength. This makes it perfect for use in aircraft fuel/oil lines, fuel tanks, other transportation areas, appliances and lighting, wire, and rivets.
AlSi10Mg
A mainstay of our 3D printing direct metal laser sintering (DMLS) process, this is comparable to the 3000 series alloy that is used in casting and die-casting processes. It has good strength-to-weight ratio, high temperature and corrosion resistance, and good fatigue, creep, and rupture strength. AlSi10Mg also exhibits thermal and electrical conductivity properties. Final parts built in AlSi10Mg receive stress relief application.
For questions on aluminum alloys, other materials, or any of our manufacturing services at Protolabs, please contact an applications engineer at [email protected] or 877-479-3680.