University KREPS Capsule Set for Space Launch with Protolabs 3D-Printed Parts
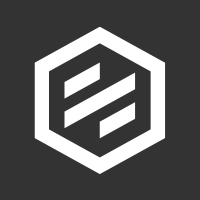
Once you’ve made history in the scientific community as part of a research-based space flight mission, what’s next? Do it again, but level up! That’s what a group of three University of Kentucky students are working on now: building upon a successful 2021 orbital re-entry project. This time around, they’re launching five capsules featuring Protolabs 3D-printed parts to space via the NASA Cygnus cargo spacecraft in hopes of collecting and validating more scientific data. We chatted with current project lead and mechanical engineering student Kirsten Ford to get the lowdown on the project’s history, hear how it’s evolved, and understand why our quick-turn selective laser sintering technology was the perfect fit for the capsule’s vital internal housing.

Breaking Records with KREPE-1
Back in 2013, University of Kentucky students created the Kentucky Re-entry and Universal Payload System (KRUPS) project to design a small re-entry vehicle that could provide affordable and repeatable access to space. The team hoped to test their thermal protection systems, scientific instrumentation, and, most importantly, validate specific codes created for re-entry flight, material response modeling, and hypersonics. These codes are necessary to simulate conditions experienced by a reentry vehicle while returning to earth but are not simple to perfect.
“As we developed these codes, we realized that we need to validate them with actual experimental data. Unfortunately, it’s not easy to acquire that data because these NASA flights you see are multimillion-dollar projects that take years to plan and execute,” Ford explained.
The opportunities for orbital re-entry flights only come around every year or two, so the team worked out other ways to collect and test their data in between those missions starting with sub-atmospheric balloon launches and progressing into sounding rocket flights. All the team’s sub-orbital sounding rocket flights take place at NASA’s Wallops Flight Facility.
KREPE-1 (Kentucky Re-Entry Probe Experiment) is what Ford refers to as her team’s magnum opus, which included three capsules that were loaded onto NASA’s Cygnus vehicle in 2021 and ultimately traveled to the International Space Station (ISS). “We were the first University to pull off an atmospheric re-entry from the ISS and the first university to fly a 3D-printed heat shield,” Ford said.
Minimizing Environmental Impact During Re-Entry
The Cygnus vehicle was designed to break up upon re-entry to the earth’s atmosphere. Why? “The astronauts on the ISS take supplies off of Cygnus, and fill it with trash, and it burns up as it re-enters the atmosphere, so the debris doesn’t fall to earth. Our capsules were stored on board that vehicle and were ejected,” Ford explained. Although the capsules are destroyed upon atmospheric re-entry, the team can recover helpful data that’s written to a computer and sent to the team via email.
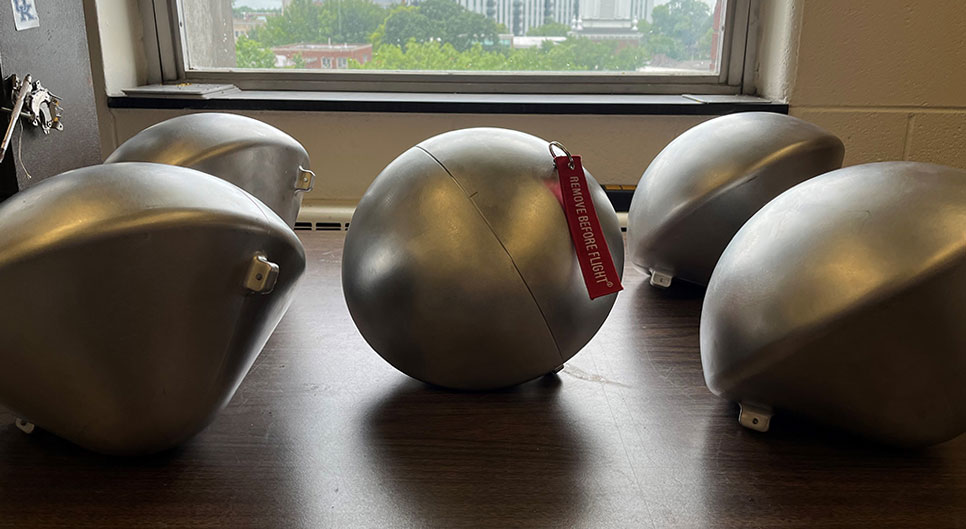
The assembled capsules ready for space flight.
Material Considerations for Aerospace
The team has used Protolabs for the last few years to 3D print the components’ internal housings for multiple missions. “We like that they’re lightweight and durable and that Protolabs can design to the exact specifications that we want. We went with Protolabs for the original KREPE mission, and we are again for KREPE-2. We 3D-printed some initial iterations in-house, but they couldn’t compare to the durability and quality of the ones that we get from Protolabs. We plan to continue working with you in the future because the internal housing is such an integral part of our payload and it’s where we house all of our electronics,” explained Ford.
When designing components to be used in space flight, several extreme conditions need to be considered. Ford explains that upon atmospheric re-entry, temperatures can get so hot, it can melt wires and singe metal, but the internal housing itself isn’t being exposed to these conditions. A heat shield, which takes the brunt of the heat exposure encapsulates the entire internal housing. The most important material property for the internal housing is maintaining structural integrity. “Although it’s not experiencing any kind of impact, there are a lot of vibrations that the capsule undergoes, especially during launch,” said Ford.
Ford worked with our applications engineers to settle on 25% mineral-filled PA12, a durable nylon material selected for both its stiffness and high-temperature resistance. Each part was printed via selective laser sintering (SLS).
The team is headed to NASA for extensive vibe testing, where the capsule is tested and shaken up it in multiple orientations to simulate the vibrational load experienced during launch.
“If we had something a little less structurally sound, there’s a high probability that those launch vibrations could crack it or damage the internal housing, which would compromise our mission because everything is held together by it. If it were to crack or splinter, that would be catastrophic for our mission,” said Ford. That’s what we like about the Protolabs manufactured one. Because it’s experiencing such high vibrational loads, we need to trust that our internal housing is not going to crack or fall apart on us, because everything is kind of hinging on that structure.”
Experimentation-based Prototyping
A lot of time is spent in the prototyping phase of the KREPE-2 project. “Our bread and butter for this project is our orbital missions, which is when you’re getting the data you want to validate those codes. Suborbital launches are never going to give you the heat profile and velocity to get accurate results,” she said.
So why are suborbital missions a critical part of the process? “They’re all part of the prototyping process. “The suborbital missions allow us to put our electronics and scientific equipment to the test. If something doesn’t work out the way we wanted it to during a suborbital flight, we have time to fix it,” Ford said. “I’m a master’s student in engineering but my job is a lot more research and development focused than traditional engineering. I’m not sitting at a desk working on CAD and equations. I’m building, testing, and experimenting. I sometimes say I’m an engineer, but I’m really an experimentalist at heart.”
Ford and her team are preparing for the culmination of the KREPE-2project: a November NASA mission, sending up five capsules to the ISS and gathering data on new experimental thermal protection systems. “People don’t see how much work goes into this. It’s a student led project and months and months of work goes into this. Not to mention the years of students that have come before us working on this project and making a difference. It’s nerve-wracking, but it’s all worth it in the end,” Ford explains.

If you have any issues getting your guide, click here to download.


Need custom 3D-printed parts? Upload your CAD file for an instant online quote.
Get Printed Parts